Introduction: Nomad Made: EDC KeyCORE System
The Goal of this Key Organizer System was to keep my key's simple, small, and efficiently organized.
The "In-Hand" feel was the ultimate measure of design success and needed to be solid and smooth.
Knowing that most keys have dissimilar holes, I needed to unite them, so the keyCORE concept was born.
I used the Nomad Pro CNC with included Carbide Create software to bring this concept from Idea to reality.
http://carbide3d.com/carbidecreate/download/
As community Manager at Carbide 3D I am very happy to be able to share this concept with the creative community.
I think it is a useful structure that can be expanded on and embellished with additional tools to suit a users unique every day carry needs.
Step 1: KEYcore Concept and Exploded View
How could you keep your keys together in a small compact assembly?
Each key would have a socket and flange "core" to keep the keys inline, and similarly spaced.
I settled on a 3mm shaft size and designed the assembly as a whole to be as minimal as possible.
The "KeyTool" would have a threaded hole to receive the m3 bolt.
In effect the keys become like components in a Swiss army knife with no side panels.
That's as minimal as it gets.
Im really excited to share this project with the Maker Community.
Its still amazing to me how quickly you can go from Concept to Real parts with a Nomad Desktop CNC and Carbide Create.
Step 2: Designing the Plastic KEYcore Parts
Using digital calipers I measured and noted my 4 unique Key's eyelet dimensions to create the small plastic KEYcore parts.
In Carbide Create these shapes can be dimensioned and and joined into compound forms if needed.
Then a tool is chosen from the library, a material defined and tool-paths are applied.
4 different tool-paths using a 1/16th 2 flute end mill were needed create the parts in total.
First a surfacing pocket to thin the total thickness of the 3mm material to 2.5mm.
Then the 3mm through holes were applied
Third is another "pocket" style cut that leaves the unique core post to fit into the keys eyelets.
Lastly the outside cut to define the 10mm outside of the bushing flange.
Leaving a thin skin of .01mm material on the outside cut keeps the small parts from flying away, and they can be popped out or cut with an exacto knife.
Step 3: Cutting the Plastic Parts
I cut my first parts out of Acrylic, which is less expensive than the final material (delrin)
This first cut is to check for fit and sure enough one of the KEYcore was to large.
Carbide Create keeps the tool-path info, so all that was needed was to adjust my line work and the tool-path automatically updated.
The Thickness of the bushing which spaces the keys apart was thin, but structurally robust.
The 10mm diameter offers a good amount of surface to allow for some friction, but also small enough to be hidden in the stack once assembled.
Step 4: Designing the Damascus Pry Bar Key Tool.
This was my first time machining Damascus steel, so I kept the design of the KEY-tool part as simple as possible.
Lots of features can be added to the tool later, for now a minimal Pry-bar with a 2.5mm hole for tapping to M3 was all that was need to prove the concept.
Step 5: Machining the Damascus Pry Bar Key Tool.
Work-holding is a big part of machining.
Using the threaded table and small clamps with a waste board below the Damascus allows for the Carbide tool to cut through the steel without damaging the black anodized aluminum table.
The Clamps create a solid hold and are clear of the cutting path.
Because Steel requires coolant, I use Hot Glue to build a wall around my cut.
When the hot glue cools I fill the "pool" with synthetic water-based coolant.
Note: Some small magnets in a tool tube can be used to remove steel shavings from the coolant pool.
Step 6: Assembling the EDC KEYcore System
Once the design was finalized I used white Delrin for the KEYcore parts.
I hand tapped the M3 threads in the Damascus Pry-bar and rounded the tip to create the pry bar on a 3m grinding wheel.
Each key gets a Delrin core, and then one M3x16 bolt with a washer is threaded through into the Steel.
The Finished assembly has a nice weight from the steel, and the keys rotate smoothly.
No jangling, no noise at all actually and the compact form is easily tucked into even the smallest of pockets.
I hope you build yourself one and take the time to design your own keyTOOL to address your specific daily tool needs.
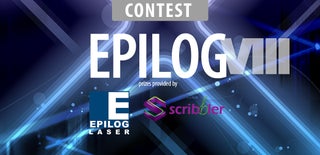
Participated in the
Epilog Contest 8