Introduction: DIY PCB Using Liquid Photoresist
I have been an avid electronics DIY guy for many years now, and I have spent a lot of that time struggling to learn how to make my own PCBs. I have tried every technique that I have come across on the internet, from iron-on print outs to dry photosensitive blue sheets. Sometimes I was successful in my efforts to make a passable PCB, but when it was time to reproduce those results, something would go wrong.
After a lot of attempts and frustration, I was determined to find a solution that didn't result in me sending my files off to a PCB fab house. I use a fab house after I have tested a design on a homemade PCB. I finally found a solution where I can reproduce aesthetically pleasing PCBs by using liquid negative photo-sensitive paint. In this Instructable, I will share with you a technique that I have developed to do this.
DISCLAIMER:
Hazardous chemicals are used in this tutorial and I am not responsible if you hurt yourself. Practice caution, follow common safety guidelines at all times, and use gloves and protective eyeware.
Step 1: Supplies
Gather the supplies needed.
1. Photosensitive paint
2. Small spatula
3. Mixing jar
4. Heat plate ( optional )
5. Silicon or plastic tongs
6. Protective gloves and eye-ware
7. Copper clad board
8. Scale ( optional )
9. Plastic container for etching
10. Aquarium pump with stone diffuser and hose
11. Inverted PCB artwork printed on a laser transparency
12. Paint brush
13. Jar to put the developing solution in
14. Clear plastic or glass plates and some clips
15. Chemicals:
Hydrochloric acid (aka Muratic Acid from hardware store in the pool section or also found as a concrete cleaner)
Hydrogen peroxide
Sodium hydroxide (drain cleaner)
Sodium carbonate (aka Washing soda found next to laundry supplies)
Acetone
Step 2: Paint
I got the photosensitive paint off ebay. (Use the tag "Negative Photoresist" in your search.) The paint is very thick and needs to be diluted. Pour some of the paint into a small glass jar, add a few drops of acetone and stir with the spatula. You want it to be a little bit thinner than it was originally, but not too thin. If it's too thin, stir it and it will get thicker as the acetone evaporates. This paint smells bad, so I recommend that you do this step outside…but not in the direct sunlight or you will ruin the paint! Do it under a car port or in the garage with the door open, making sure you have a lot of ventilation.
Pour a small amount of the diluted paint on your copper and use the spatula to spread it onto the board. You want to spread the paint evenly across the surface while trying not to leave any thin areas of paint. This can be tricky and takes practice. Initially, I tried a paint brush but it left streaks that were hard to remove. I got much better results with a spatula.
Next, you need to let the board dry out. This takes a while and I found that I could speed up the process by placing the board on a heat plate overnight. I used an old coffee maker that was about to be thrown out before I realized that it could be repurposed as a heat plate. I simply cut off the top portion off the coffee maker with a hand saw. I had an aluminum plate lying around, so I placed it on heat plate, put the freshly painted board on top and then put the whole thing in a dark shed, where I let it set overnight.
If you're starting to think that this process is going to take too long, remember that if you want quality results, patience pays off here. You have to take your time - rushing this will lead to problems. While you don't have to use a heat plate and can simply let the painted copper sit in the dark, it will take even longer to dry out.
Step 3: Expose
If the coating looks too thin after drying, apply a second coat and let it dry out. I use CadSoft Eagle in my designs and when I export a PCB image, I make sure it's inverted. In the Cam processor under "Device" I select, "PS_INVERTED", turn on layers 16,17,18,20, and 45. I use OSX, so when you open the Post Script file, save it as a PDF. When you print this PDF, go into the properties tab and make sure you print it as its actual size and print it out black and white.
For best results I used 3M laser transparencies for laser printers. The paint needs an inverted image since it is a negative photo resist. This means that wherever UV light hits the blue paint, that exposed area will not be washed away by the developing solution.
Now it's time to expose the plate to UV light. I use two transparent plastic plates I got at "Tap Plastics". Place your board on top of a plate, then place your printed transparency toner side down on top of the board, then place another plastic plate on top being careful not to move the print. Use some clips to hold everything in place. I label the PCB in Eagle with that project's name somewhere on the PCB so when you place the toner side down you can read the label. That way you know it's positioned correctly. If the text looks mirrored you put it on upside down and need to reposition it.
Another reason to position the printout with the toner side down is because if you had it the other way around, the thickness of the transparency would allow light to leak through and ruin the exposure. You don't need any fancy UV exposure rig. A simple florescent light will work just as well. Place your sandwiched plates within ten inches of the light and set a timer for 5 mins. When the timer goes off, rotate the plates for uniform exposure. Do this three times, for a total of 15 mins exposure time.
Step 4: Develop
Make the developer solution by mixing one gram of sodium carbonate (Washing Soda) with one liter of water. It's ok if you don't have a scale, just use the picture I posted as a reference and eyeball it. Place the board in a plastic container and cover with developer. Let it sit for 15 mins, then use a paint brush to wash away the unexposed areas.
This is another time consuming process and it takes a while for the developer to finish removing the unexposed areas. What you are doing is using soap to wash away the unexposed areas. If you use too much sodium carbonate, you run the risk of washing away the exposed areas too, so don't make a strong solution. Sometimes the solution turns so dark that it becomes opaque and hard to see, so when that happens, I remove it and add fresh solution. The developing process creates off gases that smell bad so make sure you have good ventilation and use protective gloves so you don't get the solution on your skin.
Once you finish developing the board, rinse it with clean water and set it out in the sun to harden. Once it's dry, it will be ready for etching.
Step 5: Etch and Strip
Now it's time to put your gloves on and mix one part hydrochloric acid with two parts hydrogen peroxide. Always add acid to water, so add the two parts of hydrogen peroxide into the plastic etching container first, then add one part of acid. Place the aeration stone inside the solution and place your board in the solution. The bubbles will speed the etching process, and you can expedite the process further by using more aeration stones. The bubbles also assist in adding oxygen, which helps replenish the solution. You will need to flip the board during the coarse of etching for better coverage. When it's done, wash the board off thoroughly with water. Now is an optimal time to drill the holes. I use a .040 size drill bit for this part.
Prepare the stripping solution. With your gloves ON, add enough water to a large frying pan to cover the board and then add about three tablespoons of sodium hydroxide. Slowly heat the solution on the stove, then place your board inside. After a few minutes of simmering, the blue parts will detach from the board. Use tongs to remove the board and rinse with cold water.
****WARNING WARNING!! ****This boiling hot caustic solution is EXTREMELY DANGEROUS and will strip your skin off if you accidentally spill it on yourself!! The solution also gives off gasses. You do not want to breath it in, so make sure you have good ventilation during this process. In addition mixing hydrochloric acid with hydrogen peroxide produces poisonous chlorine gas. I etch boards outside and have the water hose close by in case of an accident. Work slowly, keep your gloves on and be VERY careful. Just in case, make sure you have a bottle of vinegar close by to pour on yourself in case you spill some caustic solution on you. This will help neutralize it. On the plus side, it will make your pan nice and clean - so if you have a dirty pan, use that one.
Step 6: Done
Well, that's it. Now you are ready to build your project. I hope this Instructable has been useful. Good luck! Now go build something cool.
Note:
I reuse the etching solution. After a few uses the solution will turn a dark green color or even brown. If you simply leave the the solution bubbling with air, it will turn back to a lime green color and be ready to use again. You can also add a little more hydrogen peroxide.
If you don't plan on using it again you can neutralize it by diluting baking soda ( sodium bicarbonate ) in water and then adding it to the etching solution. You will need a lot of baking soda solution to deactivate the acid. You know its done when the solution can not etch anymore. You can also test the PH, and when it's at PH 7 its done. Take the remains of all solutions in this tutorial to your local hazardous waste disposal facility. Do not pour it down the drain!
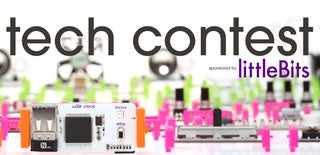
Participated in the
Tech Contest
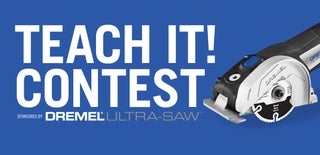
Participated in the
Teach It! Contest Sponsored by Dremel