Introduction: How to Laser Cut and Assemble a Lego Light Switch Plate
This is how to create a custom light switch plate using Lego people and a laser cut plate and graphic components. My examples are all Star Wars related, but you can use any Lego people you like to make a custom light switch plate for a child's room or a game room!
Step 1: Tools and Materials
Tools:
Access to a laser cutter
Design software like Adobe Illustrator
Materials:
Acrylic sheets in a variety of colors, 1/8" works well
Solvent Cement (I use Weld-On)
Lego People that make you really happy
Step 2: Create Your Design in Adobe Illustrator
Using an actual switch plate, I created a large plate design that is 1" bigger than the jumbo plates you find at the local hardware store. I also created a backing "ring" that is fused to the back of the plate, giving it some volume.
I also created simple burst designs and platforms that the Lego people can stand on.
I made the names Cassian and Jyn in script, so they would stay together as a single unit. My plan was to use them as a platform for those characters, so I needed a solid surface to work with.
I always dedicate one layer of my design to virtual 'testing', where I use references, like a block that represents an average Lego person, to layout my designs and make sure everything fits. I make my references green, which is a color that does not affect my laser. That way, I can add references to drawings without fear that the laser will accidentally cut, raster or engrave them!
Step 3: Laser Cut Switch Plates and Additional Components
After testing a single plate against an actual switch plate, to ensure the holes are accurate, I cut plates in several colors. I also cut multiples of all the graphic components - the bursts, the script names and the platforms - so I can play around with them to see which combinations I like best. My final designs are often different from the ones I originally had in mind, so experimentation is an important part of my process!
Step 4: Using Solvent Cement for Fusing Acrylic
Sure, you could use glue, but solvent cement has many advantages:
It's faster and easier to apply
It looks better, especially on transparent and translucent acrylic
It joins better, because it actually fuses two pieces of acrylic into one solid unit
The only disadvantage is that is doesn't work on all plastics. I tried to use the solvent cement to fuse Lego people onto a store bought plate and it didn't work, probably because the plate was nylon. Fortunately, Lego people are made out of acrylic and fuse nicely to the acrylic plates and components.
The liquid solvent is sucked up into a syringe bottle and squirted carefully on the join between two pieces of acrylic. The fluid automatically wicks into the opening, and a very little bit goes a long way.
Step 5: Fuse the Components Together
I started by fusing together the multi-layer bases. It only takes a minute for fused pieces to dry enough to move on to the next step!
Then I fused the Lego people to their bases.
While they were drying, I fused the backing ring to the back of the switch plate. This is optional, but it guarantees a tighter fit against the wall.
Then I fused characters and their bases to the switch plate. In the cases of Cassian and Jyn, I also tack-welded the heads to the plate, for extra support. For the other characters, they were secure enough by just fusing them to their bases. This leaves them flexible and somewhat pose-able, even after they are attached.
Step 6: Mount Them to Your Wall!
If you find that your plate is too translucent and you can see the opening in the wall, you can use a matching paint color to paint the back, making the plate opaque.
Step 7: You Can See a Video Tutorial of the Entire Process Here
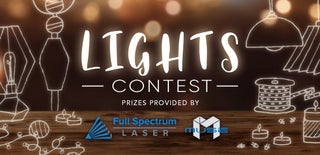
Participated in the
Lights Contest 2017