Introduction: Facet V1 Velomobile
("The Vector" seemed too generic, and "The Polygon" was too geeky.)
The Facet V1 is made almost entirely out of Coroplast, the same corrugated plastic that many election signs are made from. The plastic shell is wrapped around a Catrike Expedition recumbent trike. This is a well-known build method, with dozens of examples all over the net. I'd suspect that people have been building coroplast shells over their trikes ever since both objects existed in the same Venn diagram. So this is definitely not a new thing, but my Instructable is hopefully one of the most comprehensive you'll find anywhere.
I designed the shell of the Facet in Google Sketchup, based on a design I obtained from a fellow in Belgium several years ago. After taking careful measurements of my Expedition, I re-sized and tweaked the shell to fit. After that, I unfolded the design in Pepakura. I had full-size patterns printed on a plotter, then transferred those to large 4x8 foot sheets of Coroplast. Finally, everything was assembled around my beloved trike, using a glue technique I perfected for this specific purpose.
The result is stunning (IMNSHO). If you've got a recumbent trike, you should build a shell for it. If you don't have a trike, GET ONE, then build a shell for it! Be sure to click any images that interest you for the larger version - the quality is much better.
All of the CAD files you will need are contained in Step 4. And of course, don't forget to vote if you like this project!
Step 1: Why Jeff? WHY??
But beyond that, there are many reasons why you'd want to build and ride a velomobile. Here's my top 7:
- Weather Protection. I ride in all weather conditions, and was tired of getting wet and cold.
- Speed Boost: The aerodynamic shell of the velomobile means you can put less effort into going the same speed. Or, you can put in the same effort and go faster!
- Enhanced Visibility: Cyclists can be hard to spot out on the road. Recumbent trikes are even harder due to their height. But what driver can say they didn't see a 3 meter long red, black and white missile hurtling down the road at 45 km/h? Blind ones.
- Cycling is GREAT for the environment: A velomobile is better, because you're more likely to ride it when the weather is bad instead of taking a car.
- It's great for your health: Seriously, is there any better way to get exercise than riding a bike?
- Increase Awareness: A velomobile gets people talking. I've been interviewed twice by the press, while riding my trike. Can you imagine the reaction a velomobile gets?
- Exclusivity: How many people own a velomobile? Less than the number of people who own Ferraris. A velomobile is more exclusive than a freakin' FERRARI.
That said, I've had doubters. I don't pay attention to them very much. They can be quiet and get back in their cars for all I care.
Step 2: So What's This Gonna Cost Me?
If you want to build The Facet V1 exactly as I did, here is what you will need:
- A Catrike Expedition recumbent trike ($2500 new, $1500-$2000 used)
- 7 4x8 sheets of 4mm thick Coroplast ($15-$25 each, depending on colour and where you get them)
- Printed templates ($60 at Staples)
- 3 2 fluid ounce bottles of TechBond SI Blue ($18 each)
- 2 bottles of TechBond PolyPrep ($18 each)
- A can of acetone ($6)
- Two L-shaped aluminum bars, 48" x 1" by 1/8" thick ($30)
- One flat aluminum bar, 48" x 1" by 1/8" thick ($12)
- Four 1" inside diameter rubber-lined P-clamps (about $4 each)
- Two 1.25" inside diameter rubber-lined P-clamps (about $4 each)
- Eight 1" #10 machine screws, with matching flat washers, lock washers, nuts and nylock nuts ($10)
- 24-30 neodymium magnets, 1" x 1/8" thick ($15)
- A 100 pack of 7.5" long zip ties ($10)
Please note that there are much cheaper trikes out there than the Expedition. You can build a shell around almost any trike, but if you might need to tweak the design of my shell to fit. I tested one other trike with my design, an older ActionBent (aka TW-Bents) TT, and it fit in the shell just fine. The attachment points for the supports would differ, however.
Step 3: Sizing Things Up
Gather up a bunch of scrap cardboard and lay it on the ground under the trike. It should extend past all the corners of the trike. Tape or otherwise secure the trike to the cardboard, so it doesn't move while you are taking measurements.
Using a carpenter's square and a level, marked out the following dimensions of your trike. I simply drew the "outline" on the cardboard, then measured them later with a tape measure.
- The very rear edge of the back wheel
- The front edge of the rear wheel
- The center of the rear wheel
- The furthest forward that the pedals will extend
- The center of the BB/pedals
- The very outside edges of the front wheels
- The front and rear of the front wheels
- The maximum and minimum outside extension of the front wheels when fully turned
- The width of the seat
- The height of the seat
- The lowest point on the trike (frame, chain, chain hanger, etc)
- The maximum possible height of your knee when seated, with feet on pedals
- The height of your shoulders when seated
- The height of your eyes when seated
- The top of your head when seated
- The width of your shoulders
Based on these measurements, you can determine how wide the velomobile needs to be, where the cutouts for the wheels should go, how tall it needs to be, and how long. If you don't want to design from scratch, you can easily resize, stretch or move various parts of the model I made to suit your trike. For instance, if you are shorter than I am, you could lower the hood and pull in the nose a bit. You may end up with a few extra folds here and there, however.
Step 4: About the Design
As I mentioned earlier, the design I used was based on the work of a fellow from Belgium. His model was called the bratmobile (pretty cool name!). I modified the design very little in terms of overall aesthetics, though the model itself is heavily retouched. I removed a lot of the internal structure as well as the "rider and trike" model inside, used as measurement reference. I stretched it lengthwise and increased the size by 20%. The model was also grouped into a bunch of smaller components, which I joined back together so that Pepakura could do its thing.
Many (if not most) coroplast velomobiles are much smoother and more rounded than the Facet. They are made by cutting long sections of coroplast and bending them slightly to shape. If you're after ultimate aerodynamics, this is the way to go. But my goals were slightly different. I wanted a design that was easier to build, very sturdy, and required little internal framework. I realized that if I used flat faces, the edges of the pieces could be joined together by long, continuous flaps. Those flaps would then become a sturdy "rib," helping maintain the shape of the shell. The joined edges could also be sealed against the elements. Another benefit of this technique is the weight savings - the entire shell including supports weighs less than 20 pounds.
The front wheels on the Facet are fully enclosed, rather than exposed. One of the trickiest aspects of a velo design, and especially one in which a trike is being retrofitted, is the front wheels. The Expedition features direct steering, where the handlebars are connected directly to the kingpin. In practice that means the rider's hands are relatively close to the spinning wheels, and when turning occupy the space where the wheel used to be. To be usable in rainy conditions the front wheels require some sort of fender, but how can a fender be attached when the rider's hand will crash into it? In the end there will be some compromise - there might be some spray inside the shell or movement may be restricted. But with an enclosed design at least there won't be any outside air or water entering through the wheel wells, as with exposed wheels.
Another tricky design decision is whether to include a windscreen of some sort. I've left that option open on this design. But for now, the rider's head will be exposed. Windscreens fog up, roofs catch the wind if not done properly. I'd rather continue wearing my all-weather helmet than not be able to see!
One final consideration is with regards to lighting. Obviously, if you don't ride with a light at night you're an idiot (sorry for being so blunt, but it's true). I made absolutely sure that everyone would see me at night, by using large translucent panels in the design that can be backlit by LEDs. Indeed, the panels are ten feet long and nearly ten inches wide on each side. Yeah, that ought to do it. Since you can't stick your hands out to signal anymore, there are integrated signal lights in addition to the headlight and tail lights. I will describe the electrical system in a separate Instructable.
Make sure you grab the file called "Facet V1 corrected.zip" when you begin your project. I've included the original files that I used to build my original velomobile for your reference, but these should not be used! See Step 19 to find out why...
Step 5: Glue Testing
For the benefit of all mankind, I spent several weeks tracking down and testing various glues for bonding Coroplast together. Coroplast is made of polypropylene, a notoriously difficult-to-glue substance. Its low "surface energy" makes it impervious to water and many chemicals, but also means most glues won't stick any better than they would to a melting popsicle.
An additional difficulty I ran into was designing a glue joint with high peel strength - some glues worked just fine during a shear strength test, but failed miserably when peeled. This is important because of how the flaps are joined - pulling two panels apart means that the glue peels rather than shears.
And finally, since I intended to ride in sub-zero celcius temperatures (0F range), the glue had to stay strong when icy cold.
Long story short, the winner was Loctite 406 cyanoacrylate (superglue), with lacquer thinner as a primer. It is designed specifically for difficult-to-bond plastics like polypropylene. However, I used Tech-Bond glue for most of the construction because it's four times less expensive.
The glues I tested include:
- Loctite 406 CA
- Gorilla Glue brand CA
- Tech-Bond Blue CA
- Gorilla glue
- 3M 3764 "polyolefin bonder" hot glue
- regular hardware store grade hot glue
- Lepage PL Premium construction adhesive
The primers I tested include:
- Lacquer Thinner
- Acetone
- Loctite 7649 primer
- heat (heat gun, propane torch)
- sandpaper
For each of my samples, I first did a shear test. If that passed, I did a peel test. If the result of the peel test was good, I moved on to a secondary peel test where I ran a bead of glue in the valley formed by the folded tabs. If that joint proved passable, I tossed the same in the freezer to test its cold resistance.
Glue Test Result Highlights:
- The gorilla glue CA, gorilla glue, and PL Premium pretty much snapped right off. In fact, I was able to peel off the glue and use the test piece again.
- The 3M 3764 hot glue had great shear strength, and I was able to get an unbreakable bond by running a bead of it along the valley formed by the folded tabs. But when frozen it snapped like a twig.
- Hardware store hot glue was similar to the 3764, though not quite as strong.
- Acetone doesn't seem to do much as a primer. Neither does the Loctite 7649.
- Heat was an OK way to prep the surface for gluing, though it is very difficult to control.
- Sandpaper doesn't seem to offer much of an improvement over a chemical primer. It's not worth the elbow grease (or the risk of marring the visible surface of the plastic)
- The best primer was Lacquer thinner. As a bonus, it's dirt cheap; one small can will be more than you'll ever need
The best glue joint was definitely Loctite 406 with lacquer thinner as the primer. By simply running a bead along the valley formed by the folded tabs, a joint stronger than the plastic itself can be achieved. My 1" wide test strip was so strong that neither me nor my wife could break it. A friend at work finally tore it apart, after stretching the plastic itself a few millimeters. Finally, the coroplast itself broke rather than the glue bond. It was not weakened by cold; I was unable to break it even at -15C.
A close second was Tech-Bond SI Blue and SI Black (the difference is that the Black is thicker, and doesn't run as much), with Tech-Bond PolyPrep as a primer. The joint is also unbreakable at room temperature, and at -15C can only be broken with great effort. At one-quarter the price of Loctite 406, I used Tech-Bond for most of my construction. SI Blue was used for most of the joints, and SI Black where larger gaps needed to be filled.
I should add that it would be perfectly acceptable to skip the glue completely and use zip ties instead. By poking holes along the folds and "sewing in" the zip ties, a very strong joint can be achieved. But it won't be as pretty as the glue joint, will leak water in the rain, and may even take longer. Also, I was able to snap the single zip tie on my 1" wide test strip; something I couldn't do with glue.
More information on bonding Polypropylene can be found in this research paper: http://scholar.lib.vt.edu/theses/available/etd-62398-182953/unrestricted/Chapter2.PDF And in this forum: http://www.christinedemerchant.com/coroplast-glue-test.html
Step 6: Unfolding
I talked a bit about the design in step 4. I won't be of much greater help in that regard, I am still very much a 3D CAD n00b. Suffice it to say, you'll need to do a design that fits your trike, and that is a "surface" model rather than a "solid" model - something that can be unfolded. If you're using CAD software with a sheet metal function, use it (if you know how!)
Fortunately, a wonderful little program called Pepakura exists. It allows us to "unfold" a model into flat sheets, and add flaps for easy assembly. I bought the full version of the software so that I could save and export the files to dxf for printing.
I wasn't able to afford the full version of Sketchup, however. Pepakura had trouble importing the exported Google Earth model generated by the free version of Sketchup. So, I used a plugin called "Obj Export" which exports the design as (you guessed it) an .obj file. Pepakura had no problems with this, and imported the design beautifully.
Once imported, the first step is to unfold the design. Pepakura will try to connect all the pieces together - not really useful in this case. Using the Divide/Connect Faces tool, I went around and divided the pieces first by colour (the design uses red, black and translucent coroplast), then into smaller sections based on where I wanted the internal support "ribs" to be. This is the most lengthy process in Pepakura, and an important one, too. Putting the joints in the right place will not only ease assembly, but also increase the strength of the shell. The flaps also provide a convenient place to attach the shell to the frame of the trike without having to glue extra stuff to the flat faces of the shell.
At this point I scaled up the design to "real life" proportions. The exported file from Sketchup included a square exactly 1m in each dimension. A scale value of 25.4 was just enough to get everything the right size - the square measured exactly 1m in Pepakura using the measuring tape tool. The page size was also altered - 900mm wide by 2000mm tall (roughly 36" by 84"). These page sizes were chosen with a wide-format plotter in mind. It would be possible to print out the whole thing on 8.5x11 paper, but not very practical!
Using the "Edit Flaps" tool I added 30mm wide flaps to each edge (ON/ON). The angle of the flaps is also set to 45 degrees - by default Pepakura makes some of the flaps taper off at a very shallow angle, which isn't great for assembly. I then arranged the pieces onto as few pages as possible.
Finally, I exported the pages as "multi-page DXF," and converted the DXF files into a format the plotter could handle: PDF. This was done in Adobe Illustrator by importing the file, changing the document size, then re-saving as PDF. If you're going to have your patterns printed by a third party, it might be a good idea to stick with PDF so that there are no issues with compatibility or scaling.
Attachments
Step 7: Print the Patterns
The best way to get a set of patterns is to print them out on a plotter or other large format printer. I'd recommend a 36" or wider plotter, to fit the most pieces on a single page. This is how I sized my PDFs. The plotter or printer should print on rolls instead of cut sheets (which are usually just 48" long). Several of the pieces are longer than 48", so they wouldn't fit!
I was extremely fortunate and had them printed by the print shop where I work for the cost of a roll of paper. That saved a lot of money! Still, I could have had the patterns printed out at Staples (an office supply store) for about 39 cents a square foot - about $70 or $80. There are 8 36"x84" sheets. If you're having the patterns printed, make sure that they are printed at 100% scale! Regular paper with black and white printing is fine.
Step 8: Transfer the Patterns
As I mentioned before, I arranged my patterns for best fit on 36" wide sheets, but not by colour. Before transferring the patterns to the coroplast, mark on the patterns what colour each piece will be. I used red, clear, and black. If necessary, use the original Sketchup file as a reference. Now cut out the patterns, leaving a half-inch margin around the edges of the pieces. Sort the pieces into separate piles by colour.
I bought my coroplast panels brand new in 4x8 foot sheets from Home Hardware, a hardware store in Canada. If you can't find sheets at the hardware store where you live, or they cost too much or are the wrong colour, call around to some local sign shops. Most will be happy to supply full sheets in a number of different colours. White will almost definitely be in stock, but some colours may require special order.
Lay out pieces one colour at a time. I ended up using one sheet of clear, one sheet red, and three sheets black. Fit the templates together as close as possible to save on material.
You'll notice there are "flutes" that run in a certain direction. In certain cases you'll want to make sure the pattern is aligned with the flutes - square pieces, for instance. But for the most part, since most of the pieces are triangles, it doesn't really matter which way the flutes are pointed. You'll be cutting and folding "against the grain" on almost every joint, so why waste material trying to line up the flutes? Note that if you are building a "curvy" velomobile shell, flute direction becomes more important.
With your patterns placed on the plastic, stick them down with masking tape in key points. Be sure not to overlap any of the pieces! With a pin or other sharp pointy object, poke a hole through the template into the plastic at each intersection of lines. These holes will be used later as co-ordinates for marking out the pattern.
Once all the patterns are marked with the pin, peel off the masking tape on one of the patterns, but leave it in place. With a permanent marker mark the position of the poked hole with a dot. Visit all the points of the pattern, marking each with a dot to form a "constellation" of points. On white and red coroplast I used a black Sharpie. On black coroplast, I used a silver sharpie. Don't worry about marking up the plastic; the marks come off easily with acetone without damaging the plastic.
Now, with a straightedge, draw lines between the points using a permanent marker. Use the pattern as a guide. Once all the lines are marked, there should be an exact copy of the pattern drawn on the plastic! Use this same method for the rest of the templates: poke, mark the holes with a marker, draw lines between the points.
With all the patterns transferred to the coroplast, you may begin cutting out the pieces...
Step 9: Cutting and Creasing
Each piece may now be precisely cut with a box cutter. Make sure you use one that is at least somewhat ergonomic - I started using a folding type and it was painful. I really like the Irwin model I bought specifically for this project. On a cutting board, cut around the perimeter of all the pieces. The great thing about using tabs is that you don't have to be super-precise when cutting them out, but do try to stay close to the line.
I was able to transfer and cut one 4x8 sheet per night, in case you're wondering.
Creasing is another matter. All of the tabs will need to be folded over, and they need to be folded accurately or the pieces won't fit together well. And some of them are pretty long, so it's difficult to do by hand. So, I built a lightweight "bending brake" for the job. Be sure to check out the separate instructable documenting its construction.
Using the bending brake, fold all the creases as accurately as possible. This design relies more on precise folding than on precise cutting, so here is where you need to take your time. You may choose to fold everything at once, or simply fold pieces as they are being assembled.
Most of the folds are pretty sharp, and you'll find that the coroplast simply doesn't want to stay bent that far. In cases like this, you can hold the flap folded over, and gently heat the bend with a heat gun until the bend softens a bit. Try not to heat the plastic so much that it gets glossy and starts shrinking, though.
Step 10: The Ultimate Glue Joint
The basic idea is to clamp the tabs together, then run a bead of glue along the resulting seam. The glue seeps into the seam making it super strong, yet also resistant to "peel" stresses that result from applying the glue to the faces of the tabs only. I found that large binder clips, which are dirt cheap from office supply stores, do a great job of holding the tabs together.
Here is the detailed method:
- Dry-fit the pieces being joined. Clamp the pieces together with large binder clips, and make sure everything lines up ok according to the model. Now is the the time to make sure the pieces being joined actually belong together!
- Disassemble the pieces, and treat all the tabs being glued with PolyPrep (or lacquer thinner, if using Loctite 406 adhesive). Make sure the room you're in in well ventilated - this stuff will do bad things to you if you're not careful! Let sit for a few minutes, and try not to touch any of the tabs once they have been treated.
- Reassemble the pieces using the binder clips. Space the binder clips about 1-2" apart, depending on how much force is needed to keep the flaps held together without shifting.
- Run a bead of glue along the seam. If your velomobile will only be used in warm weather then you can use the 3M hot glue. But if your velo will be used in cold weather, use Loctite 406 or Tech-Bond SI Blue.
- If using hot glue, wait for the glue to harden before moving the pieces. The clips may be removed after the glue cools. If using CA glue, try not to disturb the pieces for a few hours. The clips can be removed after 12 hours.
- If using hot glue, run a second bead of glue between the tabs from the back. This is an optional step, but it improves rigidity and strength.
Use this method for all the assembly steps coming up...
Step 11: Shell Assembly
If you have the space, I suggest working from the bottom up. This will make it easier to add the support structures between the trike and shell (more on that later).
In my case, I built the front and rear separately until they were nearly too large to fit through the door. The key is to avoid installing any of the hood sections until after the trike is attached to the shell.
I suggest starting with some of the large sections first to get the hang of it. Line up the flaps so that the resulting faces are co-planar, and the ends of the flaps line up as well. Lay out the pieces so that the joint is facing upwards, so that glue applied to the seam flows down between the flaps. Lay a bead of glue along the seam, and try not to disturb the joint for at least an hour. You may join as many seams as you have clips for!
After 12 hours (at room temperature), the pieces may be moved and joined to other sections. Remove the clips and set them aside for the next joint. Test-fit, align so the seam faces up, and apply a bead of glue.
Continue in this manner until everything but the three hood sections are attached.
Step 12: Shell Supports
There are a few different supports that will be needed. The Anti-Sag bars, boom supports and seat supports may be measured out before the sides of the velomobile are installed, which will save you a lot of awkward bending over.
Anti-Sag Bars
The "ribs" on the bottom of the shell are strong, but not strong enough to support the weight of the entire shell without sagging! Two aluminum bars are needed to add a bit of extra strength. These bars span the width of the shell, and are placed along the ribs in front and behind the front wheels.
Grab the L-shaped aluminum bars and cut them to length, so they fit in the space inside the shell. Note that the bars will not be same length - mine were about 39" and about 37". Since the actual width of your shell might be a bit different from mine, be sure to measure before cutting.
The aluminum bars are fastened to the shell using zip ties. Along the length of each bar, on both faces, drill pairs of holes spaced 1" apart at about 3" intervals. I used a drill press for this task, using a 3/16" drill bit. Clean up the holes with a knife if there are any burrs left on the metal.
Remove the trike if it's still in the shell, and lay the bars in place. Using an old soldering iron or a handheld drill, punch a hole through each hole in the bar and through the coroplast. In this way, the holes will be perfectly aligned. Then, loop a zip tie through each pair of holes and tighten. With both sets of L-shaped bars installed, the shell will no longer sag.
The Boom Support
The boom support is made of a piece of scrap coroplast (there should be enough left from cutting out the pieces). It stretches between the boom of the trike and a section of "rib" that runs down the center of the shell. If you're building your velomobile around a Catrike Expedition, you can use the design in the attached file. Otherwise, you'll need to fashion your own in a similar style.
First, prop the velo shell off the ground about 2.25" (I used a few pieces of scrap wood) - this is how far off the ground the shell will be. Then center the trike in the shell. The frame should follow the center rib, and the wheels should be centered in the wheel wells. The distance between the boom and the center rib is the space the support needs to be customized for. Aim for about 6" of material wrapped around the boom, and flare it outwards at the bottom.
With a drill or hot soldering iron, make holes for the zip ties to pass through. Don't attach anything yet, however.
The Seat Supports
The seat supports are made of short pieces of flat aluminum bar that connect the seat frame to the anti-sag bar. These pieces should be about 4" long. Drill a hole at either end to accept a #10 (or equivalent) machine screw.
Start by clamping a 1" inside diameter rubber-lined P-clamp to the seat supports closest to the ground. Use a flat washer, lock washer and plain nut. Place the trike inside the shell again, and center as precisely as possible. Place the supports between the P-clamp and the anti-sag bar, and determine where an appropriate hole should be drilled in the anti-sag bar. Drill the hole with a hand drill. Note, you may need to remove a zip tie if it is in the way. This is OK, since the screw will hold the coroplast to the bar instead.
Rear Axle and Upper Seat Supports
These four supports must be installed after the tailbox bezel has been glued in place (see the next step). The reason for this is that the spacing between the seat and sides of the shell must first be set. So, go ahead and do that now.
These supports are a hybrid of coroplast and aluminum. They look like over-engineered flyswatters. Cut out eight trapezoid shapes from some scrap coroplast. I cut four from black (for the rear axle supports) and four from transluscent (for the upper seat supports). Drill holes as marked using a drill or hot soldering iron. Now, cut out four lengths of flat aluminum bar. Two at about 7", and two at about 9". At one end of each bar, drill holes that correspond to the holes in the coroplast pieces. Then fasten the coroplast pieces to the bars as shown using zip ties.
The rear axle supports attach to the rear triangle of the trike close to the rear axle (thus the name), using 1.25" rubber-lined P-clamps. Ensure the rear of the trike is centered with the rear of the shell, and dry-fit the support between the rib along the bottom edge of the shell and the P-clamp. The coroplast end should be pushed onto the rib as far as possible. With a drill or hot soldering iron, transfer the positions of the holes onto the rib. Then, mark where the hole needs to be drilled in the aluminum bar to align with the P-clamp. If the bar ends up being too long, cut off any excess. Do this for both supports.
Remove the support and drill the hole in the P-clamp end. Then reinstall the support into the shell, by first threading in the zip ties (this is tricky) and then bolting the P-clamp onto the support. These two supports carry the weight of the rear of the shell, and prevent it from "fish tailing."
The upper seat supports are done in a similar manner. This time, the support stretches between a 1" diameter P-clamp mounted on the upper-most part of the seat frame, and a rib that runs along the side of the shell. As with the rear axle supports, center the trike, dry-fit the supports, mark the mounting locations, drill then, and mount with screws and zip ties. The upper seat supports prevent the shell from shifting too far left or right.
With these supports in place, the trike can actually be ridden! Go ahead; I know you want to!
Step 13: The Tail Box
The tail box is comprised of two pieces, the tail box bezel and the tail box lid. The lid is attached on only one end, which acts as a hinge. This makes it easy to access the space over and around the rear wheel.
Once the trike is inside the shell and the seat & boom supports are installed, the tail box bezel may be glued in place. As before, clamp everything in place with binder clips and make absolutely sure that everything is square. That is, where the tail box lid will eventually be hinged, ensure all the vertices are perfectly aligned. You may even want to temporarily clamp on some of the other hood sections just be absolutely sure.
Once the bezel is glued in place and the remainder of the supports are installed, the tail box lid may be installed. It is glued along a single tab directly behind the rider's head. Clamp it in place and make sure it lines up well with the bezel.
The tail box lid is held down with magnets. You may choose to hide the magnets between the layers of coroplast (see the section, "Cutting out the door") or you can simply glue them directly to the face of the coroplast. After all, the magnets won't be seen when the lid is closed.
I used five pairs of magnets as in the photo. Glue them to the tail box bezel first. Don't forget to spray the coroplast with PolyPrep first! When the glue has dried, stick on the mating magnet and apply glue to the top. Close the tail box lid so the magnets come in contact with the tab, and tape in place until the glue has dried.
With five pairs of magnets, the tail box stays neatly in place and does not move around when the velomobile is in motion.
If you like, you may also choose to permanently attach the tail box lid, or leave it off completely and make the tail box bezel a solid piece.
Step 14: The Hood Panels
The hood section that surrounds the rider's head goes in last. You can either cut out the hole ahead of time or you can do it after the section has been glued. If you do it before, it will be easy to reach through the hole and place clamps along the seams. But if you've got long arms you should be able to reach through the tail box.
I purposefully did not design an exact location for the hole through which the rider's head protrudes. Mainly because I wasn't sure where it should be. Ha. When cutting the hole, try to stay at least 2.5" away from any of the seams. Beyond that, make it any shape you like. In the end the hole I cut was a trapezoid, more or less matching the outer edges of the hood piece itself.
Step 15: Cutting Out the Door
Are you wondering how the heck you're going to get in? So was I, up to the last moment. Fortunately, things turned out favorably.
The door must allow enough room for the rider to step in the velomobile (onto the seat), lower themselves in, and stretch their legs towards the pedals. The sides of the velomobile are quite high as well, so ideally the door should lower the step-over height as much as possible as well. With these criteria in mind, there's pretty much only one way the door CAN be done.
Using a permanent marker and a straightedge, I marked out the opening for the door. It extends from the head-hole down the side of the shell into the translucent side. There it runs for about a meter until going back up the side and across the hood. The door is therefore hinged about 2.5" away from the opposite edge. Take your time to get this right. MY solution seems to work quite well, I suggest you copy it.
When you're satisfied with the door dimensions, cut them carefully with a sharp knife. Take your time so the knife doesn't accidentally go astray and damage the coroplast. A few of the ribs will need to be cut where the door edge crosses - cut these carefully from the inside. Once the outline has been cut, hold a straightedge along the door "hinge" and bend it back a few times until the plastic bends easily. Make sure the coroplast only bends where you want it to! Use a heat gun if you need to.
The last step is to add some supports for the door. Glue some scrap pieces of coroplast along the inside edge of the door frame, so that when the door closes it rests on the supports.
A nice, elegant way of holding down the door is with embedded magnets. These allow the door to close seamlessly and securely. Choose several points around the door (I suggest 7 or 8) where you want magnets mounted. Using a sharp knife, excavate out the coroplast "flutes" so that only the top and bottom plastic remain - and a thin magnet can slide in between. Cut out sections on both the frame and the door. Glue magnets into the door frame locations first, and let the glue dry.
For each magnet location, determine which way the magnet in the door should face to attract the mating magnet in the frame. Apply glue to the magnet and slide it into the cavity, then close the door. The magnet should shift slightly while the glue is still wet, and align itself perfectly with the magnet in the door frame. Make sure no glue oozes out and glues the door shut!
Step 16: Finishing Up
Well that's the meat of it.
You may have noticed that the hood of the shell sags a bit. If so, you can add additional supports along the top edge using custom-cut pieces of scrap coroplast. I had to add once piece close to the door hinge.
If there are any marks left from permanent markers, wipe them off with acetone.
Another thing you may have noticed is a white haze on the red and black coroplast (it's on the translucent pieces too, you just can't see it as well). The white haze is a result of the cyanoacrylate glue off-gassing and sticking to oils on the plastic (most likely, your fingerprints). This haze can be removed using acetone and a rag. Just make sure the acetone doesn't touch the seams, or it may de-bond the glue.
If there are any gaps in the glue seams, or if the glue sank in deep, you can go over the glue joint with more glue. For filling large gaps, I recommend Tech-Bond SI Black. It is thicker and fills gaps better than Blue or Loctite 406.
Step 17: What About Lights? and Storage? and Fenders?
Yes, there is more to do!
I will document the lighting system in a separate Instructable, when it's finished. I designed the Facet V1 with translucent panels for a very specific purpose - so that they can be illuminated from inside. My plan is to add RGB LED light strips along the entire length of translucent paneling, so that I can change the colour that the Facet glows at night. It's gonna look really cool. Of course, there will also be signal lights, a headlight and tail light added as well.
The amount of storage and where it's added is very much up to you. It would be easy to glue a few bins to the interior of the shell to toss in tools, food, etc. If you need more weight capacity (like for carrying groceries) then I suggest adding some aluminum framework to the trike frame itself.
And fenders! There are fenders available for the Catrike which should deflect most of the spray back out the wheel wells in the floor. Be sure to install them before the trike is built into its shell! Another option is to craft custom fenders out of coroplast. This is what I did for my rear wheel, and what I'll probably do with the front wheels as well. I will add those instructions to this Instructable when they're finished.
Step 18: Summary and Thanks
For a few hundred dollars, you can add a shell to a recumbent trike. The benefits are numerous, including aerodynamics, weather protection, and enhanced visibility on the road. I was truly fortunate to have found a mostly-finished design that I was able to tweak to suit my needs. You may use my design files for your own velomobile, or design from scratch. If you do so, make sure that everything fits inside - that's probably the most important part.
I'd like to thank the following people for their help and support:
Brecht Vandeputte, for supplying the original Sketchup file that I modified for my design. Without this, I probably wouldn't have make it past the "dreaming" stage.
The Velomobiles -- Coroplast Group on Facebook - What a great group of clever, encouraging and helpful folks!
My wife, for putting up with my crazy ideas and the associated costs (money, time and space). She's simply the best.
And the Instructables community, for continually inspiring me to make bigger and better things!
Step 19: Bonus Chapter: Mistakes I Made.
Oh, there were mistakes made along the way. Some were big, some small. Some visible, some not. But rest assured, everything was corrected before I published my plans.
Oh, you'd like to know where I messed up? Sure! Perhaps when you build your own velomobile, you can avoid these blunders.
Horrors! The hood is too high!
Early on I had a suspicion that I had given too much clearance for my knees and toes under the hood. When the trike was finally inside the shell and it was almost time to close it in, my fears were realized: The hood was fully 2.5" too high - I wasn't able to see over it! As a result, I had to slice 2.5" of coroplast off the bottom of the entire structure, and re-glue everything back together again. Luckily it went pretty smoothly, and for the most part you can't even tell.
The nose cone looks a little funny...
I should have properly bent the "valley" in the nose cone. Or better yet, I should have made the valley a seam. But I didn't, and as a result I had to glue in a support between the two sides to pull everything together.
Soldering iron: great for holes, not so great for excavating flutes.
I originally thought that the soldering iron I had used for poking neat holes in the coroplast would also work great for excavating out the flutes, to make room for a magnet. I even did a test with a piece of scrap that went OK. But oh, did I ever mess up when I tried it again on the velo! I melted into the faces on one area and it looks kinda lousy. A sharp knife works much better.
Argh, it's dripping!
I dripped glue on the coroplast in a few places. Or rather, I applied a bit too much glue to a seam and it ran out a bit. Of course I didn't notice until after the glue had set. And then there were the times when I accidentally glued a clamp to the tab. Let me tell you, this glue sticks just as well to metal as it does to plastic. Sheesh.
Whoops, wrong order...
I should have worked from the bottom up. That would have made it a lot easier to attach the trike. But on the other hand, if I'd done that, lopping 2.5" off the bottom would have been much harder...
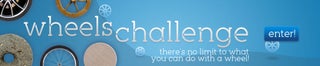
Grand Prize in the
Wheels Challenge
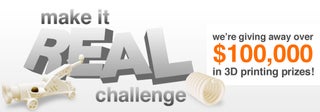
Runner Up in the
Make It Real Challenge
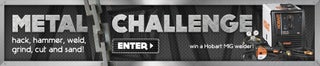
Participated in the
Metal Challenge