Introduction: From Beat Down Pram to Shiny Kids-trailer
Some months ago we where cleaning out one of our prop storage rooms (they really tend to fill up and get messy very quickly). While throwing out old useless stuff, I found the leftovers from a 50ies or 60ies pram. There was no more cover, the wheels belonged to another pram, only the body and the handle were left.
Somehow it jumped to my mind, let's build a trailer for my kid out of this!
And that's exactly what I did!
I divided this instructable in "logical steps" rather than using chronological order. So you will see various stages of the trailer conversion in each step. I did a lot of switching between different parts of the work, as this build went on for about 4 months. First I worked at the props workshop in the theatre, whenever there was a time slot I normally would have used to get home earlier or to grab some coffee and have a chat. It was also nice to work with proper tools (for example the vent for the paintjob) and to have lots of scrap wood and other materials at hand. After the hardware jobs where done I took the trailer home for sewing and upholstery.
The tools I used for this build are to many to list one by one. Worth to mention besides the usual suspects (powerdrill, spraycans, staple gun and various pliers, drills and knives,...) are probably a pipe cutter (step 3), the vent (step 4), my sewing machine (step 8), the hole punches and press pliers (step 8), all the rest you need for a project like this you probably will have at hand already...
Step 1: Planning
In the beginning there was an idea, then came a plan, at least sort of...
There was I with the leftovers of the pram. First I did some measuring. I very quickly decided to get an old kids trailer for the chassis. I found one close by for 30 €.
Back in the shop I almost couldn't believe that the lenght of the trailer was a perfect fit for my project. With the excess width I dealt later.
The side parts from the softtop of the old trailer should go in to a angled position to give a nice silhouette.
The original floor panel had to come off. I wanted a curved underbody. Like this it also should be possible to lower the seating position as much as possible to get the center of gravity down.
Step 2: Bodywork
First of all, I took of the handle and the last remaining other metall parts. Then ripped of what was left from the upholstery on the edge of the opening.
Then I cut off a bit of the sidepanels in each corner, so that the wooden frame could sit firmly on the chassis of the donor trailer.
The original floorpanel had to go as well. It was just a piece of hardboard, stapled to the wooden frame, so no problem here (just a large screwdriver and some brute force needed).
Then I built a simple curved frame which I glued and screwed to the original frame. It's purpose is to fit on a curved new floorpanel and to give additional support and stability to the lower part of the sidepanels.
The gaps between the original frame and the side panels I filled with styrofoam.
Then I added to wooden wedges on the back half of the frame for the seat and a sheet of plywood as floor for the "luggage compartment".
After this was all done I screwed on the new floorboard, starting on one end working my way around the curve screw by screw parallel on each side.
Finally I used lots of putty to hide the screws and fill all the gaps before the paintjob.
Step 3: Chassis
As mentioned before, the length of the chassis was perfect, but the width wasn't. As my friends from the metal shop didn't recommend to cut and weld (tubes to thin for a save connection with their toolset) I decide on another approach.
I cut out a piece in the center of the front and rear tube of the frame with a pipe cutter. Then took a piece of pipe with fittng outer diameter and stuck it into the ends to reconnect both sides of the frame. The inner piece of pipe was first glued in with 2K-glue and bolted thru later.
When you changed the width of a trailer, naturally you also have to change the drawbar, or your trailer will be out of center behind your bike. I did some drawing on a large sheet of paper to decide how far I had to bend the drawbar outwards (basically half of the distance I had to cut off in the middle of the frame). Then I filled the drawbar with sand to avoid to much denting in the bend, put on end into the vice and used some brute force to bend...
Step 4: Paintjob
As body and chassis where done it was time to get onto the paintjob. But first things first.
Before painting I did a lot of sanding. On the body especially where I used putty but also on the parts with the originaly finish, because there where a lot of scratches and cracks, or the paint had peeled. I started with a rough grit and worked my way to a very fine one (almost polishing). On the chassis I peeled of the remaining stickers and gave all parts a quick sanding with a middle fine grit.
On this part of the build a good filtered vent is a absolute plus! If you don't have acces to one use a mask and do it in a room with enough airflow. And cover the area around your workplace generously (spray paint flies further than one might think).
Also plan enough time to let the paint dry between layers! Be patient! Working to quickly and with to much paint will result in ugly running noses!
First I sprayed the body with two coats of primer, sanding in between and after.
Then I spray painted the inside white (two coats, no additional sanding here)
After covering the opening with strong paper and lots of masking tape came several coats of glossy red spray paint on the outside, here with some fine grit sanding in between.
The frame for the soft top got also some coats of red spray paint, and the chassis was sprayed in glossy black.
After the red paint was completely dry (I waited 48 hours to be shure) I masked everything else and painted the underbody black (no spray paint here) to match the chassis.
Step 5: Flooring
To hide away the gaps between frame and outer panels, the ugly framing and the traces of former use on the floorboard I decided to cover the floor. I used ribbed rubber mat which I glued on with contact glue.
Be careful here, contact glue and styrofoam don't mix very well...
Step 6: Joining the Body With the Chassis
After the paintjob was done, it was time to connect the body with the chassis. I used holes already in the steel tubing as pattern, drilled trough into the wooden frame and bolted both parts together with carriage bolts.
The frame for the softtop I fastened to the body by adding two L-shaped metal bars.
Then I hooked up the trailer to my bike for the first time, loaded in all the stuff I needed to continue my work and road the baby home...
Step 7: Seating and Safety Belt
In the pile of scrap wood I found the perfect piece for the backrest already with rounded edge. The seat itself was made by two other pieces I cut to size, connected with a piece of square bar. The connection from seat to backrest I did with a piano hinge.
The layout for the safety belt I took from the donor trailer.
To fix the backrest to the body I hade to add an extra bar into the back top part of the body. Into the backpanel I screwed some screw-in nuts, to fix it to this extra bar and also to fix the safety belt to the backrest.
To make the seat a bit more comfortable I glued on some PU-foam we had laying around and rounded its edges with sanding paper.
The upholstery part was very straight forward and done with white(ish) leatherette:
For the backrest I sewed a simple bag, pulled it over the backrest, stapled the front part of the opening around the corner, tucked the back part in and screwed the piano hinge on.
For the seat I took a square piece of leatherette. First I put the seat on it and marked the slot, where the center part of the seat belt had to come trough. Then I cut the slot. To reinforce the slot I sticked another small piece of leatherette behind the slot with some tape. Then I sewed to rounds around the slot and cut the slot through the reinforcement as well.
To staple the leatherette on the seat I had to be very careful to keep the slot in it's place (it helps to loop something through). After stapling I cut off the excess leatherette.
For the layout of the seat belt I took my cues from the donor trailer and adapted it to my seat. It's basically a three point safety belt with shoulder straps and a center part between the legs. It consists of a basic cross or "H" to wich the shoulder straps are attached by sliders. Like this it is possible to adjust the upper straps to the proper shoulder height.
upper straps of the basic "H" screwed to backside of backrestThe upper and middle ends of the basic cross are wrapped around the backrest and then screwed to it through eyelets, the lower ends are pulled thight around the lower edge an then screwed fix with two screws from the piano hinge.
Step 8: Softtop
This part went on for almost one month. Mainly because there was not enough spare time between work, daddy time and sleep, but also because I couldn't find a doable way to make the softtop for a long time.
The fabric was chosen (tent canvas), the rough form was given by the existing frame and I wanted to use large pushbuttons instead of velcro to stay in the vintage style. But that was about all that was clear. I made a very basic prototype and stared at it for weeks.
On the road I looked at a lot of kids trailers to come up with a pattern. Specially the side parts proofed to be difficult to come up with a solution, mainly because I wanted to much.
The side panels:
Once I could get rid of my complicated ideas (hollow seam for the tube, canvas with a sewed in pvc-window, etc. etc), it became very simple and straight forward:
I decided to make the side panels out of one piece of clear pvc foil edged with polypropylen (PP) ribbon. As simple as that. So I made a prototype and even found an easy way to fix it to the frame. After that I decided on where to put the pushbuttons and other fixtures, reworked the prototype to get a final pattern.
The top:
Here the basics where clear as well: closed top, net in front with a additional clear pvc rain cover and turn clasps to fix it to the body. So again I made a prototype/pattern out of packaging paper to get to the final pattern. Best is, you look at the pictures and read through the notes, then you will get how I made it.
Step 9: Final Touches
I designed a logo for the trailer made with reflectiv foil.
And a new set of tires I added as well.
I added reflectors an flags for better visibility on the road.
I had a special name plate made (not attached yet)
Still on the to do list are:
Attach name plate (done)
Lights
I will have to adjust the level of the seat. I started the build (and took measures) in february and the little one got bigger in the meantime... (working on it already...) (Done! Step 7 will get an update soon, or maybe I just added another step)
I really would like to add monkey lights to the wheels, so vote for me please...! ;-) (thanks to all who voted and made this instructable a winner!)
Summer side panels to allow more airflow in the sunny season.
On the "maybe to do" list:
In the future I plan to add some extra lighting. Red LED under floor lighting maybe???
Step 10: Maiden Voyage
Today was the first sunny day this week and so I took the kid on a short trip to the playground in his new trailer. He really seemed to like his new ride!
And the trailer created quite a buzz on the playground... :-)
Step 11: New Deluxe Seat
I recently changed the seating in the trailer from padded wood to a suspended seat. I took a few cues from outdoor camping seats I saw in a shop, but see for yourself….
The tubes I used come from the old trailer I used for the chassis. They are fitted to the inner frame with some special screws meant for fencing (a least that's what was written on the shelf at the hardware store). With some plastic tube it just fitted perfectly for my purpose. The net was saved from trash at my workplace, the local theatre, and the fabric was left from the softtop.
I reached the goal to lower the seating position, make the seating more comfortable and improved the seatbelt. And as an extra bonus the trailer lost a bit of weight.
Step 12: One Year After....
It took a while, but now I finally have a matching bicycle for the trailer...
The trailer itself got a few updates:
- white rally stripes to match bike and helmet
- rims painted in same colour scheme as the bike rims
- playmobile valve caps
- trolley wheel
- lights: red LEDs, battery and switch built into a vintage repairkit tinbox
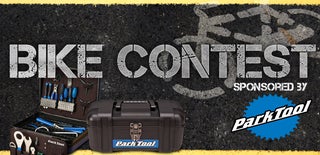
First Prize in the
Bike Contest
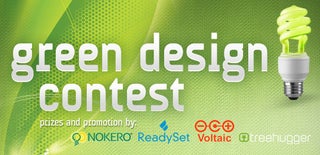
Participated in the
Instructables Green Design Contest
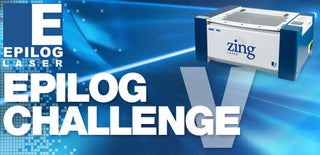
Participated in the
Epilog Challenge V