Introduction: Fast Attraction
Ooops, You Did It Again...knocking over a box of screws, nuts, needles or similar magnetic stuff and you need to get rid of the evidence in a hurry. In the past, you might have grabbed a strong magnet and found that it can be dreadfully annoying to clear the magnet afterwards - and the little bits of iron dust that will inevitably cover the magnet is next to impossible to remove completely.
That was yesterday (or last spring to yours truly). Enter the MagPick (&Release) that I have used quite a bit in the last year, including for stuff where I wouldn't normally care to use a magnet.
Step 1: Supplies
I did try several combos of plastic tubing and magnets, searching for something strong and reliable, but all the tubes I had in stock was either too small a diameter for a magnet of a suitable strength, or too large for what would be sensible and there was the little detail of sealing one end flat without getting a weak seal (it takes a bit of hammering every time it grabs a bolt or similar).
Pondering my options, it struck me that a syringe might be usable, so I tested the different magnets at hand, for best fit in the syringes and found a magnet that could move freely, without a huge clearance, in a 5ml syringe (11mm or 7/16" inner diameter, but it probably vary with what's available). Depending on what magnets you have at hand or can find in a shop, you may need a different size, but you have to check that out locally.
Regular syringes comes in two major types (plus a lot of specialized ones, which is unimportant here), Those with a rubber cap as the seal on the plunger and the slightly cheaper ones where the seal is an integral part of the (nylon) plunger. For this project, you either need the rubber capped type, or you can modify one with a nylon seal, if you want to save a (very) little or can't get hold of the other types.
Materials needed::
- 1 Syringe (or get a couple, they are handy for a lot of things)
- 1 cylindrical neodymium magnet (or a couple of flat disc types), as with syringes and chocolates, one is never enough!
- A short piece of wire or similar, preferably the "rubber" covered variety - about 7..10cm (3..4")
- Glue that can bond nylon (contact cement or some types of Cyanoacrylate-/Superglue)
Tools needed
- Side cutter (preferably flush cutting), but can be substituted by large scissors or, if you think you have too many fingers a box-cutter will cure that.
- A drill slightly larger than the size of your wire
- Emery paper around 220..400 grit, a nail file or any similar fine cutting file
- A lighter, or any small direct heat source that can melt and form nylon (like a hot-knife)
Optionally a small piece of PTFE covered baking paper or a painters (steel) spatula for forming melted nylon
Step 2: Modifying the Outside of the Syringe
The business end of a syringe, where a hypodermic needle is usually mounted, needs to be shortened and melted closed, as flat as possible and completely sealed. Do remove the plunger before continuing with that!
I realized that I should have cut further down the nib, to get a little more than half of what you see in the second pic (orange), as it was a bit of work, trying to move the excess melted nylon around.
In the last pic (blue), you see the end result. Regrettably, I have but two arms, both busy trying to get the end result, so I haven't got pics of the process, but it's simple: Heat the remaining part of the nib, but be careful not to set it aflame (blow it out if that happens), and use whatever you have at hand to move the nylon around to close the end and make it flat (slightly conical really) as the rest of the "flat" part of the syringe - I used the body of the lighter (carefully) to rearrange the "lava pit", but anything that the melted nylon won't bind to will do. The piece of baking paper mentioned, laid out on a flat surface, will aid in flattening, although I didn't use it, as it played out well enough.
Whatever method you use, don't get melted nylon on your digits or any bare skin. It will have a tendency to cling on and you might get a nasty burn!
Step 3: Attaching the Magnet
Mounting the magnet to the plunger is a quick job, if you have the rubber capped variety. Just pop off the cap and put it in your material bin for a future project.
If you have the kind where the seal is an integral part of the plunger, you need to reduce the diameter of the seal, to allow the plunger to move freely with no friction.
That done away with, grind the end of the plunger and the magnet on the mating surfaces, to remove grease and roughen up the material for a better bond.
When you glue the magnet to the plunger, be careful to get them aligned/centered, even more so, if the magnet is a tight fit, in the barrel of the syringe,
Make sure the glue is totally set before you test it out!
Step 4: Mounting a "Retractor" Loop
When the glue has set,.. To make it easy to use single handed, you need to add a loop for lifting the plunger.
I used a bit of wire covered in a rubbery "isolation" layer. This kind of wire is mostly used for plant care. Anything else goes - plastic or leather could be used as well.
Drill a hole, slightly wider than the wire diameter, right under the flat side that you push on the syringe. The plunger has got a cross shaped stem and drilling through the ~1mm nylon is not a big deal, you can twist the drill through it with your bare hands (I did - it was quicker than to go fetch the proper tool).
Thread the wire through the hole and make a loop sized for the finger you intend to use and twist the ends. Cut the wire and bend any sharp ends inwards towards the center of the stem.
If you chose a different material, you may need glue or a knot to make it happen.
Step 5: You're Done... Well Almost
This was the end of this project until I realized that it wasn't behaving extremely well without a collar. I had thought that I could perhaps get away without it, but whatever you grab will have a very strong tendency to travel along the outside of the barrel, when you retract the magnet.
Took me some time to find suitable material for this, but I still had fun with it - Oh how revealing it was to grab such amounts of nasty from a single sweep over my work desk.
Step 6: Add a Collar
I had a go with thin PET plastic from some sales packing material, but it was too thin and couldn't stand the force.
After rummaging through my collected treasures (which my S.O. disrespectful call "crap"), I ended up with some plastic from a ring binder cover, it was 0.8mm thick and had just the right amount of stiffness for the purpose.
I drew and cut a disc close to 30mm in diameter and with the inside hole slightly less than the outer diameter of the syringe (as it's hard to make the hole smaller), and used emery paper wound around a pen slightly, to widen it to fit tightly on the syringe.Finally, i heated the edges (very carefully) to polish them, although it was just for visuals.
I had expected to glue the collar to the syringe, but as it was such a tight fit, i kept it un-glued, to find the best position and it's still not glued. Should it become too loose at some point, contact cement, a splash of RTV silicone or even a bit of hot melt glue can be added.
After having used the MagPick(TM) for a host of jobs - from seeking runaway nuts, to sorting boxes with small compartments full of screws and such, where room is needed for an intermediate screw size and similar, I really treasure this more and more each time I use it.
Avoid bleeding fingertips from sharp pointed screws and do it way faster than with your bare hands - most compartments can have their content moved to another in a few milliseconds (give or take) - with bare hands, it would take a lot longer, and include loud expressions of the third kind ;)
Step 7: Aaand Enjoy
So... Here's your new (Omni-)fix - Just Say Yes!
If you reached this point, thanks, your company is much appreciated and while this may still seem obscure to you, its efficiency has surprised me on several occasions and I'm sure it has yet more applications than what I've discovered so far.
And it's so darned cheap to make - perhaps make more than one. Most of your creative friends might find it useful and we all love a gift that shows us that somebody cares about us :)
Possible improvements:
A method for "Retract on Squeeze", like I've seen on some "bee sting suckers" would alleviate finger fatigue if used extensively, paired with a light spring return, is the most helpful improvement I can think of.
Visually... Use a thin walled brass tube, with a flat bottom plate braced on, all polished to shine like gold - mahogany plunger for that steam punk atmosphere perhaps.
Other things... You tell me.
If, correction, when you make one, please post a pic of it, I'd love to see in which direction you are gonna take it and what you are going to use it for.
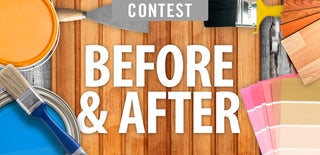
Participated in the
Before and After Contest 2016