Introduction: High Power LED Under Cabinet Lighting DIY - Great Looking and BRIGHT @ Only 23w!
First off, let me explain that "High Power LEDs" should probably read "High Intensity LEDs". By my calculations this whole setup uses about 23w of electricity.
Anyways, after getting new kitchen cabinets and getting a nice shiny granite counter top installed it was time to get some truly impressive under-cabinet lights that would complement the design I was aiming for while being wonderfully functional as well.
This instructable is going to show you how I created my DIY under cabinet lighting for less than $120 and yet achieved professional results better than every commercially available system I was able to see in person.
This is a true DIY system, not a guide on how to install a commercially available system. So before starting, know that while I think this should be considered an "easy" project some basic skills are required such as being comfortable working around electricity (which can be dangerous!) and you also need to know how to solder. Other than that though there aren't any special skills or tools required.
Thanks for reading, now on to the good stuff!
-Aaron
Also, a special thanks to my dad, who helped me with this project.
Step 1: Design the System
Fair warning, this is the longest step! This is basically my thought process on designing the setup. Skip this step to see the materials list and build instructions...
Under cabinet lights can make or break a kitchen. They can add instant and real appeal to a space, but they have to meet certain criteria. They have to be effective task lights. They have to add the right "ambiance". They have to match up with your current lighting scheme, and finally they have to work well and last a long time (due to the fact that installing lights under your cabinets often requires some modifications - it's a pain to have to re-do it or constantly fix things!).
In designing my setup I was able to cross off the typical halogen puck lights almost immediately. They are bright and beautiful, but they have many weaknesses. They are too big, too hot, and as a result they don't last very long (plastic cracks, glass falls out, and bulbs burn out quickly). Probably the worst part about them is the horrible amount of wire needed to hook them up!
For me the obvious choice was LED.
Scouring the internet for project ideas turned up very few truly "DIY" LED options. Most DIY projects were related to installing a commercial product. I checked with local lighting stores and home improvement stores and found solutions that were either woefully inadequate or ridiculously expensive. I found some modular systems that came close to what I was envisioning, but I quickly came to the conclusion that I could build it to look and perform better, for cheaper.
I have some basic LED knowledge from building a light for my reef aquarium. Oddly enough I think that the reefing hobby has given a monumental push to high-power LED lighting in recent years. I've also messed around with some normal 5mm LEDs and such while experimenting with my arduino and other electronic gadgets. I am still by no means an expert...
With LEDs you need to keep a few things in mind. Namely, LED type & placement, power, thermal management, and color.
LED Type & Placement:
LED under cabinet lighting can be divided into 2 groups, strip lights and individual lights. The strip lights typically provide more even light throughout the surface (like a fluorescent bulb), while individual, or "puck" lights offer a more dramatic lighting source with varying intensities that start out really high when you're right under the light fading out as you move further away from the light.
I went through several designs for both and found that typically strip lights use smaller SMD LEDs mounted on a long, thin PCB or flex tape. These are nice, low-profile options, however, I found that they aren't nearly as intense as single lights. If I were to do a strip light application using LEDs I would use 2 rows to get enough light. Using 2 rows increased the cost significantly though.
I ended up settling on high power 3W LEDs, just like what are commonly used in reef lighting, specifically the CREE XT-E LED. They are very versatile, they put out a lot of light and there are several drivers that are perfect for powering this type of LED, especially if you want to get fancy with dimming (many support 0-10v dimming as well as PWM dimming). The important part is getting the spacing right to avoid shadows and to have the right thermal setup. I experimented quite a bit and decided that the best light was when the LEDs were spaced evenly apart under the cabinets about 12" on center. More LEDs than that and I would probably be wasting efficiency (because I would end up dimming it most of the time). Less LEDs than that I may be sacrificing some of the practical task lighting.
Power:
For power I went with a dimmable constant current driver. The LEDs I used have a 3v forward voltage @ 700mA, to wire them in series you basically just add up the total forward voltage (I used 11 LEDs so 3x11=33v) and make sure the driver you buy supports that voltage at whatever current you want. 700mA is a good amount of current because it has a good efficiency but the LEDs won't get as hot. The LEDs are rated to much higher than that, and while they do get brighter the more current you feed them, they get a lot hotter and the efficiency drops as well. I decided to use a reliable inventronics 40W driver.
A nice thing about this driver (and some others too) is that it's scalable. According to the datasheet @ 700mA it outputs a minimum of 18v and a maximum of 54v. This means that if you have 3v LEDs you can safely use a minimum of 6 LEDs and a maximum of 17 LEDs or so (you want a little wiggle room at the top range). By using the spacing I described above you could light anywhere from 6 to 17 linear feet of counter top! If you still need more LEDs than that, don't worry. Just look for a constant current driver that supports the voltage range you require. Just take your LED voltage at the current you want and multiply it by the # of LEDs you want to get the voltage requirement. Meanwell, Inventronics, and Phillips Xitanium are just a few. A LED driver takes your homes 120v power and converts it into DC power for the LEDs.
Thermal Management:
Thermal management is going to be important in a high power LED array, and while I thought about just using aluminum channel or flat bar from home depot I ended up with a much more elegant (and more effective) solution that didn't cost any more. I spent a lot of time searching for heatsinks and while I found a bunch, they mostly came from China or they were too tall for my application (I only have 3/4" under my cabinets). I ended up deciding to use a really nifty looking circular heatsink that was designed to be used with LEDs. A typical CPU style heatsink wouldn't work in this application because the heatsink has to be up against wood, so this design is perfect to get enough airflow. Best of all, you can get this heatsink in several different heights, and no drilling is required to mount the LED or the heatsink to the underside of the cabinet! It's the Ohmite model SA-LED-113E.
Color:
Let's not forget about color! This is probably the most important... I would deal with those crappy halogen pucks before I chose a fluorescent light for this exact reason. The color temperature is going to dictate the mood of the lighting as well as how good or bad things look underneath them. Imagine you're preparing some food on the counter and the broccoli looks brown... You're not going to want to eat that. Now imaging looking at broccoli that looks clean and bright green, as if you just harvested it. That's the power of selecting the right color light.
Warm white is the color most often chosen, and the color I desired for my kitchen. The kelvin range for "warm white" is between 2700k and 3500k. Warm white has the highest CRI (color rendering index) and IMO things look most true to life under this color lighting. I decided to stay on the slightly cooler end of the spectrum though, since I don't have many windows. I chose 3250k LEDs which I found correlate quite well to the "soft white" compact fluorescent bulbs that I use in the ceiling lights. On that note you need to try to match the color of your under cabinet lights to the rest of the lights in your kitchen or it will look funny. So you would either need to find the right color LEDs or you'll need to change out the other lights in your kitchen.
So those are essentially the principles I used to design the system. Depending on your space you may need to tweak some things, but I what I put together has worked out really REALLY well in my opinion and for my purposes.
Sorry that was a lot of reading, but it's important to spend the time to do it right and enjoy the results! I'm not going to upload all of my sketches, but the excel diagram is what I ultimately ended up with (1 square is 6 inches):
Step 2: Order Materials
Materials list:
- CREE XT-E 3W high power LEDs (3250k color temperature) Here's the datasheet
- 1/2" high individual circular heat sinks (Model SA-LED-113E)
- Inventronics 40w LED driver (Model EUC-040S70DS - Spec sheet)
- 10K ohm 1/2w Potentiometer (for dimming)
16-18 gauge copper wire (stranded is easier to work with - thicker wire for longer runs - Don't go thicker than 16 gauge stranded though as the wire could suck up enough heat to make soldering difficult)
1 package of stainless steel screws #8 x 1/2" (use in the M10 holes on the heatsink to attach the LED)
1 package of stainless steel screws #8 x 3/4" (use in the 1/4" holes to attach to the underside of the cabinets)
Thermal grease
Wire staples (small ones!)
Soldering supplies (thin rosin core 60/40 solder, wet sponge, etc...)
Some small wire nuts
Acetone to clean the heatsink & LED star prior to applying thermal grease
Total cost for materials for me was about $120 because I already had the thermal grease ($$).
Tools list:
Wire stripper
Power drill
Screwdriver
Soldering Iron (40W+)
A few pairs of pliers to hold things if they get warm
Paper towels or a clean cloth
I ordered the LEDs and driver from www.ledgroupbuy.com. They buy their LEDs in a group buy format so they end up being quite cheap and they arrive fast in the continental US too. The inventronics driver couldn't be any simpler. You wire it to AC power and attach the potentiometer. It will run up to 15 or so LEDs in series. I wanted to run the LEDs in series because it's safer and because I will only have 1 wire going between my LEDs.
For heat sinks I used a product by Ohmite that is LED specific and ideal for retrofit applications IMO due to the variety of mounting options for different kinds of LEDs. The design also seems to be well thought out and most importantly effective!
Everything else you can pretty much get at your local hardware store/radio shack.
Step 3: Arrange & Prep for Assembly
Once your materials are gathered it would be wise to test everything out. You can test the LEDs with 2 1.5v batteries or with a multimeter with a diode test function. It would suck to solder in a dead LED!
Tin the solder pads on the LED stars. Just heat the pads up and apply a little bubble of solder on them. You only really need to do 1 (-) and 1 (+), but since I was going to be potentially mounting them in different configurations I figured I should just prep them all.
Next, cut some approximate lengths of wire (a little more than you'll actually need between each LED) and strip one end about 1/8". You really don't want to strip more than that or else you run the risk of shorting out the LED if a little bit of solder or a wire strand contacts the aluminum star or the heat sink. Tin the ends with solder. If you do strip off more than 1/8" or you melt off some of the sheath then you can just cut the tinned wire down to 1/8". It may take some practice to do this quickly but it's not difficult at all.
Make a wiring diagram. I wired the LEDs in series, meaning the (+) wire coming from the LED driver goes to the (+) on the first LED. Then a wire goes from the (-) on the first LED to the (+) on the second LED. The (-) on the second LED then goes to the (+) on the third LED and so on... Finally the (-) on the last LED goes back to the (-) lead from the LED driver.
If you want you can pre-solder the wire lengths you made to one side of each LED (don't solder to both sides unless there are no holes to go through). You'll have to do some soldering in pretty tight confines if you are running your wire through the cabinets. I drilled small holes under the cabinets right up front so the wire is invisible.
Also, it helped me to pre-thread the #8 x 1/2" screws into the M10 slots on the heatsink because you have to use a bit of pressure to do this and it will be much harder to do while also trying to line up an LED. Then just back them off a bit so you can fit the LED in there.
Step 4: Installation
After everything was prepared the installation was pretty easy. I just took my time and went about things methodically.
First I ran AC power to the LED driver location, which I decided would be on top of one of the cabinets, in the back so that nobody can see it. It sits pretty low. I put a low profile junction box nearby and used wire nuts to complete the connections.
You can mount the potentiometer (the dimmer knob) wherever you want. They're usually pretty small (about 1" long or less) so it would be fine either underneath the cabinet, or you could get fancy and put it in it's own low-voltage box in the wall with a fancy aluminum knob and faceplate or something. Here's a link on how to wire in the potentiometer. It's super simple (Youtube).
Once the potentiometer is wired in you can run the (+) lead (or (-) lead depending on which way you're going) down through the gap in-between the cabinets (there should be plenty of room) and start soldering your LEDs. Pay attention to the orientation of the LED (you're going to have to flip it over at some point) so you can avoid the wires crossing all over.
Once you finish soldering you can test the LEDs, though I would only do it for a quick second to prevent heat build up and also double check all of your connections first. Be cautious with cold joints and other soldering mess ups. I actually wired in my last LED using the wrong polarity. Fortunately the driver is smart and has protection for that sort of thing but overall it's probably best to double check everything.
Clean the backs of the LEDs and the heatsinks with acetone or isopropyl alcohol.
Apply a small amount of thermal grease to the back of the heatsink and position the LED onto the center of the star, such that the screw won't contact any of the solder pads. Tighten down the screws. Once the LED is fixed in place don't over-tighten the screws. Doing so can actually deform the metal "star" the LED is on and reduce heat transfer.
Flip the stars upside down and use the 3/4" screws to attach the heatsinks to the underside of the cabinet. I actually pre-drilled my holes because I didn't want any possible cracking or other uglyness, though honestly I probably could have moved a lot faster if I didn't pre-drill the holes.
Once the heatsinks are mounted you can use some low voltage wire staples to secure little bits of loose wire. I cut mine such that there was hardly any slack, so I only used a few staples. Also I didn't use the nails, I swapped them out for some tiny screws.
Total time for prep & install was about 3 hours or so.
Finally, I've noticed that in a few places in the room you can slightly see underneath the cabinet which results in quite a glare. So I've experimented with some small plexiglass "diffusers" which should reduce this glare quite a bit. I'll add this step on once I finish them.
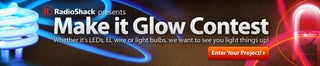
Finalist in the
Make It Glow