Introduction: Folding Bed for Car Camping
My wife and I like car camping and road trips. We also have a dog, which can make road trips challenging (try finding a vacancy in a pet-friendly hotel during prime travel season). So a couple of years ago, we traded in our Fit for a Honda Element - what my stepmom calls a "Lego car." We love it - spacious, adaptable, etc. If their production hadn't been ended prematurely, I'm certain they'd be giving the Vanagon and Westphalia conversions a run for their money as the "go-to" travel vehicle when you want to go do stuff.
After failed experiments with an air mattress (they *always* deflate, and can be rather cold on the back), I started poking around the various Element owner communities, checking out different designs for car beds. Our first version stopped at the posts for the back door (similar to the current version); we supported the bottom (foot) half of the mattress on plastic tubs, which rested on the backs of the reclined front seats. It worked okay, but we could never seem to get the same "terrain" two nights in a row.
Thus, the Narwhale car bed was born.
Step 1: The Basic Design
For those who haven't seen one, the rear seats of a Honda Element can be laid flat (forming a rudimentary bed), folded up (attaching to the upper hand grips with carabiners), or fully removed. Since we rarely carry passengers (besides Molly, our pup), we save weight and space by putting them in storage during travel/camping season.
My primary design goals were:
1. safety - principally, determining a means by which our camping gear or luggage wouldn't become projectiles or act as a "trash compactor" in the event of a collision
2. weight - less "dead" weight means less wasted gasoline. The Element (aka the "Toaster") is not known for its fuel economy.
3. simplicity - I wanted something with as few mounting points and moving parts as possible. KISS.
The stock seats clip into very solid metal brackets on either side, and in the floor. Since these are welded to the frame and are already designed to hold a human in comfort and safety, they seemed the best way to secure a bed, as well.
Working with 3/4" FSC-certified plywood (larch, I think - but it's been awhile), I cut eight blanks for the side braces. At four pieces per side assembly, this meant the braces would 3" thick - fairly robust.
To ensure that everything lined up well, I stacked and clamped each side assembly, drilling three 1" holes along the length of each. Into these, I inserted 1" dowels with 1" slots cut into each end. Wood screws drilled into the center of these slots meant that I could work with each assembly without glue until everything was properly fitted.
I cut the 2" holes with a Forstner bit. These are centered over the metal side brackets for the seats. The braces are designed to attach with 5/16" hook bolts (for simplicity, I used 5/16" hardware throughout the project). The "hook" portion rests in the space created by the 2" hole (opened up to allow for other material surrounding the side brackets), and is tightened with a rachet from 0.75" holes drilled into the top surface of the side braces.
Step 2: Cutting Tops for the Braces
If I were to do this again, I think I'd rather use 0.25" aluminum for the tops, as this would obviate the need for extra material in the tails, and provide far stronger support for the cot arms (more on this later).
The technique here is simple - take cardboard and scissors, and trim until you have a perfect fit to the back of the car (it tapers slightly). I used 0.25" wooden dowels to pin the top in place, and then trimmed the brace assemblies to fit with a bandsaw. Easy-peasy.
Step 3: Hidden Hardware
I'm a firm believer in over-engineering. Since the side braces would ultimately bear the weight of two people - plus the lever-augmented force of the cot portion (more on this in a moment), I wanted to be absolutely sure that the braces would be up to the task. So I added two-foot sections of c-channel to the back (hidden) side of each brace, inset into the brace with shallow cuts made on a table saw. These are attached with 5/16" bolts, flat washers, lock washers, and lock nuts. They ain't goin' nowhere.
Similarly, I was concerned that the j-hooks which attach the braces to the seat brackets would be bearing a lot of weight and leverage. To keep these from "pulling through" the plywood, I used a Forstner bit to countersink a 0.25" stack of 1.5" fender washers underneath the brace tops. Again, I found that a 3/4" hole through the tops was just sufficient to allow a 0.5" socket head (which fits the nuts for the 5/16" j-hooks). Once the braces and tops were pinned and glued, none of the metal hardware was readily visible.
Step 4: Gluing and Initial Fitting
I <3 speed clamps. So easy to use.
During gluing, I replaced the drilled split-dowels I'd used to keep the brace assemblies together during the earliest stages with freshly split dowels into which I inserted wood wedges. The result was aesthetically pleasing, but also required no additional hardware.
The braces fit perfectly, first try.
As you'll recall, my primary concern is safety. Although the side braces are very solidly bolted to the metal seat brackets along each side, I also wanted to secure the entire bed assembly to the metal floor mounts. Since I had a length of sturdy 1.5" aluminum pipe around (I believe it was salvaged from a concert stage), I used it as a cross-brace, attaching it to the floor mounts with a 1" nylon strap (tightened via ratchet). This was later replaced with a much stronger strap and ratchet. Plastic traction pads inserted between the strap forms a functional bulwark between the cargo and passenger areas.
Step 5: Assembling the Folding Cot Assembly
When I used to backpack more, I was especially concerned about the weight I had to carry. One of the tricks I learned early on was to get a 1/2 length sleeping pad - since our legs bear very little of our weight when we sleep. Based partly on this understanding, and partly on the old aluminum and canvas folding cots from family camping when I was younger, I designed a folding "cot" assembly that could cantilever over the reclined front seats (or behind them, if they were pushed all the way forward), and fold back under the bed when not in use.
The principle is simple: create a pivot point on either side, far enough back that when folded, the cot arms just fit side-to-side between the side braces, and accommodate a full-length mattress when deployed.
I used 3/8" clevis pins (inserting a small bolt into the hole in the base, to secure the pin in place). Because it was possible that this pivot would face a lot of force (think "human body on the end of a pair of levers"), I added an additional top brace cut from 0.25" steel. If I were to redesign the bed today, I'd either countersink the top of the pivot bolt into the metal top brace, or preferably, replace the entire plywood top to each side brace assembly with a matching piece of 0.25" aluminum plate (==bombproof).
Step 6: Second Fitting and Cot Testing
Once the cot assemblies were completed, I re-installed the braces in the car to double-check whether the cot arms would clear the seats in both reclined and full-forward position.
You may notice a few things in these photos.
First, because we travel with our dog, I wanted her to be secure in case of an accident, while still allowing her to move around a bit. If you look at the cross brace (which also has a black canvas seat cover attached), you'll notice I've attached a zip line and pulley, to which we attach Molly's chest harness. I added a short bungee section at one end, so that she wouldn't come to a cold stop, were we ever in an accident.
Second, the cot is permanently attached along the passenger's side, and then temporarily attached to the driver's side each time it is deployed. To keep the cot arm on the passenger side from pulling towards the center as the driver's side is attached, I added an eye bolt and a short length of bungee (here, only a temporary for the fitting).
Third, after cutting and fitting, I was still somewhat concerned about the ability of the 1" steel tubing to bear our weight. To "beef up" the cot arms, I bolted 1" iron angle iron along each. You could do chinups on them now.
Step 7: Cot Attached, Final Fitting
By attaching the cot material (1000 denier cordura) permanently to the passenger's side cot arm (using grommets and bolts with lock-nuts), we are able to secure both cot arms in place when the bed is stowed, by wrapping both folded cot arms with the cot material. Here, we held it in place with a bungee, but when we finished the cot, we sewed 1.5" one-wrap (double-sided hook-and-loop) between the grommets on the driver's side edge of the cot material. That thing ain't going nowhere in an accident.
I suppose I should have explained earlier - the reason why we didn't need a solid surface to support the bed is because we are using sprung plywood slats (from everyone's favorite Swedish supply store) instead. They are far lighter and far more comfortable than a solid chunk of plywood, and offer more than sufficient support. They are also rather easy to store during the off-season.
After laying out the slats to estimate spacing, I drilled holes into each end, and laced them together with paracord, using fairly thin PVC tubing for spacers. The three "additional" slats fit under the cot canvas, held in place by tension. They are quite sufficient to support our legs - my wife has even sat on the front of the cot (saying goodnight to our pup, who sleeps on the passenger seat at night). The bed is solid - not a single squeak.
Step 8: Sanding, Painting, and Final Installation
Once everything had been fitted, I tore the bed assembly down again for routing (smoothing the edges), sanding and painting. This was by far the biggest hassle of the entire project, as we have no space that's truly appropriate for painting - the shop doesn't allow painting or varnishing.
However, after hacking together a rudimentary paint booth from two boxes from our local bicycle store, and a couple weeks of "paint and wait ... and wait, and wait," it was finally finished.
I had wanted the bed to be basically invisible from the outside of the vehicle (we have limo tinting on the rear windows), so I went with flat black. Concerned about rattling, etc. while we were driving, I used plastidip - which I like for its appearance, but not necessarily its durability. Were I to improve this project, I would definitely re-think the painting.
One exception to this are the plywood slats. These, I painted completely with a standard flat black paint, and then applied black plastidip to the top surface only. This keeps the mattress from moving during the night, as we get in or out of bed, and works marvelously.
Step 9: Finished, With Demo
So here it is, fully deployed. After more than twenty nights (in all sorts of conditions), I can say that it is by far the most comfortable vehicle-based bed I have ever slept in. That includes bullis (VW busses), pop-up campers, 5th-wheel campers, and crashing in the driver's seat.
I've included a video, in which I ramble on about the bed's details, while setting it up.
Enjoy!
Parts list:
- 8'x4' 3/4" plywood - I only just over half a sheet
- IKEA SULTAN LURÖY slatted bed base, full
- 1.5" fender washers (x10)
- 5/16" clothesline hooks (x4)
- 1.5" aluminum pipe, salvage
- 1" square steel tubing (4' x2)
- 2"x1/4" c-channel (2 x3')
- 1" angle iron (3' x2)
- 5/16" clevis pins (x2)
- 1/8" aluminum bar (~2 ft - used as base/pivot for cot arms)
- 1/4" steel plate (1' total)
- 1.25" steel eye hooks (x2 - for clipping slats to front edge)
- Paracord (20' x 2)
- Plastic tubing, for spacing slats (4')
- U-bolts (x4)
- nuts, bolts, washers, glue, etc.
- Mattress (my wife insisted on the SULTAN FIDJETUN, but there are cheaper options)
Step 10: Step 10: Loaded and Fully Disassembled
It occurred to me that it might be useful to see how we pack for trips, so as I was removing the bed for storage (we've reached the rainy season here in the PNW), I took a few snaps of the cargo area.
The cooler is 36-qt. It holds enough for two of us for three or more days, and keeps ice nicely.
By chance (more than design, I must admit), two of these "3-bin modular haulers" fit perfectly alongside the gear sling, and behind the cooler. It's greatly simplified packing for trips, and managing our gear when we're on the road.
The final photo shows the entirety of the bed and platform, disassembled for storage. I forgot to bring a scale down to weigh these parts for comparison against the stock seats, but I am quite certain that the bed and platform are significantly lighter than the seats. In fact, I'll bet they're closer to the weight of just one stock seat. The gear kinda blows out any weight savings, of course.
Anyway, it disassembles very quickly - something like 10 minutes, soup to nuts. Reassembly takes a bit longer, but not by much. I can't wait until next Spring!
Apologies for the craptacular photos.
Step 11: Weight Comparison: OEM Vs. Bed
I reinstalled the bad last night, in preparation for the upcoming camping season. This time, I remembered to bring the scale down to the garage, so I could compare the weight of the OEM seats vs. the bed system.
OEM seat: 45# (x2) = 90#
Bed - side braces 16# (x2) = 32#
Bed - slats = 16#
Bed - mattress = 20#
Bed - crossbar = 12#
Bed total = 90#
So no weight savings over the stock seats (though we could shave a few pounds with a thinner mattress). But we gain a secure cargo area, zip line for the pup, and a super-comfy bed. We're quite happy with that tradeoff.
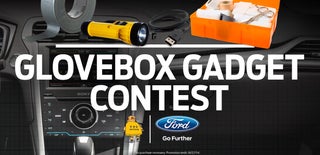
Second Prize in the
Glovebox Gadget Challenge