Introduction: Inexpensive, Easy to Build, Peristaltic Pump
Why Peristaltic Pumps? Peristaltic pumps are great! They require no priming, they can pump uphill, they can pump viscous liquids or fluids that have 'chunks', require no special materials, and can be cleaned/sanitized very easily. In short, they may be the perfect pump for the home brewer!
Learn more here http://en.wikipedia.org/wiki/Peristaltic_pump
How Peristaltic Pumps Work? Peristaltic pumps work by squeezing a tube like you might squeeze a tube of toothpaste - except in this case the tube is a 5-foot-long silicone hose, with as much "toothpaste" as can fit in your bucket. This squeezing action is called 'occlusion'. Usually, you get this squeezing force by pressing the tube against the wall of the housing with a roller. The number of rollers in a pump determines how much fluid gets pumped for each pulse, the more rollers, the more pulses per revolution, the less fluid per pulse. All things being equal you get less fluid per revolution with more rollers, but smoother output. More rollers can also reduce the hose life.
Why build your own? As mentioned previously, peristaltic pumps don't require special materials, but there's a serious dearth of manufacturers building for the home market. You can buy little peri pumps for lab use or giant ones for industrial use, but not much in between. So, if you need to pump some wort around, want to water cool your laptop or just want to make a pump you can take with you and power with a drill, then a peristaltic pump may be the answer.
Ready to have a go? Follow along and get pumped up! (har har)
Here's some info on my setup:
Test1:
Test 2
A 'tour' of the pump
Step 1: Mise En Plas
Here's my materials list you can probably edit for what you have available:
- 1x 9.5" springform cake pan - I got mine from goodwill, but you can get similar from http://www.webstaurantstore.com/9-1-2-light-tin-sp...
- 4x 2" casters from harbor freight http://www.harborfreight.com/2-inch-x-7-8-eighth-i...
- 5 ft silicone hose from the local home brew shop - it's 1/2"ID, 3/4"OD IIRC
- A block of wood - nothing special, I'm using an offcut from an ikea hack. It's 1 1/2" deep. You could easily use a 2x4 off cut. You may just need to make more cuts. A much larger piece of wood will necessitate a longer bolt, too.
- 2 large (1" or larger) washers and 2 small (1/2" or so) washers. If you have large fender washers, that will work,too. These act as bushings, so don't skip there
- 2 1/4" -20 t-nuts
- 2 1/4" -20 nuts, or 1 nut and one cap nut.
- 1 1/4"x 3" - 20 bolt
- 8 #12x 3/4" wood screws
- Zipties (what project doesn't need a few zip ties
- Hammer
- compass
- drill
- drill bits
- dremel tool or similar with grinding stone and cutting wheel (I really like the reinforced cutting wheels because they are less likely to break apart and poke my eye out)
- 7/16 socket/rachet
- 7/16" wrench
- 7/16" drill driver (if for some reason your 1/4" bolt and nuts have a different head size, you'll need a different size set of drives)
- screwdriver
- tsquare or framing square
- circular saw, chop saw, table saw, hand saw, or laser vision
- Coffee!
Now, let's begin!
Step 2: Cut and Drill Roller Mount
- Begin by laying your block of wood in the cake pan with your casters (rollers).
- Figure out the size your wooden block needs to be to mount all 4 rollers, in my case it was 3 3/16" square
- Measure twice cut once. Use the framing square to mark your cuts, then use the table saw to cut the block of wood to size.
- Use framing square to mark midpoint of your square. This step is important, so measure 3 times. one half of 3 3/16" is 1 19/32" that's a real PITA to find on a rusty framing square. Life goes on.
- Drill a hole in the middle of your square of wood.
- Now drill a bigger hole.
- You may need to drill out the very top and bottom of the hole to accommodate the the t-nuts
- Now insert the t-nuts. The BFH comes in very handy for this operation to help 'seat' the t-nuts. You can also thread in the bolt and nuts on either side, tightening them will help tighten down the t-nuts. The t-nuts are very important to the drive system at this point, so don't half-ass this step.
- Remove the bolt, not doing so makes the next step more difficult.
Step 3: Drill & Mount the Casters
- Take the wood block and decide which side is "up" it doesn't matter which, just go for it, you wild man/woman, you!
- Lay the block face up on a horizontal surface. The floor works just fine. If the block is wobbly because of the T-nut, just place one of those big washers underneath at the center.
- Place each of the casters up against the block, as evenly as possible.
- Now mark the center of the hole with a pencil, drill bit, or center punch. Or all three. Why not? Go wild!
- Once all the holes are marked, drill the holes for the screws. I forgot which drill bit I used, but since the wood screws are #12, it was probably 5/32 or 5/16. Drill the holes at an angle so that the evens are angled up and the odds are angled down. This is easier if you start with a small drill bit and step up to a larger one. The reason for doing this is so that the screws don't hit each other. Alternatively, you could uses a larger caster with more mounting holes and alternate them, couldn't you, big spender!
- Once the holes have been drilled, line up the caster with the holes and screw them down. You did remember to mark which caster went with which side of the block, right? Tighten the screws slowly, going around to each caster until everything is cinched down, you don't want to strip your wood.
- Now that the casters are mounted they should be relatively flush with the bottom of the wooden block.
Step 4: Put Some Holes in Your Housing
- Take out the bottom of the springform pan. It should be round and flat. If either of those statements don't apply to your cake pan, you may need another one.
- Find the center of the cake pan. Using a compass, stick the point on the edge, and use a scribing tool (or drill bit, or pencil, or...) to mark and arc. Now move the point to another point on the circumference of the circle. Make another arc. Repeat twice more. Where the arcs overlap will define where the center is. Now tighten up your arcs by making the compass angle bigger or smaller and repeat. Eventually you'll have a tight # shape that defines the center of the circle. Put your hole there.
- Drill out the center of the cake pan bottom. I like to start with a spring loaded center punch. It's pretty thin metal so be careful drilling as you can get little bits of metal going everywhere.
- Smooth out the hole with some dremel grinding.
Step 5: Mount the Roller Assembly to the Housing
- Start by adding your washers to the bolt that goes through the wooden block. I happened to have 2 that fit one-inside-the-other. If you don't, that's okay. A fender washer should work just as well.
- Insert the bolt through the hole in the cake pan bottom. Make sure you have it going the right way. There is a "top" and "bottom" on cake pan bottoms - who knew?
- Add washers to the underside of the bolt. Again, one inside the other.
- Thread on your nuts. I use two, one to go snug against the washers (not tight, it needs to allow the bolt to spin!), then another snug against it. Then loosen the first nut (the one on the underside of the cake pan bottom), so that it tightens against the top nut. There's a name for this technique, but damned if I remember. If you had a cap nut, this would be a good place to use it for a more finished look, and to allow an easier time driving from the back, since you wouldn't have to worry about overtightening the nuts and locking everything up.
- You now have a roller assembly, huzzah!
Step 6: Cut Some More Holes in Your Housing
- Figure out where you want your holes. I figured I wanted mine at about 10 and 2, like driving. I put the holes on either side of the spring catch mechanism, so the rivets wouldn't hit the tube. Make sure you are avoiding the catch itself as well as the part that slides in/out.
- Draw some rectangles near the bottom of the pan walls, where the rollers will be. I used a drill bit as a scribing tool again. Ensure that your tubing will fit through the holes.
- Cut out your rectangles with a dremel-type tool. Leave one edge attached. This will be how you mount the tubing.
- Bend out the tabs.
- Grind away sharp edges.
- Now insert your hose.
- Zip tie the hose to the tabs.
Step 7: The Marriage
Here's the fun bit... the end!
- Drop the top onto the bottom. Or vice versa, you rebel! The tubing will sit on top of the rollers, but that's ok.
- Cinch down the springform mechanism, ensuring the bottom of the pan is aligned with the groove in the bottom part of the side.
- Turn the pump assembly a few times by hand. The tubing should be pulled down to squished...erm...occluded by the rollers.
Now you can go pump something!
Attach that 7/16 driver to your drill, put the drill in forward drive, put the drill on the bolt and give it a few spins. Now put the inflow end of the tube in some liquid to pump, then goose the drill up slowly. You should be pumping!I hope that has shown you how you too can build a cheap, awesome, peristaltic pump at home! Good luck :)
Step 8: Next Steps?
The next steps are to try some different power sources, like an ac or dc gearmotor.
Try doing some wort pumping, see if hot wort hurts the systems performance.
Maybe experiment with different materials. Different casters, different pans, etc
Try a more robust "hub" . I'd love to try a nice bit of bent steel, but setup costs are expensive for a one-off
Whatever you guys think - I'd love to hear your suggestions!
Thanks,
JR
Acknowledgements:
Big ups to those who have inspired this work, particularly Bumbler and TheFlyingBeer over at homebrewtalk.com
http://www.homebrewtalk.com/f51/cake-pan-skateboar...
http://www.homebrewtalk.com/f51/spring-loaded-peri...
I wouldn't have thought such things were possible without other netizens blazing a trail and showing their work - Thank you.
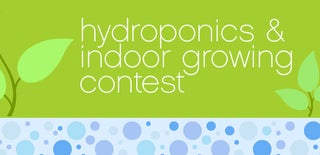
First Prize in the
Hydroponics and Indoor Gardening Contest
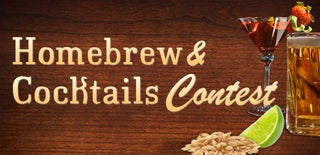
Participated in the
Homebrew & Cocktails Contest