Introduction: How to Make the USS ENTERPI
I love to make Pie. I love Star Trek. I love Instructables. There was no way I was going to miss the opportunity to combine these things and more in a culmination of awesomness so extreme it would span an entire week and three workshops before it was complete.
Step 1: Building the Pie Stand
I had an idea, it even made sense. I already owned the awesome Pi dish and knew that would have to be used. To build the stand I would need something that could support the dish filled with pie and provide a framework for the rest of the ship. I decided to brush up on my welding skills and utilize the great shop at my place of employment. I knew I would need scrap metal and had that in abundance, the missing piece was the dish frame. I'll start calling it the saucer support section or SSS.
I did not want to make a wire frame for the SSS so I went to my local Industrial scrap yard. This treasure trove of scrap is a little slice of heaven on earth. I searched around and for $9 ended up with several items that I thought would work and a beat up 10 speed with a vintage child seat on it. Random score.
These are a few pieces that I purchased that were used. On the right is a bent up flower pot support frame, on the left........I don't know but I'll make it work.
Step 2: Creating the SSS
First I used the wire wheel and sand blaster to clean up my metal pieces. Then I bent them and clamped them for welding. At the shop I used a Millermatic 130 welder. Great piece of equipment. I used my pie dish fore measurements and carefully bent the metal to create the support frame. When bending tubing be carefull not to gink it. You can do this several ways. If it is thin enough you can insert it in a long spring and bend the spring. This works well for solid brake lines on cars. For my job the metal was solid so I used what was handy, the round body of a large electrical motor.
Step 3: Turbo Lift Tower
For the neck? of the ship I used rectangular tubing left over from my last project. At this point I had to worry about scale so I went online and found some images of the Enterprise. I chose line drawings that I think are from the various manuals on the Enterprise. Then, using my pie dish as the saucer section I took some measurements. Based on the printout I had and the size of my pie dish the conversion was 2.32:1. I used this conversion to measure the drawing and then multiply by 2.32 to get the size I needed.
I knew I would need a large base to keep the Enterpi from tipping so I just chose a piece of flat steel to work with, knowing I would screw it to a larger wood base later on. The plant stand I used really went well with the rectangular steel tubing so no clamping was needed when I welded it in place.
I also pre drilled the base when it was not welded to the turbo lift tube because nothing sucks more than having to hand drill an awkwardly shaped piece of metal.
Step 4: Engine Supports and Nacelles
The Enterpi is taking shape. For the supports and the nacelles I used 1/4 inch steel rods that I also got at the scrap yard. I did the measuring thing and this time I had to deal with angles. Remember the mantra, "measure twice, cut once". In my case it should be measure 7 times, then measure again, then cut. More on that later.
Step 5: Paint!
So now I had a frame that looked like the enterprise and held a pie dish. The Enterprise is white and so I knew the top should be white. I chose black for the bottom so it would not stand out. All the metal was sand blasted before welding so before paint all I had to do was grind down the welds. The better you are the less grinding you do. I do a lot of grinding. Before I added paint I wiped the whole thing down with alcohol to remove any oil. I gave it a quick coat of primer, then the white, then the black. I gave each coat time to dry but was not too concerned with the transition areas as they would be covered by the body of the ship.
Yes XTina, that is your BM bike back there.
I have to add here that when I started on the body, see next step, I realized the engine supports were at too much of an angle. I had to bring it back to work and use the vice to bend the engine supports more virtical down low and then flared about 4 inches up. A little touch up paint and it was good as new.
Step 6: Building the Body
I chose to make the body and necelles of the ship out of foam insullation because thats what I had around. I picked up three sheets of 2 inch thick high density foam at the scrap yard last year planning to make a furry costume. See you use this stuff to make the base for the head, stacking it and glueing to get the size you need and then you carve. You then cover with the fur...............I digress, that would be a whole other instructable that I may never write. Back on track, I had the foam and was not afraid to use it. I made more measurements and sketched the basic shape on the foam. I then carved as much as I could using a serated bread knife and a pumpkin carver tool. After I had the basic shape I used 220 grit sand paper to fine tune the shape. I had never sanded foam before and may never do so again. While it works great and you can get amazing detail, it will kill you. Sanding creates fine particles of foam that are filled with nasty stuff that just wants to see you dead. Wear a resperator, a dust mask won't cut it. I was planning on having more detail but gave it up when I realized it would take days off my life to create them. I am willing to suffer for my craft but that only goes so far.
So after the body, nacelles, and various bits were made I used cement to glue them together. This project was just filled with toxic, my next instructable should be for body cleansing enemas made from organic ingredients, antioxidants, and crushed fairy wings just to make up for it.
To fit the pieces of foam to the metal frame I had to slice and carve them. This could have been done better but I was winging it and figured I could just add more glue and foam to fill any holes. To secure the pieces to the frame while the glue set I used my daughters hair ties. Most of them were these little rubber bands that always break and come in a bazillion pack. Where they contacted the glue they kept breaking so I kept adding more until the nacelles looked like tortured sausages that were celebrating diversity.
Step 7: Painting the Details
After all the details were added and the glue was dry it was time to paint. I tested Testers model paints and acrylic poster paints on a piece of foam and neither caused it to melt. If I did it again I would look for a water based primer in white as a base coat. I was out of time and did not already have the primer so I went with what I had. both paints worked ok. Its foam so nothing goes on smooth and it absorbs some of the paint. Because of this I went with the acrylic poster paints. These come in lots of colors and you can buy small or large containers of it in many places. Mine came from yard sales cause thats how I roll but if I needed to get a specific color and I could not mix it myself I would try my local art supply store cause its worth paying a little more to keep a great resource in business.
During the painting process I realized what my nacelles looked like and will never look at them the same way again. I was glad that the end result retains none of that and now look like the futuristic engine it is, capable of warp 6.
Step 8: Making It Not So Tippy
I knew that I would need to add a larger base to the Enterpi or else it would tip over. I decided on wood because it would be easier than a large metal base. I told my friend Brian about my project and asked if I could cut the wood over at his place. He has a garage set up for woodwork. He agreed and also offered to check his supply of wood. Later that day he emailed with the suggestion to make the base a large Starfleet emblem and the light went off. To do this I needed a large stencil to trace on the wood. Once again I went to the internet and found a nice line drawing. Utilizing my office resources I printed out a 24 x 16 image of an early Trek emblem.
I gave Brian the stencil on Friday and when I went by on Saturday afternoon he had cut out the wood with a jigsaw and prepped it for paint. I added a coat of black spray paint to the 3/4 inch plywood and left planning on picking it up on my way home. Later that day I picked it up with my cargo bike, I should have done an instructable of that but did not take enough pictures of my process. Along with the base I also go 2 beers!
When I got it home I taped off the edge with masking tape and sprayed it with gold. After it dried I pulled the tape off and presto! Starfleet emblem base!
I used a few wood screws and washers to attach the base and things were really looking good. The Enterpi - Pie was done.
Step 9: So Lets Get to the Pie Already
I decided on making this an open faced pie and I love blueberries. My grandparents lived in Ohio and my grandfather had 4-6 blueberry bushes that were huge. I remember Grandma making blueberry pie when we were out there and have loved them ever since. Last year I got this recipe and it became a favorite. To make this amazing blueberry pie you need:
6 cups blueberries rinsed. You can substitute 3 cups frozen but look for big ones.
1/2 cube (2 oz) butter
4 1/2 tablespoons lemon juice
3 tablespoons flour. (cornstarch will also work for a gluten free pie)
1/4 teaspoon salt
3/4 cup granulated sugar
3/4 cup brown sugar
Pie crust.
The bacon is there to give my kitchen some class.
Step 10: Roll Out the Dough and Pre Bake the Crust
This pie only has a bottom crust so make it a good one. Store bought will work fine and is easy to work with but I have a recipe I like and it is what I used for this. I'll make an instructable for the pie dough in the future. I have a great regular and gluten free crust. Soon, I promise you, soon.
Remove the dough while still cold but not frozen. The trick is to get it rolled out and into place before the vegetable shortening starts to get sticky and soft. Using plenty of flour roll it out and place it in the pan.
Trim the crust and ball up the scraps and put them back in the freezer for a quick cool down. Poke holes in the crust with a fork to minimize puffing while it cooks. To maintain its shape also add a layer of tinfoil to the crust and then a bag of beans or pie weights. I don't own pie weights but I do have beans. In fact these are quadruple baked beans as I have used them in the last 4 pies I have made. Just let cool and rebag for later use.
I then turn the oven on to 450 degrees. While the oven is heating I put the pie pan with crust and beans back into the fridge. Now take the small ball of pie dough out of the freezer and roll it out. I freehanded to bridge section out of this piece and placed them on a pan with parchment paper so they won't stick.
When the oven is hot put both the pie pan and the cookie sheet with the bridge section into the oven. Check after 10 minutes and cook until brown on the edges. Mine took about 13 minutes.
Step 11: The Filling Is Where the Love Goes
Now this is the heart of the pie so make it with good ingredients and lots of love. This can also be done in advance.
Combine 3 cups blueberries (frozen ok), butter, and lemon juice in a nonreactive saucepan. Cook over medium heat until the berries release their juice. Trust me you will know.
Add the flour. If using cornstarch mix with a tablespoon of water or it will clump. Add the salt, and both sugars and cook until the mixture thickens. Add a little more flour or cornstarch until you get the consistancy of a heavy syrup.
Remove from the heat and let cool. Fold in the remaining 3 cups of fresh, NOT FROZEN, blueberries into the cooked mixture and gently pour into the baked pie shell.
Cool until set.
Step 12: Behold! the Starship ENTERPI!
And now I am the proud owner of the coolest pie display stand ever. Thank you for checking it out and thanks to Instructables for such a great website. I am glad to be a part of it, plus I have some good pie to eat.
The sensor array was added after the pie was set. It is attached with double sided tape.
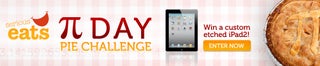
Second Prize in the
Pi Day Pie Challenge
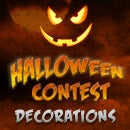
Participated in the
Halloween Decorations Contest
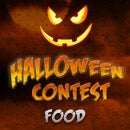
Participated in the
Halloween Food Contest