Introduction: Homemade Christmas-Gift Key Fob
I'm going to show you how to make a key fob from leather scrap. These make great Christmas presents. First we need to gather our tools and a few supplies:
Tools:
- Rawhide (or Rubber) Mallet
- Utility Knife
- Scratch and Diamond Awl (interchangeable blades work great)
- Stamping tools
- Camouflage Tool
- Backgrounder
- Burnishing Tool
- Swivel Knife
- Modeling Spoon
- Paint Brushes
- Clean Cloths (Cut up T-shirts)
Supplies:
- Leather (Scrap or Cut offs will work if they are large enough)
- Waxed Thread
- Contact Cement
- Key Rings
- Leather Prep
- Neatsfoot Oil
- Saddle Soap
- Dye
- Accent Dye (Cova Kelly Green)
- Overall Dye (Antique Medium Brown)
- Clear Acrylic (Satin Sheen)
- Finish
- Mink Oil Paste (or other protectorate)
- Resolene
- Tan Kote
Step 1: Design the Fob
This step can take some time and thought. First, figure out what shape you want to use, I used a round pointed shape and decided I wanted the leather to face both sides. The fob can just be one sided with a rivet at the top to hold on the ring. This will, however, leave the rough side of the leather exposed and does not look as finished as a duel sided fob. I'm going to put initials on my fobs as well to add a personal touch so I need each side for the initial. Attached is the pattern I used to make my fobs so you can use them or design your own shape. There are three sizes in the drawing so you can see which fits the best for you. I used the middle one as it was large enough for my initial to fit onto but not to large so it will fit in a pocket nicely.
Try different designs and once you are happy with one print it on paper first and make sure it folds correctly and is the right size. You can also fit the paper model with one of the key rings to make sure it fits well before cutting leather. Make sure you are happy with everything before moving on to cutting the leather. Print out the final pattern and cut it out of the paper use this as a template for the first cutout.
Attachments
Step 2: Cutting Out the Leather
Place the template onto a section of the leather that is free of any marks or scars. Use the scratch awl to scratch the outline onto the leather. If you do not have a scratch awl no problem, use a pen to mark the pattern but do not mark on the smooth side. Instead, mark the pattern on the back of the leather which is the flesh side.
Once the pattern is marked out, cut out the pattern with the utility knife. There are a couple of tricks to this that can make the process easier and give you better results. First, don't try to cut all the way though in the first go. Instead, score the pattern first and then repeat the score until you get all the way though the leather. Second, make sure that the knife is always straight up and down. Do not let the knife lean to one side or the other or you will have an angled edge instead of a square edge. If it does angle, either from leaning or too much pressure on the blade, then score off the over lap til it is square.
After the entire fob is cut out, fold it over and make sure both sides are pretty close to the same. If they are not then trim off the excess. Once it is evened up make sure it is still close to the original pattern. If everything looks OK then you have the first piece.
If you are making more than one then use the first cut piece as the pattern for marking the rest. It is much easier to trace around or scratch around than the paper pattern.
Depending on what leather you cut the pieces from, you may have some odd bending or curling. This is pretty simple to fix. Just wet the leather slightly on the front and back with a sponge and place under a heavy, flat object. I used a couple text books I had lying around on the table. make sure there isn't anything on the books or table that might press into the leather as it will leave a permanent mark. Text book are usually smooth and glossy so they are perfect. Leave the leather for a few hours to dry and they will be perfectly straight.
Step 3: Stitching and Decorative Groove
The next step is not entirely necessary, but will add a nice look to the leather and a channel for the stitches to set into. Also, the groove will create a boarder giving a clearly defined space for the tooling.
Use a scrap piece of leather to practice and figure out how far the groove should set from the edge of the leather. I set mine at 1/8". Once you are happy with the look, run the groover around the entire edge of the project to make a stitch channel and a decorative groove over the middle.
Start at the tip about an 1/8" from the end. If you start to close then the groove will overlap instead of meeting up. Its better to start a little further way and com back to make the lines meet than have them overlap. Run the groover down the side until you get to the other side, stopping before the end to make sure the line will not overlap. Run the groover down the other side the same way. You may need to run the groover over the same groove several times to get a nice looking groove, you want it be deep enough for the thread to sit into. Make sure to go back and make the lines meet up evenly so it looks like there is one continuous line all the way around.
Step 4: Transferring the Pattern
There are lots of patterns and designs that you can use to make a unique and interesting gift. Get creative and make something that will be neat and personalized for this gift.
I decided to put an initial of the recipient on each side of the fob. Since I'm making several of these and I wanted them to look neat and consistent I used a craftaid, which you can get here. These are sheets of plastic with a design embossed on one side. This makes it super easy to transfer the pattern and get very consistent results. This was especially important to me because many of the initials were the same letter.
To use the craftaid just dampen the leather and wait til it starts to return to its normal shade. This is the water soaking into the leather and not it drying out. If you try to start to soon the impression will not be clear or stay. Pick the placement of the letter, this is easy since the craftaid is clear, and press the craft aid into the leather. Take your modeling spoon and rub all the edges of the letter into the leather with a good amount of pressure. Lift the aid off and make sure it gave a good enough impression if not you'll need to try to place the aid back down and rub some more.
The impression will not be very dark but should give enough detail to see while you cut out the design.
Step 5: Tooling the Design
Once the pattern is transferred cut all the lines out with the swivel knife. Make sure the leather is still damp enough to be pliable and that the knife is sharp. Strop the blade by rubbing some jewelers rouge into a scrap piece of leather and run the blade down the leather at about a 25 degree angle. If you notice the knife dragging then strop it, making sure to maintain the correct angle. If it is still hard to cut then try dampening the leather again because it may be to dry. Also, keep the knife angled into the cut by tilting the knife back into the blade, keep the knife straight up and down from the leather so it does not angle into the sides of your cut. If you lean the knife it will cut under the top layer and make it difficult to bevel or cause a number of other issues.
Once cut, bevel all the outside lines. Anything that is not the actual letter should be beveled down so the letter stands out from the background. You can use a beveling tool and the mallet but it is much easier and faster to use the modeling spoon to push the bevel into the leather. Just slide it down the line with the curve to the outside of the line you want to bevel.
After all the lines are beveled you can add the stamping. I created a circular boarder by using the camouflage tool and stamping it all the way around the letter. make sure to lean the tool away from the letter so it does not imprint on the letter itself. All you are really trying to get is the semicircular pattern from the heel of the tool. After each stamp just place the opposite corner of the tool in the mark you just made and angle it a little each time to make a circle. If this is the first time you have used stamps then practice on a scrap piece of the leather first!
Now that there is a boarder we can use the background stamp to stamp down the leather around the letter. This will make the letter stand out more and give a nice dark color to the leather once its dyed. Be careful in the tight areas of the inside of the letters so you don't make marks on the letter itself. Just lean the tool away from the letter and stamp lightly so it is not knocked into the letter. Work the entire inside of the letter and around the outside, then stamp with less pressure as you approach the boarder to make the background "fade" into the boarder. If you need to use the camouflage tool again to cover any back grounding that is too close to the boarder.
Step 6: Prep for Dying
Since the leather used might not be the best (I used a couple straps that came in a bag of scrape). We need to prep the leather for dying. The first thing we should do is use the saddle soap to clean the leather. Just take some saddle soap on a clean cloth and rub it into the leather. You do not need water or to get the "soap" off of the leather, It is actually glycerin and helps to condition as well as clean and is left on the leather. It will darken the leather slightly.
Next, we want to apply a light coat of Neatsfoot oil to the leather. This will make the leather more supple and will help moisturize the leather if it is dried out (which it probably is). The main problem here is that you do not want to add too much since it is a penetrating oil and will make the leather soggy or floppy if you use to much. So apply a small amount to a clean cloth and rub it into the leather. It might look splotchy at first but that is ok. It will even itself out as it soaks in. Leave it alone for awhile and come back after no less than an hour. If it is still to stiff or dry feeling add some more the same way. Once it feels the way you want don't add any more oil. Let it dry for at least a couple hours before starting the dyeing process.
Step 7: Dyeing
This project will have a two step dying process. The first is to dye the detail and cover in a clear acrylic then dye the whole piece.
Dye Detail
To dye the detail use a small brush and paint the dye onto the detail. I used a bright green (Cova Color Kelly Green) to make the initial pop. The Cova Color is a thick paint like dye that is really easy to use for detail like this. You can also use regular dye but you need to be very careful as you paint that the brush is not over loaded and you do not get into the cuts to quickly. If you do the dye will quickly spread into areas where you don't want it. With the Cova it's thick enough that it is easy to control and you don't have to worry to much about it jumping into other areas.
Once the detail is dyed let it dry and make sure it is nice and smooth, if not put on another coat. Once it is dry apply a clear coat of Super Sheen, Satin Sheen or Block Out. Any of these will work and just add a slightly different finish to the detail. This is used to resist the dye used in the next step, if you do not use the clear the dye will most likely cover the dye placed now. make sure it is dry before moving on to the next step.
Dye Full Project
Next, we will dye the entire project a base color. I chose to dye the fob with Gel Antique Medium Brown. I think it makes a nice contrast and I had it already. Since this is a smaller project use a wool dauber or a small cut off of wool to apply the dye. Get a generous amount of the gel on the dauber and rub it onto the leather in a circular motion. Just do one side at a time. Use a piece of paper towel folded over as a pad to wipe of the excess. If you want the dye to be lighter wet the leather before applying the dye or wet the towel before rubbing the dye off. You may want to experiment on a scrape piece before committing to a method on the project. Dye both ends of the project and then dye the middle of the back. This is the only part of the backing that might be visible since the key ring will travel though this area. Don't worry to much about the edges at this time, we will touch them back up after burnishing and sewing.
Finish
Before moving on we need to apply a finish to protect the leather and seal in the dye so it will not bleed. There are several possible finishes that can be use in leather and there are lots of different opinions and reason for them. There is a great Youtube video here that compares some of them, 40 mins long. I use saddle soap, mink oil which is a protectorate and Resolene which is an acrylic waterproofing agent.
First rub the whole project down with saddle soap again to get any floating dye off. You will probably see some of the dye come off on the rag, don't worry there is always some dye that is left on the surface. Next rub on some mink oil paste and let it sit for a few minutes to soak in, then buff it off with a dry cloth. Last paint on the Resolene with a broad brush. Make sure to get it into all the tooling impressions and cuts. Lastly you can use Resolene or another product called Tan Kote on the back to seal the dye that is there and seal up the leather. I prefer Tan Kote because it is not water proof and leaves the back able to breath some. This helps keep the leather from drying out as it ages. Leave everything to dry overnight.
Step 8: Edge Prep
To prepare the edges we will do two things, Bevel and Burnish. This step can be done before or after dying. I actually did it between the detail and final dying.
Bevel
Bevelling the edge will make the edge have a nice curve instead of being square, this is more aesthetically pleasing and will make the fob feel nicer in the hand. To bevel take the edge beveller and hold it at a 45 degree angle on the corner. With a smooth motion push the edger away from you down the edge following the curves. If it falls off as you go just start a little way back from where it ended and push through. Do one side and then the other and just run off the end. This essentially cuts off the corner of the edge leaving a 45 degree angle along the top of the edge. It should not go all the way though, if it does than the edger is to large for the thickness of leather that is being used.
Burnish
Burnishing is used to smooth and harden the edge of leather. This can be the most time consuming and picky part of any leather project but doing a good job here is what makes a project look professional or amateur. There are many different methods of burnishing but really all you need is a slicking agent (Water, Spit, Gum Tragacanth, Glycerin, etc), and friction (elbow grease). I use yellow cake saddle soap and it seems to work better than just water or spit and gum trag is reported to not work well enough for me to have bought any. The saddle soap seems to work pretty well and it doesn't block dye. Make sure to use the paste form and not the liquid spray as it is to difficult to control. Take some saddle soap on a cloth and rub it briskly into the edge, make sure you have plenty of soap on the cloth. You can also use a wooden burnisher which can really help to shape the edge as well as slick the edge. Fold the fob in half and line up the edges like they will be when sewn. Use the area of the burnisher that fits the thickness of the two layers of leather. You can also use the straight part of the burnisher on the very edge to mold the two parts together and get a slightly straighter edge. The edge will start to darken and get shiny. This is not the final burnish so don't worry if the edges are not perfect yet. Do pay special attention to the area that folds over though since once it has the key ring installed it will be very difficult to get into to burnish.
Step 9: Sew
The step is only necessary if the design is mirrored. If you just have a strap and one side instead use a rivet to close on the key ring, it's much quicker but not as finished looking.
Mark the Holes
First, wet the stitching groove with a paint brush and water. Take your stitching wheel and make sure the appropriate wheel is loaded in it. I used a 5 SPI (stitches per inch) wheel. On a small project you can use a smaller wheel but make sure it is not too small for the thread that will be used. Once the stitches are marked fold the project is half again and clamp it using a spring clamp. Make sure to protect the project by putting some scrap leather in-between the project and the clamp on both sides. This is just to hold together so it does not slip as you move it. You could go ahead and install the key ring and glue at this point but it makes it much more difficult to keep it on the push board.
Punch the Holes
Use the diamond shaped awl to push out the holes at each mark. Make sure that the awl is straight as it is pushed though and that it comes out the other side in the stitch groove. This can take some practice but is not as hard as it sounds if you take your time. Once all the holes are punched turn the piece over and push the awl into the holes on the other side to get a good diamond shape and push the leather to the middle.
Glue
Now install the key ring and glue the sides together with contact cement. Brush each side with the cement and let it sit for a few minutes until it gets tacky or almost dry. Very carefully line up the sides and lightly stick them together. If you press to hard and mess up it is very difficult to separate. Once it is lined up correctly press hard and use the mallet with a scrap as a buffer to tap the piece all over. This sets the glue and makes it nearly impossible to get apart.
Saddle Stitch
Now we will saddle stitch all the way around. Saddle stitching is fairly simple but here is a great detail video explaining it, 1hr 30min. In short lock two needles on to a thread that is about 6 times longer than the length you will sew, the multiple varies with the thickness of the leather but thread is cheap so use more than you think you need to be safe. In the second (or third) hole, insert one of the needles and pull through til to the middle of the thread. Start by back stitching to the first hole, insert the "front" needle and pull through most of the way, then insert the "back" needle and pull though making sure not to pierce the thread. Once at the first hole stitch back though the same holes and keep going to the finish. Always start with the "front" and then the "back" this will be the other needle each time as they switch places. To make the stitch neat also try and put the front needle in the same part of the hole each time and the back as well. For example, the front should always going in the bottom and closest part of the hole and the back should always go in the top and farthest part of the hole. This will give the stitch an even look and help reduce the chance of the back needle piercing the thread. At the end, back stitch a few holes to lock the thread, just stitch back one or two hole, what ever you did at the beginning to make it look even. You may need to use a pair of pliers to help get the needle though when back stitching as the hole will be very tight. Make sure that you end with the "front" needle in the back as well. That way all the loose threads are on one side. Cut the thread close to the hole so it does not stick out, but make sure not to hit the leather with the knife or it will mar it. Then take a lighter and heat it up and touch it to the thread ends. Most modern waxed thread is acrylic so this will melt the ends and keep it from unraveling it should also shrink so its not as visible.
Finish
Once sewing is finished take the mallet and lightly tap the thread down so they sit into the groove nicely, use some scrap as a buffer if needed. Then take the stitching wheel that was use to mark the holes and run it over the thread, this will give the threads a nice contoured look instead of being flat.
Step 10: Finish
Now the project looks done, but there are just a few things that you want to do to really finish it off.
Burnish
First, burnish the edges again. If the two sides did not meet up very well or there is glue coming out of the middle you can take sandpaper and sand the edges down. Start with a 200 grit and work through the grits to 400 or so and a sanding block is a great help. This will make the edges very smooth. Then take some saddle soap to the edge again with the cloth and use the wood slicker to shape the edge if needed, the cloth should be sufficient at this point. Usually, a well burnished edge will be dark and shinny on its own and not necessarily need to be dyed, it also naturally protects the leather and is resistant to water and abuse.
Touch up Dye
Touch up the dying on the edge and anywhere else if needed. The detail is should be set at this point but I had a couple that flaked for some reason, also there may be some scuffs near the edge where sanding happened or from the clamps. Touch up the detail with the same green dye and add a clear coat of Satin Sheen before adding more Resolene. Touch up the rest, by applying more dye with the dauber; buff off with the paper towel and let dry. If you dye then you also need to apply finishes again to protect the newly dyed area. Apply as in step 7 and buff off. Make sure to give a few days to dry completely before using or giving as a gift! Buffing should bring out a natural shinny surface.
Notes
Thank you for reading my 'ible. Please let me know what you think in the comments, this is my first published 'ible and I have a much larger project I'm working on now and should be published soon. It will be my real first but this is a good test run. Please also vote for me if you enjoyed this and think it would make a great gift! I am making 12 of these for my family for Christmas this year so I hope they like them anyway!
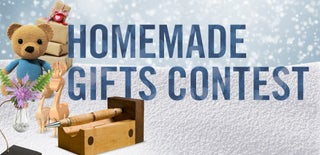
Participated in the
Homemade Gifts Contest