Introduction: Fluid In.Flux_3D Wax Printing in Water
Fluid In.Flux is a 3D printing experimental machine which prints wax in water. The Machine was a semester-wide exploration as part of the Advanced Architecture Studio called "Creative Architecture Machines" by Professor Jason Kelly Johnson and Michael Shiloh at the California College of the Arts, in San Francisco.
Fluid In.Flux is about exploring material behavior in different conditions and developing an innovative method of digital fabrication. The project aims at abstracting the input geometry and creating imprecise abstract forms through precise machine operations. These imprecise abstractions are the result of the material system of the project. The material system involves the articulated ejection of hot liquid wax in cool water, taking advantage of wax’s buoyancy, rapid phase change and wax’s ability to fuse and bond to itself and other materials. Water is used as a catalyst to solidify wax rapidly and fabricate additively in the process.The scope of the project is a form generator, to develop digitally controlled construction systems. Projecting it onto an architectural scale, autonomous machines can be deployed onto fresh water basins to create buildings, cities possibly, under water opening up to a wide range of potential applications.
The machine was designed, assembled and calibrated by Architecture students at California College Of The Arts - Darshini Shah, Ibrahim AlGwaiz and Swetha Kopuri. Please feel free to contact us with any comments, questions or feedback. Happy to share and help!
Step 1: Building the Machine
1. The machine essentially has 4 components -
1.1 Wax Reservoir and Tower
1.2 Machine Armature - 1/4" thk Plywood
1.3 Water Tank - 1/4" thk Acrylic
1.4 Electric Components and Tower.
Step 2: Making the Machine Armature
1. Laser cut the following components out of 1/4" thk plywood.
2. Follow the diagram for assembly.
3. Zip tie the plywood components of the machine.
4. Insert the stainless steel rods into the prescribed holes in the plywood components. While inserting the rods, at appropriate points, fix the gears onto the rod using a ranch.
5. After the armature of the machine has been fixed, position the timing belts accordingly.
6. The prescribed motion is therefore produced by powering the Stepper motors, that directly bring about rotation in the gears, that in turn displace the respective components such as either the Gantry, Print Head or Bed, through the interconnecting Timing Belts.
Download Rhino File Below
https://www.dropbox.com/s/r7jjo0o5bvyzqpi/Fluid%20In%20Flux%20-%20Rhino%20Model.3dm
Step 3: Making the Water Tank
1. Laser cut the following components out of 1/4" thk acrylic.
2. Fix the pieces together, using acrylic cement and clear Silicon and leave it to cure for 12 hrs.
Step 4: Making the Bed
1. Laser cut the following components out of 1/4" thk acrylic.
2. The Bed is essentially a 2 piece component. Fix the pieces together, individually using acrylic cement and zip ties.
3. The upper component, essentially the bed, is to be supported on all 4 sides by means of 4 No.s of Stainless Steel rods and Linear bearings.
Step 5: Making the Gantry
1. Laser cut the following components, in 1/4" thk plywood, to hold the 3D printed print head.
2. Support the gantry on either side by means of 2 No.s of Stainless Steel rods and Linear bearings that are inturn supported on the machine armature.
Step 6: Making the Print Head
1. 3D print the design for the print head, as attached below. This fixture holds the flexible pipe and nozzle in place, during the casting process.
2. Laser cut the following components, in 1/4" thk plywood, to hold the 3D printed print head.
3. Now fix the 3D print head onto the assembled plywood construct, using zip ties.
4. Place this assembled print head onto the gantry, by supporting it on Stainless Steel rods and Linear bearings that are inturn supported on the gantry.
Step 7: Making the Wax Reservoir
1. Take a Fondue Pot, with a heating element, that has a self regulating thermostat.
2. Drill a hole of diameter, as per the valve fittings, at the base of the fondue pot.
3. Fix the valve onto the fondue pot
3.1 solder the valve onto the fondue pot
3.2 use a water sealant to ensure no leakages
4. fix the flexible plastic pipe onto the valve with a hose clamp.
5. fix the nozzle onto the flexible plastic pipe with a hose clamp.
6. Place the wax reservoir at an elevated level, to take advantage of the gravity to build pressure, while depositing the wax.
NOTE: For detailed information on how to make the wax reservoir, follow the link -
http://www.candletech.com/general-information/do-it-yourself-wax-melter/
Step 8: Arduino and Stepper Shield
1. This is the electronic component of the machine, which requires the following -
1. Arduino Uno Board - 1 No.
2. Solderless Breadboard - 1 No.
3. Quad Stepper Shield - 1 No.
4. Stepper Motors - 3 No.s
5. Jumper Wires
6. Table Top AC/DC Power Supply Output: 12V / 3A
7. USB Cable - 6 feet
2. Now plug-in the Arduino Uno Board into the Laptop, using a USB cable, and run the quad stepper firmata from the sketchbook menu of the Arduino software application.
3. Wiring between the Arduino Uno Board and the Quad Stepper Shield.
Unplug the arduino board, and follow the following Fritzing diagram.
NOTE: The Firefly Stepper Arduino Firmata sets the following pins:
3.1 For Individual Motors:
Motor 1 - Dir To Arduino Pin 2; Stp To Arduino Pin 3
Motor 2 - Dir To Arduino Pin 4; Stp To Arduino Pin 5
Motor 3 - Dir To Arduino Pin 6; Stp To Arduino Pin 7
Motor 4 - Dir To Arduino Pin 8; Stp To Arduino Pin 9
3.2 For All Motors:
Rst Is Connected To +5v (High)
Slp Is Connected To +5v (High)
En Is Connected To Gnd (Low)
Gnd Must Be Connected Back To The Arduino Gnd
4. Wiring between the Quad Stepper Shield and the Stepper Motors.
4.1 Fix the wires from Stepper responsible for movement of the gantry along the X-Axis into Channel 1 of the Quad Stepper Shield.
4.2 Fix the wires from Stepper responsible for movement of the print head along the Y-Axis into Channel 2 of the Quad Stepper Shield.
4.3 Fix the wires from Stepper responsible for movement of the Bed along the Z-Axis into Channel 4 of the Quad Stepper Shield.
NOTE: Follow the attached SM-DATASHEET.PDF for more detailed wiring instructions.
Attachments
Step 9: Firefly Coding
Link To Rhino File
https://www.dropbox.com/s/r7jjo0o5bvyzqpi/Fluid%20In%20Flux%20-%20Rhino%20Model.3dm
Link to Grasshopper/Firefly File
https://www.dropbox.com/s/c5699pbc4cx319j/Fluid%20In%20Flux%20-%20G%20Code%20Generator.gh
Step 10: Assembling the Machine
1. Place the Water Tank.
2. Fill the Tank with water.
3. Place the machine over the Water Tank, such that the notches click into each other.
4. Place the wax tower to hold the wax reservoir at an elevated position.
5. Place another tower to hold the electronic components at an elevated position.
6. Honing the X and Y Axis of the Print Head and the Z Axis of the Bed.
7. Wiring the Steppers into the Quad Stepper Shield.
Repeat instructions 4.1-4.3 of STEP 5.
Step 11: Operating the Machine
The operation of the machine requires one to follow a protocol-
1. Start Heating the wax in a kettle
2. Set the Fondue pot in a "Keep Warm" state to keep the wax from solidifying either in the pot or in the valve.
3. Feed the 3d object into Rhino, in the prescribed drawing space, and import the geometry into Grasshopper, using the Brep Component (right click the component to select "Set one Brep" option)
4. Hone the X,Y and Z axis of the machine. The Z-axis is relevant to the water level in the tank and honing the Z-axis means that the bed is to be flushed with the top level of the water.
5. Fix an acrylic piece onto the bed with waterproof tape, for ease of removal of the sample after the casting.
6. connect the USB cable between the Arduino Uno Board and your Laptop.
7. connect the Table Top AC/DC Power Supply Output: 12V / 3A between the stepper shield and your Laptop.
with a Feeding the Entry Toolpath.
8. In the prescribed order, turn the following Boolean Toggles on Firefly, True-
8.1 Open Port
8.2 Enable Stepper
8.3 Write Stepper
8.4 Reset Timer component - This starts slicing the 3d object feed at the prescribed interval along the Z-axis, to produce toolpaths along which the print head will move, to deposit the wax.
9. Almost simultaneous to step 8.4, start pouring the wax from the kettle into the fondue pot, while making sure the valve is closed. As the print head starts moving, open the valve to deposit the wax.
10. Once the casting procedure is complete, turn off the firefly components, to stop the steppers.
11. Leave the wax artefact inside water for 10 min to cool off and harden.
Step 12: Safety and Precautions
1. Wear protective Eyeware, Inhalation masks and Hand gloves at all points during the wax casting process.
2. Install thermometers into the wax heating apparatus, to monitor the temperature of wax at all times. Heating apparatuses such as Kettle and Fondue Pots should have built in Thermostats to avoid over-heating of wax that leads to fire hazards.
3. Paraffin Wax melts at 100F / 37C. It is therefore recommended to keep the heating temperature close to 100F.
4. Unplug the power supply from the quad stepper shield, when not in use, to avoid the damages to the arduino shield and boards due to over heating.
5. To avoid short-circuiting, always keep the electronic components and cables elevated and away from the water tank.
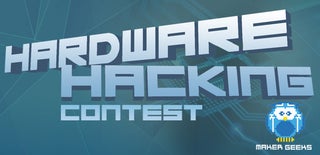
Finalist in the
Hardware Hacking
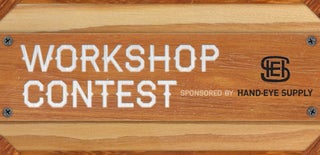
Participated in the
Workshop Contest
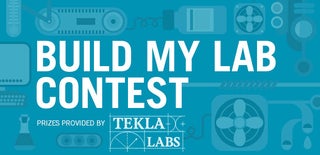
Participated in the
Build My Lab Contest