Introduction: Hurricane Balls, 3000 Rpm+ Spinning Toy.
UPDATE: Read step 7, It shows a better build method and has a link to an Ible that shows how to make the jig.
I also posted and Ible on how to join ball bearings with soft solder here.
I discovered this fun little toy while surfing around the net in the wee small hours last night on a site called www.grand-illusions.com
Hurricane balls are just 2 ball bearings joined together, when spun on a flat surface and then accelerated by blowing a jet of air at them will spin up easily to around 3500 rpm. over 12,000 rpm have been recorded in lab conditions
I was so amazed by this fun little toy that I decided that once I had managed to get some sleep that I would try and build a set of these.
Its a fun little project that is so much fun to play with. Sadly my camera is not high enough spec to really show this thing of, I will try and get a high def video posted asap.
This is quite a simple build but need to be built well as they can reach over 3000rpm if you really blow hard and this provides the potential for mayhem if the balls decide to separate at this speed.
Parts list:
2 matching ball bearings about 12 - 15mm diameter.
1 3mm machine screw.
1 Biro pen, makes a great blow pipe.
A concave mirror to run it on, a flat surface will do but it will work better on a concave surface.
Superglue, this is optional but is a good idea to help lock the threads in place.
Tools used.
:
Drill press.
2.5mm drill bit.
3mm tap and tap wrench.
2 pair of pliers
Junior hack saw.
Small flat needle file.
The retail version of these are welded together with about 8000amps of current, I did not 8000 amps available and it sounded a bit dangerous to boot so I decided to go with with what I had at hand and went down the bolt it together road.
I have since noticed that there is another Ible for hurricane balls using epoxy to glue the balls together. I just dont have faith in epoxy on metal to metal (or any non-porous surface) when high rpm and centrifugal forces are at play, there is the possibility of a high speed detachment. while your face is a few inches from the source of mayhem. The contact area between the 2 balls is just to small to trust the bond the epoxy would have.
Have fun, play safe and I hope you liked this Instructable.
Step 1: Disclaimer.
If you try to recreate this instructable, you do so at your own risk.
Because this Instructable involves high speed centrifugal forces there is a risk the balls may separate and fly off at high speed.
We have already had our first high speed separation of homemade Hurricane balls when spun to very high speed with an air compressor.
Step 2: Finding the Right Type of Ball Bearing.
Ball bearing is a generic term for any perfectly spherical metal ball.
There are several types of ball bearing available. but most balls that have been taken out of automotive or industrial bearings are most likely to have been hardened.
There are 2 types of hardened ball bearings, case hardened where the outer shell of the ball has been hardened and the center core is still soft and fully hardened which does exactly what it says on the tin.
I was lucky to have some soft steel ball bearings that where part of a Magnetics set that i have long since pilfered all the small neo magnets out of.
You can remove the temper from hardened ball bearings by heating them up until they are almost white hot and then allowing them to cool as slowly as possible. Its not the easiest thing to do but if you cant get soft steel balls it may be the only option.
Bikerbob2005 says :
to remove the hardening :
a bucket of sand a charcoal grill get the grill hot with the bucket of sand sitting on the coals drop the bearings into the red coals when a magnet will not pick them up use tongs to grab them and stuff them deep into the hot sand.put the lid on the grill let the fire go out on its own and sand cool for a day .the bearings will then be "dead soft" and drill will work fine
after drilling/tapping bearings go back into charcoal till magnet does not stick ,toss them into a bucket of motor oil.
if charcoal not getting hot enough then use a shop vac to blow on them.
I have forgotten the methode we where taught at the Tech I but Bob's comment sounds right.
Step 3: Drill.
First you will need to drill a 2.5mm hole is each ball bearing.
This is not the easiest of tasks to do.
I used a large nut to rest the ball bearing on and then just eyeballed it as best as I could.
It may be a good idea to have some spare ball bearings just in case you mess things up.
Try and drill the holes exactly the same depth in each ball as you want them to be as balanced as possible.
I drilled the ball about 8mm deep so I could get about 4-5mm of thread in the hole.
Step 4: Tap.
You now need to tap the holes in each ball to accept a 3mm machine screw.
Because this is a blind hole you will not be able to thread it all the way to the bottom so the hole must be a few mm deeper than you want the threads to be.
With the holes drilled to about 8mm deep I was able to thread the holes to about 4-5mm.
Step 5: Join.
Now screw the 3mm machine screw into one of the balls until it is tight.
Now mark the screw where it protrudes from the ball and remove the screw to see ho deep it was screwed into the ball. You now now how much thread on the screw to attach the second ball.
I had about 3-4mm of screw threaded into the ball so I screwed the machine screw into the ball and tightened it up (you can add a drop of superglue into the hole at this point if you want it to be extra tight.)
I then cut the screw down to size leaving about 4mm protruding out of the ball.
Once the screw has been trimmed down file the end of the thread to remove any burrs.
Now screw the second ball onto the protruding thread.
use 2 pairs of pliers to tighten the balls together until they are flush with each other.
Caution do not use to much force or you will wring the machine screw off like I did on my second attempt.
Step 6: Play.
Now you have a set o Hurricane balls that you didn't have to pay for. Hurrah! I hear you say.
To use the Hurricane balls you spin then on a flat surface and then use the a blow pie to blow a jet of air at them from a few cm away.
You should easily get the balls to spin up to a few thousand rpm.
They will spin for about a minute and then stop abruptly.
Have fun, and enjoy.
Try them out using an upside down sweetie / cookie tin as the flat surface, it sounds amazing.
I used a Roses tin left over from Christmas it sounds like a big v12 engine at full throttle
Step 7: Better Build Method Using a Drill Jig.
As this Ible has become popular and there has already been one case of high speed separation I decided to see if I could build a better quality set using a drill jig to allow me to drill the balls much deeper and uniformly so to allow for a better amount of thread in each ball.
Making this simple yet very effective jig is covered here.
The drill jig allowed me to drill perfectly centered holes to a depth of 10mm.
This in turn allowed me to have good quality thread in the holes to a depth of 6mm before the threads start to taper, this taper also helps give a very strong grip on the ends of the screw.
The jig allowed the balls to fit together in perfect alignment. which also aided how well the 2 balls could be screwed together.
Once the balls where screwed together to a hand tight fit i used pliers to give them 1/4 turn more to lock them in position.
This better built set of Hurricane balls are much easier to get up to speed with less amount of lung power.
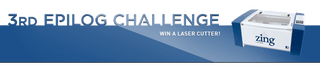
Participated in the
3rd Epilog Challenge