Introduction: How to Build a Wooden Drill-Press Vise | DIY Woodworking Tools #3
I've been needing another vise for quite a long time now. I have one vise, Which is in my room (My room serves as a workshop). Sometimes, When I do messier projects, Such as ones with a lot of sawdust, I prefer doing them in our balcony. Because I have one vise, And it is pretty difficult to remove it from my table each time, I end up working in my room. Even though I use a Dust-Mask, It does result in me inhaling small dust particles that I shouldn't be breathing in.
What am I doing? As a 13 year old kid, Am I trying to "invite" lung cancer for when I'll be older? I'm tired of this, I need a new vise!
But there is only one problem: VISES ARE SO EXPENSIVE!
To explain more, Here's a short argument between my wallet and I, About the Vise. This is pretty much what went through my head. Enjoy ;)
My Wallet: "You already said it-- Vises are so expensive! When was the last time a 13 year old like you had some spare $100 bills to spend on a new vise?"
Me:"I know that, But I still want one! I want a big vise: One that has a huge clamp capacity, And really wide jaws. It's almost impossible to work on woodworking projects without a good vise."
My Wallet: "I already told you, Yonatan. These vises are expensive. You can't afford a vise like that..."
Me: "Look Wallet, I told you-- If I need a vise, I'm going to buy a vise. That's how it works in life."
My Wallet: "No." (***Lightbulb goes off***) "Yonatan, I have a genius idea!"
Me: "And it is... What?"
My Wallet: "You can make your own vise! You can make it with free scavenged wood!"
Me: "GENIUS idea! I recently started a new hobby-- Woodworking. I've already built a my own Wooden C-Clamp, So why not try making a wooden Vise?"
A little over a week and a numerous amount of hours later...
I present to you, The Ultimate Homemade Wooden Vise!- A 100% homemade wooden vise:Built to have a 5" (14cm) Clamping Capacity, And 6.5" (16.5cm) Wide Jaws!
I built it with free scavenged wood, And the basic beginner's woodworking tools that I have, And You can too, With basic hand-tools! No Table-Saw, No Miter-Saw, No Welder, No CNC, No Drill-Press!
Also, Guess what? This whole vise was built with materials that I had laying around, Meaning that I built it for FREE, Obviously!
Step 1: More of the Backstory, Plan, & Sketches
I recommend seeing the image note that is in the second image. By any chance, Now, Is your mouth wide open?
If you would ask me "Which one of my tools is my favorite?" I would probably reply "My Vise". I love vises!
If you would ask me "What do I dislike the most about making things with my vise?" I would immediately reply "The marks that are left on my projects from my Vises' Jaws". They drive me crazy!
Well, For most vises, There's a really easy way to solve this problem: Wooden Soft Jaws, Right? Yes, But they don't work on my vise: The clamping capacity of my metal vise is less than 2" (4,5cm), So if I put soft jaws, It wouldn't really leave any space for clamping something...
Looks like I need a new vise... ;)
I began designing my vise (To make things easier, Obviously). I started by sketching it in the shape of a machinist's vise. After several hours of trying to sketch it out (~4 hours, I believe) I wasn't able to turn it into a vise. 4 Hours sounds like a big waste of time, But it DEFINITELY wasn't. I learned a lot from not being able to do it:
"I didn't fail, I just found many sketches that can't be built into vise" - My horrible (-ish) transformation of Benjamin Franklin's & Thomas Edison's quotes
I understood that it wasn't my level: I didn't have the tools or skills that were needed to build it. After all, This is just my third woodworking project!
After fantasizing so much about the vise, I wasn't ready to give up. But still, I didn't know what to do.
Then the idea hit me! I remembered that during the summer, I wanted to buy a vise (This was before my grandpa gave me My Great-Grandpa's Vise, Which I restored) on eBay, And I found something that was called a "Drill-Press Vise". To be honest, Back then, I didn't even know what a "Drill-Press" was. It looked kind of small to me, But it was significantly cheaper. I think it costed around $25 (Though it didn't matter because it was still too expensive for me...). Yes, Many people would say that $25 isn't a lot, But there is no reason to pay that amount of money when you can make something (that is probably better) for free.
A Drill-Press Vise holds the workpiece (A small wooden piece, For example) almost totally flush with the surface, Which makes it ideal for small woodworking projects (What I make). I decided to design and build my vise in the shape of a Drill-Press vise for MANY reasons:
1. Easier & faster to design & build (Aka impossible for me to build it) ✓
2. Uses less wood (All of the wood that I use is wood that people throw away, And I find and use it. I don't have a lot) ✓
3. Has a better grip on wood (Or other materials, Because of it's big jaws) ✓
4. Clamp capacity can be adjusted quickly ✓
5. Doesn't need very accurate tools to be built (Because my tools aren't very accurate) ✓
6. Very low friction in the threaded part of the Eyebolt (Meaning that it can be opened and closed impressively faster) ✓
7. Grip before tightening function (Materials don't fall/move until you finish tightening the bolt) ✓
8. Can easily be taken apart for adjustmenting, Enforcing & Modifying ✓
9. Can be used with a short Eyebolt/Threaded Rod (Aka Cheaper to make, & I was able to use the Eyebolt I had) ✓
10. Has an unlimited clamp capacity-- All I have to do to enlarge the clamp capacity is add another board to the end and drill holes accordingly ✓
11. Can also serve as a regular woodworking clamp (Somehow the most similar to a Pipe-Clamp) ✓
12. Doesn't need to be tightened very tightly (Because of it's big jaws, High contact area) ✓
13. Woodworkers that have a big workbench can make it without the base-- It can be built and implanted right into their workbench! ✓
14. It's flat. I can easily mount it on a wall (with any possible tool holder) for easy storage ✓
15. Can be used in a Drill-Press (I'll have an Instructable on how to make one-- Coming Soon!) ✓
I will explain more about most of these features later in the Instructable
And that's what I decided to make!
As I do with many of my projects, I searched on YouTube for a "DIY Wooden Vise" but there weren't any really great results, But they did somehow help. Hopefully, With my Instructable, You'll be able to make your own woodworking vise-- Easily!
Almost nothing in the world makes me happier than building my own tools! It makes my happy because I built a complicated project, Learned a lot from it, And saved a lot of money (Ingnoring the fact that I don't even think that it's possible to buy vises that are this big)!
Let's get started!
Step 2: What You'll Need:
Hardware & Materials:
An Eyebolt (Or a Threaded Rod)
2 Identical Hex-Nuts (That fit on the Eyebolt)
A "Finishing" Washer
Wood: I used a mix of Pine & Extremely Dense Plywood (Dimensions in Step #2)
Salvaged Metal Rod: 10mm Diameter & 10cm Length
Salvaged Metal Rod: 10mm Diameter & 7cm Length (Preferably with a soft rubber coating)
Salvaged Metal Rod: 8mm Diameter & 9.5cm Length (Support Rods)
Several Wood Screws
One Wide Rubber Band
Chemicals & Adhesives:
2-Part Epoxy (That can adhere to wood)
Wood Glue
CA Glue (Optional)
Tape
CG-90 (or grease)
Varnish (Or Lacquer)
Tools (+Attachments):
5mm Chisel
Several Clamps (I used several Transformers as weights, 1 C-Clamp, 1 Bar-Clamp, & 1 Spring Clamp)
Caliper
Hacksaw
Permanent Marker
Sanding Stone
Pencil
Back-Saw
Speed Square
Utility Knife
File
Rasp
Vise
Rasp Planer (Or a Regular Planer)
Icepick (Punch)
Glue Mixing Stick
Drill-Bits (in mm): 1.5, 6, 8, 9, 10
Sandpaper Grits: 24, 60, 100, ~100 (Silicon Carbide), 180, 400
Flat Screwdriver (For prying open the Varnish Container)
Paintbrush
Eraser
Electric/Power Tools:
Jigsaw
Drill
Dremel (Or any other Rotary-Tool)
------------------------------------------------------------------------------------------
Why: I NEED A BIG WOODEN VISE! (The last two steps have gone over that quite a bit...)
Safety Gear Needed: Respirator, Goggles, Ear-Muffs, & A Ventilated Environment
Cost (for me):FREE!
Needed Skills: Intermediate at Woodworking (I'm pretty much a beginner, And this was a complicated for me to build, But I did it!)
Approximate Time: 15 Hours (It would probably take ~1 hour for a woodworker that has more experience and tools than a 13 year old like me...)
Step 3: Marking & Cutting the Wood to Size
I started by planning the size of the boards that I wanted. I did this on a board of Pine wood (As I mentioned before, This is wood that I found for free, That's why it has blue paint on it) with a Speed Square, A Ruler, And a Pencil
I clamped the board to a table, And sawed all of the the boards by the dimensions with my jigsaw.
***Plot Twist***
Why did I not give you the dimensions? One day after that, I found some EXTREMELY strong Plywood* outside.
It was obvious that I was going to use it! I used a backsaw to cut it to size
Here are the dimensions:
Pine: 2 Pieces of 28 X 22 X 3cm (Base)
Plywood: 1 Piece of 6 X 13 X 2.5cm ("Hexed" Support Piece)
Plywood 2 Pieces of 16.5 X 6 X 2cm (Vises' Jaws)
Need the dimensions in inches? Use this Converter
I wanted to use Plywood as the base, But I didn't have enough. After making it, I can definitely tell you that the Pine is good enough...
*It was built in some kind of unknown structure to me, My best guess is that is was part of a Baby Crib or an Arm-Chair. The plywood was bent beautifully, And was strong enough to hold my weight when I sit on a "U" shaped part. I'll send more close up pictures if anyone can help me identify this type of plywood, Please!
I, Obviously, Used the parts that weren't bent
Step 4: Roughen, Glue, & Clamp the 28X22's on Top of Each Other
To make the base, I glued both of the 28X22's on top of each other.
It didn't bother me that there was paint (As I mentioned earlier) on both sides of the boards, Even though it weakens the adhesion. This part doesn't need to be extremely strong
First, I started by scoring random lines along both boards. Although this is optional, It wasn't a lot of work, And still does dramatically increase the adhesion. I just did it to compensate on the fact that I didn't remove the paint...
I some smeared some glue onto the boards, And clamped them together. Because I don't have a lot of clamps, I stacked about 15 Kilograms of transformers on the boards, This is the way to ensure great adhesion ;)
In electronics, This would be called "tinning" and "soldering them in parallel", If you know what I mean...
As I mentioned earlier, The wood I used had blue tape on it. On the top part, It did bother me, So I started removing it with a Rasp Planer, Then 24 Grit Sandpaper, And when I had removed all of the paint, I smoothed it out a bit with 60 Grit sandpaper. Yes, This makes it pretty smooth. I would have made a separate step for this, But I figured that I'm probably the only one that had to do this. To give the base a smoother look, I also used my Rasp-Planer to give it a "Routered Round-over" look
Step 5: Drill a Hole in the Middle of the 6X13cm Piece of Wood
If you've seen my Homemade Wooden C-Clamp Instructable, You know where I'm leading you too...
First, I punched a small hole in the middle of the 6 X 13cm piece of wood
After that, I used a Drill-Bit that was slightly wider than my Eyebolt to drill a hole all the way through the piece of wood. The drill bit has to be 100% perpendicular (90°) with the wood. I have to admit that I'm really proud of myself for drilling it that accurate, Without a Drill-Press, Of course!
I don't have a Drill-Press, But it would definitely make this process easier. Still, I managed to do this accurately
Quick Tip: From my experimenting, It's easier to drill with more precision when drilling at high speed, And low pushing force. This way you focus more or positioning it correctly, And less on the drilling action. Trust me, It helps a lot! And as always, Clamp the wood to your table so it doesn't move.
Note: Some of the pictures show a different piece of wood. This is because I later replaced with plywood. Pay no attention to it...
Step 6: Drilling Holes for the Support Rods
After thinking quite some time on how to clamp materials while being able to keep the front jaws parallel with the back jaws, I came up with the idea of using "Support Rods"* (more about them in the next steps). I used metal rods that were 10mm in diameter.
I apologize for not having any good pictures (No worries! More better ones later!), But, First, I made sure to clamp the 6 X 13cm piece exactly over the 1.6 X 6cm (The front jaw). After that I used a Drill-Bit that was slightly wider than the Rods to drill two holes (Totally through the 6 X 13cm piece, And halfway through the front jaw), As shown in picture #3. The Rods should line up straight, And you should be able to move the 6 X 13cm piece across the rods, Like an axis (Is that the right word?)
In the beginning, I didn't think about making them. I thought that the only way was to make beveled edges, Which was pretty impossible with the tools I have. I then saw one of Irwin's (A company that makes woodworking tools) woodworking vises, I knew that Support Rods were a great for this project
Step 7: Trace Around the Hex-Nut, Chisel the Hole, & Add Epoxy
Remember the piece that had a hole that was drilled in the middle?
I made sure that the hole of the hex nut was aligned perfectly over the hole I previously drilled. I then traced the outline of the Hex-Nut over the hole.
After that, I used a 5mm Chisel and My Homemade Plywood Mallet to chisel out a hole in the shape of the Hex-Nuts in the wood, The depth of the hole should be chiseled to the exact height of both of the Hex-Nuts when they're stacked on top of each other.
A great way to check this is with the depth gauge on a Caliper. Here's a video on how to do use the depth gauge on a caliper
Lastly, I mixed up some 2-Part Epoxy, Made sure that all of the insides of the hole were covered, And placed both Hex-Nuts inside. Make sure to cover the the exposed part of the Hex-Nuts, While being careful and not letting any Epoxy accidentally drip inside.
This has to be really strong, Meaning that you MUST let the Epoxy fully cure. Being "Efficient" is not smart in this step...
Step 8: Drilling Pilot Holes, Gluing, & Screwing the 6X13 Piece (The "Hexed" Support Piece)
I had some Small 90° Plastic Shelf Brackets that I wanted to use to secure the "Hexed" Support Piece to the base. They look weak, But they're very strong. I've used them in several projects before...
I used a 1.5mm (0.02") Drill-Bit to drill Pilot-Holes in the "Hexed" Support Piece (There is no need to countersink because the bracket has already been countersunk) and screwed in some small screws to secure it in place.
Although this is optional, I did smear some Wood-Glue onto the bottom of the "Hexed" Support Piece, Because this needs to be very strong.
Same as before, I drilled Pilot-Holes and screwed the bracket (That is connected to the "Hexed" Support Piece) onto the base.
Step 9: Cutting & Shaping the Support Rods
As I wrote earlier, To help keep the my Vice's front Jaw Parallel with the back jaw, I decided to add two "Support Rods". Well, They have to be modified a bit!
First, I clamped the Rod in my Vise, And cut it to a length of 9.5cm with the help of my Dremel and an abrasive cutting wheel. This can be done with a Hacksaw, But it is way quicker with a Dremel. I chose to cut it at that length because it was the a little bit longer than the threads of the screw, When pushed all the way through the hole that was previously drilled.
After cutting the Rods, The edges were pretty sharp. I inserted them into the chuck of my drill and pushed them with a lot of strength into the side of a sanding stone, To help round the tip a bit. Improvised Lathe! ;)
I then used a small piece of Silicon-Carbide Sandpaper (The Grit# isn't written, But I can estimate that this is about 100 Grit) to smooth everything a bit more. You're probably thinking that 100 Grit won't make it smooth, But it has to be Not Sharp, Not Very Smooth...
The others side, On the other hand, Has to be rough (More on that in the next step). I, Again, Clamped the rod in my Drill's Chuck, But this time, With the other side facing outwards. I then used a file to scratch the tip of the rod. Again, Basically like a Metal Lathe works...
Step 10: Epoxy-ing the Support Rods in the Front Jaw
I used Epoxy to glue the Support Rods in the holes that were previously drilled. Epoxy is the ideal adhesive because it is very hard, But also slightly flexible.*
First, I mixed some 2-Part Epoxy, And coated the tip up until ~1cm from the tip. I also covered the outside. A rule of thumb is that if you don't see the connection point, You've put enough Epoxy.
I quickly slid it into the holes in the Support Rods' holes (obviously) to ensure that the Epoxy would cure in the correct position
See my comment (Yonatan24) on This Forum Topic for more info about Epoxy
Step 11: Cutting to Size & Attaching the Knob (Twist Handle)
I decided to use a salvaged printer rod that has a rubber coating* for the Knob. This way, When I apply more torque (close the jaws tighter) It is more comfortable on my hands.
I first used a ruler, And found out that the longest I could possibly make the Rod was 7cm. I then cut it to size with a Hacksaw.
I also used my Dremel, With a Sharpening Stone Bit to roughen the inside of the Eyebolt to increase the (future) adhesion.
To finish everything off, I glued the Rod inside of the hole (aka eye) of the Eyebolt with 2-Part Epoxy. If a regular bolt was used (Instead of the Eyebolt), I would've had to drill a hole in the middle of the Bolt, Which is pretty complicated. I actually did do this here.
Note: Let the Epoxy fully cure before applying any pressure to avoid ruining the adhesion
*The rubber is used to increase the amount of friction (Is traction the right word?) between the rod and the paper. This Rod gets spinned by a motor(through several gears), And it is what pushes the paper out of the printer.
Step 12: Glue on the Finishing Washer
I Finishing Washer* is a very important part to add. It stops the Eyebolt from boring a hole in the wood of the Front Jaw when pressure is applied. It works pretty similar to the pad in a C-Clamp
I applied 2-Part Epoxy to the inside (My common sense tells me that this part is the inside. Google didn't help me out a lot) of the finishing washer, And Clamped it tightly to the Vises Front Jaw, As shown in picture #2
*Let's all give a big Round-of-Applause to Francis Peterson, The man who invented the Finishing Washer! ;)
Step 13: Mark & Drill Holes in the Base (28X22's)
Have you ever seen a Vise that doesn't have a Back Jaw?
I wanted the vise to be able to grip on any sized object, So it was important for me to drill holes in the right places. The range between the minimum jaw opening and the maximum is called the "Dynamic Range"
My dad helped me figure this out: I need the distance between each pair of holes to be shorter than the length of the Eyebolt. This enables me to grip on any sized object. I also was very careful and kept that farthest hole several cm from the edge, To stop the base from breaking.
I used a 10mm Rod (In diameter), Which I previously cut to size with a Dremel at 10cm in length.
The thickness of the base was 5cm, And I didn't want to drill right through it, So I wrapped a small piece of tape on the 4.5cm mark of my 10mm Drill-Bit (I decided to use a 10mm Drill-Bit because this has to be a very tight fit). This way I know exactly when to stop.
I used my Drill to drill all of the holes, While making sure to have the Drill-Bit as perpendicular with the base as possible.
After drilling the holes everything is pretty simple: Choose where to insert the Rods (Based of the piece's size, Put the the Back Jaw (The 16.5 X 6 piece)
Step 14: Oil/Grease the Bolt & Support Rods
It is very important to have the Bolt and Rods oiled properly, It is really easy to do, And significantly improves the overall ease of using the Vise. Oil dramatically reduces the amount of friction, Making it a lot easier to open and close the jaws, And stops squeaks (If there are any).
I sprayed some CG-90 (An amazing Grease Spray!) onto the Bolt and both of the Rods, I also sprayed it onto the Finishing Washer (The part where the Bolt touches)
Note: Oiling should be done on a regular basis (Regular depends on how much you use it), Because the dust from wood can clog up the Bolt.
Step 15: Erasing Pencil Marks, Sanding, & Applying Varnish
Same with all of my previous Homemade Wooden Tools, I wanted to add Varnish (Lacquer can be used too) because it protects the wood.
First, I had to erase the visible pencil marks from the wood, The ones that were made for arranging where to drill the Back Jaws' holes. I did this with an eraser, Obviously.
Before applying almost all kinds of finishes, It's very important to sand very well. Because this isn't a piece of furniture, More like a tool that will probably get scratched quite a bit, It doesn't have to be sanded very smoothly.
Because this has already been sanded with 60 Grit Sandpaper, I began with 100 Grit, And then moved on to 180. Is it true that the same Grit of Sandpaper can sand a softer type of wood smoother? I think that's how it was with this Pine.
I don't know what kind of manufacturer was the genius that decided to make my 180 Grit Sandpaper green, It gave my my Vise a slightly green tint! (Hint-Hint if you're seeing this)
I removed the wood dust* then applied a pretty thick coat of Varnish, Waited 2 hours (According to the Instructions), And sanded it with 400 Grit Sandpaper. Once more, I removed the sawdust, And applied the second coat of Varnish.
Note: I didn't sand the bottom of the base, Meaning that I left it with the blue paint, But I did apply Varnish onto it too, To prevent the wood from possibly warping.
I don't know the rules about painting, But I think that now after the Varnish dries, It is possible to apply paint. I see no reason to do that, Because it just hides the beauty of the wood's grain, But I'm sure some people do like doing that...
*With a secret method of mine that I've invented, Which I will share in a future Instructable :)
Step 16: How to Use the Ultimate Homemade Wooden Vise
I've showed it to several people since I've finished building it, And everyone used it wrong. This is because it should be operated in the opposite way of most people's common sense. Below, I've added a Step-by-Step tutorial on how to use it, With pictures that accompany it (Click Show More)
This is used differently than store-bought Vises, Pay close attention if you make one:
Step #1: Clamp it on to a Worktable. This is the easiest way to keep it portable. (I might use Toggle-Clamps in the future)
Step #2: Install the Back Jaw
Step #3: Put the object (Such as a piece of wood) between the Front & Back Jaw
Step #4: Push the Support rods onto to object without tightening the screw. This is a special feature that allows you to clamp something quickly, Without having it falling apart (While gluing, For example) until you finish tightening the Bolt. This also reduces the friction. This step is pretty similar to the differences between a Bar-Clamp and a C-Clamp
Step #5: Tighten the screw. Because the vise has very wide jaws, You don't have to tighten the jaws very hard to be able to get a good and strong grip. I also have another Instructable, That's coming pretty soon on how to improve the grip even more!
Step #6: USE IT! (And don't forget to enjoy your Homemade Vise!)
But... Does it really work? Find out in the next step!
Step 17: DONE! | But... Does It Really Work? Let's Try It Out...
"Fake!", "It'll Break", "It won't work", "It has no practical use"
Say,WHAT?
I hereby declare that "The Ultimate Homemade Wooden Vise" works, Is extremely strong, And does not break, Even under extreme pressure! I even have an experiment to show that!:
I found a Pine-Cone, And decided to use it for the experiment.
I took the Pine-Cone, Placed it between the jaws, And squeezed the living daylights out of it.
I lifted the whole vise only by the tip of the Pine-Cone as you can see in the picture, Up high in the air.
See! Do you think I would be like that, And lift it up like that if I wasn't 100000% sure that the grip on the Pine-Cone was clamped extremely strong? It could break and smash into pieces if it fell...Let me get something clear: This Vise weighs over 2 kilograms (4.5 pounds)
Unfortunately, My poor little Pine-Cone did not survive the experiment, We brought him to the ICU, But he died there.
Dear Pine-Cone, Please Rest in Pieces (Pun intended!)
------------------------------------------------------------------------------------
Don't forget to Follow me on Instructables, I have over 60 Instructables that I'm sure you'd like!
And a Vote... Is the biggest the biggest compliment you can give me! Thank you so much!
Also, Make sure to let me know if you like it!
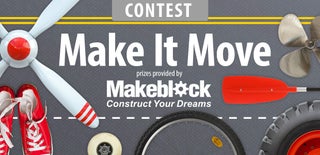
Participated in the
Make it Move Contest 2016
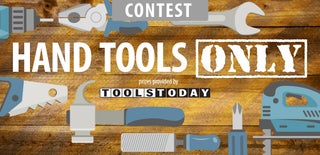
Participated in the
Hand Tools Only Contest 2016
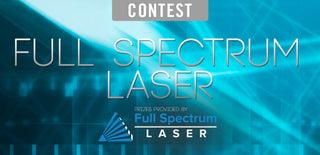
Participated in the
Full Spectrum Laser Contest 2016