Introduction: Hummingbird
Hummingbird is a hummingbird themed automata I designed for my wife, who smiles from ear to ear while feeding and watching the gathering hummingbirds at our home. Hopefully it will bring smiles to many more faces.
Hummingbird consists of 97 3D printed parts (38 unique parts) and, as I discovered, requires plenty of time and patience to print, assemble and tune. Along with the 3D printed parts, Hummingbird also requires a "uxcell 16mm DC 6V 60RPM Speed Torque Gear Box Electric Motor for Robot" (available from a variety of sources), a 6vdc power source, and four 1/4" or thicker stick on felt or rubber pads (for the base).
The file "Images.zip" contains all cad images and photographs included in this Instructable.
As usual, I probably forgot a file or two or who knows what else, so if you have any questions, please do not hesitate to ask as I do make mistakes in plenty.
Designed using Autodesk Fusion 360, sliced using Cura 3.2.1 and printed in PLA on both an Ultimaker 2+ Extended and an Ultimaker 3 Extended.
Attachments
Step 1: Print the Parts
I've included file "Hummingbird Parts.htm.zip" which contains the parts list and print parameters I used to print Hummingbird.
I've also included the file "STLs.zip" which includes all the parts in stl format.
Hummingbird is a high precision print and build. Prior to starting assembly, test fit and trim, file, sand, etc. all parts as necessary for smooth movement of moving surfaces, and tight fit for non moving surfaces. Depending on the colors you chose and your printer settings, more or less trimming, filing and/or sanding may be required. Carefully file all edges that contacted the build plate to make absolutely sure that all build plate "ooze" is removed and that all edges are smooth. I used small jewelers files and plenty of patience to perform this step.
Hummingbird uses threaded assembly, so a 6mm by 1 tap and die may be needed to clean the threads.
And finally, I used petroleum jelly judisiously on the gear train and between the rotating contact surfaces.
Attachments
Hummingbird Parts.htm.zip
Arm Base Left.stl
Arm Base Right.stl
Arm Body Front.stl
Arm Body Rear.stl
Axle Wheel Base.stl
Axle Wheel Body.stl
Base.stl
Body Left.stl
Body Right.stl
Bolt 6mm, 8mm head, 4mm shoulder.stl
Bolt 6mm, 10mm head, 4mm shoulder.stl
Bolt 6mm, 12mm head, 8mm shoulder.stl
Bolt 6mm, 12mm head, 23 mm shoulder.stl
Bolt Pivot Shoulder.stl
Bolt Pivot Wing.stl
Bolt Wheel Base.stl
Bolt Wheel Body.stl
Bushing Axle Gear Base Long.stl
Bushing Axle Gear Base Short.stl
Bushing Wheel Body.stl
Flower.stl
Gear Compound (60, 20 Teeth).stl
Gear Motor (10 teeth).stl
Gear Wheel Base (60 Teeth).stl
Gear Wheel Body (30 teeth).stl
Pivot Shoulder.stl
Pivot Wing.stl
Rod Connecting 6.3mm Hole.stl
Spacer 8.2mm.stl
Spacer Axle Gear Compound.stl
Spur Gear (30 teeth).stl
Stem.stl
Tail.stl
Wheel Base.stl
Wheel Body.stl
Wing Left.stl
Wing Right.stl
Axle Gear Compound 60, 20.stl
STLs.zip
Flower.f3d
Rod Connecting 6.3mm Hole, 2.2mm thick.stl
Step 2: Assemble the Base
Press "Gear Motor.stl" onto the motor, then press the assembly into "Base.stl".
Assemble "Gear Compound (60, 20 Teeth).stl", "Axle Gear Compound 60, 20.stl" and "Spacer Axle Gear Compound.stl" as shown, then lace the assembly into the base and secure with two "Bolt 6mm, 8mm head, 4mm shoulder.stl" as shown.
Assemble one "Wheel Base.stl, "Axle Wheel Base.stl", "Bolt Wheel Base.stl" and "Bushing Axle Gear Base Long.stl" as shown. Position "Gear Wheel Base (60 Teeth).stl" in the base as shown, then slide the assembly through the Base, Gear Wheel Base (60 Teeth) and the Base as shown. Insert "Bushing Axle Gear Base Short.stl" onto the free end of the Axle Wheel Base, followed by the remaining "Wheel Base", then secure with the remaining Bolt Wheel Base.stl.
Finally, apply four 1/4" or thicker stick on pads to the bottom of the base, one in each corner.
Step 3: Assemble the Transmission
The first image shows (left to right) "Bolt 6mm, 12mm head, 23 mm shoulder.stl", "Arm Body Front.stl", "Arm Base Right.stl", "Spacer 8.2mm.stl", "Spur Gear (30 teeth).stl", "Arm Body Front.stl", "Arm Base Left.stl" and "Bolt 6mm, 12mm head, 23 mm shoulder.stl".
Position "Arm Body Front.stl" and "Arm Base Right.stl" as shown, then slide "Bolt 6mm, 12mm head, 23mm shoulder.stl" and secure loosely in place with "Spacer 8.2mm.stl" as shown.
Position "Spur Gear (30 teeth).stl" onto the spacer.
Complete the assembly with the remaining components as shown.
Step 4: Assemble the Body
Securely attach nine "Spacer 8.2mm.stl" to "Body Right.stl" using nine "Bolt 6mm, 8mm head, 4mm shoulder.stl".
Assemble "Bolt Wheel Body.stl", "Wheel Body", "Bushing Wheel Body.stl" and "Axle Wheel Body.stl" then position on "Body Right.stl" as shown.
Place three "Spur Gear (30 teeth).stl" onto the assembly as shown, then secure "Body Left.stl" to the assembly using nine "Bolt 6mm, 8mm head, 4mm shoulder.stl".
Finally, attach the remaining "Bolt Wheel Body.stl", "Wheel Body" and "Bushing Wheel Body.stl" parts to the assembly as shown.
When complete, the gears must rotate easily.
Step 5: Assemble the Wings
Position "Pivot Wing.stl" onto "Pivot Shoulder.stl" and secure in place with "Bolt Pivot Wing.stl" as shown. The shoulder pivot and bolt must rotate easily in the wing pivot.
Position "Wing Right.stl" onto "Pivot Wing.stl" as shown, then secure firmly in place with "Bolt 6mm, 10mm head, 4mm shoulder.stl" as shown.
Snap the small end of "Rod Connecting 6.3mm Hole.stl" onto the ball on "Pivot Wing.stl" as shown.
Position the assembly on "Body Right.stl" as shown, then secure in place with "Bolt Pivot Shoulder.stl" as shown.
Snap the large end of "Rod Connecting 6.3mm Hole.stl" onto the ball of the right body wheel as shown.
Repeat the assembly process for the left wing, then attach the left wing assembly to "Body Left.stl" as was the right wing.
Step 6: Attach the Transmission to the Base
Slide "Spacer 8.2mm.stl" into "Spur Gear (30 teeth).stl", then position the assembly into the base as shown.
Position the transmission assembly on the base, then secure in place with two "Bolt 6mm, 12mm head, 8mm shoulder.stl" as shown.
Position the right and left base arms on the base wheels as shown, then secure in place with two "Bolt 6mm, 10mm head, 4mm shoulder.stl" as shown.
To test the assembly, remove the motor and make sure the gears turn and the transmission pivots freely. Reinstall the motor, and attach a 6vdc power source to the motor such that the right "Wheel Base.stl" rotates clockwise as viewed from the arm side of the wheel.
Step 7: Attach the Body to the Transmission
Attach the two "Arm Body Rear.stl" to the base assembly using two "Bolt 6mm, 12mm head, 8mm shoulder.stl" as shown.
Slide one "Spacer 8.2mm.stl" into "Tail.stl" as shown the position the assembly into the body assembly as shown.
Slide one "Spacer 8.2mm.stl" into one "Spur Gear (30 teeth).stl" as shown, the position the assembly into the body as shown.
Lower the body onto the front and rear body arms an secure loosely in place using four "Bolt 6mm, 12mm head, 8mm shoulder.stl" as shown.
Step 8: Attach the Stem and Flower to the Base
Press "Flower.stl" onto "Stem.stl" as shown, the press the assembly into the base assembly as shown.
Hope you enjoy Hummingbird!
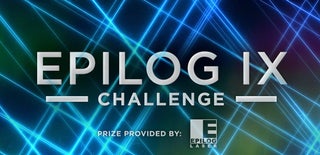
Participated in the
Epilog Challenge 9