Introduction: How to Make a Solder Buddy (from Sheet Plastic)
[UPDATE - Thank you to everyone who voted in the UP! 3D Printer Contest - I was lucky to win an UP! Plus, so now I can proceed with Solder Buddy Mark III (Mark II is improving Mark I with you suggestions below) and then release the CAD files*.
*I am also looking for CAD software to do this in [sponsorship welcome if you know anyone who works for a CAD company!] - as Sketch-Up is going to take forever!
The full videos are up in a playlist, here. Everything is free on Design Modelling, so thanks for your support!
Hello, I'm Jude - and I'm a Design Engineer. I've been making models of all sort of things since I was a kid... however, I've been doing it professionally for it for about 4 years now and I'm still enjoying it immensely!
I created a website called Design Modelling and I’ve been running workshops showing people how to use simple materials to explore their ideas, be it for professional work or personal creative projects... as some point it really helps to get ideas out of your head and into your (or someone elses) hands!
Solder Buddy was a quick project that I did one evening to show the possibilities for what could be made with ABS plastic sheet. I’ve had a few requests on how I did this so I have uploaded an Instructable. However, if you are new to working with plastic or would like to know a few ‘pro’ tips I’ve picked up along the way, check out the techniques first.
This instructable should be a good example to show the possibilities of working in plastic, but if you are really serious about learning, I have a full video going into more detail of how I made this and explaining some of the design thinking behind it, here. The combination of the techniques covered and the application will be valuable to anyone trying to create robust models for the design industry.
Please let me know how you get on (Design Modelling on Facebook) - and have fun!
Step 1: What You Need
I have included a layout of the ABS Plastic Sheet parts, as well as a [poorly drawn] exploded diagram. Try to have a go yourself, to plan things out - as obviously you will have different equipment and parts to what I had available. The trick is to ensure you have enough space for things to fit, so be generous on your first attempt.
(If you have never set out a plan for something like this before, you might like to work in cardboard first, as it is cheaper - I did a previous project which might be useful too).
SERVO BUDDY EQUIPMENT:
PARTS
- Brake Cable.
- Servo Motor (from an old RC car, but you may modify a new one too).
- Sugru (making handles, grippy feet on box, etc).
- Bearing or small rotating wheel on a mount.
- Rubber bands / inner tube from bike.
- ABS Plastic (about 2mm thick).
- ABS/Styrene rods/tubes/etc. (assorted sizes from hobby shops).
- Solder on a reel.
- Enough batteries to power servo.
- ‘push-on’ switches.
- Heat-shrink (covers solder joints).
- Extra wire.
- Brass Inserts - with bolts to fit.
- 2 small springs.
TOOLS
- Pliers.
- Soldering iron.
- Dremel / Proxxon (latter is better, imho).
- Scalpel + blades.
- Metal ruler (NOT plastic).
- Calipers.
- Marker.
- Insulation tape.
- Zona/Razor/Hack saw.
- Screwdriver.
Step 2: Techniques - for Working in Plastic
Step 3: Plan the Layout of Your Solder Buddy
To begin, take a piece of paper and position the components you will use to make your solder buddy. As you can see from the diagram - you will need to fit the batteries and other electronic components inside. The servo and solder reel on top - along with space for the brake cable to be securely fastened.
You might find it helpful to try out a few different designs.
Step 4: Box Assembly
The nest step is to glue these together with super glue (please wear goggles).
Tip: Insulation Tape will not stick to superglue (easily) and hence, can be used to hold things in place - both before glueing and also while drying (and avoids you getting stuck to the model!)
Check out the video if you need a demo.
Step 5: Sanding Down
Sticking a sheet of sandpaper to a block of wood helps keep edges flat, stops the paper slipping around and gives a level finish.
Pictured, is black 'wet and dry' [sand] paper. It is available in many different grades, so you could either go for a fine polish (1200grit) or have your box with a 'matt finish' (around 600 grit).
As you can see, I have also made improvised sanding tools, which is a good thing to be aware of to work in difficult areas and to stop your fingers aching as much! More tips, here.
Make sure the open sides of the box are both flat - by sanding in circular motions.
Step 6: Servo Modification
You will need to Google this info if you have a different one (than my HS311) - but it's quite simple to do.
I made a quick video of the image below, for more details, here.
Step 7: Roller System
Creating the solder-wire rolling mechanism is probably one of the trickiest parts of the project.
I have also made a video, here, but these are the steps involved:
- Cut the rubber into a strip. Wrap it around the bearing. Measure where it goes all the way round. Cut this measurement 1 or 2 mm shorter - to give a tight fit. Glue the ends of the rubber (use a cocktail stick to apply super glue). Join together carefully. Allow to dry. Snap around the bearing. Use a scalpel blade to apply glue in between the rubber and the bearing.
- Repeat for the wheel of the servo.
- Using an off-cut of ABS plastic - make a 'cross' for the bearing to fix onto. Glue it lightly in place, so that you can work out the position - before gluing permanently.
- The bearing and wheel should be fixed so that they are close enough to provide grip (without stalling) and not too far apart (so slippage occurs). Use a bit of plastic tube to feed the wire in between the wheel/bearing - while running - to check performance.
- Glue in place thoroughly, when happy with it.
- Make supports for the feeding tubes - on either side of the wheel/bearing. Glue in place.
Step 8: Check Roller Operation
Show on the right - you will need to make a spindle for the solder-wire reel. This can be simply done using the score and snap technique (shown earlier).
After this, you can put the servo/Roller Mechanism beside it and power it up to see if it all works.
Step 9: Brake Cable
The brake cable has three 'layers' to it. Care need to be given not to cut through them, as you do not want the solder touching the metal winding of the brake cable.
See the diagram of how to create this assembly.
Step 10: Stand for Brake Cable / Spring on Roller / Connectivity Check
Next you can see that the brake cable needs to be mounted to the top case of the solder buddy. One can make a ‘A-frame’ from the plastic to secure it into place. The Brake Cable should be at the same height as the wire exiting the Roller system. This will be tricky. Take you time - you you want a smooth transition.
Secondly you will need to add a spring onto the end of the ‘in’ side of the roller mechanism tube. Then attach a wire to this, so that a connection can be made between the solder and the rest of the wiring. (see diagram again if unsure).
Finally, I have used a Multimeter (on ‘beep’ mode) to check the connections along the bike cable and the solder winder.
Step 11: Cut Button-hole / Solder the Circuit / Heat-shrink
Using a dremel/proxxon drill out the hole for the 'feed' button. Tidy up with a scapel - take care not to cut towards yourself and only trim a little at at a time!
Step 12: Brass Inserts (a Professional-style Fixing for the Base)
These are used when you need to repeatedly take apart and reassemble an 'enclosure' / box, as if you used conventional screws (self-tappers) in a boss, these would eventually wear out.
*Given that you've 'made it' this far, I guess you must be pretty serious about learning something, so in this case, I'd say this is a great section and has the potential to really raise your test-rig-building game, as it were. It's pretty lengthy stuff, so I included another video again.
Brass inserts can be used in a variety of ways, but this is one of them that is common.
Step 13: Sugru Time
If you are not familiar with Sugru, check this out!
I have used it here, to do a few things:
- create a handle for comfort.
- secure the workings of the button on the brake cable.
- give durability to the end of the feeder.
- insulate the wires from shorting out.
- stopping the case from sliding around.
- add some funky colours.
The clever bit, on this project, for me, was taking covering base in Sugru - and then working it flat, but putting it on a flat surface and adding a little water - then buffing it flat.
I also needed to cut-out the excess Sugru that got in the holes for the screws, but it was very easily removed.
Step 14: Final Assembly & Thanks!
Thanks for watching and please do visit Design Modelling website or Facebook - I'd love to see/hear how you got in.... and most of all what you did differently. After all, these tutorials are about enabling you to define your own design direction.
Have fun!
Jude
Step 15: Appendix - Feedback
Here are some more photos of the mechanism, as requested by people, here on Instructables.
Please let me know if you have any other questions!
Best wishes,
Jude
PS - In case you are wondering why it looks different - I built it 'on the fly' first of all and then remade it again for this tutorial.
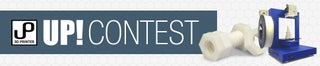
Grand Prize in the
UP! Contest