Introduction: DIY in Ear Monitors
In ear monitors, also called musicians monitors, are canalphones used to listen to music (or with respect to musicians, to hear custom mixes of vocals/instrumentation during live music performances or while recording music in a studio). They are custom fitted to the users' ears to provide superior comfort and bass response, as well as unsurpassed passive noise reduction (up to -25dB). They are also exceedingly expensive (an equivalent 3-way design from Westone or Ultimate Ears would probably run $1,000+), putting them out of the reach of the average music enthusiast. These aren't earbubs-turned-psuedo IEMs, this is the real deal. This article will show you how to make your own custom fitted in ear monitors for about 1/4 the cost of a professionally made equivalent.
Step 1: Tools and Materials
Obviously lots of variables here. I'll list the things I used, and then along the way explain why I used what I used and what some suitable alternatives might be.
Tools:
-Soldering iron
-A helping hands
-Utility knife
-Wire cutters
Materials:
From Mouser:
-Balanced armature drivers (Knowles Acoustic: (2) CI-22955-000, (2) DTEC-30008-000, (2) WBFK-30019-000)
-(2) 1 uF capacitors (Mouser part#: 581-SA305E105MAR)
-(2) 7.32 ohm resistors (Mouser part#: 270-7.32-RC)
-AMP female connectors (Mouse part#: 571-665059)
-AMP male connectors (Mouse part#: 571-665079)
From Earplugstore:
-Earmold impression kit
From Microsonic:
-Acoustic tubing
-Acoustic dampers (green ones and yellow ones; also available at Mouser)
From a quality art store:
-A mold making material (for making molds of the impressions; I used SmoothOn Reoflex)
-A body making material (for making the body of the IEM; I used SmoothOn Crtystal Clear; please see my safety comments regarding this product on page 4)
-Some copper stranded wire, whatever you have laying around
-And you'll have to either make a connecting wire, cannibalize one from some other headphones, or buy one like this. I originally made my own, but I couldn't find the same kind of small gauge, soft-jacketed wire, so I eventually broke down and bought a Westone cable that I ended up modifying. If you have a lead on the kind of wire use in headphones, but all means share it. If you use a wire that's too stiff, in addition to it being awkward you'll also get unpleasant microphonics.
A note on impressions: Please read this before attempting to make your own impressions. There is a potential risk of serious injury, including permanent deafness. If you're unwilling to take this risk you have the option of having impressions professionally made by an audiologist. Also, while Earplug Superstore sells a kit, complete with the impression material, syringe, bite block, and ear dams, it is also possible to by these materials from Microsonic (since you'll need to buy some supplies from them anyway). The syringe isn't necessary, though it is helpful. Biteblock isn't necessary, and alternatives could be used. You must use an ear dam, though you could easily make them yourself using some foam and string. Don't try to make impressions with anything other than materials specifically made for doing so.
A note on crossovers: If you'd like to read more about high-, low-, and band-pass filters, this is a pretty good introduction. I've also found a handy RC crossover calculator. The resistor and capacitor values you choose will depend of the impedance of your drivers and your desired roll off. For more complicated circuits, including how to (properly) wire a 3 way crossover (unlike what I did), check out this. But note that you cannot use inductors with balanced armature drivers (BA drivers have inductive coils in them, if you use inductive crossovers you'll get inductive coupling).
UPDATE - took me a while to find them, but the IEM connectors are called TF10. A quick search will yield lots of results.
Step 2: Making the Impressions
The impression making kit I got came with a two part foam resin, a syringe, and ear tampons (or at least that's what I call them). You stick the ear tampon down your ear canals with a Q-tip, mix the foam, put it in the syringe, and then use the syringe to fill your ear canal. You want to get the ear tampon in there as far as you can, about as far as you can get it without hurting (at some point, if you go too far it will hurt A LOT). Look at my hand little anatomy diagram. Your goal is to get past the external acoustic meatus. The foam stuff cures in like 10 minutes, and you just pop it out. The ear tampon should come with it, but if not there's a handy little string attached.
Step 3: Make Casts of the Impressions
Mix the mold making material, enough to submerge your impressions. SmoothOn Reoflex is urethane rubber, which is quite sticky, but the impression material is silicone, so they won't stick together. But since I used urethane plastic to make the IEM bodies, those two urethane products can stick together, sometimes permanently. You could use a mold release agent, or make the molds with a silicone rubber compound. But since the impression material is silicone based, those have a tendency to stick together as well = needing a mold release agent. Anyway, whatever you use, mix it in something disposable, because whatever's left might not come out after it cures. To house the molds, I used some shot glasses that I lined with plastic wrap, but if you can get little 2oz. disposable wax lined cups at the grocery store (sometimes they're called "bathroom cups,") that are the perfect size. To keep the impressions "floating" in the liquid rubber I strung some string through them and then taped the string to the shot glass. Another method I've used is to take long wood screws and screw them into the tops of the impressions, then clip them into a helping hands. After the rubber cures you should be able to just pop out the impressions.
A note before we continue: if you'll look at one of the photos here, you'll see an exploded diagram of a Westone earpiece. Notice that the body of the earpiece is actually a hollow shell that the internals sit it, and the shell is sealed by a lid (called a faceplate). I didn't have any easy way of making a hollow shell, so I my design actually encapsulates all of the electronics in the earpiece. This obviously means that after they're done they can't be serviced (easily). The way they make the shells isn't a secret, but getting your hands on all of the tools and supplies would be difficult and expensive. But this is DIY, so try and make 'em hollow if you're feeling crafty. Two methods: 1) If your compound cures relatively quickly, fill you impressions, then pour out the excess. Now that the entire inner surface is evenly coated, slowly rotate them until it hardens. 2) If your compound takes longer to cure, do the same to coat them, but then wrap them up in plastic wrap, put them in a plastic bag, and throw them in a clothes dryer, set to air (no heat), and let them tumble away. Again, just be aware that moving forward I did not make hollow shells, and the methods for installing the internals will be quite different if you end up making a hollow earpiece.
Step 4: Construct the Internals
Lots of flexibility here. I wanted a three way design, with a woofer, mid, and tweeter. You could obviously simplify things and make a one way earpiece, and at $25-$50 per driver, that would save you quite a bit of money. However, if you're going to the trouble of making yourselfcustom IEMs you might as well go the distance. The drivers I used were based on a few things: drivers known to be used in commercial products, frequency response curves of the various KA drivers, and availability. I went with CI (~$27) as my woofer (this is a common application), DTEC (~$48) as my mid, and WBFK (~$48) as my tweeter. TWFK (~$50) is commonly used as both a mid and a tweeter, and has the added benefit of being a dual driver, but it was unavailable at the time. I chose DTEC because of its frequency response and because it's also a dual driver. WBFK is basically the single driver version of TWFK, and has a nearly identical frequency response. The capacitor acts as high pass filter (blocking low frequencies) for the tweeter, and the resistor a low pass filter (blocking high frequencies) for the woofer (there's more about this back on page 1). Additional shaping of the output is achieved via the acoustic dampers.
**Update** Through digging around on the Knowles site, it appears that TWFK is not simply two WBFK drivers sandwiched together. It consists of one WBFK driver and another FK series driver, and they claim that it's internally crossed-over, which means that's it's a mid AND tweeter in one package. And since TWFK is the same price as WBFK, that makes it a pretty good deal. It also means you can make a two driver earpiece with TWFK and CI and still have a three way; this is the setup I would recommend.
First, using some glue (I used an epoxy) attach (and fully seal) a length of acoustic tubing to the driver (about two inches; be sure that your glue doesn't actually get in the tubing, above the output of the driver). Ultimately, you want to woofer to have the longest length of tubing, and the tweeter to have to shortest, but don't worry about this right now. Just give yourself extra to play with later. You can pop in the acoustic dampers if you want (green in the woofer, yellows in the mid and tweeter) or wait till later. Next, solder leads onto all of your drivers. In some of my photos you'll see that at first I went to the trouble of insulating all the connections to each driver, only to surreptitiously discover that, for some reason unbeknownst to me, it doesn't matter. So what I later did was use the capacitor as a lead for the tweeter, a resistor as a lead for the woofer, and for all other leads just a single strand of copper wire (you can kind of see this in the first photo). I think you want the caps and resistors to be used as anodes, which is what I did, but I'm not an electrical engineer, so if someone knows more about this please correct me. Next, join all of your anodes together and solder into one of the female connectors, and then do the same for the cathodes. You have the option here of bypassing the connectors and just soldering the connecting wire directly to the leads (I don't know why, by IEMs always have connectors, so I followed suit). After the leads are soldered to the connectors you have to "seal" the connectors with shrink tubing (female connectors are hollow, and when you pour your casting resin over the internals they will fill up if they aren't sealed). Again, ignoring that my connectors are insulated in some of the photos, you should end up with something that looks like picture 3. If you've made your own connecting wire, you should be all set. If you've cannibalized one, or bought a Westone cable, you'll have to make the male connectors that corresponde to the female connectors in the IEMs, so solder the male connecters to the ends of the wires and fashion some kind of termination. Next, test 'em out. Plug the connectors into your connecting wire and crank up your iPod. Test that each driver is working by blocking the tubes from the other two. If you want to actually test them out in your ears you can take some foam earplugs, fillet them, insert the tubes, and then carefully insert the earplug into your ear. Keep in mind the bass might not be that impressive if you don't get a good seal. Once you're happy everything is working you'll need to fit the internals into the molds. Before you can do this, you'll have to make a hole in the very bottom of each mold, at the tip of the "ear canal" for your tubes to come through, a la photo 5. The two easiest ways to do this are 1) go back in time and position your impression in the shot glass with the end of the ear canal right next the to edge of the glass so it's easily located, or 2) take a bread knife and cut off the bottom of the mold such that you just barely expose the end of the canal (I chose option 1, minus the time travel). Once you have your hole you can feed the tubing through and then situate your internals, keeping in mind that you want the acoustic tubing from the woofer to be the longest (about two inches from where the opening will be at the tip of protrusion into the ear canal to where the driver sits in the earpiece), the followed by the midrange (about an inch), with the tubing to the tweeter to be the shortest (about half an inch). Now, flip your molds upside-down (like photo 5) and seal around the tubing (the spaces between the tubing and the mold) with some epoxy. IT MUST BE SEALED or it will leak when you pour your resin in the molds.
A note on the SmoothOn Crystal Clear: I wanted a clear earpiece so I could admire my work when I was done. However, there aren't a ton of products out there that are optically clear. What the pros use is an acrylic compound that is actually cured by exposure to UV light. Acrylic is completely, 100% inert to the human body; it's used to make medical device implants precisely for this reason. The SmoothOn Crystal Clear is not acrylic, and is not inert to the human body. It's a urethane plastic, and urethanes contain chemicals called aliphatic isocyanates, which are potent antigens. I learned this the hard way when, after a week of using these for the first time, ended up in my doctor's office because my eyes and ears were swollen shut. What I ended up doing was coating them with nail polish, which has worked fine, no more itchy ears. But if you don't want your IEMs to be clear, find something else to use so that you don't have to deal with this. If you decide to work with the Crystal Clear be extremely careful: use chemical resistant gloves and a respirator when dealing with the liquids, when handling them after they've cured (ESPECIALLY if you need to sand/smooth/shape them), and until you've coated them with something inert (like nail polish).
**Update** I've found a source of crystal clear liquid acrylic casting resin: Electron Microscopy Sciences.
Now then, time to take the plunge. With your internals in the molds, and the tubing sealed at the bottom, connect your male connectors from your connecting wire into your female connectors like in picture 6, and using the helping hands, position the connectors where you'd like them to be (the are typically located where I positioned them). Once you have everything the way you want it, pour in the material you're using to make the body. In the last photo you'll see what the result should look like.
**Update** I've included a recommended wiring diagram for a two way design from Sonion.
Step 5: Finish Them Up
I ended up tinting my resin with some purple enamel (while it was still liquid), otherwise they would have been crystal clear. When they first come out of the molds they are very rough and jagged, like picture 2 except the excess tubing will be sticking out. Obviously cut the excess tubing. They take a bit of finish work before they're ready. First, do some light sanding to get them smooth (picture 3). If you're working with the SmoothOn Crystal Clear, since they'll need to be coated with something (like nail polish), you can be a bit more aggressive in how much material you take off (since the coating is going to make up the difference), but be very careful not to distort the contours too much (those are the contours of YOUR ears after all, and that's kinda the point). One area that took some shaping for me was the curve at the area that corresponds to the external acoustic meatus (as you can see in picture 4). I made some blanks before I did the real thing, and noticed that I couldn't comfortably get them in and out of my ears with this protrusion (or course, everyone's anatomy is going to be different, and you might not have such pronounced landmarks). Whatever material you end up working with you'll need to give them a coating of something at the very end anyway. This is called build up. You actually want them to be a bit bigger than your anatomy to ensure that they seal. But again, there's some finesse involved here as you're removing/adding material, and potentially making the final product too big or small: Too big, and you're going to feel pressure that over time will become very uncomfortable; Too small, and you won't get an adequate seal needed for both bass response and noise reduction. As an added bonus, you now have the chops, and impressions of your ears, to make yourself some custom earplugs.
Now, time to enjoy the greatest sounding headphones you've ever heard...
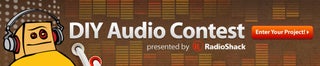
Second Prize in the
DIY Audio