Introduction: DIY Rolling Tool Chest
I have always envied the professional grade mechanics tool chests. You know the type, usually glossy red or black, steel, fancy name branded beasts. They are great.
I recently had a chance to help my Dad at the shop where the company he works for takes care of all their 18 wheelers. My Dad's diesel mechanic friend has a huge $15,000 or so blue snap on chest with umpteen million cubic inches of storage space, pneumatic tire wheels and a hot tub for you and five friends. No but it is a nice dark blue color. The drawers glide like silk even with 100 plus pounds of sockets and rackets and so on. I wanted something like that before I ever had a chance to use one of such caliber.
In fact I already had a sheet of 3/4 inch plywood leftover from building table saw and miter Saw tables that I planned on creating tool.storage or an assembly table out of.... The ease of use that big blue box gave me and my need for more storage beat out assembly table. Onto building my tool chest.
As I am a bit of a jack of all trades I have many tools for many shop disiplines. Some automotive, some metal working, but my main focus is wood working.
Wood working for me involves power tools. I appreciate and own enough hand tools like chisels and planes to do a few things but call it lazy or just too busy with life and work I prefer power tools. The problem of wood power tools is that they don't fit well into commercial style steel tool chests on average. Now I know the super expensive range includes a deep drawer or cabinet that could fit a circular saw and some of that nature.
I don't have thousands or even hundreds of dollars to spend on tool storage. I also need it to fit my needs, space, and style.
Step 1: Design
My design criteria were pretty standard. Maximize plywood to use the least amount of wood but come up with the most usable space to save money. Fit all my current tools and have room for more. Also fit in my shop space and be more than just a chest.
I started by going through all my scrap wood to clean it out and minimize how much wood needed to purchase for this project. I will go deeper into that with the materials section in the next step.
I made a quick sketch on paper to pin down the measurements. It helped me to know how many drawers and how deep they needed to be and how to cut the wood onto the most effecient pieces with no wasted drops.
For tool fitment. I have got to the point where my current organization system is not finding proper, convenient homes for my tools. Things were getting out of hand. I knew I wanted drawers for sockets and wrenches, another for air nailers/staplers and their hardware, one for big power tools like circular saws and belt sanders, then areas for misc hand tools and such and finally room for expansion.
As far as being more than a chest, the size I picked make the top of the 4 ft tall chest perfect height for detail work. I can stand next to it and it's just below eye level. Great for soldering or detail painting. It's also 3/4 inch plywood shelf basically so I can set stuff on it, unlike a think sheet metal lid that comes on top of many cheaper store bought chests.
Step 2: Materials
I had a full sheet of 3x4 inch MDF from a previous project taking up a ton of space on my scrap wood rack. I also had several other drop peices that I wanted to use up. This was part of the inspiration for the build and helped keep it cheap for me today since I had bought a large amount last spring.
All in all if your going to build my exact chest you will need 3.75 sheets of plywood.
The cabinet frame took 1.25 sheets total. The six drawers I built took 2.5 sheets. I bought 1/2 inch cdx grade plywood for my drawers. I had enough scrap wood to use 3/4 bottoms on two drawers and the rest were with the 1/2 plywood
I also used 22 inch full open drawer slides. I got mine off eBay. the more you buy the better the deal. I bought a ten pack when I built my daughter's dresser storage bed this fall.
On the bottom I used 4 four in swivel casters. Ebay or harbor freight have good deals on these as well.
In total the 2 sheets of half in. ply were 38, the .75 ply was (including scraps) 25, the drawer slides 20 and wheels 15. I maybe have $100.00 plus time into this tool chest. It has approximately 35,000 cubic inches storage space.
In comparison harbor freight has a 72 in wide, 18 drawer, tool chest with 34,200 cubic inches of space for $1199.99 at time of writing (Feb 2016). That's not a bad deal for a huge hight quality box but I like my price better. Also for 1200 bucks the biggest drawer would be a tight squeeze for a circular saw let alone all the other stuff I wanted to out in mine.
Step 3: Time Lapse Video
This is something I am just testing and practicing. This video condenses the whole project into a few minutes. It's not the greatest quality but I feel it shows the whole process in an easy to understand manner.
Step 4: Chest Construction
NOTE: All the photos for this step are pulled from video frames.
A chest is (like many carpentry
projects) just an open front box. Also the drawers are open top boxes. The ability to build wood into a box is often the way to build most anything. It could easily be argued that a wood framed house is still just a wood box.
To make it simple in words I used my design cut list and cut out all the pieces and then used an 18 gauge narrow crown stapler with 1.5 inch long staples to quickly assemble the entire box. Then I went back through with a drill and 1.25 inch drywall screws to give it more strength. I would have used glue but it was too cold in my shop for my particular brand of wood glue to actually work. I'm not too worried though.
1. Cut out all the peices. I use a table saw when I can to make sure all the peices are the same size and square. Otherwise use a good strieght edge clamp to cut a good cut with a cicular saw or jig saw.
2. Lay the biggest side down and then set a perpendicular side next to it. A 90 degree clamp may help hold it up.
3. Fasten together. I use an air stapler to lightly secure the. go back through with screws for a stronger connection.
4. Repeat until the box is complete.
5. At this point I attached the caster wheels on the bottom.
Step 5: Drawer Construction
The drawers are just tiny version of the chest. It's a bottom and 4 sides. I set my table saw and did all the same sized peices at once to try and be very consistent. Consistency is very important when installing drawer slides.
When assembling the drawers I used a pair of 90 degree clamps to hold the sides of the drawer to the bottom while I put in staples. After the drawer was assembled I put in screws for extra strength.
1. Cut out drawer bottom.
2. Cut out all four sides.
3. Place one side onto bottom and secure on each end with a 90 degree clamp.
4. Fasten with staples, nails, or screws.
5. Using 90 degree clamp attach opposite side.
6. Slide remaining sides in and fasten.
7. Attach drawer slide onto drawer.
Step 6: Drawer Slide Installation
Drawer slides have very little tolerance for error. I honestly hate them. I love using them when they work but making them work right is a bit hard. This is my third time making slide drawers and it is getting easier but lots of fuss.
Being accurate in measurement, cutting and assembly is a must. It can be very frustrating. Toil not though as I have a few tricks. If you feel you will err, err to the tune of the drawers being a little too small. Drawers too wide will need to be cut down. I have sanded, routed, and planed drawers to fit... It is hard, messy and if you hit a metal fasteners it ruins blades and tools. Try to avoid all that by going a tiny bit too small instead of too big.
Why small you say...? Because shimming the drawer slides to fit is not terribly hard. I have found that small washers make for fine drawer slide shims. If you need more than 3 washers to shim then upgrade to laun underlayment plywood or wood paneling or even thicker 1/4 plywood.
The best trick to use a washer as a shim is to put it on the slide pieces that attach to the cabinet frame. Do this by using packing tape to adhere the washers over the screw holes on the backside of the slide unit. Bonus tip: Use a marker or sharpie to color in the hole on the tape over the washer to make that mounting hole easy to recognize. Most slides have many holes but you only need to put screws in a few of them.
This is a fast, cheap, easy way to shim out a drawer slide some small fraction of an inch.
Trick on proper spacing of drawer slides installation onto cabinet frame. This is a technique I picked up from instructibles member seamster on his ible
https://www.instructables.com/id/Project-ideas-to-organize-your-garage-workshop/
.
Basically use a piece of wood as a measurement transfer guide. The wood acts like a jig in the manner that both the front and back of both left and right slides are all equal distance from the previous slide. I hope that it's easy to see this in the video and stills and also seamster's ible shows it well also.
To reiterate... Cut a price of scrap wood that is taller than your drawer. (I added .25 inch approximately)
place it onto the drawer slide below so it stands up vertically and hold your next slide tight on top of it. Secure front with screw. Repeat with back. Repeat with other side. Move up to the next drawer.
Tip for the bottom slide. Use a piece of .5 inch plywood as a guide to keep the slide off the bottom of the cabinet and so that the slide is equal distance on each end front and back and also both sides.
Be very careful inserting the drawers the first time. If they don't fit don't force. Be calm and search for the problem. Add or remove shims until everything slides nicely. Also a but of wd40 may help if you get a lot of dust on your slides or accidentally rubbed off too much of the factory grease.
Step 7: Finished Chest
Yeah its not the most beautiful tool chest in the world. I may had finished wood faces and glossy paint to give it a pro feel. Or I may leave it like this. It works great and does what I built it for. And it was cheap in comparison to buying on off a showroom floor.
Things I may add...For starting I am using cardboard to organize some of the tools inside. I can get tons of it free from trash at work. Once I get to a point where I am happy with how I keep the tools inside I will begin building wood organizers.
At that point I may also add a second layer system. Sliding trays inside of the drawers for more storage.
I might also add a rim to go around 3/4 of the top so when u roll it around nothing falls off.
Thanks for checking this out. Let me know what you think and what you would do differently. Also any feedback on the time lapse would be great. This is my first try at something like this. I know the lighting and image quality are not awesome but I will improve with time.
Also sorry for the wired placed... especially where spaces go. my phone is terrible at hitting the wrong button or auto correcting the wrong words.
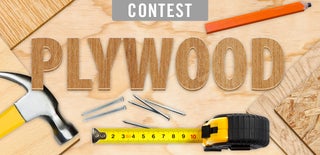
Participated in the
Plywood Contest
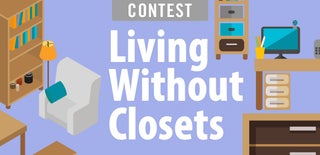
Participated in the
Living Without Closets Contest
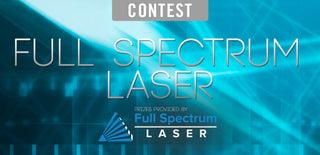
Participated in the
Full Spectrum Laser Contest 2016