Introduction: How to Build a Spark Gap Tesla Coil (SGTC)
The key to this coil's performance on such a tight budget is that all of its components are designed to work well together. Using some basic concepts from AC circuit design, the components are matched to perform well without requiring massive amounts of power. Some "coilers" use microwave oven transformers to pump kilowatts of energy through poorly matched circuits, resulting in large losses and mediocre performance. This instructable will show you how to avoid making such mistakes and how to properly design a spark gap Tesla coil.
UPDATE: This Tesla coil is now on sale on eBay for a starting bid of $99.99, less than the cost of the materials! http://www.ebay.com/itm/250-000-Volt-TESLA-COIL-Assembled-2-Foot-Tall-8-12-Sparks-/180826521311?pt=LH_DefaultDomain_0&hash=item2a1a19bedf
For contest entry details on this instructable, see step 10.
UPDATE: New diagrams for primary capacitor, primary coil, and spark gap construction have been added. Click the top left information icon to view them in full size.
Featured on Hacked Gadgets!
Please don't forget to rate!
(I named it the "Valentine's Day Tesla Coil" in this video because I finished it over Valentine's Day weekend 2011)
To read more about this project, visit my website: http://xellers.wordpress.com/tesla-coils/sgtc-ii/
Step 1: Theory and Warnings
Although I don't want to spend too much time talking about exactly how a Tesla Coil works, I think that a rudimentary description is worthwhile given the amount of misinformation that exists on Instructables and elsewhere on the web.
Essentially, a Tesla Coil is a type of alternating current transformer that operates almost like any other (transformers are found in many electrical and electronic devices and are used to step up or step down the voltage of an alternating current signal). However, it relies on the principle of electrical resonance in order to massively increase the voltage of the alternating current signal.
One comment misconception is that the primary circuit (capacitor and inductor) "amplify" the signal from the high voltage transformer and that the ratio of turns between the primary and secondary coil is then used to create a high voltage. However, this is not quite the case.
During each alternating current half-cycle, the transformer charges the primary capacitor until the voltage across it exceeds the breakdown voltage of the spark gap. At this point, the capacitor and primary coil are connected and momentarily form a series LC circuit. Because the capacitor has an initial charge from the transformer, the LC circuit will oscillate much like a stretched spring will move back and forth once it is released. In fact, the differential equation describing a stretched spring moving back and forth with friction is virtually identical to the one that describes an LC circuit with an initial charge on the capacitor oscillating with stray resistance in the wires of the circuit.
These oscillations can exhibit three different types of forms: overdamped, critically damped, and underdamped (second image). In the overdamped condition (high damping factor, ζ), the current decays without crossing zero, while in the underdamped condition (low damping factor), it crosses zero many times and oscillates before decaying. This last condition is the one we hope to achieve in our coil.
Once the circuit is oscillating, the rising and falling magnetic field around the primary coil will induce current into the secondary coil. The goal is to maximize energy transfer between the primary and secondary coil and minimize energy lost to heating as a result of stray resistance.
The secondary circuit also acts as an RLC network. Its impedance, or resistance to an alternating current, will change as a function of the frequency that the primary circuit oscillates at. The third picture shows this relationship. If the frequency of the primary circuit matches that of the secondary circuit, then the amplitude of the secondary voltage will increase dramatically because the secondary impedance will be very low. Once the oscillations in the primary circuit have decayed, the transformer will switch polarity and recharge the capacitor, causing the cycle to repeat. This is similar to what happens when you try to force a sping to move back and forth; if you're not at the correct frequency, then it resists your push, but if you do manage to hit the right frequency, then even a small application of force can quickly increase the amplitude of its oscillations.
If you want a more mathematically rigorous explanation, be sure to take a look at this paper: http://tayloredge.com/reference/Machines/TeslaCoil.pdf There's actually quite a bit more going on than I made it sound like, so consider taking a look even if you're going to skip the mathematics.
SAFETY WARNINGS (READ THESE):
That said, I want to give a few warnings to anyone who is considering this project. Tesla coils and other high voltage devices are extremely dangerous in the wrong hands and can easily injure or kill anyone who does not practice proper high voltage safety. I am not responsible for any accidents that may occur as a result of these instructions.
I also do not guarantee that your coil will work or that you will be satisfied with the results. Only attempt this project if you are willing to face failure on your first attempt and don't cut corners - if that capacitor has to be rated to a certain voltage or that wire has to be enameled, don't try to get an inferior product for less. It's better to wait and save up for the higher quality part than to end up with a pile of cheap, burnt out components.
Be sure to read the entire instructable and completely understand what you will have to do before attempting this project!
Step 2: Gather Materials
The materials that you will need for this project should cost you no more than $200 and you can easily spend less than $100 if you invest some time into searching for good deals. Here is how I distributed my money:
Electrical Parts:
$35 - (1) 9kV 30mA Neon Sign Transformer
$35 - (100) 1.5kV 0.01uF Polypropylene Film/Foil Capacitors (the type of capacitor, in addition to it's value, is critical)
$5 - (100) 10M 1/2W Resistors (I actually bought 200, but didn't use half of them)
$20 - 680 Feet of 23 AWG Enameled Wire
Hardware Parts:
$15 - Wood from Home Depot - I cut a large piece into (2) 13" x 16" x 3/4" pieces for the base
$3 - 20" Long 3.5" Diameter PVC pipe for the secondary coil former
$2 - (1) 2' long 1" diameter PVC pipe for the primary coil former
$2 - (8) Nuts and bolts to hold the primary formers down - I used #8-32 x 1 - 1/4" Machine Screws
$0 - Primary Coil Wire - I used some relatively thick insulated wire I found at a recycling center, one could easily use flexible copper tubing or thick speaker wire for this purpose
$0 - (1) 1' by 1' piece of acrylic - I had some extra pieces from a laser project, but any moderately-sized sheet of plastic will do
$0 - (2) Metal objects to form a spark gap - I used a pair thick nuts and bolts for this
$3 - (1) 6" Styrofoam ball for the topload former
$0 - Aluminum foil to cover the topload
$0 - Spray-on Polyurethane Varnish or Shellac
TOTAL COST: $120
Coil Specs.
Power Supply: 9kV 30mA NST (270W)
Primary Capacitor: 10nF 15kV MMC
Spark Gap: Single static gap made from a bolt and a washer
Primary Coil: Flat spiral coil made from 9 turns of 10AWG wire tapped every quarter turn with 0.25" spacing
Secondary Coil: 3.5" by 18" winding of 23AWG enameled wire
Topload: 6" Styrofoam sphere covered in aluminum foil
Max. Spark Length: 14" to ground, 11" to air
Step 3: Build the Primary Capacitor
Because most neon sign transformers do not have the same output voltage/current ratings, each transformer transfers different amounts of energy into the primary capacitor during each operating cycle. Since we want the capacitor to charge and discharge completely during each cycle, this implies that it must be "matched" to the transformer's output characteristics in order to maximize the coil's performance.
To do this, we set the output impedance of the transformer equal to the reactance of the capacitor:
Xc = 1/(2πfC)
XT = E/I
Therefore, if Xc = XT , then
C = 1/(2πfXT)
where f is the frequency that the capacitor is being charged at (the mains frequency); this is standardized to 60Hz in the United States.
For my particular transformer, a 9kV 30mA NST, the optimal capacitor value was calculated as follows:
C = 1/(2π*60Hz*9000V/0.030A) = 8.8nF
Here is a convenient online calculator that automates this procedure: http://deepfriedneon.com/tesla_frame6.html (select "Capacitor to Transformer Match")
In reality, however, it is undesirable to use a perfectly matched capacitor because if the spark gap fails to fire, then the "resonant rise" of voltage across the capacitor and transformer will almost certainly lead to a transformer breakdown. You can read more about this here: http://www.richieburnett.co.uk/resonant.html
I chose to use a slightly larger than resonant capacitor value of 10nF in my coil. It's better to have some extra capacitance than it is to have a bit too little because this way, some of the energy storage capacity of the capacitor is wasted, while in the latter case, some of the energy from the transformer is wasted.
Next, in order to calculate the necessary voltage rating of the primary capacitor, we find the peak AC voltage of the transformer. Because Vpeak = 1.4 * VRMS , the peak voltage for my transformer is 1.4 * 9000V = 12600V. Since we don't want to run the capacitor right at its maximum allowed voltage, we usually add several kilovolts of headroom. Ideally, the capacitor should be rated to twice the RMS voltage of the transformer. I decided to build a capacitor rated for 15kV due to financial considerations. With my 10nF 1.5kV capacitors, this works out to 10 strings of 10 series capacitors, giving me exactly 10nF at 15kV, perfect! (DeepFriedNeon also has an MMC calculator that you can use to find the best primary capacitor configuration)
Finally, each capacitor should have a 10 megaohm resistor in parallel with it so that the bank does not stay charged once the coil is turned off.
Physical construction of the capacitor bank is not very critical. I used a square of plexiglass that I drilled with 200 holes to mount the capacitors and resistors (see first picture). However, to make things easier, I drew a diagram (image 2) that explains how I drilled the board and mounted the components. View the full size image for better readability.
Step 4: Wind the Primary Coil
Together with the primary capacitor, the primary coil makes up the LC resonator that drives the secondary coil. Because we want to transfer the energy in the primary circuit to the secondary circuit over several RF cycles, allowing the primary circuit to resonate, the coupling between the two coils is relatively low. This is why many spark gap coil primary coils are flat wound (this is not the case in solid state coils where the goal is to switch as much energy into the secondary circuit as possible with each cycle).
At this stage, you can use DeepFriedNeon's LC frequency and secondary coil calculators in order to find a combination that suits your components or you can use ScanTesla in order to "scan" for the configuration that will maximize the coil's perormance, however, I will not cover these approaches here. I think that I have found a primary/secondary combination that works reasonably well and if this is your first coil, I would advise you to follow what I did before you experiment on your own.
For my primary coil, I used a flat spiral made of 9 turns of thick stranded wire with 0.25" spacing tapped every quarter turn for tuning. If you can afford to use a flexible copper tube, then I recommend you do so because it is easier to tune and work with than insulated wire.
I used 4 supports made of 1" by 6" PVC pipe bolted down to the wooden base. Here is how I marked and drilled them to support the primary coil: http://www.loneoceans.com/labs/teslacoil2/sep9_pridesign.gif (with 5 tubes instead of 7 and 0.25" spacing instead of 0.5")
While you should wind the primary coil as neatly as you can, my coil worked fine even though the stranded wire didn't form a perfect spiral. See picture 5 for a diagram:
Step 5: Build the Spark Gap
While a well-quenched multiple segment spark gap is desirable for this type of coil, two bolts held about half an inch apart will do just fine at first. My spark gap use one L bracket and two nuts on one side to secure a bolt that can be used to adjust the distance of the gap and another L bracket with a nut and bolt to secure a washer on the other side that can be rotated "reset" the gap after it corrodes with use. This is particularly useful in long demonstrations where the corrosion on the bolt and washer can eventually reduce the performance of the coil. See pictures 3 and 4 for building instructions for this type of spark gap.
Another popular type of gap known as an "RQ mutliple gap" uses several copper tubes bolted in a circle inside of a PVC pipe with a fan at one end for cooling and quenching. It can be adjusted by tapping the gap after different numbers of tubes to alter the total arc distance. This is the type of gap that I hope to construct sometime in the future. Here is a helpful diagram: http://www.capturedlightning.org/hot-streamer/stk/tc/cylndr.gif
Pro Tip: Don't stare at the spark gap during operation. It produces dangerous amounts of ultraviolet light that can damage your eyes. Seeing as there is no need to operate this coil for more than a few minutes at a time, it won't need to be covered, but it can still be dangerous if you look directly at it.
Step 6: Wind the Secondary Coil
Winding the secondary coil is probably the most tedious part of this exercise, however, the 23 AWG secondary wire that I used in the coil is thick enough that it should not cross over windings without you noticing or rip if pulled too hard. All you have to do to wind the secondary coil is tape the wire down about an inch from one end of the 3.5" diameter PVC tube and spin the tube so that you get an even and tight winding from one end of the tube to the other (see second picture).
If you are using 680 ft. of wire, a standard size you can buy on eBay, then all you have to do is keep winding until it runs out. This should give you a winding with about 18 inches of length. Cut the tube about 1 inch above the end of the secondary winding and leave several inches of wire at each end to make connections.
Once the wire is wound and taped at each end, apply a few heavy layers of spray-on polyurethane varnish or shellac to make sure it doesn't break or unwind.
Important: some websites may tell you to drill holes at each end of the secondary to thread the wire through so that it is more secure. While this may work for a smaller coil with a long secondary winding, it is generally considered bad practice as it leads to arcing inside of the PVC tube in more powerful coils and will cause permanent damage (ie. burns and carbon trails inside of the tube) that will render the secondary unusable. Varnish and a piece of masking tape should easily be enough to keep the secondary coil from unwinding.
Also, recently, I have found that I am getting roughly the same performance from a 14" winding of 28AWG wire on 2.5" PVC pipe as from my previous 18" winding of 23AWG wire on 3.5" pipe, but it looks more impressive because the sparks are larger with respect to the secondary coil. In fact, because it uses less materials, you might want to start with the smaller secondary if your budget is limited. I encourage you to experiment!
Fatter, shorter secondaries tend to work better to a certain extent, but if they are too short, then problems with primary - secondary arcing can arise. One common error that Tesla coil builders often make is to wind a very long and thin secondary coil. The misconception that these secondaries would give better results was started in the early to mid-20th century by hobbyist magazines that featured diagrams like this one: http://amasci.com/graphics/tcoil1.gif.
Step 7: Make the Topload
The topload is easily the simplest part of this project. I used a 6" Styrofoam ball from A.C. Moore covered in aluminum foil with a piece of wire taped to the top for a breakout point. It isn't pretty, but it works well. Alternately, you could spend several dozen dollars on a machined aluminum toroid on eBay. This should increase the performance significantly (if you buy the right size), but I haven't had the change to try it out due to financial limitations. A small volleyball or soccer ball wrapped in foil also works if you can't find any Styrofoam.
An alternate method of making simple toploads is to use conductive spray paint to coat a spherical object like a lightbulb. I have not tried this yet, but it should give better results than anything you can make with aluminum foil. Here is an example of this approach: https://www.instructables.com/id/Van-De-Graaff-Electrostatic-High-Voltage-Generator/
Remember, the Tesla coil I describe is relatively small and adding a huge topload made of aluminum ducting will not increase the spark length. The key is to get just the right sized topload, large enough that there are no problems with multiple breakout or coronal discharges at the top of the secondary windings and small enough that it doesn't decrease performance.
Picture 1 is of the 6" sphere sitting on top of the 3.5" secondary and picture 2 is of the same topload sitting on the 2.5" secondary.
Step 8: Make Connections
At this point, all of the electrical components have been assembled and all that remains is to connect them together and mount them on a base. I chose to use two 1' by 1' wooden boards nutted and bolted together with 0.25" nuts and bolts to make a small box to screw or nut/bolt everything into. Have plenty of nuts and bolts, they're cheap and they come in handy when you're assembling the base!
Once the parts are mounted, use 10AWG or thicker insulated wire to connect everything correctly (see schematic). If this seems too confusing, then perhaps you should try a simpler electronic project first to familiarize yourself with reading and following electrical schematics. Make sure you keep the connections as short and tight as you can to minimize stray inductance and resistance that can hurt your coil's performance. Specialized high voltage wiring is not necessary unless you plan on sticking your fingers into the coil while its operating (bad idea!).
While you can use alligator clips to test everything before you mount it, be aware that the performance of the coil will decrease and you risk destroying your clips due to overheating. I melted multiple alligator clips this way - they often fail where the wire is soldered to the clip and can usually be fixed by resoldering the two together.
If you are building a significantly more powerful Tesla coil than I did, it may not be the best idea to use wood in your design. Wood is not an insulator at high voltages and on a humid day, you might find that your primary circuit will arc through the wood and start a fire. At the very least, do not mount any electrical components directly onto the wooden base, use plexiglass, acrylic, or plastic or ceramic insulators wherever possible. This is not a concern unless you are pumping a kilowatt or more into your coil. (A 9kV 30mA NST only draws about 270W).
Step 9: Fire It Up!
Remember that the first time you turn the coil on, chances are that it will be completely out of tune and will not make large sparks. Be patient and slowly adjust the primary tap until the sparks reach their maximum length. The "sweet spot" in my coil is only about half a turn wide and it took about half an hour of tuning to find. Be patient!
Once the coil is in tune, it will also be necessary to adjust the spark gap. While you are tuning, it should be set to 1/8" or 1/4" separation (if you are using a single gap). Then, once the coil is in tune, slowly increase the length of the gap. The goal is to keep it as wide as possible, thus allowing more energy to be stored in the capacitor before the gap fires, while still firing regularly at 120Hz. If the gap doesn't fire regularly or doesn't fire at all, then there is either too much corrosion or the separation is too wide, or both.
If you are using a very smooth polished aluminum toroid or sphere as your topload, then the coil might break out on its own at one point and no breakout point will be required. However, if you are using a topload made with aluminum foil, then the coil will probably break out in multiple places, reducing the overall spark length. To combat this problem, you can tape a short piece of wire to the top or side of the topload so that the output is concentrated there.
I have found that if the breakout point is too short, then there will still be multiple sparks across the topload, so make sure that it's a few inches long and very sharp at the end. The breakout point concentrates the sparks to one point because the sharp end of the wire creates a larger electric field gradient and promotes breakout there more than anywhere else on the topload.
If you still have problems with multiple breakouts or coronal discharges at the top of the secondary windings, then you need a larger topload. On the other hands, if you think your sparks are too small, then try using a smaller one. The key is to experiment.
Good luck and have fun!
To read more about this project, visit my website: http://xellers.wordpress.com/tesla-coils/sgtc-ii/
This is what first light looked like for me:
Step 10: Contest Entries
Don't worry, this is not a construction step! This is where I will justify why I have entered this instructable into various contests:
1. Space Contest
If bolts of lightning shooting into the air aren't already sci-fi enough, see picture 1!
Result: Winner!
2. USB Contest
See picture 2 to better understand how my Tesla coil "interfaces" with various devices via USB.
Result: Finalist!
3. 2nd Annual Krylon Contest
Apart from the secondary coils being painted with spray-on varnish, the background in the space contest photo is a piece of cardboard spray-painted black to make the sparks more visible - I use it all the time in my Tesla coil photography.
Result: None.
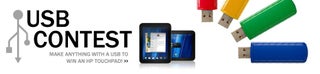
Finalist in the
USB Contest

Runner Up in the
Celestron Space Challenge
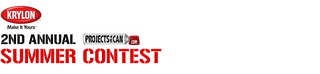
Participated in the
2nd Annual Krylon Summer Contest