Introduction: How to Make a 3D Printed Bracelet
This instructable requires at least a beginner's level in 3D modeling although it should be easy enough to follow along even if you've never modeled anything before.
I have a background in architecture and once used 3d Printing in grad school for an architectural model. I remember staring down at my fragile, crumbling model thinking-- this technology is limited right now but I bet in 10 years it will be pretty amazing. Well fast-forward only 5 or 6 years to when I stumbled upon a website for a company that offered 3d printing to anyone with a 3d printable design, in a variety of (non-crumbly) materials. I started designing jewelry and recently came up with the Faceted Cuff.
The idea for the Faceted Cuff stemmed from the fact that (similar to a trend in architecture) forms no longer needed to be limited to simple, repetitive, regular forms. 3D Printers (and 3D modeling) allow you to create irregular complex shapes and- as long as you follow some basic guidelines- are able to print those shapes layer by layer almost as easily as it would a box.
Step 1: 3D Printing Basics
Before we go any further I should clarify what is involved and what is needed in 3D Printing your own jewelry.
First of course you'll need an idea for what you would like to design. I tend to sketch a lot before I jump right into 3d modeling.
Next you'll need to decide on a software that can export files that are usable for 3d Printing. Right now I'm using Google Sketchup because it was easy to learn, works on a Mac, and... well because it's free. ;)
Third you'll need to find a 3D printing service (unless you're lucky enough to own your own 3d Printer). I've used Shapeways and Ponoko but a simple google search should give you several options.
Lastly you'll just need a basic grasp of how 3d printing works. If you think of the printer you have in your home or office, that piece of equipment takes 2D information (x and y) and prints it out on paper. A 3D printer uses a similar concept except that it takes 3d information (x, y, and z) and "prints" it. It requires a clean continuous model with no holes in order to be able to print an object layer by layer. You should also keep in mind that with 3D Printing, price is not based on the complexity of the model but on volume. So if you can express a design in a limited amount of material, even if that design is extremely complicated it would still be cheaper than printing a solid box of the same dimensions.
Step 2: Modeling the Faceted Cuff - Creating a Series of Frames
Though there are endless possibilities for what kind of 3D Printed jewelry you can create, I'm going to focus on one of my bracelet designs - the Faceted Cuff. While the Faceted Cuff might look complex at first glance, when you break the model down it's actually pretty simple. It consists of basically two systems-- the framework, and the connecting members.
With this design I wanted something that was faceted but irregular. While there are several ways to model that, the way I settled on was to create a series of frames set at an equal distant apart. While each of these frames had the same number of points, the location of the points varied. This was so that when the connecting members were drawn in, it would suggest an irregular surface.
Just a note to anyone who has started using Google Sketchup-- you've probably noticed the software is pretty limited and at some point you'll get to a point where you need to install some plugins in order to do what you want (or to do it faster). For my framework and connecting members I used the following plugins:
TubeAlongPath.rb
lines2tubes.rb
There are probably others, and it might even be possible to do this in sketchup without a plugin, but I found these to be the easiest to use.
Also I've noticed when using plugins in Google Sketchup it's best to work at a large enough scale (sketchup doesn't like small models) so you may need to scale the model up while working on it so there are less errors/weird things happening to your model. Just make sure to scale it back down before exporting.
Step 3: Laying Out the Frames
I needed to set up my frames in the shape of a cuff and again turned to a plugin for that. It's also possible to just lay them out manually but using the plugin is much easier. For this I used clf_shape_bender.rb (shape bender). It allows you to take a grouped object (the set of frames) and bend it around a drawn shape (the oval cuff shape you see in the photo).
Step 4: Adding Connecting Members
I then added the connecting members in between the frames by drawing them in as lines and then using one of the previous plugins I mentioned to create the tubes.
Step 5: Exporting for 3D Printing
After looking over the model, I decided it was ready to go and exported the file as a ".dae".
From there you can use a free program like Meshlab to open the model and convert it to an ".stl" file.
After that, the last step is to open it in a program like Netfabb to run it through some checks and repair any problems (holes I missed, faces that were oriented the wrong way, etc). After double-checking the scale, I exported the fixed file.
I then uploaded the file to my preferred 3d printing service, checked to make sure it shows up properly, and ordered the design in one of the offered materials.*
*I should add that you'll want an idea of what material you'll be printing in BEFORE you start modeling to make sure your model meets all the thickness/detail level requirements for that material. There's nothing worse than having to start over because your model isn't thick enough.
Step 6: And Lastly Waiting...
The last step may be the most difficult... waiting several weeks for your pieces to arrive. ;) But once you see what you can create you will be hooked on 3D printing.
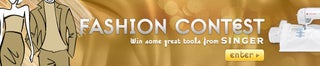
Participated in the
Fashion Contest
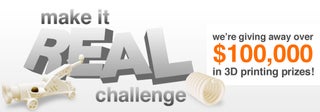
Participated in the
Make It Real Challenge