Introduction: Extension Cord Reel
Yesterday I stopped in a Goodwill store and found a 100ft, 14 gauge extension cord... for $15! I looked it up online and the same exact cord sells new for $40-$80 depending on where you look! I love Goodwill :) My wife was a little irritated that I bought it since we already have several cords but none of them are this heavy duty so I couldn't pass it up. Then, last night, I was geeking out on here and I noticed the tools competition, so of course I had to make something I've been wanting to make for several years. I trash picked a wire spool a few years ago and ever since i've wanted to make an extension cord reel with built in electrical sockets like my dad made years ago. Only I had ideas on how I would improve the idea.
His has two sockets in a metal electrical box mounted on top of the reel, with the cord run inside and up to the box. I wanted my sockets to be inside the reel because the box always seemed like it was in the way when winding up the cord. I also wanted a knob for winding it up and a base so I can set it on the ground and just pull the cord to the outlet. I also wanted the base to be a hand hold for winding it back up.
This morning I stopped at my local home improvement store and started searching for parts. It took me a while but I eventually found all the parts I needed. I already had the cord and the spool and I had a wooden knob from a piece of furniture I fixed up. Oh, I also used a scrap of household electrical wire and a wire nut, both of which I already had.
I ended up buying:
(2) tamper resistant duplex outlets
(1) two gang electrical box
(1) metal outlet cover
(1) PVC toilet flange
(1) PVC toilet flange extension ring
(1) 4 inch PVC adapter
totaling $18.30 after tax. I ended up not using the flange extension ring so that takes off close to $4 after tax and puts the total spent right around $30, if you include the cord. I also used a few fasteners I already had on hand.
The tools I used were:
Jig saw
oscillating tool
drill with bits
philips and flathead screwdrivers
file
sand paper
wire cutters
regular and needle nose pliers
multi meter
***Caution***
A couple helpful comments have been made by some of our knowledgeable cohorts. They pointed out that if the cord is used while coiled around the spool, especially at a high power load, the wire will be subject to an effect known as inductance. Basically, it creates a magnetic field which then affects the conductor and if the current is high enough it can cause the cord to overheat. If you want a more in-depth explanation, there is a link below where you can find a ton of info about. You can also look in the comments to see an photo of a cord on a spool that overheated.
Long story short, if you are using an extension cord it is best to unwind it completely when you use it, especially if you are putting a high load on it (i.e. welder, lathe, electric heater, microwave, (most power tools and appliances really). These examples are not the only things that can draw a high load, check the power ratings on a tool or appliance to be sure. I've also included a page that has common power consumption ratings, it gives a good perspective of how different tools and appliances stack up.
http://electrical4u.com/what-is-inductor-and-induc...
http://www.absak.com/library/power-consumption-tab...
Step 1: Cutting the Holes
First thing I had to figure out was "how is this crap gona fit?" I used the jigsaw for this part.
It took a bit of finagling with the size of the hole to be able to fit the parts through without making the hole too big. In the end I had to make it bigger than I wanted so I used a scrap piece of hard board as a mounting plate. (I forgot to mention that before. I also had that on hand.) I forgot to take a picture of the mounting plate after it was done. I sanded the edges of it help it look better. In retrospect, I wish I had cut a bigger piece and made the mount plate round to completely cover the metal tabs on the top of the spool. I could have cut a larger hole which would have made things a little easier later on. I also cut a couple tabs off the electrical box.
I also cut a bigger hole on the other side to fit the flange. Be careful with this part, my blade went off track a little and the hole ended up not being as round as I wanted it.
Step 2: Building the Base/Hand Hold
The flange is going to act as a base and also as a hand hold for reeling it in and out. I can't really go much into how I came up with what I did because it mostly looking at it, scratching my head, looking at it more and trying to imagine how it would work. I ended up cutting the adapter piece where the smaller section meets the larger section, leaving the beveled part with the large section. I had to cut the larger ring in half to fit it through the hole on top, thats why I wish I had made the mounting plate bigger and cut a bigger hole.
The way it fits together, the flange goes in through the bottom, the other pieces go in through the top, the smaller ring around the flange and the larger ring around that with the bevel against the bottom of the spool. It's all glued together with caulk. I recommend doing what you can to keep that larger ring in one piece, I'm worried that where the two pieces meet is going to rub on the spool and keep it from rotating smoothly. I might rebuild that part later if it is a problem. It's hard to tell right now because the caulk hasn't set and I don't want to rotate it until it is.
The way I assembled it, I put a bead of caulk around the inside of the beveled sections, put those in place, put another bead in the top of the gap between the flange and those two pieces and then slid the smaller ring in-between and pressed it all together.
Step 3: Wiring
Next up is the wiring. I had to pause a second when it came time to cut the female plug off the cord. Once I cut it off there would be no turning back, but i figure out of the cords I have, its the best one to use for this so off it went. I cut about a foot of the cord off with the plug so I can use that for something else later on. I don't know for what, but I'm sure it will come in handy at some point.
***CAUTION***
Electricity is dangerous so if you are not familiar with how to wire an outlet, make sure you study up on that so you don't wire it wrong. The black wire is hot and goes to the brass screw and the white wire and goes to the non-brass screw. The other (it was green in my cord) goes to ground. Here is a link to an Instructable with a video if you need a visual aid https://www.instructables.com/id/How-to-install-an...
I cut off the plug, stripped the wires and ran it through a hole that just happened to be the perfect size and spot. I can't guarantee that your spool will be as cooperative so do what you gotta do. I drilled two small holes in the bottom of the electrical box and used a zip tie to secure the cable. Next up, I used the scrap of household wiring to connect the two plug sets together, then I attached the cord to the other set of connections on one of the socket sets. There was only one ground connection per set so I left a tail coming off one of them and used a wire nut to attach the ground wires. It's kinda hard to see in the picture, sorry that didn't get a better one.
I tested it with the multi meter to make sure everything was wired correctly.
The outlets I got are described as "tamper resistant". If you look in the outlet in the last picture, there are plastic pieces blocking the openings. They move out of the way when you plug something into it. The display where I found them said that it's supposed to be safe for kids but I think it will be great for keeping saw dust and other debris from getting into the outlets.
Step 4: Final Assembly
Now to wrap it all up. The outlets, box, and cover plate were attached to the mount plate which was then attached to the spool. Then I attached the knob and wrapped the cord around the spool.
Hope you like this, if you do, I'd love some votes! Thanks
After Thought -
In all honesty, the base/hand hold will probably bother me and most likely I'll end up taking this thing apart and rebuilding that and putting a bigger hole on top with a new mounting plate. If I do, I'll probably shorten how far the hand hold goes inside so it's easier to wrap my fingers around in there. Right now it's too close to the electrical box to get a good grip in there so I recommend cutting maybe a half inch off the shaft of the flange and cutting the other two pieces to the same height.
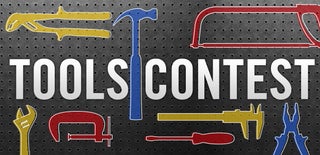
Participated in the
Tools Contest