Introduction: Glass Fused Filament Deposition Modeling (FFDM)
Warning! This project uses a oxygen/propane welding torch mounted to an industrial robot. Extreme caution is advised!!
I was an artist in residence for the Fall 2016 cohort at Pier 9. During my residency, I developed a Glass Fused Filament Deposition Modeling (FFDM) Process. This project merges my traditional craft training with strategies of human/machine collaboration.
Tacit knowledge of craft processes has immense potential to enhance emerging technologies. The sensibilities gained through hands-on experience provide sophisticated comprehension of material behavior, physical properties and responsiveness to environmental conditions. These insights have led me to pursue merging traditional craft proficiency with contemporary technology in an effort to expand the boundaries of material processes. I have developed additive manufacturing processes and subtractive molding processes to integrate glass-forming techniques with robotic technology. Some of my projects are here. My embodied knowledge of material processes is essential to forging innovation with collaborative human/machine fabrication.
My past efforts have demonstrated that collaborative robotic fabrication shares elements of acquired skill, similar to analogue fabrication. For complex processes, the human operator must adjust the various environmental and material parameters continually as a participant within the collaboration. These adjustments are refined with repetition, experience and accumulated skill. The feedback loop between operator, robot, tool and material is continually adjusting and adapting; observations made by the operator are nuanced, sensitive and complex. This sequence of observation, analysis, and action is tacit or embodied by its nature. As both an artist and a researcher, my objective is to develop technological systems to support the integration of embodied human knowledge: how can the nuanced behaviors of a human operator be translated to data for the purpose of designing customized hardware and software? At Pier 9, I pursued these lines of inquiry and developed novel fabrication strategies that exploit inherent physical phenomena accessed through the digital automation of process.
Step 1: Material Form Finding
First, I pay attention to the physical properties of matter. I look for moments of emerging properties in material phenomena. I perform analog experimentation to observe how material behaves. Specifically, I'm looking an ability to accumulate, stack, fold, and self organize, this phenomena can then be exploited using automated processes.
Glass falling onto a moving surface creates a sequence of sewing machine patterns analogous to the phenomena of viscous threads falling onto a steadily moving belt. By changing the parameters of belt speed, height of the thread, and temperature, I am able to replicate stitching patterns with an industrial robot and a glass.
For the past few years, I've been developing a Glass Printer at the Rhode Island School of Design. This design requires a glass furnace at 2100º F to charge a printing cartridge. At Pier 9, I wanted to make a glass printer that doesn't require a furnace for its stock material. I designed a filament based glass printer.
Attachments
Step 2: Choose a Filament Driver
For this process, I will use glass filament as stock material. Therefore, I will need a filament driver. I decided to modify a driver that is used for driving plastic filament. There are lots of filament driver designs to 3D print, but I chose to purchase an aluminum body with a kit. It was very reasonably priced and I could easily customize this driver. I purchased mine here. It came with the following package contents:
1 x Aluminum main extruder body with tension lever and adjustment hardware pre-installed
1 x Stainless filament drive gear for 5mm bore (NEMA 17 shaft)
2 x PC4-M6 straight tube fittings 1 x Assembly screws
1 x NEMA 17 Stepper Motor 57oz-in 40mm long body, with connection cable
Step 3: Find a Filament
For the glass deposition process I experimented with many different filaments of glass. The filament needed to melt quickly, be resistant to thermal shock and work with the driver system. Different thickness of material can be driven through the filament driver, however some modifications have to be made to the gears. I have included the drawing of the gear I machined in a later step.
The glasses I tested:
Moretti Effetre Clear, 5.6 mm - Too large!
Moretti Effetre Clear stringer, 3.5 mm - Works with filament driver, but did not melt sufficiently
Pyrex clear, 3 mm - works with filament driver, melting point too high, need thinner filament
The best filament was Bullseye 1 mm stringer clear and Bullseye .5 mm stringer. These worked well with my driver system and melted at the temperatures I'm using.
Step 4: Wire the Arduino
The next step is to figure out how to drive the stepper motor.
I used the following:
Arduino Uno
Nema 17 Motor
4988 Driver
10K potentiometer in order to change the speed of the motor
I used this to wire the motor. I used sixteenth steps for the stepper.
Below is the Arduino Code used to power the stepper motor.
Attachments
Step 5: Analogue Experimentation
I did a lot of analogue experimentation to figure out how to design the tool for automation. I designed many different prototypes of the tool and experimented with many different kinds of heat. I first used a butane torch, which caused the glass to blacken and become sooty.
Step 6: Prototype Tool
Once I could successfully melt a glass bead using my hand held tool, I began to prototype the tool for the robot arm. I used a Fortus 3D printer at the Pier. I changed the torch to an "Smith Little Torch" for oxygen/propane with a twin flame welding head. Make sure to use flash back arrestors on the regulators for the oxygen and propane tanks.
I then began testing using a Universal Robot 5 different tool paths to find the optimal orientation to deposit the glass.
Step 7: Refine Tool: Fusion 360 CAD
Once I worked out the design of the tool, I wanted to CNC mill the end effector. The PLA plastic of the Fortus PLA 3D print has a low melting point and not the proper material to put in a kiln. I designed the end effector using Fusion 360.
The tool is made of three parts. Here is the CAM for each part:
Step 8: Mill the Tool
Use the CAM files in the previous step. Measure your stock material and update the set-ups. This is the most amazing instructable on learning the CNC mill.
Step 9: Manual Lathe: Nozzle and Gear
I made a custom Nozzle and gear for the driver. Above are the drawings for these parts. I recommend putting a set screw in in the side of the gear.
Attachments
Step 10: Warm the Build Chamber
Many of my early prints delaminated due to temperature changes between layers. I found that I needed to print into a kiln. I purchased the Paragon Caldera. Due to the size of the tool, I could only print smaller objects in this kiln. I think I will need a larger chamber to accommodate both the tool and the print. For smaller prints, this works great and is an economical kiln (it also runs on 120V).
Step 11: Protect Your Wires!
During a long print, I melted the wires to my stepper motor. I purchased a ceramic sleeve and inserted the wires inside. You can buy this from McMaster-Carr. I also placed a ceramic fiberboard gasket underneath the motor and between the robot and the tool.
Step 12: Program the Robot
To program robot tool paths, I use Robots IO for Rhino/Grasshopper. I draw the environment in CAD: the table, kiln, tool and work surface. I can simulate robot movement to make sure that I do not crash the robot into anything Here is a sample screenshot of my programming. Although this is helpful, it is not completely reliable. Sometimes the simulation does not accurately depict what the robot will actually do. So always be prepared to stop the robot if it does something unexpected.
Step 13: Print Glass!
This is not a plug and play machine. The operator must drive the machine and continually make adjustments. As you can see from my documentation, I'm an active collaborator and participant in the printing process. I utilize URScript to program robot movements and an Arduino to drive the filament driver. The torch temperature, kiln, filament speed and robot speed are continually adjusted manually throughout the printing process. Different geometries require different deposition rates. Next steps for the project will require me to design a singular interface to run the machine. Therefore, I will be able to establish relationships between the parameters of filament speed, robot speed, torch temperature, and build chamber temperature.
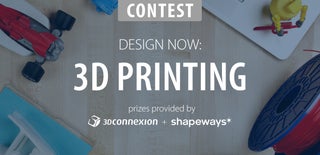
Participated in the
Design Now: 3D Design Contest 2016