Introduction: Fiber Optic Sea Warrior
As a designer who is mostly interested in illuminating us all by finding new ways to use lighting in costumes, bioluminescent sea creatures are naturally a very big influence on my work. So, when Andre Mistier, frontman of electro-rock band The Adversary, asked me to design him an illuminated stage look with an aquatic theme, I was very excited. I wanted to push myself to use some new techniques and materials, so I brought on an awesome collaborator, Ashley Newton (Technorainbows) of Sustainable Magic, to help design the lighting system for the outfit. I had originally planned to use primarily el wire and a few LEDs, but Ashley suggested that I could get a similar but more interesting effect by using large diameter, side-light fiber optics instead. It was a brilliant idea. The fiber optics really took this design to a new level and allowed me to discover a material that I will certainly be using a lot more in the future.
Side-light/side-glow fiber optics are a fairly new type of fiber optic strand that emit a glow along their entire length when a light is shone into one, or both, ends. They look a bit like el wire, but they can take on any color based on the light you are shining into them, and they don’t have the shorting issues and soldering annoyances that make el wire tricky to work with. The final outfit I created was quite a complex undertaking and consisted of three pieces:
A Headpiece: which incorporates laser cut leather, el wire, side light fiber optics, individually addressable RGB LEDs (WS2812), an Arduino microcontroller, a lithium polymer battery, an on-off switch, and a component to hold the fiber optics in place, which Ashley designed and 3D printed on a Makerbot in Ninjaflex TPE flexible filament -- a filament with properties similar to rubber.
A Chest Harness: made primarily of laser cut leather, 3D printed chest and shoulder shells which I designed and printed in two materials on the Objet printers at Instructables, and inner components designed by Ashley and 3D printed in Ninjaflex on the Makerbot, as well as an Arduino microcontroller, an on-off switch, a battery, individually addressable RGB LEDs, and 6mm diameter side light fiber optics.
A Pair of Pants: which I embellished with leather and six 3D printed shells which diffuse individually addressable LEDs controlled by a microcontroller and powered by another lithium battery.
This project was an adventure. I ended up completing it on the playa under very trying conditions with an immense amount of help from my amazing boyfriend Bruce Lindsay. So, some of what I learned in this process what not to do, and how to pull together something incredible in a harsh environment, with limited sleep and a lot of dust.
*Photos in this step by Hep Svadja, heptic.net
Step 1: What You Need
A lot of time and patience, an awesome collaborator who knows about fiber optics and LEDs, and a kick ass boyfriend willing to hand sew for hours by headlamp on the playa….
…Oh, and of course:
A sketch of your design
A computer
A vector design program like Adobe Illustrator or Corel Draw.
3D modeling program. I used Autodesk Fusion 360 to model the shells on the chest, shoulders and legs. Fusion 360 is an Autodesk modeling program still in beta testing and thus available for free online here. This program has a lot of potential because it incorporates both solid modeling and organic, sculptural modeling, but is still a bit buggy and takes some patience. My collaborator, Ashley used Solidworks to model the nodes that attach the fiber optics to the LEDs.
A 3D printer: We used two very different kinds of printers for this project.
I printed the shells on a Objet Connex 500 printer at Instructables. This is a UV cure resin printer that can print in two materials simultaneously, which is how I got the black and grey stripped effect on the shells. If you don't have direct access to a printer like this, you can send your file to a printing service like Fathom, or you could print the shells in one material only.
Ashley printed the nodes that attach the fiber optics to the LEDs on a Makerbot in Ninjaflex TPE flexible filament, which was essential for it’s strength and flexibility.
A laser cutter: (if you don’t have access to your own laser cutter you can send your file to an online laser cutting service like: https://www.ponoko.com/, or look up local laser cutter in your area). I really don’t recommend cutting out this design by hand, but it would not be impossible.
A sewing machine: We hand sewed a lot of this design but in the future I might sew it by machine. A home machine may have trouble handling the thicker leather so I would advise using an Industrial machine or even a walking foot if you have access to one. Either way, a leather specific needle makes a huge difference.
Leather: I used two kinds of leather, one white, one dark grey. Both stamped with a reptile pattern. Though both were relatively sturdy, my white leather, was a little thicker stiffer than the grey, which worked well. You will need a lot of both to complete this whole project. I probably used about 1/4 to 1/2 a hide of each. You can order leather online from places like Tandy.
A stiff translucent fabric: you will need about a yard of this to make the base for the el wire “fins” on the headpiece. I used a whitish netting, but something with a tighter weave would have worked better.
Fabric for the gathered trim on the headpiece: I used a stiff black tricot, but you could use anything fairly thin and stiff.
Side light (or side glow) fiber optics: The most cost effective way to get these is to order them in bulk from China from places like aliexpress.com, but this can take a few weeks. There are a few different kinds of fiber on the market which can be confusing to filter through. One kind has a clear sheath over it, and another doesn’t. I generally prefer the unsheathed kind, but it is stiffer, and therefore not great for applications like the chest and shoulders of this costume where it needs to bend and flex. We used four different diameters for this project. Sheathed ones for the chest and unsheathed for the head.
For the head: about three meters of 3mm and three meters of 4mm fibers
For the chest: about eight meters of 6mm fiber
LEDs: I used 60 per meter fully addressable RGB WS2812 LED strip
For the head: 36 LEDs
For the chest: 22 LEDs
For the shoulders: 28 LEDs in each
For the legs: 9 LEDs in each leg
Wire for the LEDs: We used three-strand servo connector wire like this, because it is very flexible, color coded, and already configured into 3 strand ribbons. It also comes with connectors already attached. You will need quite a few sections.
3.7v lithium polymer batteries: At least 3, one for each piece of the costume (and preferably spares to plug in when the first ones run out). We used these 2500 mAh hour batteries from Adafruit for all three pieces. This size works well for the headpiece, and lasts relatively long, but the chest and pants could take a larger battery if you wanted longer battery life.
Micro USB charging boards: One for each battery. Ashley suggested we wire these into each lithium battery, because it means you can safely charge a battery anywhere with just a mini USB cable instead of needing a complicated charging station. We used these.
Microcontrollers: We used 3 Arduino Micros in this project, but almost any simple microcontroller will work. Ashley recently introduced me to the DFRobot Beetle, which I like quite a lot.
Small on/off slide switches like these: 3, one for each costume piece to turn the lights on and off
JSTtwo-wire connectors like these. You will need one for each battery.
El wire: I used about 20ft of white and 20ft of teal 2.6mm high bright el wire in the headpiece (not the colors pictured here). I get all my el wire at Cool Neon in Oakland.
An el wire driver: you will need one capable of powering at least to 30ft of wire. The Quieter Blue Fish from Cool Neon was a good size for this headpiece and it doesn’t make a loud buzzing noise like some drivers, which is really annoying to have close to your ears.
El wire soldering supplies: copper tape, solder, one Y connector, and heat shrink tubing, which can all be purchased from Cool Neon.
A soldering iron
A soldering helping hands
A hot glue gun
Electrical tape
A heat gun, blowdryer, or lighter
A wire stripper: if you don’t want to go crazy stripping el wire, I suggest one like this.
A wire cutter
Needle nosed pliers
Rivets: for most of this project I used small silver rivets, like these, and also some slightly longer ones like these. Whats nice about both is that you can set them with only a hammer.
Snaps to match your leather and the appropriate snap setting kit
Two 5/8” buckles
A Hammer
A leather punch
Scissors
A large-ish hand sewing needle
Thick white thread
One yard of 1” wide black elastic
Superglue
Fabritac or Magnatac
Small white zip ties
Double sided tape
A pencil
An exacto knife
A ruler
Optional:
Oaktag: if you want to alter my pattern or create your own
3 power boost converters: these lithium batteries are 3.7v, but LEDs are designed to run at 5v for maximum brightness. This outfit can run straight off the 3.7v, but if you want the lights to be a bit brighter (which looks good in the chest and legs, but isn’t necessary for the head), you can wire in a power booster.
3 buttons for switching between lighting programs: if you want the option to program more than one lighting pattern for your LEDs, you will need to wire a button onto each of your microcontrollers.
Step 2: Mocking-Up the Headpiece
I decided that the headpiece was going to consist of two main sections. The outer el wire fin, and the inner fiber optic crest which would rest on a leather sort of cap on the head. To get the right shape for all the components of this headpiece, I used oaktag, muslin and a head form to “drape” a mockup of the piece. First I mocked up the fins and side ‘straps’ in oaktag, all the while referring to my sketch, trying the piece on and altering it until it was the shape I wanted.
Then I used muslin to drape the center section of the head which will be the leather ‘cap’ that holds the micro controller and batteries.
After that I went back to paper and oaktag to create a mock up of the structured leather box or platform that will sit on top of the cap and hold the LEDs and fiber optics. The flat top of this box needed to be wide enough to accommodate three rows of led strips, and deep enough to fit over the electrical components that power both the LEDs and el wire. It was a little tricky getting this shape right to curve over the head, and I definitely needed to try it on an actual human, since the proportions of my head form were a little off.
Step 3: Turning the Mock-Up Into a Pattern
Once I had these components draped, I marked where they intersected, disassembled them, and used them to create more precise pattern pieces. Some of the pieces needed to be scanned and turned into laser cutting patterns and some simply needed to be traced onto paper.
I decided to laser cut the side straps, and the two pieces of the box because they needed sewing holes and slits for weaving el wire. So I scanned them on a flatbed scanner, and then imported them into Adobe Illustrator where I traced them and added details. I used the pattern brush tool to create the sewing holes and el wire slits. It is a useful tool and I will show you how to use it in the next step.
I also scanned the large fin piece because I needed to use the shape of it’s lower edge to create a shaped pattern piece for the white leather strip woven with el wire that will embellish the base of the fin. I divided this strip into two symmetrical sections that will be sewn together at the center front, and added el wire slits to each with the pattern brush tool.
I took the muslin pieces that made up the head cap and simply traced them onto paper to create precise pattern pieces.
I left the fin piece in oaktag because it was already precise enough.
Step 4: Using the Illustrator Pattern Brush Tool
I made my sewing holes and el wire slits using the Illustrator pattern brush tool, which is a great tool for creating any repeating feature. Basically you create a swatch, and then the pattern brush tool repeats this swatch along a path.
Making a Pattern Brush for Sewing Holes:
- Use the ellipse tool to draw two tiny circles about .05” in diameter and arrange them next to each other .25” apart from center point to center point. Make sure your circles have no fill, and a stroke value of .001. Group these two circles.
- Draw a rectangle .25” high and .5” wide. (You want the width of your rectangle to be exactly twice the distance between the center points of your two circles so the spacing of your holes will repeat evenly).
- Center this rectangle over your circles using the align tool, and give it no stroke and no fill.
- Drag to select both the rectangle and the circles and then drag and drop them into the brush pallet. In the dialog box that appears, choose ‘pattern brush’, in the next dialog bog, name and save your brush.
You can now use your brush to create your sewing lines. To do this draw a line parallel to your cutting line, but inset by 1/8”. I like to do this by using the Offset Path tool under Object > Path. This way you can get a line that is exactly parallel to your cutting line and then use the direct selection and Cut Path tools to divide up your offset line into the sections where you want sewing holes. Once you have done this, just select your line and apply the new pattern brush to create lines of sewing holes! You can alter the size and spacing of the holes to your liking, depending on how thick your leather is.
Making a Pattern Brush for El Wire Slits:
- Draw two vertical parallel lines with the stroke width set to .001, and the fill off. Make the lines 3/8” long and 3/16” apart (the appropriate line length depends on the thickness of your leather, so you need to test this on your own leather to find the right size slits.)
- Group these two lines.
- Draw a rectangle. The width of the rectangle should be twice the distance between the two lines, and the height should be the same as the height of the lines.
- Align the rectangle so it is centered directly over the lines, and turn off both the fill and stroke on the rectangle.
- Select the whole thing (rectangle and lines) and drag it over into the brush palette to create your pattern brush.
You can save your pattern brushes for use in other files by clicking on the little library icon at the bottom left of your brush palette and selecting ‘Save Brushes’. Then you can find them later from any file by clicking the same library icon and then selecting ‘user defined’. I’ve been developing a whole library of brushes for use on different leather thicknesses.
*IMPORTANT: Whenever you apply your pattern brush to a path, make sure that the fill is off! If you leave the fill on, the laser will cut a line down the center of your path an ruin your holes or slits!
Step 5: Cutting Out the Pattern
Once all my pattern pieces were made, I cut them out. First I I took my paper pattern pieces traced them onto my grey leather with chalk and cut them out with scissors. I cut one center piece, and two side pieces. (My pieces look a little funky in this picture because I was running out of leather).
Then I laser cut my white leather pieces. (If you are planning to make the whole outfit, it would be best to wait until you have also created the patterns for the chest and legs, and then laser cut them all together.)
I used one of Instructables’ awesome 120 watt Epilog laser cutters, with the following vector settings:
White (thicker) leather:
- Speed: 40
- Power: 45
- Frequency: 550
Grey (thinner) leather:
- Speed: 40
- Power: 30
- Frequency: 550
Every laser cutter is different, as is every piece of leather, so always test your settings first.
Leather tends to warp as it’s cut, so make sure your piece is secured to the laser bed as well as possible, and make sure your file is set to cut all the inner cuts and holes before cutting the outlines of the pattern pieces. You may still need to pause your cut periodically to remove pieces, or tape down edges that are warping.
Leather smells terrible when you cut it. Make sure your laser is adequately ventilated and wait a minute before opening the door when the cut is complete.
The laser will create some soot marks on both sides of the leather, I usually use a damp towel to clean these off, though I’ve recently found that baby wipes work even better.
Step 6: Sewing the Fins
Now I took my piece of stiff white netting and used it to make the base which the el wire will be woven through to create the outer ‘fin’ of the headpiece.
To do this I folded my netting in half, pinned it together, placed my oaktag fin pattern on it and traced it. Then I used a ruler to draw lines perpendicular to the bottom line of the fin spaced out evenly in a few places. These will help you know what angle to sew your channels at. Then I cut a rough rectangle around the pattern very roughly, leaving about 2 inches excess on all sides.
Sewing the channels for the el wire is a pretty tedious process. I like doing it by eye, but I have also tried creating a template to help guide the lines. Basically I just start in the center and begin sewing a series of straight lines to fill in the outline of the fin shape and create channels about 3/16’ wide that you can later run your el wire through. The trick is that the angle of your lines has to tilt with the shape of the fin, so in more curved sections of the fin you have to leave a little wedge of space between each channel so they fan out and remain parallel to the base of the fin.
Once I had sewn all the channels, which takes a few good hours, I was ready to weave in my el wire, but first I had to solder it…
Step 7: Soldering the El Wire
I took my 20 feet of teal and 20 feet of white 2.6mm el wire and divided each piece in half. I did this because I wanted to start threading my el wire from the center of the fin and work outward on each side.
Then I took an el wire Y connector, cut off the two female ends of the Y and soldered one teal and one white el wire strand to each wire like this:
Take your two strands of el wire and strip about 1” off one end of each strand using your automatic wire stripper. You can adjust how deeply the stripper cuts by turning the little wheel on the front. Your goal is to expose the phosphor covered core wire, without breaking the two tiny hair wires next to it. It might take a few tries to get this right.
Now shave the phosphor coating off the ends of the core wires with an exacto knife.
Using a pair of needle nosed pliers, twist the bare ends of the core wires together, then use your soldering iron to tin them with solder.
Wrap a piece of sticky copper tape around the plastic covered ends of the two wires. Use your fingers to twist the two tiny hair wires together, and fold them down over the copper tape.
Leaving about two inches of wire before the white connector, trim and strip the two wires of one branch of the Y connector so they line up with the hair wires and core wires of the el wire respectively.
Slip a piece of heat shrink tubing over the black wires of Y connector, and then use the helping hands to hold the el wire and Y connector in place so you can solder them together.
Once it's soldered it is wise use a hot glue gun to cover your solder connection with hot glue, this will help prevent the connection from failing or shorting out.
Once it’s soldered, use a heat gun, lighter or blowdryer to shrink the tubing over the connections.
Now do the same with your second pair of wires and the other branch of the Y connector.
before moving on, be sure to test your el wire by plugging it in to a driver and battery.
For more tips on el wire soldering, follow this great Cool Neon tutorial.
Step 8: Threading the El Wire
Once I had all the channels sewn in my netting, and my wire soldered, I threaded my wire into the netting to create the fin.
I started in the very middle of the fin, from the bottom edge, making sure to start with the same color el wire on each side. From there I worked outward, alternating wires and making sure to always keep the same color on the outside. I pulled the loops of wire fairly tight at the top and bottom, but not tight enough to distort the netting.
When I was done I trimmed off the extra aqua wire on each side but left the extra white hanging because I planned to use it for more detail work later.
Finally, I trimmed the netting to a good shape, about 1 1/4” from the edges of the wire.
Step 9: Attaching the Fin to the Side Straps
After Completing my fin threading, I attached a strip of leather to the bottom of the fin. I created the pattern for this piece by tracing the bottom curve of my oaktag fin onto paper and then measuring out 3/4” on each side of that line. I cut this piece out in leather and sewed it to the netting overhang on the bottom of my fin using a zipper foot, being careful not to sew into the el wire, that would be bad.
Then I took my two laser cut leather side strap pieces and pinned and sewed them onto this leather strip, referring back to my original fin pattern to see where they should intersect.
Once all these were attached, I took the Fabritac glue and glued the top edge of the leather strip down to the netting and wire of the fin.
Step 10: Making the Central Leather Section
The next step was to sew the grey leather cap that would cover the center of the head and attach the structured white leather box to it.
First I sewed my grey leather pieces together. Then I folded under the 1/2” seam allowance on each side and sewed that down to finish the edges. I used a leather needle on my home machine, but an industrial machine or walking foot would have worked better. I intentionally left the back end of this cap piece extra long because I wasn’t sure exactly how long it was going to need to be.
Next I constructed the white leather box, or platform, that was going to sit on top of this grey piece and cover the electronics. I hand sewed these two pieces together using a thick white thread and the sewing holes I had laser cut in the leather.
Once these two components were constructed, I needed to attach them to eachother, so I added a small leather piece to the front of the box which allowed it to be sewn down to the cap while still leaving room for the wires from the el wire fin to feed through.
With these two pieces put together I got out my electronic components (the microcontroller, lithium ion battery, el wire driver and 9V battery). And arranged them on top of the cap, under the white box, to see where they fit best. I marked these spots and then sewed down strips of 1” wide elastic which would eventually hold each component. For the battery, I created a small leather pocket on top of the leather cap at the base of the head.
Step 11: Putting the Pieces Together
Now I attached these two main components of the headpiece by sewing the fin down onto the cap where the two intersect at the front of the head. This was rather tricky as it involved sewing through a few layers of leather, so I would recommend using an industrial machine.
Once this was done I tried the headpiece on to determine how long to make the elastic that will hold it together in back. Then I pinned the elastic on, and tried it on to test it again. The grey cap was going to attach in the back by making a loop that would fit tightly around the elastic band, so after I sewed the elastic on, I marked the place where the grey leather should meet the elastic, then riveted it around the elastic.
After that I figured our where the back end of the white box should lie on the grey cap, and then riveted two snaps on to act as the closure for the box. The idea is that the box can be opened by undoing these snaps and lifting it up to expose the batteries and electronics.
Step 12: Adding the Embellishments
The first step in embellishing the outside of the headpiece was to create the feathered strip of black ruffle that I wanted to put along the base of the fin. To do this I simply took a long strip of stiff black tricot, at least 4 times it’s final gathered length, and about 5” wide. I folded this over so it was only 2 1/2” wide and sewed a double row of long shirring stitches along the folded edge. Then I gathered it to the right length and feathered the edge by cutting into it with scissors.
I glued this piece down along the base of the fin with Fabritac.
Next I took the two thin white strands I had laser cut and sewed them together at the center front. I took one of the white piece of el wire I had left hanging at the end of the fin and wove it through this strand, then glued the strand down on top of the black ruffle.
Now I took the remaining lengths of white el wire, and wove them through the slits in the grey leather side strap sections.
I did most of this in the the back seat of a truck squashed under many bags of costumes on my way to the playa…
Step 13: Creating the 3D Printed Base for the Fiber Optics
Now it was time to work on the center section of the headpiece which would incorporate LEDs, fiber optics and a 3D printed piece that would connect the two. This was where the amazing Ashley Newton came in.
Ashley and her business partner Sean Stevens have been creating amazing things with technology for quite a few years now (check out their website, Sustainable Magic) and they have found some clever ways to marry fiber optics to LEDs using 3D printed nodes. In the past they have used variations of this idea to create fantastical pieces of art like this fiber optic sound-reactive weeping willow tree, interactive robotic illuminated flowers, and neuronal light nodes for a model-brain art car at Burning Man. For this project Ashley modified her existing design for the fiber optic nodes to create a cover that fit snugly over three LED strips, while also holding a fiber optic strand directly over each LED enabling every fiber to have its own dedicated light source, thus achieving maximum brightness and customizability of programming.
Ashley modeled this part in Solid Works and printed it in Ninjaflex TPE filament on a Makerbot. Ninjaflex is great because it is not only strong and flexible, it also diffuses light quite well, which gave the whole 3D printed piece a nice glow when the headpiece was complete.
Step 14: Wiring the LEDs
Once we had printed the base, Ashley showed me how to solder the LEDs which would go underneath them.
We soldered together three strips of LEDs: a strip of 11, a strip of 14, and another strip of 11. I used the servo connector wire to connect them and made sure I left the right amount of wire between each to nest properly into the LED base. I also left about 5” of wire at the input end of the LEDs with one of the black servo connectors attached.
LED strip is pretty simple to solder, but it can be a bit delicate, especially depending on the kind you have. At the cut lines between LEDs, there are little pads which you solder onto. Some LED strands have little holes in these pads, some don’t. The strands with holes are far, far easier to solder because you can feed the stripped ends of your wire into the holes before soldering, which makes your connections much stronger. I highly recommend trying to get the strip with the holes whenever you can.
I am by no means an LED soldering expert, so I will instead point you in the direction of this excellent Instructable for further assistance.
The difference between the LEDs in this Instructable and the ones I used, is that mine have three soldering pads, power, ground, and data all of which need to be connected to one of the the three wires of the servo connector wire. We wired ours with: white wire to data, red to 5v power, black to ground.
Also the fully addressable RGB strip like mine has a designated data direction, marked by small arrows on the strip. Be sure to orient your LED strip correctly so that data 'flows' out of the microcontroller and into the LED strip in the direction of the arrows.
Ashley and I did most of this at 3am the night before we were supposed to leave for Burningman….
Step 15: Attaching the 3D Printed Base
I decided to use small rivets to attach my 3D printed part and LEDs to the top of the white leather box. For this purpose I had asked Ashley to put holes in the sides of the part she modeled. I hadn’t planned ahead enough to laser cut corresponding holes in my leather, so I used the 3D part to mark where these holes needed to go, then punched them with a leather punch. I also cut a larger hole in the front of the leather box top, big enough to fit the connector on the end of the wire leading to the LEDs.
Before attaching the part to the leather, I tacked my LED strands into the indentations Ashley had modeled in the underside with some hot glue. The LEDs will be held down pretty effectively when they are sandwiched between the 3D printed part and the leather, but a little extra adhesive helps.
Then I took this whole assembly and riveted it down to the leather, first threading the LED lead wire through the hole so the connector and the wire came through to the inside of the box (the picture that illustrates this here is from another project, but you get the idea).
At this point I had made it to the playa and was doing most of this work at night in my tent, by headlamp…
Step 16: Wiring the Electronics
Now it was time to connect all my electronics and light everything up!
So I got on my bike and rode down along the dusty Esplanade to where Ashley was camped with The Phage, luckily only a few blocks away. Ashley and Sean had a whole box truck set up as a soldering and electronics station and were busily trying to finish the Dr. Brainlove art car they were working on, but Ashley sat down with me long enough to help me make a collection of rechargeable battery components, while she soldered the Arduino, switch and connectors together and showed me how to do it for future iterations.
All three costume pieces, head, legs and chest, used the same basic wiring scheme which I will describe here:
First we soldered a mini USB charging board to each battery we were going to use, as well as a JST 2 wire connector, replacing the existing manufacturer's connector which is inconvenient to repeatedly detach and reattach.
We wired the charging board directly to the battery connection wires, with red wires to Bat+ pin, and black wires to Bat- pin, and then taped the circuit down to the battery to protect the wires from being pulled, which basically turned it into a single battery-with-charger component. This way you could swap out different batteries for charging or use, just by disconnecting a 2-pin connecting wire between the battery-charger component and the micro controller, and could charge the lipo battery with a micro USB cable and 5v power source.
Then we wired the microcontroller to a slide switch so it could be turned on and off, and two connectors, a red one to connect to the battery, and a black one to connect to the LEDs.
We connected a male 3-wire "servo extension" cable to the end of the LED strip, and a female one of these cables to the Arduino so the board could also be connected an disconnected from the LED strip, making the whole project modular.
We had soldered our LED strip with: white wire to data, red to 5v power, black to ground.
On the Arduino, we connected the matching 3 pin connector's white wire to a data pin (in our case we used pin 4, but any digital pin works). The red wire was joined with the red wire from the on-off switch, and then connected to the Arduino's raw pin. In this way, the LED strip was powered directly from the battery to maximize the amount of power it received, since the lipo battery only outputs 3.7v and the LEDs are designed to run at 5v. We could have added a boosting circuit to this assembly, but that added complexity and when we tested the LED program we wanted to run, it worked fine with lower power.
The black ground wire was also joined to the black wire from the 2-wire connector that went to the battery, and those joined wires were attached to a ground pin on the Arduino. In this way all components had shared ground and power.
Once this was all wired up, we were able to connect a battery and LED strip to the arduino, and using the switch, could turn the arduino and LEDs on and off. All major components were modular and easy to remove if one needed to swap in a freshly charged battery, or if the LED strip or arduino stopped working, they could also be swapped without cutting any wires.
Step 17: Programming the LEDs
I know virtually nothing about Arduino programming, so Ashley was mostly in charge of this department. Because we were pressed for time, we ended up just using a slightly modified version of the rainbow fade that comes as part of the Adafruit Neopixel sample library, which actually looked quite nice. We altered the number of LEDs in the code to match the number we were using and the percentage of the rainbow fade we wanted to see at any given time (so that it wasn't the full rainbow ever) for each costume piece and adjusted the speed an brightness to our liking.
For the headpiece we added in a button to enable the user to select from a variety of color-specific modes. The programming for the button relied on counting the number of times the button was pushed, and matching that number to one of the programmed modes, using a switch case.
Since I my efforts to explain Arduino code will only serve to confuse you and lead you astray, I will refer you to the Arduino learning page, where you will find many helpful tutorials.
Step 18: Fiber Optic Gardening
With my microcontrollers loaded with programs, and my batteries wired, I biked back through the dusty glowing darkness to my tent at Kostume Kult, where my very heroic boyfriend was still crouched over a pile of leather with a headlamp, hand sewing another part of this costume.
I slipped all of my electronics for both the LEDs and el wire into the elastic and leather slots I had prepared for them on the grey the leather cap of the headdress, plugged in the batteries, flipped the switch and snapped the white box over them.
Now came the fun part. In the dark tent I took out my 3 and 4mm fiber optics and started cutting them into lengths and sticking them into the holes in the glowing 3D printed base piece. The 4mm pieces went in the center and were longer, while the 3mm pieces formed shorter rows along the sides. I tried a few different kinds of glue to help keep the fibers in place, and found that superglue works the best, though even it doesn't work great.
I increased the height of the pieces as they went back and cut the ends of each fiber at a diagonal to match the swooping shape of the crest. I wanted this part of the piece to really look like some magical cross between the illuminated tentacles of a jellyfish, the fins of scorpion fish and the glowing lure of an anglerfish... and I have to say, I think I succeeded.
Step 19: Designing the Shells for the Chest, Shoulders and And Legs
Unfortunately, when the headpiece was finished the rest of the outfit was still far from complete. Bruce and I had been working on all three components of the outfit simultaneously and there was still a lot more to to be done on the chest and legs. Making these two pieces was a long and complex process which began with designing and modeling the 3D printed shells that would diffuse light and house the LEDs that illuminate the fiber optics. All this was done about a month earlier back in the comfort of my own studio.
I am still relatively new to 3D modeling, so a lot of my process involves bumbling around in Fusion 360, trying to see what I can accomplish with the tools I know.
I started creating these shells by drawing a to-scale sketch of what the chest shell would look like from above.
I then scanned this sketch and imported it into Fusion 360 as an attached canvas.
I created the basic shape by sketching successively smaller outlines of the shell on different planes, and then lofting between them in the sculpting environment of Fusion, and thickening the shell created by the loft.
Then I went back into the modeling environment and cut into the shell to create the striped sections.
I wanted the shoulder shells to be deeper, and have a more angled shape than the chest shell so they would fit over the curve of the shoulder. I took a copy of the chest shell model, sliced it up and reassembled it into the shape I wanted. In retrospect, I probably should have just started fresh with the shoulder shell model, because all the slicing and reassembling made a bit of a mess. But it still worked out pretty well.
For the leg shells I just took the shoulder shell, and stretched the model sideways a little then scaled it down to make the three sizes I wanted for the leg.
I printed a test of my chest shell in a few sizes first to see how it would look and how it would diffuse the light. (I'll tell you how I did that in the next step). After that I altered it to the right size and added holes for the fiber optics to feed into. and sewing holes, which I didn't end up needing. For the shoulder shells, I needed to leave room for the fibers to enter along with the leather strands that they were going to be woven through. So I made these holes rather large and elliptical. On the Legs, I made small holes on each side of the shell use to attach them.
To be honest, a lot more planning could have gone into how I attached the shells and how the LEDs fit inside them. At this point I was running out of time, and trying to make sure I snagged a place on the coveted Objet printers before I had to leave for the playa, so I just had to make a choice and print my final parts without proper testing and iteration.
Step 20: Printing the Shells
The printers we use at Pier 9 are Objet Connex 500s. They print in two materials simultaneously, as well as a support material. You can load a variety of different materials into the machines, but the main two types are Vero (hard), and Tango (soft). The Vero comes in clear, white and black, and the Tango comes in clear and black. You can also combine materials to make a digital material that is somewhere on a spectrum between hard and soft or white and black etc.
Before printing my files I had to make sure that the dark striped sections and lighter striped sections were separate objects, but still touching. Then I exported them as two STL files, one for all the dark stripes, and one for all the lighter ones.
I chose to print my shells on a printer that was loaded with Vero White and tango Black. I imported my files into the Objet print software by shift+clicking on both files and importing them as an assembly. This brings them into the print software properly aligned. Once the files were imported, I clicked on the two kinds of stripes and assigned them different materials. For my final print I went with a digital combination of 80% black and 20% white for the dark spines, and 80% white and 20% black for the lighter spines. I did this because I didn’t want the black sections to be too soft, and I also wanted the light sections to have a slight give to them. In retrospect I might have gone with full white for the light sections, because the grey didn’t diffuse the light as well, and made it look a little dirty.
On the Objets you also have a option to print “glossy” or “matte” which just means that if you print in glossy, the printer will avoid putting down support material whenever possible to keep the surface of your print glossy. This does not mean that your whole print will be glossy though. Depending on the shape of your object, there will still be a lot of areas covered with support material, which sometimes makes your object look uneven and weird once it's cleaned. With these shells however, printing in glossy worked quite well, and there were only a few places on the outer surface of the shells that ended up covered in support material.
All the shells together were a pretty big print that took about 15 hours.
Step 21: Making the Pants Part 1
I designed the pants to have three shells on each leg, starting right below the knee and going down the calf with a piece of LED strip under each one. I decided it wasn’t worth it to make the pants from scratch, so Andre (my client) and I just bought a pair of white jeans that fit him well, and I attached the shells to those. I’m not the kind of maker who feels the need to personally make every element of the things I design. I’m very comfortable with the fact that some things can be made more quickly and easily by other people, and in many cases I’m happy to let those people (or manufacturers) do what they are good at so I can focus on what I’m good at.
The first step in making these pants my own was to wire the LEDs. I decided how far apart I wanted the shells on the legs and how many LEDs I could fit inside each one, then measured how much wire should be between each set of LEDs.
I ended up soldering two strings of: 2, 2, and 5, LEDs (from top to bottom) with a long section of wire coming out the top end, long enough to reach the battery pack which was going to live in one of the front pockets.
I positioned the LEDs where they would sit under the shells and tacked them down to the jeans with a rough hand sewing stitch. On the side away from the pocket where the batteries were going to live, I cut a small hole in the top layer of the waistband and fed the end of LED wire through to the other side, where I cut another hole to let it out so it could run down into the pocket with the batteries.
Step 22: Making the Pants Part 2
At this point I think it was about Tuedsday of burn week on the playa and Bruce and I had decided to take over a table in the crafting dome at Kostume Kult. So even though we hadn’t gotten to go out and enjoy any playa adventures yet, we at least got to watch people come in and pimp out their bikes with faux fur while we worked wearing silly hats…
I planned to attach the shells to the pants by embedding them in a piece of leather that I would sew down to the pants, and hide the wire that led to the LEDs under a strip of the same leather going up the side of the pants like a tuxedo stripe. This plan was not that well thought out, and the piece of leather that I laser cut to fit over the shells was too small, which Bruce had discovered during one of our late night work sessions in our tent. He ended up having to re-cut a properly sized piece of leather by hand, and we decided that riveting it down to the pants was really a better idea than sewing.
We used the holes I had modeled in the shells to attach them to the leather (they ended up being a bit smaller than was ideal), and also glued the edged of the leather down to the shells with superglue.
Then I hand sewed down the 'tuxedo srtipe' of leather that I had laser cut with sewing holes to go over the LED wire, and Bruce riveted down the leather that held the shells with small silver rivets.
I had already wired the microcontroller, battery and switch in the same way as the others, and loaded the microcontroller with the rainbow fade, so the last step in making the pants was to connect the electronics to the LEDs and make a small leather pocket to hold and protect these parts. And then it was done!
The Adversary, Andre Mistier’s band, had a show that night on the other side of the playa, and I wanted to get him at least part of the outfit before he played. So as soon as we finished the pants, I took them and the headpiece and biked over to his camp. He wasn’t there, but I managed to track him down on an art car shaped like a yacht. He was very excited about the pieces, and I got a boost of creative gratification to help me go back and finish the rest of the project.
Step 23: Mocking Up the Chest Harness
The final piece of the costume to be completed was the chest harness. Bringing this piece into being was a long process that started back in the Instructables studio about a month before Burning Man.
To create the leather body of the chest harness, I first created a mockup in oaktag. I referred to my sketch and tried to create a shape that fit well around the body. I wanted the chest to have three tentacle like strands of leather laced with fiber optics that would be illuminated with LEDs housed inside the chest shell.
The glow of these side light fiber optics starts to fade a few feet away from the light source at one end. So I decided that, as much as possible, I would try to design the fiber optic portions so there was an LED at each end. I managed to make the longest strand (which came out of the chest) loop around, continue up slits in the back of the harness and end up connecting to a second LED in the shoulder. Both epaulette loops on each side of the shoulder also looped around to connect to an led on both sides of the shell. This double LED method not only gives the fiber an extra strong glow, it also gives you the ability to have a two color fade from one end of the fiber to the other if the LEDs on each end are different colors.
I used the shells I had already printed to help figure out the exact configuration of all these fiber optic 'tentacles'. I decided to attach the shoulder shells by riveting the ends of the shoulder tentacles down to a wide patch of leather on the shoulders.
I gave the piece 3 straps in the back which would close with buckles and also added a strap under the arm which would include a pocket to hold the battery and microcontroller.
Once I had a first version of the harness draped, I marked all the places where pieces intersected, disassembled it, and then traced it onto a large piece of pattern paper. I refined my lines on paper, adding any details I wanted, then scanned it and drafted it in Illustrator. As with the headpiece, I used the pen tool to trace the outline of the pattern pieces, and the pattern brush tool to create the sewing holes and el wire slits.
Then I laser cut the pattern in oaktag and re-assembled it to see if it was all fitting together and looking right. I also got a chance to fit it on Andre at this point and make a few fit changes. If the changes were major, I marked them on the oaktag, re-scanned it, and altered the Illustrator file accordingly. If the changes were minor enough I could make them by eye in illustrator without re-scanning the pattern.
Step 24: Laser Cutting the Harness
I had decided to make the main part of the harness two layers to hide the wiring, with the front layer in white and the back layer in grey. So before I cut out my leather I used my original illustrator pattern to create a second pattern with slight alterations for the back piece.
When I had my illustrator file finished I cut it out on the laser cutter using the same settings as I did for the headpiece.
Step 25: Machine Sewing the Harness
I had drafted hand sewing holes into most of the harness, but there were a few pieces I needed to sew by hand, which I did on an industrial walking foot machine… an amazing machine that will sew through anything!
I sewed together the shoulder seams on the white pieces, the center front seam of the grey pieces, and the two layers of the front strap leading to the pocket which will hide the wires.
I also designed and sewed the simple pocket which I attached to the underarm strap leaving an opening to thread the battery wires through. I added snaps to this pocket as closures.
I made sure to finish this step before leaving for the playa, as I knew amazing walking foot sewing machines would probably be in short supply in the desert…
Step 26: Lacing the Fiber Optics
Before I could proceed with hand sewing the body of the harness together a few other things needed to be done, the first of which was lacing the fiber optics through the slits I had laser cut in the leather tentacles.
First I cut sections of the 6mm fiber optic to the correct length, then wove them through the leather on the chest and the tentacles that drape around the waist and shoulders. I cut an extra long section of fiber for the longest chest tentacles and wove the back end of these up through the slits on the back of the harness to where they would connect to the shoulder shell.
Step 27: Creating the LED Nodes
Then Ashley and I needed to figure out exactly how these fibers were going to attach to the LEDs inside the shells. We had planned to create 3D printed parts for the chest and shoulder shells that would fit inside the shell and securely fix the end of each fiber optic strand over an LED, as we had done on the head. Due to our time constraints, this didn’t come together quite as planned… but we made it work.
We ended up using a part Ashley had created for a previous project which was a single strip version of the LED cover we used on the head, also printed on the Makerbot in Ninjaflex TPE flexible filament. I took these 3D printed strips and made them into loops which would nest inside the shells. After trying a few methods, I found that sewing the ends of the strips together was actually the best method of connecting them. Apparently you can also melt them with a heat gun and sort of weld them together, but I never got that to work very well.
We made one loop for each shoulder and one for the chest.
Step 28: Soldering the LEDs
In order to illuminate both the fiber optic strand and the shells themselves, we needed to have LEDs facing both inward and outward. To do this we decided to create double sided loops of LEDs to fit inside the loops of 3D printed nodes.
I measured the wire distance between the pocket and the closest shoulder, the shoulder and the chest, and the chest and the second shoulder, and then soldered three strands of LEDs with the appropriate length connecting wires between them and a connector on the input end to connect them to the microcontroller:
28 LEDs (for the shoulder), 22 LEDs (for the chest), 28 LEDs (for the other shoulder)
I folded each length of LEDs over onto itself, and nested them inside the 3D printed loops so each outer LED was aligned with one of the apertures for the fiber optics. Then I used zip-ties to secure the LEDs to the 3D printed loops.
Step 29: Assembling the Harness Part One
Now it was time to put it all together. Which was mostly done by my incredibly patient and skilled boyfriend Bruce while I was woking on other aspects of the outfit.
Using the sewing holes I had laser cut in the leather, he stitched together the front and back of the harness with a saddle stitch. At the places where the straps and fiber optic leather strands met the main body of the harness, he sandwiched them between the white and grey leather layers and sewed them together.
Before sewing the section around the chest shell, we had to fit the chest shell into the hole I had laser cut for it in the white leather. Then we inserted the fiber optics into the holes in the shell and attached them to the 3D printed loop with the LEDs inside. This whole configuration didn’t work as well as we had hoped, and could definitely use some refinement.
The fibers turned out to be a bit too big for the holes in the pieces Ashley had printed. I ended up stripping the clear sheath off the ends of the fibers so I could fit them into the holes, and I had to try a few different kinds of glue before I found one that worked fairly well, which was super glue. (Hot glue, which I tried first, wouldn't adhere to the fibers). I also wasn’t able to find a way to fit the bottom two fibers into the LED nodes, which left them without their own dedicated source of illumination. Clearly this part of the design needs to be refined.
Once the fibers were secured inside the chest shell, Bruce continued sewing it together, sandwiching the shell, LEDs, and wires between the two layers of leather, and moving on to the shoulders.
Step 30: Assembling the Harness Part Two
When it came to attaching the shoulder portions of the LEDs, I realized that I was going to have to cut the wires, feed them through holes in the white leather and then re-solder them.
We also needed to rivet a small length of leather ‘tentacle’, onto the back of the harness on each side where the long piece of fiber that looped around from the chest shell emerged from it’s row of slits. The end of the long piece of fiber would be woven into this short strip and eventually both would be inserted into the innermost of the three holes on the backs of the shells. (This would enable the end of that fiber to be attached to an led, and the end of the leather strip would be riveted down to the harness itself to hold the shell on in the back.)
Once that was done, Bruce could hand sew the rest of the harness before we attached the shoulder shells.
While Bruce sewed, I attached the fiber optic and leather loops to the shoulder shells by inserting them into the holes in the shells and then riveting the leather back onto itself. I left the front innermost strand on each side un-riveted, because I was going to rivet these pieces of leather down to the shoulders as the font attachment point of the shoulder shells.
When Bruce had finished sewing the whole thing together, we could attach the shoulder shells. First we attached the back side by inserting the short leather strand and the end of the long fiber into the innermost hole on the back side of each shell, and riveting the end of the leather piece down to the harness to create a loop that held the back of the shell in place.
Then, we could proceed to insert the ends of the fibers into the 3D printed nodes and glue them in place, using the same method as we had on the chest.
The last step was to rivet the lose ends of the inner front leather strands down to the shoulders thus fixing the shells into their final position.
Step 31: Whew!
Bruce and I finished this step at about 6pm on Thursday night of burn week, exhausted, dusty and sleep deprived. At 8pm that same night Andre was officiating a playa wedding (for which I had also designed the wedding dress). I made it across the playa with this last piece of the costume just in time for Andre to wear it to the ceremony.
The last few weeks had been frustrating and stressful, but seeing it all come together that night, with friends all around celebrating something beautiful, reminded me why I put so much of myself into the things I make, and why I can't imagine myself doing anything else.
Since then this outfit has been worn on stage by Andre at many performances and parties in New York. The video above from the Adversary shows the costume being worn (along with a few of my other designs) at the Gratitude Axis Mundi party in NYC this Fall. For this performance I added to the outfit by creating a set of fiber optic armbands using the same technique as I used on the head.
I also got a chance to do a photo shoot of the outfit on the beach with the awesome photographer Hep Svadja, and equally awesome model Gabriel Patin, whose other skills include managing the Pier 9 3D print lab.
You can see this piece in person along with a lot of other amazing things, at the Artist in Residence art show at Autodesk Pier 9 from Jan 22nd-24th 2015.
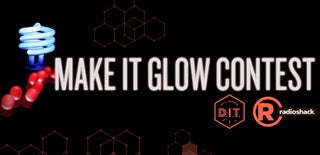
Participated in the
Make it Glow!