Introduction: Grill Drip Pan - Heavy Metal Edition
Stainless steel is a great corrosion resistant material, leading to its use in many barbecue grills. However, many of the "stainless steel" grills on the market only feature stainless steel on the prominent exterior surfaces (like my mid-range grill). Much of the interior metal and support pieces are made from regular steel and will rust out well before the shiny stainless steel surfaces. Even worse, these pieces are often made from light gauge steel (20 gauge or thinner) that simply doesn't last. One of the first pieces to rot through on my grill was the large drip pan under the cooking area. I couldn't bring myself to buy another light gauge replacement pan for $70, so I made my own out of heavy 16 gauge steel. This heavy duty piece will likely outlast the rest of the major components of the grill, and it gave me an excuse to play with a bunch of sheet metal fabrication tools.
I made this at TechShop www.techshop.ws
Step 1: Materials and Equipment
16 gauge sheet metal (approximately 24" x 24")
1/4" x 3" bar stock
High temperature grill paint
Hydraulic shear
Corner notcher
Turret punch
Sheet metal break
MIG welder
Angle grinder
Sandblaster
C Clamps
Hammer
(Okay, you can get by without a bunch of these but they sure made it easier)
Step 2: Mark and Cut Main Piece of Sheet Metal
Drip pans are normally made in a giant hydraulic press that forms a single piece of sheet metal into a shallow pan-like shape. I won't be making an exact replica, but rather a basic V-shaped pan from cut, folded, and welded sheet metal. The critical dimensions for my grill are the overall width of the pan and the size and shape of the tabs that hang the pan from the bottom of the grill.
My pan is 21.5" x 15.5" and I want to have 3/4" high sides, so I cut a 23" x 17" rectangular piece of sheet metal. I marked the fold lines 3/4" in on each side, as well as a fold line along the center of the metal. I also marked where the drip hole will be located along that center line.
Step 3: Punch a Drain Hole
Next I used a turret punch to make the 1.25" diameter drip hole (where the grease will drain through to a can hanging below).
Step 4: Notch the Corners and Center Fold Line
In order to make the folds, the excess material has to be removed from the ends of each fold location. I used a corner notcher to easily remove perfect squares from each corner and a V from the two sides.
Step 5: Make All of the Folds
A sheet metal brake is used to make nice straight folds. The folds must be made in the correct order or else the piece won't fit in the brake for the final folds. I started by folding the short tabs up 90 degrees. Next, I made the center line fold (that makes the primary V shape of the pan). This is a much shallower bend, and should be made so that the depth of the new pan matches that of the original pan. Finish by folding the last two tabs to 90 degrees.
Step 6: Cut and Fold End Brackets
This particular tray hangs from the bottom of the grill by two L-shaped end brackets. These brackets are 8.5" wide with a 1/2" lip. I used the hydraulic shear to cut out the two pieces (note the bottom portion matches the V-shape of the main tray). Two quick folds on the sheet metal brake and the brackets are done.
Step 7: Weld It All Together
The metal should be cleaned in preparation for welding (as well as for eventual painting). I sandblasted the entirety of all three pieces (and will re-sandblast any portions impacted by the welding). Clamp the first bracket onto the side of the pan with c clamps. MIG weld the seam between the bracket and the pan. I made sure to completely fill the gap so that grease can't leak out any small holes along the seam. Flip the pan around and do the same thing for the second bracket. Finally, weld the short seams along the four corners of the pan. I then used an angle grinder to smooth down the horrible looking welds that I made...
Step 8: Add a Hook
Left as is, the drip hole won't cleanly divert the grease into the hanging can. Using a hammer, I pounded the area around the drip hole from the top so that the pan slopes down to the hole. This doesn't have to be over a very large area, just immediately around the hole (perhaps a 1/2" back or so). I bent the short piece of bar stock into a hook and welded it to the bottom of the pan next to the drip hole. This is where I will hang a can to catch the drippings from cooking.
Step 9: High Temperature Paint
I made a final pass at sandblasting the welded areas in preparation for painting. Then, using a high temperature paint made for barbecues I carefully painted all of the surfaces of the drip pan. I applied two coats to slow down the eventual rusting of the pan (which should be enough to outlast the useful life of the grill).
Step 10: Start Grilling!
Time to install the drip pan, run the grill for a bit to burn off any fumes from the paint, and start grilling. Get out the steaks!
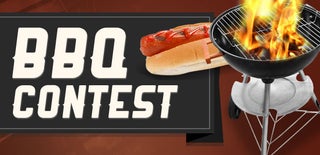
Participated in the
BBQ Contest

Participated in the
Craft Contest