Introduction: Galvanized Pipe and Glass Insulator Wall Sconce
With some 1/2" galvanized pipe, some connectors, glass telephone insulators, and some time you can create a unique wall sconce for your home. My wife found examples of these in Pinterest and Etsy and wanted to have them for our new house, so we decided to try making our own. You can keep track of other projects at our house blog, OnceUponAnAcre.blogspot.com. Here's how we put the wall sconces together.
Step 1: Materials Needed
Most good hardware stores should have galvanized pipe and pipe connectors available in 1/2" sizes near the gas or electrical conduit sections. Look for the electrical components in the lighting section, usually in a back corner where replacement sockets are stocked.
For the main housing you'll need:
* 1 x t-connector. There are several sizes available, make sure you get one with 1/2" connections on all three ends.
* 1 x 1/2" end cap
* 1 x reducer or coupler that goes from 1/2" to 1/4" threads
* 1 x 1/2" short threaded coupler. This is basically a really short pipe that's threaded the entire length.
* 1 x 1/2" floor flange.
NOTE: See step nine for an alternate list of galvanized parts if you want to hard-wire this sconce into a standard wall receptacle.
For the electrical connections you'll need:
* A candelabra base keyless socket. There are many types out there, but the ones at my hardware store were adjustable keyless sockets that you can extend to various lengths.
* Some two-strand electrical cable. Or, if you want to use this as a lamp rather than wiring it up to a wall switch, you can get an extension cable and add an in-line switch pretty easily. Or find an old lamp from good will and use the cable from it. Just make sure it's still in good condition without any frays or breaks in the insulation.
* A candelabra bulb. These are the lights typically found in nightlights.
Other items:
* 1/4" threaded "steel nipples".
Note, you will normally find lengths of threaded brass tubes in what's labeled 1/8" IP or IPA. In order to connect to the 1/2" to 1/4" galvanized adapter, you need the 1/4" IP sections. They're just slightly larger with wider-spaced threads.
* A hacksaw (to cut the threaded pipe and candelabra sections)
* J-B Weld, either Kwik or normal version, depending on how much time you want to wait for it to set.
* Clay, play-doh, plumber's putty, or something else similar. This is used in a later step to create a "water dam" for drilling.
* 1/2" diamond hole saw, preferably a "core" version that drills out a plug of glass. I picked up a two-pack of 1/2" and 1" size bits from Amazon, but there are various types for various prices on the internet or in your local hardware store.
* Water. Easy enough to come by, hopefully.
* A drill press. You could potentially work with a hand drill, but I wouldn't recommend it just for ease of use and accuracy.
* Rubber washers, or felt, or some kind of foam sheet, or cork.
For the main housing you'll need:
* 1 x t-connector. There are several sizes available, make sure you get one with 1/2" connections on all three ends.
* 1 x 1/2" end cap
* 1 x reducer or coupler that goes from 1/2" to 1/4" threads
* 1 x 1/2" short threaded coupler. This is basically a really short pipe that's threaded the entire length.
* 1 x 1/2" floor flange.
NOTE: See step nine for an alternate list of galvanized parts if you want to hard-wire this sconce into a standard wall receptacle.
For the electrical connections you'll need:
* A candelabra base keyless socket. There are many types out there, but the ones at my hardware store were adjustable keyless sockets that you can extend to various lengths.
* Some two-strand electrical cable. Or, if you want to use this as a lamp rather than wiring it up to a wall switch, you can get an extension cable and add an in-line switch pretty easily. Or find an old lamp from good will and use the cable from it. Just make sure it's still in good condition without any frays or breaks in the insulation.
* A candelabra bulb. These are the lights typically found in nightlights.
Other items:
* 1/4" threaded "steel nipples".
Note, you will normally find lengths of threaded brass tubes in what's labeled 1/8" IP or IPA. In order to connect to the 1/2" to 1/4" galvanized adapter, you need the 1/4" IP sections. They're just slightly larger with wider-spaced threads.
* A hacksaw (to cut the threaded pipe and candelabra sections)
* J-B Weld, either Kwik or normal version, depending on how much time you want to wait for it to set.
* Clay, play-doh, plumber's putty, or something else similar. This is used in a later step to create a "water dam" for drilling.
* 1/2" diamond hole saw, preferably a "core" version that drills out a plug of glass. I picked up a two-pack of 1/2" and 1" size bits from Amazon, but there are various types for various prices on the internet or in your local hardware store.
* Water. Easy enough to come by, hopefully.
* A drill press. You could potentially work with a hand drill, but I wouldn't recommend it just for ease of use and accuracy.
* Rubber washers, or felt, or some kind of foam sheet, or cork.
Step 2: Assemble the Galvanized Components
The galvanized pieces of pipe are easy enough to put together. The 1/2" threaded section is used to connect the flange to the short end of the t-connector. The plug connects to one of the straight ends. The 1/2" to 1/4" adapter goes into the other end. Finally, test that the threaded brass tube screws into the adapter. As a tip, take a moment to mark the brass tube with a permanent marker at the point it stops, so that you know how far to screw the pieces back together with everything assembled later.
Step 3: Disassemble the Candelabra Socket
If you found the same candelabra adapter that I did, you'll notice that there are two screws on the side of the silver metal section that can be loosened up to lengthen or shorten the adapter. You'll want to completely remove those two screws and the sliding components, just leaving the candelabra base and two metal "prongs".
The metal is soft enough to bend easily, and you can squeeze the sides together slightly to see how it can grab the threaded brass tube in the galvanized pipe. The sides are much too long to fit inside the glass insulators as they are, so in the next step we'll cut them down to the length we need.
The metal is soft enough to bend easily, and you can squeeze the sides together slightly to see how it can grab the threaded brass tube in the galvanized pipe. The sides are much too long to fit inside the glass insulators as they are, so in the next step we'll cut them down to the length we need.
Step 4: Cut the Threaded Connector and Candelabra Legs
The candelabra base I'm using has a single screw in the base of the socket that holds both of the metal "legs" together. Just remove that screw and the legs should pull off.
What we're going for is about 1/4" of space between where the bottom of the socket and the start of the brass tube. This is enough room to get our wire through on each side to connect to the socket later on. On the candelabra base I'm using, that came out to be exactly where the "legs" widened out and bent in on the sides slightly.
Once you have that measurement, we want to measure another 1/4" to 1/2" of the metal to leave behind that will be glued around the threaded brass connector. This is where we need to cut the metal of both "legs". I was able to use a vice to clamp the legs together, back-to-back, and cut through them with a hacksaw. Take a look at the second photo here to see how much metal was left after I finished the cuts. Reassemble them onto the candelabra base, then squeeze them together slightly to test-fit it onto the threaded brass tube again.
What we're going for is about 1/4" of space between where the bottom of the socket and the start of the brass tube. This is enough room to get our wire through on each side to connect to the socket later on. On the candelabra base I'm using, that came out to be exactly where the "legs" widened out and bent in on the sides slightly.
Once you have that measurement, we want to measure another 1/4" to 1/2" of the metal to leave behind that will be glued around the threaded brass connector. This is where we need to cut the metal of both "legs". I was able to use a vice to clamp the legs together, back-to-back, and cut through them with a hacksaw. Take a look at the second photo here to see how much metal was left after I finished the cuts. Reassemble them onto the candelabra base, then squeeze them together slightly to test-fit it onto the threaded brass tube again.
Step 5: Drill Through the Glass Insulator
There weren't many instructions with the drill bits I received, so I did a bit of quick research online for the best practices when drilling glass. The most important point I found is that you need to keep the drill bit cool to function correctly. The easiest way to do that is to keep it submerged in water while drilling. And the easiest way to do that is with a "water dam" technique. All this really means is taking some clay and building a little cup around the section of glass you want to cut, then filling it with water. This keeps the drill bit completely under water for the entire process.
The second piece of advice is to "pump" the drill bit while you work. This just means that you should apply slight pressure to the drill bit for a second, then release and move the bit back out of the hole to allow more water to flow into place. Then repeat until you cut all the way through the glass. This keeps the water in contact with the tip of the drill bit, keeping it cool, and also helps remove the glass particles from the cut as they're ground away. As practice the very first time, I drilled through a cream soda bottle that I had in the garage, which you can see in the last photo.
As I mentioned at the start of this instructible, I highly suggest using a drill press for this process. Glass insulators are fairly thick, and getting a straight, clean hole drilled through is much easier with a stationary drill press.
Start by marking the center of your glass insulator with a permanent marker right at the location you want to drill.
Next, take some clay and work it into a circle. Then, apply it around the top of the insulator and squeeze it up into a small cup-shaped section.
Fill the clay section with water. About 1/8" to 1/4" of water should be plenty.
Most drill presses should have an adjustable base plate that you can slide up or down to get closer or farther from the drill bit. Set the glass insulator on that base, then adjust it up until the tip of the drill bit is dipped into the water, but not pressing on the glass yet. Lock the base at that spot. You should also place a plastic bowl or container under the base to catch the water that will drain out when the hole is cut. Also make certain you don't have any electrical connections anywhere near where the water could flow to if the container doesn't catch it all! In the picture of my drill press you can see I put the entire thing inside a large plastic tote we had in the garage.
Move the insulator so that the center dot you marked earlier is in the middle of the hole saw drill bit. This can be slightly tricky when looking through water due to refraction, so check the placement from all angles around the drill press to center it.
Once centered, hold the insulator in place as steadily as possible. Placing a damp towel under the glass can help. Also, just as a precaution, I would suggest wearing strong leather gloves to hold the insulator as protection for your hand, just in case the glass cracks or shatters.
If your drill bits didn't come with speed instructions, set your drill between 700 and 900 RPM for the 1/2" drill bit. If you're using a slightly larger diameter bit, the speed should still be fine. But check online for glass drill bit speeds, that's what I ended up doing.
Start the drill press and begin drilling. Don't press too hard, just let the drill do most of the work and don't forget to only drill for a second or so before releasing and repeating to keep the bit cool. Be patient and keep at it, and eventually you'll feel the bit cut all the way through. At this point you can lift the drill bit and the water will drain through the newly created hole.
Carefully wash off the insulator in some clean water. Be cautious around the cut edges, as they could be sharp. The final hole should be just barely larger than the 1/4" threaded brass tube. Test it now to make sure. If it sticks, run the hole saw through the hole again with slight pressure along the sides to widen it a tiny bit. If you can, have someone else help at that point, to keep water on the drill bit as you work. I cut through four insulators and all but one fit perfectly the first time. The last only needed a tiny bit removed at the base to fit fine.
The remaining glass "plug" should fall out of the hole saw bit at the same time. If it doesn't, remove the drill bit and tap it lightly on a desktop or against the side of a bucket and it should drop out. Be careful picking up the plug, as the end opposite the dot you marked earlier tends to be sharp. No matter how carefully you drill, the very last millimeter or so of glass tends to crack rather than cut due to the pressure applied. You'll also find quite a few small glass shards in the water that you were using, so very carefully dispose of that!
The second piece of advice is to "pump" the drill bit while you work. This just means that you should apply slight pressure to the drill bit for a second, then release and move the bit back out of the hole to allow more water to flow into place. Then repeat until you cut all the way through the glass. This keeps the water in contact with the tip of the drill bit, keeping it cool, and also helps remove the glass particles from the cut as they're ground away. As practice the very first time, I drilled through a cream soda bottle that I had in the garage, which you can see in the last photo.
As I mentioned at the start of this instructible, I highly suggest using a drill press for this process. Glass insulators are fairly thick, and getting a straight, clean hole drilled through is much easier with a stationary drill press.
Start by marking the center of your glass insulator with a permanent marker right at the location you want to drill.
Next, take some clay and work it into a circle. Then, apply it around the top of the insulator and squeeze it up into a small cup-shaped section.
Fill the clay section with water. About 1/8" to 1/4" of water should be plenty.
Most drill presses should have an adjustable base plate that you can slide up or down to get closer or farther from the drill bit. Set the glass insulator on that base, then adjust it up until the tip of the drill bit is dipped into the water, but not pressing on the glass yet. Lock the base at that spot. You should also place a plastic bowl or container under the base to catch the water that will drain out when the hole is cut. Also make certain you don't have any electrical connections anywhere near where the water could flow to if the container doesn't catch it all! In the picture of my drill press you can see I put the entire thing inside a large plastic tote we had in the garage.
Move the insulator so that the center dot you marked earlier is in the middle of the hole saw drill bit. This can be slightly tricky when looking through water due to refraction, so check the placement from all angles around the drill press to center it.
Once centered, hold the insulator in place as steadily as possible. Placing a damp towel under the glass can help. Also, just as a precaution, I would suggest wearing strong leather gloves to hold the insulator as protection for your hand, just in case the glass cracks or shatters.
If your drill bits didn't come with speed instructions, set your drill between 700 and 900 RPM for the 1/2" drill bit. If you're using a slightly larger diameter bit, the speed should still be fine. But check online for glass drill bit speeds, that's what I ended up doing.
Start the drill press and begin drilling. Don't press too hard, just let the drill do most of the work and don't forget to only drill for a second or so before releasing and repeating to keep the bit cool. Be patient and keep at it, and eventually you'll feel the bit cut all the way through. At this point you can lift the drill bit and the water will drain through the newly created hole.
Carefully wash off the insulator in some clean water. Be cautious around the cut edges, as they could be sharp. The final hole should be just barely larger than the 1/4" threaded brass tube. Test it now to make sure. If it sticks, run the hole saw through the hole again with slight pressure along the sides to widen it a tiny bit. If you can, have someone else help at that point, to keep water on the drill bit as you work. I cut through four insulators and all but one fit perfectly the first time. The last only needed a tiny bit removed at the base to fit fine.
The remaining glass "plug" should fall out of the hole saw bit at the same time. If it doesn't, remove the drill bit and tap it lightly on a desktop or against the side of a bucket and it should drop out. Be careful picking up the plug, as the end opposite the dot you marked earlier tends to be sharp. No matter how carefully you drill, the very last millimeter or so of glass tends to crack rather than cut due to the pressure applied. You'll also find quite a few small glass shards in the water that you were using, so very carefully dispose of that!
Step 6: Cut the Brass Tube and Glue on the Base
Now back to the lighting components. The legs of the candelabra base are ready, so we need to glue the base into place, then cut the brass tube to the correct length. First, make sure the "legs" of the candelabra base are firmly squeezed onto the brass tube. Do some test fitting and bending of the pieces to get a solid seating before you add the glue for best results. Just make sure you have the 1/4" gap between the base of the socket and the brass tube for the wire to come out later.
Second, follow the instructions on the JB Weld to mix together the two parts of the epoxy, then spread it around and into the gaps of the metal legs and the threads of the brass tube. You'll want to be careful to not get any (or at least not much) into the threads above the metal legs, since that's what slides through hole you drilled in the glass insulator. Once you have every section covered, let it set for the recommended time from the instructions.
Once everything is fully dried, it's time to measure:
a) the thickness of the glass you drilled through earlier,
b) the length of the brass tube that screws into the 1/2" to 1/4" galvanized reducer, and
c) the length of the brass tube that the metal legs of the candelabra base covers, including the glue you've applied.
Add those lengths together to get a rough length for the tube. Then, subtract about 1/8" from the measurement. This will leave you with a long enough section of threaded tube to go through the glass insulator and screw into the galvanized pipe without being too long. If you're even slightly longer than needed, you won't be able to screw the sections together enough to lock the glass insulator in place.
The best way to make sure this works is to get the measurement calculated above, mark that line on the tube, then slip it through the glass insulator from the inside all the way. Measure from the glass to the mark you made and make sure that's slightly less than the measurement of how much of the threaded tube can be screwed into the galvanized section.
Once you've measured twice, go ahead and cut once. Use a hacksaw to cut through the brass tube at the mark you finalized. A brass tube should cut through pretty easily with a normal hacksaw blade. After making the cut, test fit the tube into the galvanized base again. If it all looks good, do a final test fit with the glass insulator as well. Don't screw the two pieces together too hard right now, so you don't scratch or crack the glass, but make sure the glass isn't loose. If it's too loose, cut a bit more of the brass tube and try again.
Second, follow the instructions on the JB Weld to mix together the two parts of the epoxy, then spread it around and into the gaps of the metal legs and the threads of the brass tube. You'll want to be careful to not get any (or at least not much) into the threads above the metal legs, since that's what slides through hole you drilled in the glass insulator. Once you have every section covered, let it set for the recommended time from the instructions.
Once everything is fully dried, it's time to measure:
a) the thickness of the glass you drilled through earlier,
b) the length of the brass tube that screws into the 1/2" to 1/4" galvanized reducer, and
c) the length of the brass tube that the metal legs of the candelabra base covers, including the glue you've applied.
Add those lengths together to get a rough length for the tube. Then, subtract about 1/8" from the measurement. This will leave you with a long enough section of threaded tube to go through the glass insulator and screw into the galvanized pipe without being too long. If you're even slightly longer than needed, you won't be able to screw the sections together enough to lock the glass insulator in place.
The best way to make sure this works is to get the measurement calculated above, mark that line on the tube, then slip it through the glass insulator from the inside all the way. Measure from the glass to the mark you made and make sure that's slightly less than the measurement of how much of the threaded tube can be screwed into the galvanized section.
Once you've measured twice, go ahead and cut once. Use a hacksaw to cut through the brass tube at the mark you finalized. A brass tube should cut through pretty easily with a normal hacksaw blade. After making the cut, test fit the tube into the galvanized base again. If it all looks good, do a final test fit with the glass insulator as well. Don't screw the two pieces together too hard right now, so you don't scratch or crack the glass, but make sure the glass isn't loose. If it's too loose, cut a bit more of the brass tube and try again.
Step 7: Find or Make a Spacer for the Glass
You should now have almost everything ready for assembly. The last component is some kind of washer or spacer to place between the glass and the galvanized pipe that will allow you to tighten the two together without fear of breaking or scratching the glass. There are quite a few things you could use here. A rubber washer would work, or some thin cork, or a piece of foam sheet cut to size. Since this is a candelabra light, the bulbs don't typically produce much heat. Especially if you go with LED versions, like I have. So you just need something soft enough to use as a buffer, and shouldn't need to worry about heat tolerances unless you try to use a high-wattage bulb.
In my case, I went with the foam sheet. Just cut out a circle that's slightly smaller than the circumference of the galvanized pipe, then cut a smaller circle from the middle that's big enough to fit the threaded brass tube through.
In my case, I went with the foam sheet. Just cut out a circle that's slightly smaller than the circumference of the galvanized pipe, then cut a smaller circle from the middle that's big enough to fit the threaded brass tube through.
Step 8: Assemble and Wire the Light
Now it's time to put all the pieces together. There are two ways to do this, which depends on what kind of wiring you're going with. If you plan to install the light directly into the wiring of the house with a normal wall switch, you'll be using two-strand wire without any controls or plugs attached. This is actually the easiest way to assemble, because you can thread the wire through the components after you attach it to the candelabra base. However, if you want to use the light as a lamp, with an attached plug and on/off switch, you'll need to run one end of the wire through all of the components first, then wire it into the candelabra base. Still not terribly difficult, just slightly more cumbersome.
Also, if you're going to mount the light to a wall as a normal lamp, you'll want to grind out a notch in the back of the galvanized floor flange for the wire to run through so that the flange will still press flush against your wall. You can use any grinding tool of choice, either an electric hand grinder or a dremel, although the dremel may take some time. We didn't need this ourselves, so you may want to experiment on an extra floor flange to find out the best method to use.
I'll assume you'll be using the plug and switch method here. Just thread one end of the wiring through the back of the galvanized pipe components, then the washer, the glass insulator, and finally the threaded brass tube. Before threading through the brass tube, split the end of the wire into the two strands.
Look closely at the two strands of wire, or feel them with your fingers, and you'll notice that one of them is smooth and the other has one or more notches or grooves in it. This indicates which side is the "neutral" wire that needs to be attached to the silver screw on the candelabra base, as the instructions for the socket should say. So slip the wires through the brass tube so that the correct wire can be pulled out next to the required screw terminal.
You can strip the insulation back from the ends of the wire by 1/2" to 5/8" and twist the strands together before or after threading it through the brass tube. I found it easier to have them stripped and ready first. Now you see the reason we left a 1/2" gap between the brass tube and the base of the candelabra base. Wrap the wire clockwise around the loosened terminal screws, then tighten the screws to hold the wire into place. Once everything is wired together, replace the cardboard tube over the candelabra base to cover the exposed wires.
At this point you can insert a bulb and carefully plug in the end of the cable to make sure you're connections are good. Just don't hold the bulb base while doing this, in case of any shorts in the connections. If everything lights up, great! The last step is assembly!
Just pull the wiring back through the pipe until you can connect the threaded brass tube into the galvanized pipe. Now this will mean some twisting of the wire as you turn the bulb base to connect it, so twist everything counter-clockwise a few times first, then start screwing the components together. If you still have some twists in the wire, you should be able to twist the end coming out of the back of the galvanized pipe as well with a little fiddling. Screw the components together enough to get a solid connection between the galvanized pipe, the washer, and the glass. The glass shouldn't be loose at all, but you don't need to over-tighten the pieces.
Once assembled, mount the flange to your wall (preferably to a stud, or using drywall anchors), plug it in, and enjoy your unique lighting!
We're going to be using our sconces as artwork lighting attached to a wall switch in some new construction. Since the 1/2" base of the wall flange in this tutorial is smaller than the typical receptacle an electrician installs, we'll need to use slightly different parts to make this hard-wired ready. Check out the next step for the adjusted parts list.
Also, if you're going to mount the light to a wall as a normal lamp, you'll want to grind out a notch in the back of the galvanized floor flange for the wire to run through so that the flange will still press flush against your wall. You can use any grinding tool of choice, either an electric hand grinder or a dremel, although the dremel may take some time. We didn't need this ourselves, so you may want to experiment on an extra floor flange to find out the best method to use.
I'll assume you'll be using the plug and switch method here. Just thread one end of the wiring through the back of the galvanized pipe components, then the washer, the glass insulator, and finally the threaded brass tube. Before threading through the brass tube, split the end of the wire into the two strands.
Look closely at the two strands of wire, or feel them with your fingers, and you'll notice that one of them is smooth and the other has one or more notches or grooves in it. This indicates which side is the "neutral" wire that needs to be attached to the silver screw on the candelabra base, as the instructions for the socket should say. So slip the wires through the brass tube so that the correct wire can be pulled out next to the required screw terminal.
You can strip the insulation back from the ends of the wire by 1/2" to 5/8" and twist the strands together before or after threading it through the brass tube. I found it easier to have them stripped and ready first. Now you see the reason we left a 1/2" gap between the brass tube and the base of the candelabra base. Wrap the wire clockwise around the loosened terminal screws, then tighten the screws to hold the wire into place. Once everything is wired together, replace the cardboard tube over the candelabra base to cover the exposed wires.
At this point you can insert a bulb and carefully plug in the end of the cable to make sure you're connections are good. Just don't hold the bulb base while doing this, in case of any shorts in the connections. If everything lights up, great! The last step is assembly!
Just pull the wiring back through the pipe until you can connect the threaded brass tube into the galvanized pipe. Now this will mean some twisting of the wire as you turn the bulb base to connect it, so twist everything counter-clockwise a few times first, then start screwing the components together. If you still have some twists in the wire, you should be able to twist the end coming out of the back of the galvanized pipe as well with a little fiddling. Screw the components together enough to get a solid connection between the galvanized pipe, the washer, and the glass. The glass shouldn't be loose at all, but you don't need to over-tighten the pieces.
Once assembled, mount the flange to your wall (preferably to a stud, or using drywall anchors), plug it in, and enjoy your unique lighting!
We're going to be using our sconces as artwork lighting attached to a wall switch in some new construction. Since the 1/2" base of the wall flange in this tutorial is smaller than the typical receptacle an electrician installs, we'll need to use slightly different parts to make this hard-wired ready. Check out the next step for the adjusted parts list.
Step 9: UPDATED: Flange Size for Electrical Boxes
After a bit more online and in-store research I found out that the 1 1/2" galvanized floor flange is the perfect size to fit onto a standard square or round outlet box that an electrician installs in the wall for light sconces. So, if you plan to use these as traditional light sconces, here's the adjusted parts list. The only change is to the galvanized pipe components. The electrical remains the same.
* 1 x 1 1/2" floor flange
* 1 x reducer or coupler that goes from 1 1/2" to 3/4" threads
* 1 x 3/4" short threaded coupler. This is basically a really short pipe that's threaded the entire length.
* 1 x t-connector with two 1/2" and one 3/4" threaded ends.
* 1 x 1/2" end cap
* 1 x reducer or coupler that goes from 1/2" to 1/4" threads.
You could also go with all 3/4" pipe, if you wanted to, rather than having the t-connector change back from 3/4" to 1/2" pipe. It's mostly for the look you like, since there are reducers/couplers from 3/4" to 1/4" threads as well as the 1/2" to 1/4" threads in the list above. The main take-away is that the 1 1/2" floor flange has the screw holes in the exact location to attach it to a standard wall sconce electrical box.
If you want to just have a wall light with a plug-in and on/off switch that isn't hard-wired into the house, you can certainly stay with the original parts list for a more compact design.
Thanks for reading!
* 1 x 1 1/2" floor flange
* 1 x reducer or coupler that goes from 1 1/2" to 3/4" threads
* 1 x 3/4" short threaded coupler. This is basically a really short pipe that's threaded the entire length.
* 1 x t-connector with two 1/2" and one 3/4" threaded ends.
* 1 x 1/2" end cap
* 1 x reducer or coupler that goes from 1/2" to 1/4" threads.
You could also go with all 3/4" pipe, if you wanted to, rather than having the t-connector change back from 3/4" to 1/2" pipe. It's mostly for the look you like, since there are reducers/couplers from 3/4" to 1/4" threads as well as the 1/2" to 1/4" threads in the list above. The main take-away is that the 1 1/2" floor flange has the screw holes in the exact location to attach it to a standard wall sconce electrical box.
If you want to just have a wall light with a plug-in and on/off switch that isn't hard-wired into the house, you can certainly stay with the original parts list for a more compact design.
Thanks for reading!
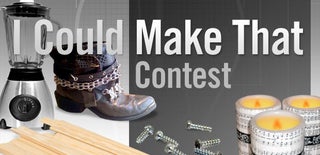
Participated in the
I Could Make That Contest