Introduction: Flat-Pack Picnic Table From 1 Sheet of Plywood
We live a block from Greenlake in Seattle. On nice days, if you don't get a picnic table by 10:30AM, then you're out of luck until after dark. We love to load up the grill and have picnics at the park, but without a table, it can be a little tough on these old bones. While researching flat-pack furniture for a CNC machine, I came across these plans for a flat-pack picnic table (see attached PDF file). I've always loved "One Sheet Plywood" projects, so this was right up my alley. It's cheap, easy and fits our need perfectly.
I'm entering this in the flat-pack contest, so if you like this Instructable, please vote for me at the top of the page!
Attachments
Step 1: Layout
Handling full sheets of plywood is always a challenge for one guy, so rapidly reducing the size of the stock you have to work with is a good idea. To accomplish this, lay out the table top, seats and seat supports first, then cut them off to rapidly reduce the size of the plywood panel you have to work with when laying out the more complicated parts. I used 3/4" sande plywood from a big box store which was only $40 for the 4'x8' sheet, so this project won't break the bank. I plan on finishing it and protecting the plywood from water since there's no guarantee the grass in the park will be dry.
I'm used a circular saw (Skill saw) to make my cuts, so I had to take some additional precautions to ensure my cuts came out nice. I made my reference measurements, made a tick mark with a pencil, then laid down 1.5" blue masking tape where the cut will go, then redid my tick marks in Sharpie marker, then using a straight edge, laid out my cut line. All of this additional effort is because circular saws cut on the upstroke, so the masking tape on the top veneer will protect the plywood from tear-out.
The dimensions on the plans I used are extremely confusing, as they all reference each other so it's easy to propagate a mistake. In reality, it's much easier to just reference the edge for all your measurements. So after I cut out all my parts, I drew up a much easier diagram in AutoCAD (see attached PDF). Once you've lopped off your top and seat parts, you can use the interior measurements to rapidly layout the more complex parts.
The plans call for putting a 4" radius on various corners. It just so happened that my roll of tape was exactly 4" in diameter. This dimension is not critical, but you do want a nice large radius. Please note that almost every intersection/corner gets a radius except the interior corner where the seat slats go. I didn't catch this in time when I cut out my parts, but it's an easy fix with the Japanese pull saw. I also opted out of the fancy radii on the feet.
Layout: 1.5 hours
Attachments
Step 2: Making Your Cuts
As previously mentioned, all the tape was to reduce the tear-out from the circular saw, which worked really well, as expected. I clamped a straight edge in place, making sure to offset the level by the distance from the blade to the edge of the shoe (1-7/8" on mine - your saw may vary). I then lopped off the five rectangular parts for the top and seats. Once that's done, you're ready for the layout and cutting of the interior parts.
WARNING: You must be VERY comfortable using a circular saw for the next step!
Taking your circular saw, make a plunge cut on all the interior cuts. Start in the middle of the cut line and work your way back to the radius (fillet - pronounced "fill-it"), keeping your blade right on the Sharpie marker line. This is one of the trickiest cuts you can do with a circular saw, so practice on some scrap wood if you're not experienced with plunge cuts. Now move the saw forward to the other fillet and stop. Do all of your plunge cuts the same way. The good news is that since your fillets are all still intact, your plywood will stay in one piece while you work.
Once all straight cuts are made with the circular saw, you can cut out all of the fillets with a jig saw (aka sabre saw). Because the two saws have different blade thicknesses, they remove a different amount of wood (kerf). This means you'll have to do some clean-up on your fillets. I used the end of a stationary belt sander to sweeten up the interior fillets and exterior radii. You can see the before and after in the last two pics.
Cutting Out Parts & Sanding: 2 hours
Step 3: Details: Slots I
Now that the parts have been rough cut out, it's time to add some of the details that make it go together. The first step is to notch the seat supports for the thickness of the seats. You could just ASSume that the plywood is 3/4" thick, but it's probably 23/32" thick. So instead of measuring and getting yourself in trouble, just use a piece of scrap to determine the thickness. Another plunge cut cuts out most of the notch. Then finish up with a hand or jig saw.
NOTE: In my haste to make progress, I forgot to tape the first plunge cut on the seat support, so you can see what a difference it makes.
I laid the seat support on the seat to make my layout marks, once again no measuring required. There's a notch in the seat support, but I'm going to wait until further in the build to make those to verify their location/depth.
The pull saw made quick work of cutting right on the line to make sure the half lap joint fits. You can use a jig saw to liberate the waste, but I used a chisel. Pop the support into the seat and voila, your first sub-assembly! Flip the seat over and check out the joint.
The sides and top support get a similar notch. Now for the first time, you can slip your picnic table together to get an idea of what it's going to look like!
I'm really happy with the joints. They slip together easily, but hold together and the sub-assembly is surprisingly stable. There's very little racking of the table, even without the seats in place or spacers under the table top.
Slots I: 1 hour
Step 4: Details: Slots II
Next is cutting all the rest of the slots for the half lap slots. Once again, I used a piece of scrap to determine how wide the slots should be. I also used the previously cut out seats to determine how deep the slots should go. Then I cut out the slot and rounded over the corner with a rasp. That's to keep it from just breaking off.
I changed the depth of the slots in the seat supports. I wanted a stronger connection, so I made the slot 3" deep on the table side and cut that out. Then I used the support itself to figure out how deep to make the corresponding slot. To do this, slide the support into the table side backwards and make a mark at the edge of the plywood. This will make the second slot the perfect depth so that the support sits flush then the joint is assembled.
Slots II: 1 hour
Step 5: Details: Holes
One of the features on the plans is cutouts for handles on the larger parts. This also allegedly helps you carry the whole thing bundled together if you make the clips in the plans.
Making these cutouts is actually a little tricky to do well. First make your layout marks. I'm using a 2-1/2" hole saw because I wanted the large 1-1/4" radius to match the radii on the rest of the table. I chose to make the holes the size of those two circles tangent to each other for aesthetics and practicality. The handle shown is in the middle of the table top, leaving over an inch of plywood for strength. Start your hole saw on the center marks and drill only deep enough for the drill bit to poke through. Do not drill the hole saw all the way through! It will create a huge tear-out disaster. Now flip the board and use the center holes that poked through as your starter and finish drilling the hole saw from this side all the way through. Remove the plug from the hole saw and drill the other hole the same way. NOTE: You can start all holes on one side, then finish them on the other to reduce flipping.
Now take a straight edge and draw two lines tangent to the edges of the holes, parallel with the edge of the board. Using a jig saw, cut on the lines. Use a wood file to sweeten up the lines on both sides. I put one handle cutout in the middle of the top and two on each table side, so five cutouts in all. None of the other parts were large/heavy enough to justify a cutout.
Holes: 1.5 hours
Step 6: Test Fit & Sit!
Now that all of the slots are cut, it's time for another test fit! The parts all fit perfectly together and the table is even more stable with the seat supports locked in place. I immediately was able to slide right in and take a seat. I'm 6'2" and 200 pounds and not only is the table comfy, but felt rock-solid. My wife sat on the other side and that made it even more stable. She was a bit dubious at first, but after seeing it all put together and sitting on it, she thinks it's very cute and was very happy with the stability.
It was time for me to clean up and put the table away for the day. It was actually a little difficult to disassemble, the pieces were so locked together. I'll wait until I'm done rounding over the edges and sanding and see how it feels.
Assemble & Disassemble: <5 minutes
EDIT: The next day, I found out why the table had been difficult to disassemble. In my haste to do a test fit with the freshly cut slots, the sharp edges bound up a little bit. Upon disassembly, some of the plywood tore out. Most of this was fixed when I used a router to ease the edges, but it was a lesson learned, which now you can avoid.
Step 7: Round Over All the Edges
The next step is to round over all the edges to make the table more user-friendly. Since the plywood is nominally 3/4", you could technically use a 3/8" round over bit. But I find that if you use a bit that's half the thickness, then when you are rounding over the second side, your bearing is riding on the first side's round over, which can be problematic. With that in mind, I used a 3/16" round over bit. Also, I used my 3-1/4" Hp router, but you can use a much less expensive laminate trimmer. Actually, you could do a pretty good job easing the edges with a hand sanding block with some 80 grit paper.
If you're using a router, set the router bit corner flush with the bottom plate. This will give you a smooth, round edge. For interior cutouts go clockwise, for exterior go counter-clockwise. This is a little confusing but it has to do with the rotation of the bit. I remember this by OUT is in cOUnTer-clockwise.
For the mating slots, I didn't want to run the risk of a round over causing too much slop in the joint, so I just chamfered the edge with a sanding block.
You can see how nice the finished rounded over parts look and they're much more comfortable to handle.
Rounding all edges: 3 hours
Step 8: The Finish Line
I was anxious to try out our new table, so on a beautiful Sunday afternoon, we loaded the picnic table into our little wagon and setup camp in the park. As predicted, all of the park tables were taken, but not a problem for us!
With the edges rounded over, the table goes together and takes apart much more easily. We all sat there and had a snack while people walking by were checking out our little setup.
I used penetrating epoxy on the feet and coated the entire table with regular epoxy to make it waterproof both above and below.
This table is the perfect compromise between actually being a usable table and being portable enough to take anywhere. At around 10 hours total, this would be a long single day project, but is very doable over a weekend. I had planned ahead and already bought the plywood after work, so I was able to start right in on Saturday morning. If you buy plywood ahead of time, you're probably going to want to lean it up against a wall somewhere. Make sure you don't leave it there for long as it will bow the plywood slightly.
Once again, if you liked my Instructable, please vote for me for the Flat Pack Contest by clicking the ribbon icon at the top of the page.
Total Time (not counting finishing): 10 hours
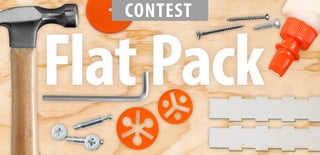
Grand Prize in the
Flat Pack Contest