Introduction: Design Your Own Reference Bookshelf Speakers
A few months back, I went into a big box consumer electronics store and wandered back to the elite section. Curious about the fuss, I asked the man to play some music through a pair of fancy $2000 speakers. Wow. I had no idea that music could sound that good.
As any DIY person would do, I looked closely at the construction and materials. It was top notch, shiny, well-finished--as expected for the price. Hmmmm...this was just lacquer or veneer covered CNC'ed MDF (Medium Density Fiberboard). As I have a CNC machine at home, I searched the internet. I was surprised at the extensive resources available to build custom speakers for 10 cents on the dollar.
This might be doable.
First, a shout out to noahw and his instructable How to Build Custom Speakers. I think that's the first link I found after visiting the big box store. That got me started with the online resources I needed. My goal here is to complement his resource and demonstrate how to design your own bookshelf speakers; specifically, how to use Sketchup and a CNC machine (or power tools) to design and build a better set of bookshelf speakers. It's a logical step to imagine using these skills to build a full size house-shaking, mind-blowing, floor-standing set for your home theater.
You could build a wooden box, cut some holes in it, drop in the speaker drivers and make a visually pleasing enclosure. You might get lucky, and it will sound great. However, without taking into account the technical details and specifications of a particular driver or driver set, you'll have no way of knowing if your box sounds the best it can sound.
My goal here is limited. I am not going to wind my own crossovers or get into the weeds about how to break down which frequencies get distributed to which driver. I am going to start small. I do have my mind set about building a full size house-shaking, mind-blowing, floor-standing set eventually. :)
The amount of technical expertise, knowledge, and opinion available is astounding and intimidating, but you have to start somewhere. This is where I started. Your constructive comments are welcome. I will update my instructable as needed.
Step 1: The Goal
My goal is to build a nice computer or bookshelf speaker set with a small amplifier. I want to build speaker enclosures with a nice set of drivers that expose some of the fine details and texture of good music without being too shrill or too boomy.
This project did not happen in one fell swoop. I made lots of calculation errors, ruined a bunch of MDF and redesigned them multiple times. I still don't know if I got it right. But the process is part of the fun.
For this project, I have released my files, but if you want, design and build your own with your own specific drivers. With respect to the tools that you have access to, you may need to design your enclosures differently. A table saw, router, and scroll saw could replace the use of CNC machine with some design changes. Even hand tools used with skill could build an accurate box. However, I am going after technique and method. Hopefully these instructions will carry over to your specific project.
There's some math involved, and I am trying to be accurate. Accuracy is only important as far as planning goes. Your ears may not even be able to tell the difference between good and perfect. The humidity of the air, the moisture in the wood, and even your personal preferences, etc., play a larger role in what the optimum speaker cabinet design for a particular set of drivers. There are bunch of other theories and equations that may be just as good if not better. Some of the calculators I've used probably apply to bigger drivers like subwoofers, but I wanted the experience.
Step 2: Driver Selection
To create a pair of bookshelf or computer speakers, I needed to find a full range driver. (Drivers, by the way, are the parts that vibrate to make sound) But, you might ask, what about tweeters, mids, woofers and crossovers? I am glad I got you excited about those things, but I want to figure out how to optimize just one type of driver for this project.
Drivers are manufactured to optimize sound reproduction for a particular range of sound. Tweeters focus on the high end of the audible spectrum, woofers/subwoofers on the low end, and mids the middle range of human perception. In traditional speakers, using a combination of drivers and circuits called crossovers, the audio signal is distributed to each driver in accordance to its optimal performance. This can get complicated quickly since you have to pick each component, figure out how you want the signal split, and then design a speaker box to optimize the performance of the drivers. Your own tastes play a big role in decision making. I find some tweeters annoying, and they tire my ears quickly. I like some bass, too, but it depends on what music is playing.
For this project, I simplified the approach and found some highly-rated full range drivers from Parts-Express.com with a good frequency range and a flat response. Full range means I don't have to add tweeters or a sub. The flat response means annoying bass and shrill noises won't come of my boxes.
For the purposes of this project I chose Dayton Audio's ND91-8. It's a relatively inexpensive ($20-30) full range 8 ohm 3.5 inch driver with published technical specs. I purchased two, but I noticed people buy lots of them to place in speaker arrays--and that's another project for another day.
Check your amplifier before deciding on your driver. You will need a 20-30 watt amplifier to drive this set. Amazon has a number of inexpensive amplifiers under a $50, some of which include bluetooth. Most consumer amplifiers work well with 8 ohm drivers.
Step 3: Speaker Box Enclosure Design
Before I started to design the speaker box, I needed to know some of the following parameters:
- Volume of the box that resonates the sound.
- Volume and cross-sectional area of the port if needed.
- Thickness of the construction material.
- Thickness of the internal acoustic sheeting. (Optional)
- Diameter of the hole for the driver.
Unit calculations will be in English, though lots of driver specs come in metric, so watch the units of measure.
Step 4: Port or Not to Port
The first decision to make is about porting. Speaker box enclosures are either completely enclosed or ported. An enclosed box has no holes to the outside with the driver mounted outwards. The driver essentially vibrates the box to increase the efficiency of sound transmission. A ported enclosure has a hole with a secondary chamber open to the air which improves the efficacy of the lower frequencies of the driver. Whether an enclosure is ported does not necessarily indicate the quality of the sound it will produce.
To decide the optimal design for this driver, I looked up the Free Air Resonance (Fs) and Driver Electrical "Q" (Qes) on the Dayton Audio ND91-8 technical spec sheet. Using www.diyaudioandvideo.com's excellent resources; this calculator to helps the decision.
Referencing the spec sheet, the Fs was 69.6Hz and the Qes was .46. The results were a Efficiency Bandwidth Product (EBP) of 151 and the recommendation was to PORT. Porting adds complexity to the design, but I hope it will help out the low end.
(There are a lot of variables to design a speaker enclosure. If you're curious, others have done a good job of explaining them. For this project, I wanted some reasonable numbers for design sizing.)
For reference the equation is Efficiency Bandwidth Product (EBP) = Free Air Resonance (Fs) / Driver Electrical "Q" (Qes).
(BTW There is an overwhelming amount of information available. www.diyaudioandvideo.com is an excellent start. I recommend mh-audio.nl as a comprehensive resource.)
Step 5: Resonant Box Volume
How big should the resonant box behind the driver needed to be? The resonant box, as I am calling it, is the chamber directly behind the drivers that helps amplify the sound. Vibrating that chamber improves the efficiency of the given driver so it sounds louder with the same amount of electricity.
Going back to www.diyaudioandvideo.com's excellent resources, I found the speaker box calculator. I entered the numbers from the Dayton Audio spec sheet.
The calculator asked for Equivalent Volume (Vas = 1.31 liters), Free Air Resonance (Fs = 69.6 Hz) Total Q (Qts = 0.40), Actual System Q (Qtc = .707 default which makes for a smoother low end), Effective Cone Diameter (D = 6.22 cm), and Resonance Frequency (Fb = Hz I let the system calculate it).
The effective cone diameter I had to calculate from (surface area of the cone) Sd (30.4 cm^2), since it was reported as an area of a circle, I computed the diameter of 6.22 cm. It's likely done to not confuse consumers. If you buy a 3.5" driver and the specs say that the effective diameter is only 2.45", you might not want to buy that driver-- though that's just physics, not someone trying to cheat you.
The calculated result was a Volume of 1.31 L or 79.94 cubic inches.
There's two port choices buttons for this calculator: regular and Butterworth B4. The different results weren't too different, but per the help FAQ I ended up choosing the Butterworth B4 method. A good engineering reference can be found here.
Step 6: Port Volume and Surface Area
The port opening and length calculated to be 1" in diameter and 9.21" long respectively. Total volume of the port cylinder would be 7.23 cubic inches. The calculator assumption is that the port will be an internal cylinder ported to the outside. When constructed that way, the enclosure box total internal volume should be the port volume cylinder (if mounted inside) plus the resonant box volume. But I wanted something a little different. I wanted a slotted port that runs out the back with an independent resonator box.
This was a design choice. The port length was calculated to likely much longer than I could enclose in a reasonable size box. I could have put the port outside the box, but did I want a 9.21" long 1" cylinder sticking out the back of my speaker? I bet that would look awkward. I could route PVC pipes internally, but I'd probably need to bend them with PVC joints. It was easy to come to the conclusion that I needed a slotted port.
Round cylinders offer less air resistance than rectangular tubes, but in this case, I made a trade off. I run the risk of generating extra internal frequency reflections or wind noise through the port. These are relatively small drivers, so I am not concerned about huge volumes of moving air. If it was a large subwoofer, the numbers would be very different and other design considerations would be needed, i.e. very narrow ports won't work as well.
Step 7: Driver Displacement
The driver takes up space inside the resonant chamber. Place the driver in the hole and some part of it occupies the air that you want to vibrate.
So one more calculation to make. The spec sheet lists these measurements in the metric system, so that's how I entered them. Keep an eye on those units.
From the spec sheet, this calculator asks for the Effective Cone Diameter (D = 62.2 mm), Mounting Depth (56.4mm), One-way, Linear Excursion (Xmax = 5.1mm) Magnet Diameter (42.2 mm), Magnet Height (27.6 mm), and Front Baffle Thickness (.75") MDF. I chose not flush mounting.This resulted in an estimated 3.1 cubic inches for the driver displacement.
The calculator result accounts for the volume of the hole cut through the MDF, so I can ignore the hole for volume calculations. Adding the driver displacement to the original resonant box volume totaled 83.04 cubic inches.
Using calipers, the driver diameter measured 3.1 inches which will be the size of the hole through the front face.
I think we have all the numbers.
Step 8: Numbers
Final numbers. Do they sound reasonable? If you get something that doesn't sound right, go back and review the calculations.
- Diameter of the hole for the driver = 3.1 inches.
- Volume of the box that resonates the sound = 83.04 inches.
- Volume and opening surface area of the port = 7.23 cubic inches, 0.79 square inches.
- Thickness of the wood I am using = .75 inches.
- (Optional) Thickness of the acoustic sheeting = 0.04 inches.
Step 9: Sketchup, 123 Design, and Alternatives
I used Sketchup to the Computer Aided Design. Sketchup is free for personal use and is a very intuitive process to draw and construct 3D objects. If you're looking at some of my drawings, don't be intimidated. They were way easier to construct than what you might think. I got started watching Youtube videos a few weeks ago.
Rob Cameron on YouTube has done an excellent job of getting people started using Sketchup for Woodworkers. I highly recommend it. It uses an older version of Sketchup, but I found it helpful to figure out the mechanics of drawing, creating components, sizing, creating dados, and putting things together. Spending an afternoon with the videos and drawing the bookshelf example he uses was worth my time.
I think it's a blast to use, mostly because good results come quickly with a very short learning curve.
Autodesk's 123Design is also a good option. It features similar 3D design tools. I don't have much experience other than to say its tool set tend to be more discrete. For example, to make a fillet, there's a button tool to do that in 123Design whereas Sketchup requires a path and follow me tool. 123Design is part of a family of apps for getting your feet wet in making things. It includes CAM software that can even drive a CNC machine. Worth looking into, but not part of my current tool set. To be thorough, Solidworks, Inventor, Fusion 360, FreeCAD or OpenSCAD are all viable options depending on your budget and experience.
There's a simpler way to do this if you wish. Use diyaudioandvideo.com calculator for speaker box volume. That won't give you as much flexibility in sizing, but it should give you numbers that you could easily cut with regular power or hand tools.
Step 10: Designing the Resonant Box
Now that all the numbers have been determined, it's time to do some design work. Nothing fancy here, just a rectangular box.
I am using a precision of 1/100th's because I can with a CNC machine. If you're using a table saw or hand tools, shoot for a precision of about 5-6/100th's or about 1/16 of an inch. If you don't have access to a CNC machine or service, it be easier for you to stick with 1/8" intervals for selecting any particular linear measurement. For a box, for example, you'll have to make two choices about length, width or height. The third variable will be a function of the volume of the box you're trying to build and probably will not be an interval of an 1/8 of an inch. Is 4-8% variation from the ideal going to matter? Probably not. You don't really need a CNC machine to do this, but it makes some of the design work less constrained.
Designing for resonant box volume first, I chose a height and width of the front face in a pleasing ratio and calculated the length as a function of the volume I needed. Arbitrarily, the front face is 5" x 8.09" with a 3.1" hole centered 2.5" from the top. Because I am using .75" MDF then my effective internal dimensions are 3.5" x 6.59" (actually 3.42" x 6.51" because I will place .04" acoustic sheeting on all sides internally) My total volume needed is 83.04" the resultant internal box length is 3.810". (I added the thickness of the acoustic sheeting x2 to the length as well).
Step 11: Designing the Port
The port is completely separate from the resonator box in this design. The port exits out the bottom back plane, up and over a second MDF baffle and then down the back wall and exits. The port design constraints are a cross-sectional area of .79 square inches, a width of 3.5 inches (without lining the port with acoustic sheeting), which is the internal width of the resonant box and a path length of 9.21 inches. That means the height of the port needs to be .22 inches.
For simplicity I am assuming that the length down the center of the path is sufficient. Square corners will introduce turbulence, but I think at this scale it's not going to make much difference.
The port is not contained within in the resonant box, so I do not need to alter the internal dimensions of the front chamber.
Step 12: Final Design Considerations
When designing this speaker, I don't want to use different size materials or introduce structures that would require CNC bit changes. I am going to use the same MDF and same router bit for all cuts.
Other design consideration is dados. Dado cuts are partial thickness gouges that create a stable joint for joining wood from two different planes. Routing out pockets on the side pieces makes it easy to glue and air nail the bottom, top, front back and internals in perfect alignment. One of the woodworking Sketchup videos teaches you how to do that.
I could have saved myself some time by skipping the dados and making straight squares of material instead. I spent a lot of time fiddling to get my CNC machine just right. CNC is great for making multiple things quickly, but sometimes making one-off parts it's overkill. To use a scroll saw and/or table saw to make the parts, you'd need extra patience to get everything aligned and glued properly.
So let's assemble the materials, equipment, etc. that we haven't already addressed.
Step 13: Materials
MDF is medium density fiberboard. It's sawdust and glue with thick paper on the top and bottom surfaces. Some MDF contains formaldehyde, which is terrible on tools. It dulls blades and bits quickly. Nevertheless, it's probably the best choice to construct your speaker boxes. It's machinable, temperature and moisture stable, consistently flat, and dense. Maybe nice expensive multilayered baltic birch would do come a close second, but I experimented here and felt guilty.
I would not recommend particle board or solid wood. Particle board is difficult to work with because it crumbles easily and probably only glues well. It's cheap, so it's what most mass market speakers are made from. Solid wood warps and changes with moisture: not features you'd want for speaker enclosures.
Before you begin designing, measure the MDF with some calipers at multiple locations. Mine came in at .7510". Thousandths of an inch in wood working is a fool's errand. 4/100ths was a bigger deal. I made one set of boxes with some scrap LDF (low density fiberboard) that I didn't measure first. It looked terrible when it was done and I had a bunch of sanding to do. It measured .71". Oops.
Design for the wood that you have rather than what you think you have.
Step 14: Equipment and Materials
This is what I used.
Materials
- 3/4" MDF sheet 2' x 4'
- Wood glue
- Nails or screws
- 2 - Dayton Audio ND91-8 Driver - Parts-Express.com
- Speaker Wire - 18 gauge or better
- Polyurethane Coating (optional)
- Terminal Binding Posts (optional)
- Automotive acoustic or sound deadening sheeting - probably 3 sq ft needed. (optional)
- Rubber speaker feet
Software I used
- Sketchup - Free
- V-Carve Pro
- LinuxCNC - Free
- Microsoft Excel or OpenOffice
Equipment
- CNC Machine - CRP4848 CNCRouterparts.com
- 1/4" Compression Router Bit
- Finishing Nail Gun
- Sander
- Scissors
- Razor blade
- Wood chisel
- Paint brushes
Cost
Material cost is under $100 with the drivers taking up most of the cost. I had extra MDF, wire, glue, poly, and some acoustic sheeting sitting around. The acoustic sheeting was purchased years ago, and I do not remember the source. My Amazon recommendation is just something that looks like the equivalent. Nothing I've suggested requires a proprietary source that would be a deal breaker if you don't have it.
Step 15: CAM Software
As I mentioned, I did the CAD (Computer Aided Design) work using Sketchup. The next step is CAM (Computer Aided Manufacturing software). (A scroll saw and table saw will work, too.) There are lots of CAM options for CNC machines. Years ago, I selected V-Carve Pro, so I will talk about how I use V-Carve Pro. If you've operated a CNC machine as a hobbyist or at a hackerspace, some of what I do will look familiar to you regardless of the software. If you don't have any CNC skills, then this is the time to find a mentor--be it YouTube or a friend.
If you have no interest in CNC, skip forward two steps...
I imported my enclosure box Sketchup file directly into V-Carve Pro. (You can also export the 2D DXF files in Sketchup and print them out for the power tools.) V-Carve Pro imports the Sketchup components directly and lays them out in 2D form. Not all the vectors come through, so double check V-Carve's work.
Selecting particular vectors, I moved related lines to new layers: a pocket layer and two cut layers and then color coded them to make sure it looked right. As I worked on each layer, hiding the other layers avoided some confusion.
Path #1 & 2 - Pocket layers
In CAM software, a pocket is a router move that moves back and forth or in concentric paths to form a cut out. Pockets do not typically go all the way through the material. I needed two types of pockets. The bottom needed a very shallow pocket to run the wire out to the back. I made a 1/4" straight run at 1/8" depth.
The second pocket formed the dado joints for the port baffles, back, front, top and bottom. This was done at a 1/4" depth with dog bones. Dog boning is moving the router bit into the corner of the material for inside corners. Router bits are round and can only make outside square corners. Inside square corners result in a bit of material still in the corner since the bit is round. Moving the bit slightly inward 45 degrees will remove that material. You can use a chisel to break out the material by hand if you don't dog-bone. The last time I got in a fight with a chisel I lost. Couple of bandages and steri-strips helped.
Path #3 - Inside cut profile layer
In VCarve, a profile path is a CNC move that typically will cut all the way through the material. You can specific the number of passes that the bit will perform over that path until it reaches the depth you desire. In this design I needed two types of profile cuts.
The hole that accepts the speaker in my case needed to be 3.1 inches. I specified where the router bit moves. If you move the router bit directly on the line you've drawn for the hole, the bit will cut a radius distance into the wood larger than the line. So you have to tell the CNC machine to keep the bit inside the circle that you've drawn to create a 3.1" hole.
Path #4 - Outside cut profile layer
The last and final cut is cutting out all the parts for your project. It doesn't make any sense to not make this path last. If you cut out all the parts first and then pocket and do inside cuts, you don't have the material support to prevent the router bit from ripping out the part from the sheet of MDF and destroying the piece. The final path is potentially the most frustrating because all the time spent machining the beautiful pockets is for naught if you don't get the last path right.
In this case, I chose to make multiple passes to not put too much lateral force on the material. I also added tabs to the piece to keep it into place. The tabs are then broken by a chisel to remove the piece from the wood. Tabs prevent each piece from flying into the router bit as the bit moves.
Each path requires various settings to determine the speed of the router bits rotation and how fast it moves in the X, Y and Z direction. This is highly dependent on the CNC capabilities, router power and type of bit. This is where experience or a mentor can be helpful.
After I finished all the paths, they were then loaded onto the CNC Machine.
See? A table saw would have been easier!
Step 16: CNC Machine
CNC machines are fantastic, but they are complex, sophisticated, and dangerous. Probably the biggest risk for CNC machines isn't cutting off a finger but combustion. Don't walk away from it while it is cutting. Saw dust, rapidly moving air from the vacuum and a spark or heat off the router bit or router, and you will be sad. There's a fire extinguisher next to the machine and the dust extractor is grounded with a wire wrapped around the plastic vacuum hose. There is a lot of static electricity that is generated when the sawdust moves through the tube. And sawdust makes an excellent fuel. One of the pictures about shows a spot where I didn't move the bit upwards fast enough. I saw a smoke and a bit of char from the inside of one of the speaker holes. I will need to increase my plunge rate for the next set of boxes.
I use a CRP4848 built from a kit from CNCRouterparts.com. Over the years I've built a dust collector, a vacuum table, lighting and laser sights. (Because lasers!) It runs LinuxCNC on an old PC. Any CNC machine will work as you can machine the biggest part off the bed. There are lots of great Instructables for building a cheap CNC machine. (Don't let anybody convince you that a CNC machine is more than 3-4 stepper motors, a wood router or dremel, a power source and a cheap computer.) I recommend the CNCZone and LinuxCNC forums as a resource.
I've uploaded my file to the LinuxCNC computer to drive the paths on the CNC. I've homed each axis and zeroed the tip of the router bit to the surface of my spoilboard/vacuum table. I place the MDF sheet on top of the bed. Align the router x and y to the sheet and press... No stop.
This is the part that always gets me. Pressing go means I am committed to making or destroying a beautiful piece of wood. Usually I go back one more time and make sure my measurements are correct and that the numbers make sense. I double check my paths for depths and router speeds, and make sure the paths are referenced to the bottom of the sheet. Ok.
Place in ear plugs. Start vacuums for table and sawdust collection. Make sure there is no animate or inanimate objects near the machine. Safety equipment, check. Go.
This is the part I love to watch. Each step the computer mindlessly follows until it results into parts I drew in Sketchup. The machine stops when the paths are complete. I use the vacuum to suck up all the extra dust and use a small chisel to extract the parts. That's intensely gratifying when it works. On to the next step. (Secretly I watch YouTube videos of CNC machines for fun. Weird. I know.)
BTW I discovered that compression router bits are the bomb. They have two sets of flutes that rotate to push the sawdust together as the bit moves through the wood. It is the equivalent of an up and down endmill that nicely cuts both sides of the wood, so that there is no tear-out or splintering on either side of the board. The compressed sawdust adds a tiny bit of support to the material in place. It does require some vacuuming when it's all done, but the sawdust doesn't go far.
Step 17: Parts
After the parts are pulled off the board, I examine each one for damage. Sometimes I have to go back and make one more because the path wasn't quite right or by some fluke the board moved while it was cut, and the piece isn't quite square.
For each part I remove the tab with sand paper or flush cutting pliers. I lightly sand the edges of the MDF where there might be a little tear out from the routing. Blow off the dust without breathing it in, and then I put the pieces together, lightly clamping to see how it's going to look. When satisfied, I break out the air compressor, finishing nail gun, wood glue and rest of the clamps.
Step 18: Construction
This part is both the most exciting but subject to failure. Since I've put the parts together to see how they work, I need to think through the construction steps. Figure out what piece will go on last. And figure out how best to keep the parts square. Think through this a few times before you begin.
Step 19: Inside Coating
The first step prior to gluing is painting the internal surfaces with clear polyurethane or shellac or something that will seal the internal wood. You could even use paint. I just coated the visible surfaces not the surfaces to be covered with glue or joining. I painted mine with a water-based poly and then let it dry for a few hours.
In retrospect, I think this is optional. With big boxes and moving lots of air, I would definitely add this step. I added some acoustic sheeting to the resonant box, and the polyurethane coating helps with the adhesive on the back of the sheeting. That should be sufficient.
Step 20: Wiring
In the bottom plate I ran a small channel for some wire to go to the driver. I gave myself a bit of slack, so it would be easier to solder the wires to the driver. I hot glued the wire into place and ran some scrap wood over the top to remove the excess glue and kept it flat
Step 21: Acoustic Sheeting
Acoustic sheeting is used to prevent harmonics from forming inside the box. Some speakers have foam placed on the inside of the resonant chamber. To minimize the size of the box, I chose acoustic sheeting for inside. It's relatively inexpensive, and you won't need much for a small speaker. The trick here is to line the sound-exposed surfaces without getting into the joints. It cuts easily with a razor blade or scissors. The bottom plate requires a hole for the internal driver wire.
Step 22: Gluing and Air Nailing
I glued and nailed the parts together at the same time. I used wood glue to make an airtight seal and used the finishing nailer to keep the wood in place and strategic clamp use to keep things square.
The speaker enclosure is going to shake, rattle, and roll for years. It might be tempting to try to get away with glue alone, but nails or wood screws will prevent having to build another set later.
Some of the joints were too tight with my design. Light sanding or the use of a rubber mallet to get the parts in tight proved useful. In my next design I might add a 1/100 of an inch to make construction easier. The wood glue forms an airtight bond and a meniscus to seal those small joints making very tight joints unnecessary.
Step 23: Wiring Part 2
I found some inexpensive terminal posts on Amazon and installed them on the back plate. I designed a hidden tunnel through to the back for the wire. I pocketed out a spot for the back of the posts and screwed them in tightly, and applied some glue to keep it airtight. This was a little tricky, because I didn't want a lot of slack in the wire, so I cut the wire at the top of the terminal pocket.
Step 24: Solder and Installing the Driver
Write down your wire convention or verify with a multimeter. I soldered and heat-shrunk plastic over the driver connectors. I used wood screws to secure the driver to the front face.
Before installing the driver, paint, veneer or lacquer your enclosure. The driver will get in the way of finishing. I was not my goal to "finish" this set, since it's going in the garage.
Step 25: Finishing and Things I Would Do Differently
I like the DIY MDF look, but I have some ideas for future sets. I have a selection of wood veneer samples, and I tried lacquering a piece of MDF. Even a piece of hardwood to go on the front would be a nice finish. I put rubber feet on the bottom. The proof of concept works for me, but before I tell you how they sound, here's what I would do differently.
Things I would do differently
- Flush mount the driver with the finish in mind before hand.
- Dado the front panel to make it easier to align.
- Make a rounded resonant chamber just to see what it would sound like.
- Router the outside edges of the enclosure.
- Use a bench sander instead a finishing sander.
- Angle the front face upwards to point toward the listener's ears.
Step 26: Results
Unfortunately, I can't demonstrate how they sound. No Youtube or audio file is going to be able show you they work, since the sound will play through your speakers.
In short, they are stunning. I connected the set to a relatively inexpensive amplifier and played a variety of music. I heard details that had completely escaped me from music I thought I knew. The range was full and satisfactory. They weren't loud, but the volume was adequate for a desk or my garage. They sound like medium to small speakers, but certainly bigger then they look. Thirty watts aren't going to give a fully immersive experience like a floor-standing speaker set or surround system.
But they do make you feel a bit like you've been ripped off by those computer speakers you buy in the store. The lushness of full range music this set produces feels embracing and lush.
Overall, they are nice, warm, and inviting, neither shrill nor boomy. You can hear the not quite silence of analog mastered of older tracks. I hear breath sounds of the singers as they inhale. I can hear subtle instruments I've never noticed before. Jazz, pop, bluegrass, acoustic pieces, or heavy vocal tracks are outstanding.
Amplifier aside, is it the driver or the box that made a difference? Connecting the driver to the amp with no box, the drivers sound okay. Drivers in the enclosure sound much better, but if I didn't have good drivers, the box wouldn't matter. They work well together.
Step 27: Final Thoughts
As a first step to bigger goals, I'd count this project as a success. So what comes next for you or me?
- Make a set of traditional tweeter, mid and woofer speakers. Learn about active and passive crossovers.
- Make a bluetooth or Airplay box that incorporates some of these design considerations.
- Make speaker enclosure CNC molds to create concrete enclosures with ideal chambers and porting.
- Add a subwoofer to make a 2.1 system to add that EDM kick.
- Create a speaker array with full range drivers.
- Make something unique that looks and sounds awesome.
I hope these notes are helpful. I am looking forward to some constructive comments. I hope you're inspired to make something cool. This was a project well worth the effort. These speakers are enjoyable. I wish you as much or more success. I don't think I'll be going back to that big box consumer electronics store. I have some new projects to sketch out.
Attached is the original Sketchup file and DXF file from V-Carve.
Attachments
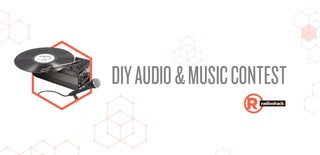
Participated in the
DIY Audio and Music Contest