Introduction: Fixing and Improving a Fisherprice Green Meadows Bouncer With a Wall-Wart.
This was entered into the green contest, because I am converting it from being powered off of wasteful batteries, to being powered by a reusable wall wart. Thus preventing the batteries from ending up in the land fill.
May 1st, 2013 marked the birthday of my beautiful daughter Nadia Sophia. As such, most of my tinkering seems to revolve around fixing and improving the stuff that we use for her. A friend of ours gave us a used vibrating Baby Bouncer. Upon installation of one of those hideously expensive (and wasteful) "D-Cells", much to my delight, nothing happened! I LOVE an excuse to pull something apart, add some extra goodies, and then put it back together. My long suffering wife just rolled her eyes when she saw the look of excitement on my face.
The Mennonite inside of me couldn't bare the thought of continuously reloading and discarding those D-Cell batteries. Being the typical tinker, I have a drawer full of wall-warts. A broken toy is the perfect excuse to use up some spare junk lying around, and learn something new.
Cracking open the case revealed a simple circuit consisting of a motor, and a switch. The motor is a small DC brushed affair, with an eccentric weight on it. When the eccentric weight rotates about the motor shaft, vibrations are created due to an unbalance. This effect is very similar to a car wheel running unbalanced.
Step 1: Diagnosing the Problem
Using my trusting Digital Multimeter, I ohmed out the two battery terminals. The + and - terminals were open, even when the switch was closed. This must mean that there was a broken connection somewhere. I opened up the case, and found that one of the motor terminal connections had broken loose.
I quickly repaired the joint, and then inserted the D-Cell. Switched it on...and NOTHING HAPPENED. I gave the motor shaft a spin, and it started up okay. Applying too little voltage on a DC brush motor results in low starting torque. If the voltage is too low, the shaft is unable to start spinning. Using my regulated variable power supply, I slowly increased the applied voltage until the motor would start without any help. 4.5V seemed to be the magic number. Conveniently, I had an old wall-wart that would supply 5V DC, 200ma Max.
I think there might be something wrong with this particular unit, because it wouldn't start up under design conditions. Close examination of the switch revealed that there was a 0.5 ohm drop across the closed contacts. You generally expect 0-0.1 ohms across closed contacts of any sort of switch. Having resistance in a switch means that there will be a voltage drop across the switch. This means that heat is being produced in the switch, and that is not a good thing. In addition, if you are dropping voltage across a switch, and you are driving a motor, the amp draw in your motor can increase.
Inductors are rated in VA (Volt Amps). Unlike a purely resistive load, the VA of an inductor will remain constant. If you have a motor that is rated at 100VA at 50 volts, it must draw 2 amps. If you drop the voltage to 25Volts, that same motor will then draw 4 amps. (50V * 2amps = 100VA, 25V * 4A = 100VA). In addition to drawing more amps, motors supplied with too little voltage will not have as much torque.
I don't know for sure, but I surmise that there may be some kind of tiny SMD bump-up voltage regulator in the switch. There is a tiny piece of copper clad board on the bottom of the switch, and it does have an unmarked, smd three terminal microchip similar in shape and size to a small lm series voltage regulator.
I searched for the motor datasheet online, and it should work from 4v-12v dc, so applying 5v DC is plenty safe.
Step 2: Installing the Wall-Wart
- Since the only part of the case that there would be enough clearance to route the cable through was the battery compartment, I drilled 2 holes. One in the battery compartment panel, and one in the bottom of the battery compartment.
- Thread the power wire through the battery compartment panel, tie a knot for strain relief.
- Thread the power wire through the bottom of the battery compartment into the motor housing and switch area.
- Look at the simple ladder schematic I drew of how the motor is connected. The switch breaks the negative leg of the motor. In high voltage circuits, the hot side should always be switched. If you switch the neutral leg on an AC circuit, you potentially leave live wires in the mix ready to shock someone working on it. This is bad. Always switch the hot wire.
- Solder the positive lead of the wall-wart to the red cable on the motor.
- Solder the negative wall wart lead to the connection point corresponding to the negative battery terminal.
- Inspect your work, make sure you didn't short anything out. Using a DMM, check out the ohms of resistance between the + and - side. You should read between 50-300 ohms, depending on the resistance of the motor windings. If you read less than 1 ohm, you created a short somewhere and you shouldn't turn on the power.
- Finish up by sealing any holes you drilled by filling it with a dab of epoxy, hot glue, or quick setting silicone.
- Be sure to check that your motor works before putting the case back together.
Step 3: It's Done!
It works! This is my daughter Nadia Sophia, enjoying the fruits of my labour. We went from having a broken battery powered bouncer, to a bouncer than runs off of AC mains.
For those of you that care, she was born 10 days early, and weighed in a 5 lb 11 oz.
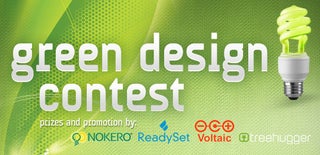
Participated in the
Instructables Green Design Contest