Introduction: Etch a Family Portrait
So it’s Christmas again, and anyone with a large extended family knows it can be quite expensive come gift time.We use the Secret Santa process where you buy for single family member using a set budget.The only problem with this is I still can’t shake the urge to do something slightly over the top.Living in a small secluded northern town can make this tricky.Sure you can order online, eBay is one of my best used services, but this involves some advanced planning, something our family is not the best at.Usually the secret Santa list is set out early, but I tend to forget about it until its too late to order something in on time. This year I picked my brother in law to buy for, and I couldn’t figure out what to get him.He was hinting at a hydrometer, but the weather up here wasn’t permitting me to drive to the next town to get one.Time was running out and I still had no inspiration…
Prologue: In early December a friend of mine Oliver James Brown who runs a tattoo shop (Divine Ink) had his foot pedal beginning to die, (it runs his tattoo gun).I was over getting an arm sleeve started and we talked of my various instructable builds.He asked me if I could machine him a new foot pedal and I thought why not.He said it didn’t have to be special, but I thought why not do something interesting with it.I suggested etching the metal with acids and asked him for a couple of his logos to use.Within a short amount of time it was finished and It turned out awesome with a nice deep etch.One day I will write the instructable for it as well.The photos below show the etched portion of the switch, basically the top portion of the pedal.
A week before Christmas I was sorting out some of my photos on the computer and found the ones I had taken of the switch and that’s when I realized I could etch him a family portrait into metal. I would use a photo snagged from facebook featuring his wife Nicole who kindly helped model my Apron of Holdinga while back, in addition to his daughter Mia and son Asher. This would be something that would literally last forever, and with the etch being nice and deep he could use it with his small children as a rubbing plate as well.
Disclaimer
This instructable uses dangerous power tools and evil chemicals.
you have been warned, if you’re not careful you could be
- Cut
- Electrocuted
- Burned by Acid or Hot metal
- And my personal favorite – gassed.Nothing quite like the sensation of feeling your lungs wither in your chest!
Scary enough? Good, this will keep you safe.As long as you’re careful and take precautions everything will be fine.But… if you are the sort of person who likes to play it ultra safe, this may not be the thing for you, maybe you should stick to macaroni art.“inside joke for certain readers”
Lastly, I will be entering this instructable here on on the instructable site in several contests, one being the Christmas contest of course, this being a Christmas present and all, but I am also entering this in the ShopBot Challenge in an attempt to win the CNC router they have up as their No.1 Prize. That would be awesome for everything I build, for building lay-outs to 3D relief patterns and artwork. I would be a very busy body indeed. Either way, if voting makes you feel uncomfortable please rate me, it lets me know how I'm doing. Or, please feel to ask a question or leave a comment.
Step 1: Tools and Supplies
The main choice you have to make is what kind of metal you are going to use.I used Aluminum plate as takes a nice etch and finishes well.Aluminum is not my favorite metal by far as it is not as forgiving as plain steel, but it was perfect for both the tattoo pedal and for use as a portrait medium.A couple years back I made my best friend a steel box shaped like a book from the TV series Battle Star Galactica “The new version” with the intent of holding his Battle Star Galactica DVD series.Inside it had DVD sleeves and was lined in felt.Outside the corners were nipped off just like all the books on the show.The front cover, back and spine were etched with logos and pictures from the series, it looked much rougher but felt and looked almost alien ancient once complete.This used a different chemical for the etch, Stump killer “copper sulfate” mixed with salt, baking soda and water.Etching aluminum however requires a different solution to maintain fine detail.This mix will work with brass, steel and even copper to a degree.It will also happily etch you as well!So some safety gear is required!Check the list below
Supplies used
- Aluminum plate, mine was about 1/8 thick but you can go as thick as you want really, size is up to you
- Muriatic Acid – found at the hardware store
- Hydrogen peroxide – drug store
- Enamel paint – model paint or even nail polish works great
- Acetone
- Slippery high gloss paper
Tools used
- Something to cut your plate to the size you like
- A plastic or glass tub deep and wide enough to hold your plate when time to dip
- Small artist paint brushes
- A way to print on paper using toner type printing – aka laser printer or photo copy machine
- Various grades of sandpaper
Safety supplies
- A very well ventilated place to work from!!!The chemicals you are working with are nasty enough alone, but when you mix them and introduce your aluminum plate you will cause a chemical reaction that can generate a poison gas.This is serious
- Rubber gloves, the longer the better – dish gloves are just fine
- Safety splash goggles or even better, what I used -full face gas mask
- Clothes you can throw out after.
- some sort of device to lift the plate out of the solution with, (I just wrapped some plastic twine around the plate prior to the dip)
Step 2: Manipulate Your Photo
Prepare you picture for tonerization!Ok, tonerization is not really a word, but I am going to use it anyway, so best get used to it.You can use what ever software you like, but I her I used GIMP.Its free open source software that has almost all the bells and whistles one needs for a project such as this.An additional program I used was Inkscape, you don’t really need to go this far, but I like how it lets you turn your photo into a vector drawing.This makes your lines incredibly crisp
- After you have installed the software open your photo of choice with GIMP – I sneakily downloaded a photo from Dave’s wife’s facebook profile.Showing her and there two children Mia and Asher
- Click on filters, from the drop down click Artistic then click Cartoon.
- A pop-up will show a small preview.Slide the 2 two bars back an forth until you are happy, keeping in mind you will be erasing all color and shades.Eventually only having either black or white – click OK
- From the tool box choose the icon of a paint can tipping over.
- Set the color to white and try clicking on a color section where there is no black.By increasing the threshold you will increase the areas chosen to white out.I would bring it up to 125 for most areas, but where there is fair bit of detail you will have to scale it back a bit.If you white out to much just use the “back” button.
- Go back to your tool box and select the magic wand button, increase your threshold again click on the white sections.To select multiple areas hold the shift button down at the same time.When you have selected all the areas, click Layer from the top of the screen
- From the drop down choose transparency and select add alpha channel
- Next from the top of the screen click on Select, another drop down will occur – choose clear
- Where you successfully selected area you will see a grey on grey grid, often revealing sections in white you didn’t notice.Just go back with the wand and select these areas.You wont have to go through the step of adding the alpha channel again, just select and use the clear button.
At this point you can save it and hit print, BUT make sure you save it in a lossless format.I always use .PNG as almost any program will open it after.If you save it as a .jpg you will undo you work making the back ground clear!There are a lot of choices to save to from.tiff, .bmp, .gif and many others I have yet to use.To smooth it more go on to the next 3 steps and open Inkscape
- Once opened in Inkscapeclick on the image, this will cause a black box with arrows on the corners to appear.Select path from the top and choose Trace Bitmap
- In the pop up choose Greys and select Scans to 2 and check mark remove back ground – Click OK
- Your black lines will now be more rounded and smooth.Save it once again in a lossless format.Don’t be alarmed when Inkscape says your not saving it in the SVG format they prefer, for this project its not necessary.
Step 3: Prepare the Plate
Ideally your plate of metal you use should be as smooth as possible to start with.My plates were pretty smooth with very little scratches.You should still sand it though to ensure your getting any contaminants off prior to applying your toner.I started with 220 wet sand paper and worked my way up to 400 and 800 before finishing off with 1200 grit.Keeping sanding until nice and smooth.Later you can always go back and polish it to a mirror like finish, but until then don’t waste your time.
Step 4: TONERIZE
Choosing your medium
- Find some "cheap" high gloss paper. This is actually trickier then it sounds as the whole point behind most high gloss papers is to provide a surface that produces excellent photo reproduction. So, its designed to absorb and hold the ink on the paper. In reality you are wanting a high gloss paper that does not absorb and or hold the ink. Now of course I am not really talking about ink at all, here we are using toner. But I digress, paper... I have tried a variety of papers with mixed results. All of the high end gloss photo papers worked somewhat ok. Sections of toner would transfer, but some sections no matter how much heat or pressure applied would transfer the toner. This resulted in splotchy transfers. I then tried using the coated paper found under sticker sheets. This worked well for the transfer, but the initial printing due to its ultra slickness left lateral tracking lines of toner. Lastly I tried something similar to magazine print. It was the cover sheet advertising loose leaf paper from staples. Found when you buy small packs of loose leaf paper, its the top colour sheet advertising staples brand paper that is vacuum sealed in the plastic pack. The only trouble is you get one sheet per pack. This is what I used for the photo. When I went through the process it left an icky white fuzz of dissolved paper, later I discovered this actually a good thing. I used another brand for the Daves name. The toner transferred awesome and left no paper residue. i thought it would turn out even better, boy was I wrong. The additional paper helped resist the etching solution. Suffice to say the photos pure black sections are ultra smooth. Where as Dave's name is actually quite mottled. Of course most people think this is intentional and I let them think that...
- The kind of toner used varies just as much as the paper. I have found the best toner is always just the old school black kind found in old photocopiers. I have a colour laser printer at work that prints beautifully and transfers toner well for the ironing method. But it doesn't resist the etching solution all that well. Unfortunately i discovered this while doing this very instructable. Both the photo and the wording degraded more then I liked. If this is the only toner you have available, limit your time in the dip tank later on, and or check it often = which is what I should have done - doh! In my initial etch of the tattoo pedal I used toner printed from a old photo copier found at my local Shoppers Drug mart. It was looked and felt layered on, this is what you want. The script on the tattoo plate held up amazingly well, to actually feel the depth of the etch just can be expressed in a photo. Anyway enough prattle, lets begin.
- Insert paper into printing machine of choice
- Send image to printing machine, ensuring it is a reverse image
- Retrieve image and look for irregularities in the print job
- Repeat at nausea.... Why? I don't care if you are new to this or have done it a hundred times, errors will occur. It is much better to have a couple extra sheets lying around if the first one magically goes on perfectly, then to have to go back in the middle of the game to print out more sheets.
- At this point your tonerized is susceptible to smearing, treat it gently. Of course this make the next step tricky, but worth it. Flip your image over and lightly trace in PENCIL the perimeter of the image. You will use this tracing when you line up the image on you plate as the toner will be facing down. You will not regret this step!
Step 5: A Little Light Ironing...
- Heat up your iron, I set mine between cotton and linen - ensure you are not using steam. If your iron doesn't let you turn off steam, make sure to drain it first of any water
- lay out a towel on your work surface
- lay your plate on the towel - the towel helps the plate from moving around
- Carefully lay your image toner side down on the plate, lining up the image where you want it. Aren't you thankful you traced in pencil on the backside now?
- Others usually put something over the image at this point. I don't bother. Just lay your iron over the image gently, try not to move your image. Let the iron just sit there for 4-5 minutes. This will cause some of the toner to stick to the plate effectively gluing it on. Gently begin to move the iron all over the image in lazy circles for several minutes with light pressure.
- Now increase the pressure moving laterally back and forth and side to side for several minutes, Always keeping mind you could shift the paper which is not good! Doesn't hurt to hold down the edge of the paper with a gloved hand to keep it from shifting. Your essentially burnished at this point, soon you will begin to see your image through the paper, but not always.
- Its patience time. Turn off your iron and walk away for 1/2 hour to let it cool. Do not plunge it into cold water to speed up the cooling process. You can develop steam jackets that can lift your toner you just worked so hard to apply right off the plate.
- Once its cool enough to handle comfortably toss it in a bucket/sink of room temperature water. Resist the urge to use hot water to speed it up. Once again, walk away for 1/2 hour.
- By now your paper should be nice and soggy but dont just try to peel the whole paper off. Instead using just your finger tips rub the paper. After a minute or so, the paper should begin to ball up under your fingers. Keep going, abrading the paper on with your finger tips. After 5 minutes or so the paper should be disintegrated and your image now right side up will be revealed. It will most likely be nice and dark with the odd speck missing. Those missing speck can be touched up easily enough with some paint. however if large portions are missing or lots if intricate detail will have to be painted on, I hate to say you may have to start over. Re-sand and start again. Ugh
Step 6: Touch Ups
Options
- Iron another image. I decided to iron on the picture first, then go back and apply my lettering. In the pictures you will notice the image and the words are of a different colour, this is because I used a different kind of paper that left no fuzz. In theory you could iron in small sections as well, though I think this may prove problematic.
- Paint. This is the method of choice for touch ups, in addition to reinforcing your toner. This is what i should have done for the image and Dave's name. It is what I did on the tattoo pedal, and the results were clear at the end. Now you may ask yourself if this is redundant, or why bother using toner at all? Well, if you are that good of a painter be my guest. Myself, I have found over the years I have fell out of practice of painting free hand with any level of quality. However painting over the existing black toner is simple with a nice thin enamel and a quality fine tipped paint brush. You can use model paint or even nail polish just as long as it is an enamel paint that has been thinned a little. Model paint and nail polish especially are to thick to paint with any fine detail. So paint in any missing parts and while your at it, go over your toner sections as well.
- Wax or Vinyl. I have seen others paint on wax or even use sections of sticky vinyl cut out and applied. I really can't judge it as I have not tried it. I don't know if I would use though as the solution literally boils with a exothermic reaction. Quite a bit of heat is generated so it has the potentially to melt off the wax or break down the glues holding the vinyl on.
Step 7: To Frame or Not Too Frame
This all about personal choice, but choosing not frame it will not get you out of yet another step. You can frame it by simple applying a border of paint around your image with enamel paint, the same kind you used for your touch ups. Make it how ever you like, either laser straight intricate or jagged like I did. I find the jagged look reminds me of a rough sand cast effect that can only be appreciated in real life, pictures just don't do it justice. But each to his own. Either way you will have to apply paint to the edge of the metal and the entire backside of the plate to protect it from being eaten away. In theory you could apply the frame using the toner method, but that seems like a lot of extra work that take minutes with paint, and you would still need to paint the edges at least. I found the easiest method was to have my plate raised on something that would allow my fingers the space to grab the plate from top and bottom of the middle to flip it after. First I painted the frame. The carefully flipped it over resting it on the middle of the plate. Then i painted the edges and backside. I used blue model paint. The colour doesn't matter, but i couldn't help but stare at the beautiful translucent colour after it was done. It looked like anodized jewel tone. let it dry for 24 hours!
Step 8: Mix
Ok, this is where you really need to start paying attention and learn from the mistakes I made while etching the tattoo pedal
- Muriatic acid all though not the strongest acid out there should be treated with respect. When I bought it, it came in a 1.5 litre bottle that was wrapped in a second layer in the form of a heat sealed plastic bag. I decided to open the bag with just bare hands thinking it was all sealed. Whoops, a tiny trace amount of the acid got on the side of my thumb and I immediately felt it going to work. The pain was incredible as it quickly dissolved a few milometers of my epidermis about the size of a pencil eraser head, with odd looking striations edging out from the initial wound. The wound took about a week to heal and hurt almost the whole time. USE SAFETY GEAR!!!, just imagine what that would have done to my eyes - very scary shit indeed - sorry for the potty mouth
- Mistake No.2 - When you mix up your chemicals, never walk away from it. I mixed my solution, dropped in my plate and watched as nothing much happened. Sure, some little bubbles started to form on the bare aluminum and rise up like weak club soda, but not the reaction I was looking for. I was expecting a flurry of activity where none was taking place, so I left the detached garage where I was working and went back inside to look at the formula thinking I had done something wrong. I thought at this rate it will take hours! That's when I read the exothermic reaction takes a minute or two get started. It hadn't been 5 minutes when I walked back out side and promptly heard a continuous whooshing sound coming from the garage, and noticed a copious amount of yellow tinged gas streaming out of the open garage door - which leads to my next mistake.
- Mistake No.3 - When someone says to do a certain type of work with plenty of ventilation, really you should be doing it outside! Not in a small shed with one small door open as your source of ventilation. I was lucky as I had taken my full face gas mask with me inside. I used to work in a paper mill where you are exposed to all sorts of lethal gases. I ran into the garage, plucked the way to shallow tub of boiling acid up with some tongs and took it outside where I promptly dumped a bucket full of snow in it to dilute the reaction. After much cleanup and fanning out of my garage the dangers were over.
- Ensure your tub is wide enough to just hold your plate laying down, but ensure it is at least 5 inches deep to contain splashing boiling acid!
- Plan where you are going to do the dip, the chemicals when mixed produce toxic fumes but its when you introduce the aluminum that the real nasty gases are produced. Make sure your area is extremely well ventilated - ideal is outside, which is where I did it. This time...
- Get your safety gear on prior to starting, its not going to help you when you are on the ground with your melting out of your sockets and your lungs have withered away like deflated balloons! At the absolute minimum be wearing splash goggles and rubber gloves. Really though, a full face gas mask with appropriate filters is best. Your face is protected, and you can breath still - breathing, that's a nice perk
- Once you are all Darth Vader-ed up you can mix your chemicals. The ratio is 2 parts 3% Hydrogen peroxide to 1 part muriatic acid - in that order! Never add the peroxide to the acid as it can cause an unstable reaction
Step 9: Dip
HEY, WHY NO PHOTOS OF THIS STEP? YOU SAY! Well the vapour caused by this has the potential to etch my camera lens - which I just purchased, so your just gonna have to trust me
First a little planning.
- How are you going to lower the plate into the solution with out splashing acid all over the place?
- How are you going to remove the plate to check the progress?
- Do you have a bucket of water to dilute the acid on the plate so you can check the progress?
- Get some plastic twine and loosely tie up the plate like ribbon on a Christmas present with several long strands attached about a foot long. Sure you could lower it into the solution with your rubber glove, but now your glove is covered in dripping acid. The gloves are there to protect you from accidental exposure to the acid, not to be used as a tool
- Make sure all you safety gear is on !!!
- Gently lower your plate into the solution holding on to the attached strands. Lay these strands over the edge of the dip tank
- Little bubbles will begin to form, step back several feet and wait for several minutes as the reactions begin to take place. After about 3 minutes carefully approach the tank and gently lift the plate using the attached strands out of the solution. Allow the excess to drain off and lower into the tank of water. Gently lift it in and out of the water several times to flush off the acid. Check your progress, the toner and or paint will still be present but the exposed aluminum should now be etched away evenly and will look dull grey. If you think it needs more dipping put it back in the solution and check every minute until you are happy with the amount of etch. Keeping in mind, you can't really add back whats been taken away.
- Put the plate back in the tank flush with plenty of fresh water.
- The solution can be reused again, wait for it to stop reacting and bottle. I never seal it air tight though out of fear it developed pressure and explodes. Someone please inform on the correct procedure for this!
- Once all is cleaned up, get out your acetone and pour it in a shallow container. Add your plate and let it sit for several minutes. With gloves on you can now start scrubbing the paint and toner off the back, side and front. I used a mild scrubbing pad designed for Teflon pans. It has a bit of abrasiveness too it, but not enough to really scratch the aluminum under neath.
- At this point its a personal choice of polishing. You can sand and polish the just face further or you could even go in a polish the darker grey aluminum. I chose neither as the exposed aluminum was shiny enough and I liked the contrast the dark grey gave it
Step 10: Finish It Up
I left it as it is, as I wanted Dave's children to be able to handle it and feel all the grooves made by the etching. But you could always fill the etched areas with paint, melt some glass enamel in to the etched sections or perhaps frame behind glass. Another simple step would be to epoxy on a small hinge on the back to act as a self stand up frame, or a loop to hang it from a nail on the wall. Its up to you at this point, be safe while doing this, but have fun
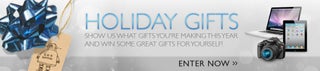
Participated in the
Holiday Gifts Challenge
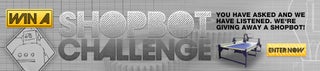
Participated in the
ShopBot Challenge