Introduction: How to Sand Cast 3D Printed Objects
As anyone with access to a 3D printer knows, it's relatively easy to print off custom designs from the printer in a few minutes or hours. However, many people come up short in how to translate these fragile plastic pieces into actual working parts on a budget. This instructable is courtesy of our friend, Evan Daniel, who teaches metal pouring at Techshop RD. All credit for an awesome Saturday goes to him. We took the pictures and generally got in the way. If you are interested in following more of his work, simply click his link to view the latest Instructable he's put together. To make a 3D metal piece from plastic, you will need a few simple tools:
1) Plastic part or model master
2) Sand
3) Molding Box
4) Raw aluminum or other metal
5) Kiln or furnace to heat the metal (We used Techshop RD's)
6) Cold water to cool off the metal afterwards
7) Baking oven (you can use your oven at home or any oven that heats up to an even 400 degrees)
8) Tongs
9) Protective metal gear: gloves, helment, and apron
Now, you're ready to make a real cast from plastic in a few short hours without breaking the bank. We cover simple medallions, complex 3D prints like this owl, and compound machine parts. Hopefully this will allow you to do 3D casts of anything you can dream up at home or your local hackerspace/techshop.
Step 1: 3D Print Your Plastic Model
This first part is pretty simple. Plastibot, Instructables, Techshop, Shapeways, and a number of other services in our area offer competitive rates for 3D printing. If you want ideas or are looking for something fun, I encourage you to check out Thingiverse. We used Plastibot to do ours as we find they have the most detail for the price when doing 3D prints, better than even MakerBot. Plus, they use PLA which bakes out more evenly.
Again, for your print use PLA, not ABS, as you want something that melts cleanly and is non-toxic. If you have any specific questions, Luis Freeman (owner of Plastibots) who runs our local 3D printer meet-up group every two weeks here is very knowledgeable. These are a few pictures from our March Workshop Event on How-To-Make-3D-Printers from scratch. Lots of fun all around.
So print in hand, what do you do next?
Step 2: Make a Sand Mold With Your 3D Print (Basic Flat Surface)
Alright, this next part is a little tricky if you're not there in person. Hopefully, you can see from all the pictures we took the process. Working with sand casting involves have a mold frame to pack the sand around the mold (either metal or wood). In our case, we did 2 metal tubes and a compound box to show you different variations used in the industry to pick what works for you. Please note, all of these methods work equally well, but are designed for different structures.
First, here's how you make simple flat shapes with a smooth bottom. Take a basic round mold, place the piece to be copied face up with the flat surface on the bottom. Slowly fill with lightly wet sand crumbling it with your fingers to make it fit as much as possible into the grooves. Beat the sand down with a hammer or flat piece of metal to pack the sand as tightly as you can. Scrap off the extra sand with a cake knife or small metal rod to make sure it is even. Gently flip the sand form and set it down on a flat surface. Lift the 3D print out of the sand. You can lift it with one fingernail first if you are worried about moving the sand.
This is ideal for metals, awards, custom jewelry, medallions, cosplay, and other pieces that have a flat surface on one side and details on the other. We did our local Techshop logo here.
Step 3: Casting Complicated 3D Prints (Bake Method)
Alright, this next method is our favorite as it mimics traditional jewelry wax casting, but the original 3D print is destroyed in the process. Again, take an empty 2-part mold and fill the bottom piece 1/3 full of sand, place the piece you are casting in the center and carefully pack sand around it as you go. Make sure you end up with the flat or bottom of the piece facing up. You are looking at the owl base here after we had melted it out. Once the molded piece in in place, turn it gently upside down and place it on a drip pan in your oven at 400 degrees to allow the PLA to melt out over time. This generally takes 4-6 hours depending on the 3D print size. Once you are done, take the top of the 2-part mold, fill it with sand, and place a sprue through it that will end up at the base of your piece. A sprue is simply a complicated way of saying poke a hole in the sand to give you a channel to pour your metal into. We just use a stick (chopsticks work great) to do this and then put the top piece on. Doing it separately first and then putting together the mold prevents you from accidentally poking sand into your mold. Stack the 2-part mold together and place it in the casting area while you finish up any other pieces you are doing today. If you have done lost wax casting before, this will feel very familar.
Step 4: Casting Complex Shapes You Want to Save (Box Method)
Alright, this last part requires the most set-up, but allows the user to re-use masters which can be important if your piece is very complicated to print or takes a great deal of time to do so. Below is a 3D gear part we printed for a machine that needed to be fixed. Taking the two-part box, unlock it and pack sand around the pieces you need similar to the flat method used for just medallions or metals. If your piece has a front and back, you can cast the front and back using traditional methods and putting the two halves together. Once done, lock your box, and poke a sprue in the sand to the side at least 2-6 inches from the piece you are casting with a connector to each. We did ours in the center as we were casting multiple gear parts and Evan wanted to save time. If you are a thoughtful designer like he is, you can chain together multiple pieces to save time sand casting series.
Now we have all three molds set-up, lets cast some metal!
Step 5: Light the Kiln
This next part is pretty simple, turn on your kiln and heat it up.
Step 6: Add Metal Stock
For our pour we used aluminum as it's easy to work with and handle, you can use something else. Once the kiln was hot, Evan simply dropped in our bar stock, and allowed it to melt. Go Evan!
Always remember to have your gloves on for safety at this point.
Step 7: Check/Pour Off Impurities
Once the metal is hot, check it for impurities on the top and pour of the top film to get rid of yours. This way your metal will be nice and clean to work with so you can buff and polish your piece afterwards. Evan poured off a little in this metal tray before starting the pour.
Step 8: Pour Your Metal Into the Mold(s)
Working quickly to prevent the metal from cooling, fill each of your molds with hot liquid, pouring into the sprue or flat surface. You want the force of the metal to disturb the mold as little as possible so pour gently. The metal should be filled to the top of the mold afterwards and the metal will cling to the surface of the sand. This will give you something to watch to see the metal cool and know when to remove it for quenching.
Afterwards, pour off the extra metal for reuse next time. A little metal goes a surprisingly long way here.
Step 9: Allow Your Metal to Cool
This process generally takes 5-30 minutes, but allow your metal to cool until it becomes solid again. This generally varies depending on the size of the mold and the piece being cast. Evan will test if the metal is cool enough by taking the tongs and using them to pick up the discarded metal (You can see him here holding the pre-pour in his tongs.) or moving the mold lightly and seeing what the extra metal you poured on top does. The metal will be bright, but solid to the touch. Many people will wait an hour just to be sure the metal is solid.
Step 10: Break Apart Your Mold(s)
Now, the fruits of your labors. Break apart your mold to recover your metal cast. If you did an open mold, this may be as simple as just taking a pair of tongs and lifting out your work, but more complex molds will need to be disassembled. You can use a hammer and tongs over a box (Hey save that sand for next time) to beat, ding, punch, or break the sand apart to reveal your inner treasure. Be careful not to burn yourself at this point. The outside mold should be cool to the touch as Evan demonstrates here, but the inside will not be.
Step 11: Knock Off Any Extra Sand
Taking your metal piece in your tongs, knock the tongs against the side of your sand box to knock off any extra sand that may have adhered to it in the process. This will help clean your sand and also prepare the piece to be quenched.
Step 12: Quench Your Metal
Taking your metal piece firmly in your tongs, walk over to your quenching vessel. This will simply be a large tub full of water which will bring the metal back down to room temperature. Standing back from the water, dunk the metal into the water to rapidly cool it. You will see steam escape and hiss up. Do this several times until the metal is cool to the touch. Viola, you're done.
Happy making! These are the 3 pieces we did, what will you make with yours?
Please note: At this time, Techshop RD has free monthly pours during the cooler months of the year. If you are interested in watching the process or having a 3D print of yours made into metal, check the calendar and drop by.
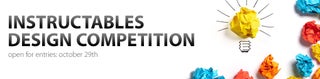
Participated in the
Instructables Design Competition