Introduction: DIY Magnetic Hand-Saw Guide
UPDATE: I've made a magnetic saw guide that's even better! It's stronger, more compact, easier to use and even more accurate! You can also cut miters with it!! Check out the video:
https://www.youtube.com/watch?v=IDGZmSuTRfE
-
I think handsaws are WAY better than circular saws for many reasons, but I always come across one problem: I'm never able to saw perpendicular, aka square, at a 90° angle. You can see the example for this here.
I have (finally!) received the saw that I won back in the 2015 Shelving Contest with my Ultimate Magnetic Pegboard. It's extremely sharp, beautifully made, and has a really comfortable handle. However, it is very thin, and doesn't have any aligning support on the top, so it bends really easily while sawing.
A well known solution for this is a Miter-Box. I've bought one, but it just doesn't work. Instead of having the sides hold the saw, I just saw into the plastic...
One day I was daydreaming a bit: "If I take that magnetic dovetail jig that I saw in one of Jay Bates' videos, and align it differently, will I be able to use it for sawing at 90°, perpendicular, and square to the wooden board that I'm sawing?" So I do a quick search and: "Wait, WHAT? It costs 50 DOLLARS?"
"OK, nevermind. I'm making my own!" I decided that I'd make myself a magnetic guide, which ensures that the cut will be square in all directions. Alternatively, you can modify it, and use it for dovetails, miters, or anything else.
Let's get started!
Tired of skipping through boring DIY videos? In case you don't already know, I now make short, tightly edited Youtube videos about homemade tools, tool hacks, woodworking, electronics, metalworking projects and much more - Subscribe to so you don't miss out! :)
Step 1: What You'll Need
Below is a list for everything you'll need to complete this project. If you don't see something that you think should be here, please let me know in the comment section below. If you would like to know more about a specific tool/part that I used, feel free to ask in the comments.
-
Hardware & Materials:
Salvaged 90° piece of wood
Neodymium magnet (salvaged from an HDD)
Moist paper towel
Synthetic towel
-
Chemicals & Adhesives:
Epoxy
Alcohol swab
Contact cement
-
Tools (+Attachments):
Handsaw
Speed square
Pencil
Clamps
Glue mixing stick
File
Silicon carbide sandpaper
-
------------------------------------------------------------------------------------------
Subject: Woodworking
Recommended Safety Equipment: Respirator
Approximate Time: <2 Hours
Cost (for me): FREE
Difficulty: Fairly Easy
Step 2: Choose Your Magnet
Choose your magnet! I recommend using a magnet that is stronger than what you need. You see why in a few steps...
I found a magnet that I had salvaged from a hard drive which I thought would work well.
I don't have a pictures of removing the magnet from the other metal part (ferrite?) because I did this a long time ago, but Ben has a great tutorial. See step 1.
Step 3: Choose Your Piece of Wood
Since I didn't have a saw that can actually saw wood accurately, I needed to find a piece of wood that was accurate. I looked through my collection of wood until I found an accurate one, which happened to be a leg of a chair that I had taken apart. This chair was made of European Beech.
If you're going to be taking apart a chair, I really recommend Making your own (non) Dead-Blow Hammer, since most chairs are made with mortise and tenon joints, which are very strong. I did a quick measurement with my speed square to make sure that it was square...
Step 4: Sand!
I sanded both the endgrain of the chair, and the magnet, until I saw that a bit of material had been removed. This is a very important step, because it allows the adhesive to adhere significantly better. I used silicon carbide sandpaper, which I estimate was about 200 grit.
While sticking the magnet in some dirt, as an attempt to clean the magnet, the thing that was funny was that the dirt actually stuck to the magnet! A wet paper towel did the job better...
Step 5: Epoxy-ify Them Together!
I cleaned the magnet thoroughly with an alcohol swab, and mixed some Epoxy (more like WAYYY too much). After that I used a screwdriver to apply it onto the magnet. This was another mistake, as the screwdriver kept sticking to the magnet, which of course, did its job very well :)
I finally stuck the magnet onto the wood, and cleaned the part of the magnet that was exposed.
Step 6: The Anti-scratch Cloth
If I recall correctly, these magnets are made of really hard material, meaning that they might scratch the saw. The magnet is also really strong, so I thought it would be a good idea to reduce the friction somehow.
After letting the Epoxy cure for a few days, I got back to work. I found some type of synthetic towel, which I thought would work well.
I cut it to the size that I wanted, and applied contact cement to one side, and onto the magnet. About an hour later, I stuck them together.
Step 7: Cut Off the Excess Wood
As you might remember, the piece of wood that I used was an old chair leg, meaning that it was pretty big.
First, I clamped the guide to the table, and then started cutting it. I made sure to leave enough space so it would be easy to use in the future...
Here, you can see why you MUST wear a welding mask when I saw!
Step 8: DONE! | How to Use It | Examples | Video!
DONE!
If you LOVE watching horribly edited videos, you can click here to watch my video about it. If you liked it, make sure to check out my new YouTube Channel, as I upload quick videos of my projects in action, and more!
To use it, first, you need to mark a line, which represents the angle that you want to cut. This can be done with a speed square. After that, you need to clamp both the guide, and the board onto your workbench. Nw you can start sawing! You'll be amazed at how accurate the cuts are!
Do whatever you want with it: crosscuts, dovetails, miters - Anything!
-----------------------------------------------------------------------------------
Don't forget to Follow me on Instructables, I have over 80 Instructables that I'm sure you'd like!
DON'T BE SHY! Liked it? Let me know! Didn't like it? Let me know why!
Are you a hand-tool expert? Leave your handsaw tips in the comments below!
I read ALL comments, and reply to as many as I can, so make sure to leave your questions, suggestions, tips, tricks, upgrades, improvements, and any other ideas in the comments below! - Thanks!
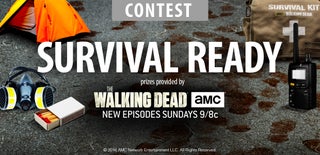
Participated in the
Survival Ready Contest
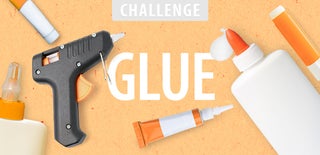
Participated in the
Glue Challenge 2016