Introduction: Customizable Work Bench
TLDR; Go to my blog post to use my interactive, mobile-friendly, 3D widget to input your dimensions and instantly generate a materials list and cut list for your customized workbench. Follow the rest of the steps for instructions assembling the workbench.
I've been getting my garage into shape to be able to work on all kinds of projects. I anticipate doing all sorts of making from coding, to soldering electronics, to woodworking, to 3D printing and other CNC projects. Over the last fews years, I've accumulated some fun toys such as a MakerBot Replicator 2 (won in an Instructables contest), a Pocket NC 5-axis desktop CNC machine (traded for some programming work) and some other more common tools such as a soldering iron and other traditional tools. I'd like to have access to these tools on my work bench while still having plenty of room to work. I'd also like to be able to work standing up or sitting down, so I figured a standing desk with a stool would be the way to go.
A friend of mine made some standing work benches for his shop that I liked but were not quite as deep as I wanted. I figured a 3 foot deep work bench would work great. I always like to have a programming component to my projects, so I adapted my friend's design to be an interactive OpenJSCAD widget which allowed me to set the depth along with any other dimension to my taste. You can play with the widget yourself on my blog post (don't worry, no coding required). It allows you to customize the table to fit your space, to suit your height, or just tweak things to taste. I've read that the ergonomic height for light work is about 3 inches below the height of your elbow, so I made mine 43 inches tall, but you can adjust the height to anything you like. All required boards and exactly how to cut them will be generated for you along with the number of required screws. Give it a try! You can design your own table and follow these instructions for how to assemble it, or just follow along to build the same one that I did.
Thanks for taking a look at my Instructable. Please consider voting for it in the Tables and Desks Contest!
Step 1: Design Your Table
The first step is to design your table! Head over to my blog to use the widget. Note that the widget requires WebGL, which is active by default in all major browser, but your device must support it. It will not work on some older devices.
Once you're on my site, scroll down and you will be presented with an interactive 3D model of the table that we will be building in the following steps. You can adjust the settings for your table and a list of the necessary boards and how to cut them as well as the number of screws will be generated for you below the widget. Just modify the different parameters and click the Update button to get an updated 3D model and materials list. It's even mobile friendly, so you can pull it up on your phone or tablet rather than printing anything off. Here's a description of each parameter:
Table Width - The total width that your table will take up. Have a specific space in mind and an 8ft table just won't quite make it? Adjust this to the exact size for your space (max of 8 feet).
Table Height - Not 6'1"? Want a sitting desk rather than a standing bench? Adjust this to match your height needs. I recommend 3" below your elbow when standing for light work (soldering, small assembly) or 6" below your elbow for heavy work. This is the measurement from the ground to the top face of your table.
Table Depth - Want to use a whole 8'x4' sheet of plywood for your table top? Just half? Adjust this value to change the depth of your table to match your needs.
Backboard - Check this box if you want a backboard with a shelf on top. The backboard leaves a 3-1/2" gap between the peg board and the table top (so a 2" gap that cords can fit through). The shelf above the peg board also has a 2" gap between the frame and the shelf so cords can easily be run down to the table. Leave this unchecked if you just want a table.
Shelf Height - This measurement determines exactly how tall your shelf will be from the ground up. Keep in mind how deep your table is. While I can readily reach things on my shelf, I made it a little too tall to easily reach the power strips that I mounted to the top of the frame. This height and the table height determine the height of the peg board. The default settings make the peg board come out to 24" tall, exactly half a 8'x4' sheet.
Shelf Depth - How deep the shelf will be. The default value of 11.875" allows for both the 36" table top and shelf to be cut from a single sheet of 8'x4' plywood with an 1/8" kerf (saw blade thickness). Setting this to 0 will remove the shelf and the Shelf Height measurement will represent the height of the backboard frame instead.
Overhang - Suggested in the comments. This allows for you to design the plywood sheet to hang off the front of your table for easier clamping and sweeping debris off the table top.
After designing the table how you'd like it, follow the rest of these instructions for how to assemble your customized version of the table. If you don't want to go through the trouble of using the widget, the dimensions for the 2x4s, plywood and peg board as well as the number of required screws are listed in the images above.
Step 2: Tools
Next, gather your tools! These are the tools I used in this project:
Miter saw - Used to cut the 2x4s.
Impact Driver - Used to screw everything together.
Tape Measure - Used to measure everything. This one is especially thick, which allows it to span 11 feet or more while unsupported.
Combination square (optional) - The combination square was helpful when marking off lengths and getting a 45 degree mark. This one was a gift and is rather pricey, but there are suitable alternatives for less than $15.
Step 3: Cut Your Materials
Cut all your boards using the dimensions generated by the table widget (see step 1 for the dimensions I used). Everything will be labeled A-K or A-F if you don't want a backboard. The boards labeled F have two 45 degree cuts on the ends and the boards labeled I have a 45 degree cut on one end as pictured above. Your local hardware store may be able to cut the plywood and peg board for you (that's what I did).
Step 4: Build Table Top
Lay out the frame of the table top using boards labeled A and B and start screwing everything together, 2 screws per joint. I used 3" screws. The distance between supports varies depending on your configuration (see dimension I, in my case 23-5/8"), but they will be no more than 2 feet apart and are evenly spaced.
Next, place your plywood sheet labeled C on top, square it up with the frame you just built and screw it down. I used 2-1/2" screws to secure the plywood. I put a screw in at the edge of every support (just over from them, so I didn't hit the screws that were already in).
Step 5: Attach Legs
Next make each leg, by screwing together the 4 pairs of 2x4s labeled D using three 3" screws each. Flip the table top over, as we'll be attaching the legs with it upside down, but don't screw the legs in yet.
Before attaching the legs to the table top, we need to attach the crossing supports labeled E and F. Layout two legs, along with the cross supports as shown in the photo using spare pieces of 2x4 as spacers. The 45 degree cuts should be flush with the top of the leg. The height of the top of board E should match dimension II (by default 24-3/4"). Sink two 3" screws through the legs (D) into the horizontal joist (E). Sink two screws through each leg (D) into the 45s (F), one 2-1/2" and one 3" along. Attach each leg to the table with four 2-1/2" screws (2 on each side that the leg connects to the table). Once the legs have been fastened to the table, sink an additional 2-1/2" screw and 3" screw through the horizontal joist into each of the 45s. I made the mistake of fastening everything together before attaching the legs, and had to take out screws to fit the legs into the table top. The screws into the 45s, though, aren't accessible once the legs are in, so leave those in or use longer screws that can go through everything.
Step 6: Attach Backboard and Shelf
Now for the backboard. You'll need the 2x4s labeled G, H and I, plywood labeled J for the shelf and peg board labeled K.
Lay out your G and H 2x4s to start framing out the backboard. Space the joists using dimension I (in this case 23-5/8"). Screw everything together, using 2 screws per stud. I used 3" screws.
Place boards labeled I next to each joist that you just screwed together and attach them each with three 2-1/2" screws. The top of each shelf support should be 4-1/4" from the top of the frame. Once the plywood shelf is placed on top, there will be a 2" gap for power cords to fit through.
Set the plywood labeled J in place and attach it using two 2-1/2" screws per support. Then attach the peg board labeled K, using three 2-1/2" screws per support.
If you have a friend handy, this would be a good time to grab them. Lift the whole backboard assembly onto to table with the peg board down and the shelf hanging off the edge. Tip the backboard up, and get it flush with the back of the table. Hold it in place while you tack it in place with a 4" screw in the middle. Place two 4" screws on either side of each support, angling one of them back so they both are secured into the table's back 2x4 or into one of the joists.
Step 7: Fill It Up With Tools!
The last step is to fill your work bench up with tools! I also put two 4' power strips along the top, so it's easy to get to power anywhere on the bench. The chords can feed down through the gap in the shelf through the gap at the bottom to any devices on the table. Here's how mine turned out. This is the stool pictured above. It raises high enough to work well as a seat even with my 43" tall table top.
Thanks for reading along, I hope you enjoyed it! Please consider voting for my Instructable in the Tables and Desks Contest.
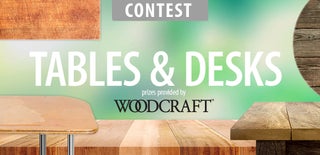
Third Prize in the
Tables and Desks Contest 2016