Introduction: Hand Making a Grand Piano Action Model
Hi, I made a Grand piano action model for the "Make it Real Challenge" and "Woodworking challenge".
I just bought a spanking new 7'6" Shigeru Kawai SK7 and thought that a nice feature piece like this would be awesome to show guests and family how the piano works.
I did a search online and the thing costs around $150 for cheap ones and $500 for the more expensive brand ones. My piano dealer said it costs $600 to get one for my particular grand piano.
Since I am pretty much broke at the moment from buying the piano, I don't really want to spend much on this action model and decided to make it myself. The whole thing ended up to cost around $4.00~$5.00 because I already had most of the wood/parts hanging around in my garage.
The whole thing took around 6 days (thee weekends) to make. Probably not full days though, I worked on other stuff so probably effectively 4 days I guess. a lot of time, but I guess I saved a lot of money too =)
Anyway, here is a video:
Step 1: Understanding the Piano Action
I watched many videos, looked at photos to study how the piano transform a key press into the swinging of the hammer.
I found out it is a very interesting procedure. Here is one video: http://www.youtube.com/watch?v=01DBtig_Fgw (credits to: dberg001).
a good site for reference: http://www.musicplay.com/Musicplay/How_Pianos_Work.html
in a nutshell:
1. Player presses key
2A. key pushes the whippen assembly up, which is also pushing the hammer up via the jack. The whippen assembly (AFAIK) is the assembly of the jack, whippen and repetition leaver (Correct me if I am wrong).
2B. at the same time as 2A, the damper is lifted up through a series of levers.
3A. Jack hits the stopper; jack tilts left to lose contact with the hammer knuckle (the round thing on top of the jack) thus the hammer is no longer driven by the whippen. the whippen keeps going up until the key is fully depressed.
3B, Once the hammer is sent flying and the jack is disengaged, the repetition leaver hits the stopper, causing it to tilt down, allowing the hammer knuckle to lower, and allow the hammer to get caught on the "backcheck" to reduce bouncing of the hammer.
4. The player releases the key.
5. Whippen assembly lowers, springs pull the repetition leaver and jack to the initial position and the backcheck is lowered, releasing its grip on the hammer, allowing it to fall back to the resting position.
All of this can happen as fast as 12 times a second on a MIII Kawai, or as fast as the player can tap the key =)
(Source: http://www.pianoworld.com/forum/ubbthreads.php/topics/1175402/Kawai%20Mill%203%20action%20-%20Differen.html)
Note: if anything here is wrong, just tell me to edit. I am not a piano technician, I just studied the action model for a few hours and came to these conclusions during design and building and building.
Step 2: Creating a Model on CAD
I used Autodesk Inventor 2011 to model my action. it can be downloaded from www.autodesk.com for a 30 day trial (or a 3 year student licence, if you are a student).
This is probably the second most scariest part of the whole project. I had to take apart* my 2 week old $AU 115,000 (RRP of coarse) piano. If I messed it up, I would have been screwed. I was sweating and concentration level was up the roof so I wont ruin it. The keybed was really heavy, a lot heavier than my old grand piano (probably 3 times heavier).
*Apart meant to take the fall board off, take the two side wood bits off, the front wood bit off and slide the action keybed out.
Anyway, this step was so I could take measurements of the piano. I used my trusty calliper along with rulers, and drew a rough sketch on the sizes of each part. I then took photos of each part with a ruler next to it to it, just in case I need some dimensions but missed or forgot to write it down.
Also, I have not drawing everything that is required on CAD, I figured that it would be simple to get. I.e. screw threads and round wood sticks. if the floating assembly looks and makes no sense to you, jump to the intro or end to view photos of the final product and video.
putting the piano back together is probably the most scary part. the springs were really stiff compared to my old piano so I had to give it quite a push to stick the keybed back in. Tested it the piano for an hour just to make sure nothing is broken =)
Although I took reference to my piano for most of the measurements, It was mainly just to get an overall size of the assembly. I adopted some WNG designs as well as throwing some of my own design ideas up while thinking about how I'm supposed to make it.
The PDF of the model is attached on this step;
Attachments
Step 3: Building the Model
I was planning to get it 3D printed, but guess how much it is gonna cost? $385. I was thinking around $30~$40 to be acceptable price but almost $400? haha makes me laugh (and seriously to get a personal 3D printer).
I layed out all the parts into a 2D image, so I can use them as stencils for cutting. Cut the paper template as close as you can to the black line.I used standard glue sticks to stick the paper to the wood.
NOTE: that the PDF has some parts replicated, but shown in another angle. the parts should be very close together which means they are same parts, just a different projection.
I started by making a DIY router table. so I can shave some wood with precision. Instead of a normal router bit, I used a saw drill bit, so there is less kick back when trying to mill small pieces. the routers normally accept 1/4" bits. Metric bits wont fit as 6mm is too small and 6.5 is too big. Actually I used a 6mm bit, but had to wrap some electrical tape to beef up the diameter. it works really well (although would not recommend because it is a really dodgy method) . it only sees problems if you use for extended amount of time and the bit heats up and softens the tape. If I had a band saw or scroll saw, it probably would have been a lot better and cut (lol, pun) my time by maybe 3-4 hours to make these parts
I also had to change the design of my parts, I could not make the cool circles and holes because it would be too difficult with the equipments I have. so It is pretty much same, but a simpler look.
To make the knuckle, I got some round wood rods and cut it 1cm wide, sanded one side flat (approx 0.1mm) and drilled 2 holes 1mm wide and 5mm deep. I used some paper clip along with expoxy to make some studs. I drilled 0.5mm deep into the hammer shank and expoxyed the knuckle in. This makes it really strong. if there were no metal reinforcement, i reckon the joint will fail easily. see the final photo on this step for picture
Step 4: Assembling
I used some left over wood for the keybed (the base) and and some more left over wood for the side wall. I choose a dark wood for the wall because it gives contrast and it is easier to see the action parts.
I didn't make any CAD drawings for this part as it very simple to make and visualise. and plus, I didn't take the dimensions and I don't want to take apart the piano again.
The cantilever rectangle things (see second photo) are screwed on the side wall to support the parts and position them in the proper place. The exact location for these parts will never be the same in any hand made builds, so I gave up measuring. I just assembled as much as I could, then marked where the rectangle cantilever things will need to be placed, then drill and screw them in.
To make everything assembled without falling apart, I needed to make the stoppers work. I just drilled 3mm holes and fitted a fine threaded screw in reverse. Before fitting, I used my dremel and cut a slot at the end of the screw, forming a slot, so i can make easy adjustments (see picture 3 and 4)
Step 5: Making Some Springs
As mentioned in step 1, there are some springs in the model. The original designs are shown in picture 1 (I drew on MS paint where the spring loops).
This was a bit hard for me because I adopted the WNG jack stopper design (see photo 2, hover over text) mainly for good looks. This gets in the way of the original spring design unless i make some really awesome straight cuts between the jack stopper (picture 3), but this is really difficult for my wood hand-cut whippen (It would be really easy if it was 3D printed or some CNC machines).
I had to change my design slightly. I used coil springs which were sourced from clicky pens. Used a steel cutter and then shaped it do what I needed.
The modern spring designs from Kawai, yamaha, renner is a 1 piece spring, I don't know if one section of the spring will effect the other, but to me it looks like it does not matter if it is 2 springs or 1 large spring. The only thing the springs do are (with reference to photo 1)
1. keep pulling the jack towards the whippen (clockwise motion), and make sure it makes contact with the jack stopper.
2. keep pulling the repetition lever in a clockwise motion, and make sure it contacts with the stopper.
Actually, I tried torsion springs first but they failed miserably for me.
I had to make some hooks to hang the springs on each end of the parts. The hooks were made from paper clips haha. Just had to cut them and bend them to shape.
Drilled a 1mm hole in the positions required and used epoxy to fix them in place (see picture 5)
Have to remember that it is best to use these coil springs in tension, not compression. I found that the springs need some centre support if used in compression otherwise they will just buckle and distort.
Step 6: Making the Key
The key is surprisingly long. it measured to be approx 63cm long, 2.5cm wide. I didn't measure the depth but I assumed it according to the proportions of the key. in my case, the thickness is 2cm.
I first had to determine where to position the key. I did this by fully assembling the whippen and hammer. This makes the model actually function the basics (i,e, move the hammer up when press the key).
Measure how high the key needs to be off the keybed and mark with pencil. I made a triangle wood as the balance rail. I tried to keep the key as level as possible while in resting position. there is a large gap between the key and whippen. use a piece of scrap wood, just the size of the gap and slot it in between. now when the key is pressed, the action should work!
play with the key, change the distance between:
1. key and balance rail
2. key and whippen contact point.
Mark the best position down. a good postion is when the action fully works (i,e, all the stoppers are contacted when the key is fully pressed, the hammer has a good blow force, keys displace approx 1.7cm down (from the end of the key).
Now we need to fix the key to that position. we dont want the key sliding and moving around as it is pressed. to do this, we need two pins. A great way to get very stiff pins are from old drill bits. I mounted the drill bits in reverse on my drill press and polished the shaft. Then cut the bit to approx 4cm. I made a slightly smaller hole on the triangle balance rail and hammered the pin in.
I needed to drill a special hole on the key (see photo 4). The key needs to be able to rock forward and back. for this, you need a drill press. first drill a normal hole, where you marked as the 'best' position. Then adjust the stopper on your drill press such that it will never drill through your key, leave about 2-3mm. Start drilling another hole slightly closer to the whippen assembly than the previous hole. Need to claim the wood down or hole with a lot of pressure to make sure the drill press does not slip and go back to the original hole. I made a MS paint drawing to show more clearly (picture 5).
The same thing is done for the second pin. The pin is located on the head of the key. the only difference is that we cannot drill through the entire key. we have to limit maybe 2-3mm otherwise it would look ugly. (picture 6)
Finally, need to make a little cap, to stop the key from sliding out. The piece of wood is drilled one step smaller than the pin, then slightly expanded with a file. it is then push into the pin, making a very tight fit so it is removable, but will not fall out by itself (picture 7)
Note: I also drilled the pin on the balance rail a bit close to the right, as that is where all the pivot action occurs. the other side does nothing. I also cut some random felt hanging around my garage to dampen the wood-to-wood contact noise.
I had some left over white key tops (bought a set of 88, but only needed 85) so I used one for this project and one as a book mark =)
Step 7: Adding the Strings
I need to have the hammer hitting something so, to install some strings, I need to make a pinblock and a hitch pin.
The pinblock holds the pin, which holds the string. the hitch pin is just a super stiff pin which holds the string on the other end of the piano.
I wanted a wood that looks similar to what a pinblock wood looks like in a real piano. I went for some cheap laminated wood that were hanging around. its cool because you can see the layers, which gives it a pinblock look but it is quite weak, it hasnt broke yet, which is good, but if it does, I'll probably replace it with Jarrah.
I actually stole the pins from my old grand piano. the piano needs string replacement and new pins anyway so I just took them out.
I was being stingy on the pinblock wood. I should have made it much bigger to 1. support the tension of the string under high tension and 2. add space for 2 pins.
The tension of the string is really lousy at the moment, the sound it makes is not really great. I also realised that the hitch pin actually isolates the tension of each side of the string REALLY well. I need to tune both sides independently. If one side is fixed, it will stay floppy while the other side gets tight. There is no immediate slipping unless you hit the strings many times.
I really planned to install some agraffes (Steal them from my old grand) to align the strings, but It worked well with just some screws on the pinblock (picture 3 and 4). It does not look as good as brass agraffe, but works. I'll put agraffes in in my next build (when I get access to a 3D printer).
Step 8: Adding the Damper
The damper is the cloud looking thing. it sits above the strings. I used a V wedge damper because there are 2 strings. I have this damper felts hanging around from an old project.
It was unexpected, but I ran out of room for the dampers! initially, I was going to use steel rods, not strings, so I didnt need the hitch pin. Now that it is in, I had to move the dampers slightly forward. It looks a bit funny now, with a Z shape metal rod, where in most pianos, it is just a straight rod. I had to stop the damper from tilting while it was moving up. this was a small problem, fixed by shoving bluetak in the hole then inserting the metal rod through. it makes it adjustable still but much more resistant to turning while lifting.
I noticed that some piano makers use weights on hinge of the damper. I guess this is to put more pressure on the dampers and string (make it more effective at silencing the strings).
I probably wont add weights though, the strings pretty much has no sustain. if the damper gets sticky later on, I might add some weights so it can go up and down easier. I'll probably have to add some weights on the key side too, to counter act the weights on the dampers
Step 9: Felts
to reduce mechanical noise, add some felt between the point of contacts of the piano parts. I know the knuckle is supposed to be wrapped around some really awesome material that is strong and tough, while also has some cushionness to it to reduce noise. I didn't have that material so I just placed felt around the whole contacting area of the repetition lever. It kind of reduced the noise, but still a lot louder than normal pianos ( oh well).
Instead of felt, I should have tried foam for the hammer resting felt. it seems that it is that part that makes the most noise.
Step 10: Finished!!
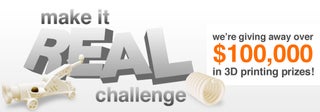
Participated in the
Make It Real Challenge
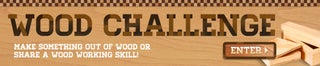
Participated in the
Woodworking Challenge