Introduction: How to Make a Ball Launcher
This is a DIY launcher built with Makeblock suits. We used two CNC motors to drive friction wheels, of which the speed can reach 120km/h theoretically. The machine is strong enough because of its metal framework. The maximum no-load speed of the friction wheels could be close to 10000RPM, so that please be careful in your progress of testing.
Glad to tell you that Makeblock is just about to sell this package ! And you don't need pick all the material one by one anymore! http://www.makeblock.cc/friction-wheel-launcher-p...
Step 1: DIY High-Speed Friction Wheels Launcher——Updated Version
We improved our launcher so that it can lauch the ball automaticly now.And the launcher is still improving...We need your support and advice! Most of out components are from Makeblock. And you can choose what you need on: http://www.makeblock.cc/
Step 2:
List:
- Beam2424-312 *2
- Beam0824-144 *3
- U Bracket-C *4
- F688ZZ Flange Bearing *4
- PU Wheel 125 *4
- Wheel hub 3 *4
- D Shaft D8x96mm *2
- Timing Pulley 62T *2
- Timing Pulley Slice 62T-New *4
- Plastic rivet 4060 *4
- Plastic rivet 4120 *4
- GB_SOCKET_TYPE7 M4x14-C *24
- Jbckscrew M5x5 *4
- Washer 8x1.6 *2
- Beam0824-320 *4
- Rubber foot *4
- CNC Motor Case *2
- CNC Motor *2
- Timing Pulley 90T *24
- mm D shaft 56mm *2
- Timing Pulley Slice 90T-New *4
- Shaft Connector 4mm V2.0 *2
- Jbckscrew M3x5-C *14
- Flange Bearing 4x8x3 *2
- Bracket P3 A *2
- Beam0808-136 *1
- Shaft Collar 4mm *10
- Bracket 3x3 *2
- Acrylic Sheet for circuit *1
- 1-direction motor driver *2
- Shaft D4x160mm *2
- Beam0808-312 *2
- Plate 45° *3
- Bracket P1 *6
- Hexagon socket button head screws M4x22 *24
- Hexagon socket button head screws M4x35 *8
- lock nut M4 *28
- Hexagon socket button head screws M4x30 *6
- Hexagon socket button head screws M4x16 *12
Step 3: Introduction
Now, I will show you the details of building.
This picture shows all components you need.
Step 4:
1. Build the frame after you prepared all the part.
The picture does not include the necessary nuts and screws.
Step 5:
The main frame is an L-shaped configuration. There is something wrong with the side beams (shown in red arrows), we didn’t notice it until we took the corresponding picture. And it will be fixed later.
Step 6:
Two piece of right-angle connectors are installed on the rear end of the base to fix the hypotenuse of the triangle structure, which is helpful to the rest assembling.
Step 7:
The figure of main frame
Step 8:
Leave the screws of four corners alone when assembling the main flame, for it should be used to set foot pads. All nuts of the frame should be lock nuts, because that this machine has a relatively severe vibration when it works.
Step 9:
Fix the rubber foot pads on four corners of the seat after put on the screw.
Step 10:
The frame finished.
Step 11:
Put the frame aside and begin install the friction wheel module.
Step 12:
Screw all the parts with the shaft and tighten the screw.
Step 13:
Processed the plastic rivets according to the picture.
Step 14:
Stick to rivet and timing belt with glue. And do not tighten the headless screw before the whole machine assembled.
Step 15:
Install another friction wheel module in the same way.
Step 16:
Next, after you prepare the part used in friction wheel bracket.
Step 17:
Install the friction wheel module on the frame.(Restore the side beams at this time)
Step 18:
Then, install the second friction wheel module. Please pay attention to their position.
Step 19:
Please remember to set the timing belt on the shaft when you install the friction wheel module. We forgot do that when shooting the picture above, and the figure below shows the fixed result. The long one is installed on the topside, and the short one is downside.
Step 20:
Then prepare all parts of motor module, and begin working.
Step 21:
Install the synchronous belt wheels firstly.
Step 22:
Then put the timing belt wheel through the shaft, and make it together with the motor. This motor is used to install CNC drill bit, so we could assemble the shaft with the motor easily without any coupling.
Step 23:
Install the other motor module in the same method.
Step 24:
Next, install the motor on the main flame, and it needs two motor brackets.
Step 25:
The timing belt should be covered on the synchronous belt wheel while installing the motors. What’s more, the belt shall be as tight as possible.
Step 26:
As we know, the motor output shaft is cantilever structure and then it would be easy shaken even damaged. To avoid this kind of tragedy, we also fix the other end of the shaft on the frame. In this parts some bearings and some certain related components is necessary.
Step 27:
Adjust the position of the bearing carefully to make sure the tension of timing belt is appropriate. And then fix it on the thread slot.
Step 28:
Two pairs of beams shall be added in order to increase the strength of the whole structure.
Step 29:
While installing this two double beams, you may need a helper to hold the frame.
Step 30:
Till now, the instruction of mechanical structure is completed.
Step 31:
Next, start the installation circuit system. Weld wires on the motor first. Because the working current of the motor is bigger (about 5A), more than 1.5mm2 section of wire is recommended. Place heat shrinkable tube on the welds, to avoid short circuit.
Step 32:
After welding wire on the good motors, please prepare two pieces of motor-speed-control boards. We could modulate the output voltage to control the motors’ speed by the knobs on these two boards. This kind of board supports the 12V-30V input voltage, constant current can be up to 5A, and peak current can be up to 10A. In addition, a piece of wood or acrylic board could be prepared to fix the circuit board.
Step 33:
Install the circuit board and acrylic sheet to the frame. (Acrylic board is just to be set in the thread groove of double beams.)
Step 34:
Then make a power cord according to the power used. In this testing, we use two pieces of 3S aircraft model lithium battery, so that T joint is chosen.
Step 35:
Finally, connect the power connector and the motor driver board, done!
Step 36:
This is my favorite part. Actually, you can transform this tennis ball launcher into another ball launcher by adjusting the gap between two friction wheels. Here are some examples.
Step 37:
Step 38:
Get this package:
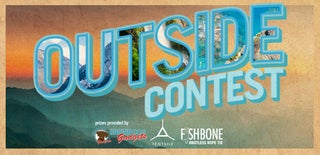
Participated in the
Outside Contest