Introduction: Intro - How to Design and Build a Bamboo Cargo Bike (Box Bike - Bakfiets).
The bakfiets is an incredible machine. I was turned onto these bikes by Josh Muir of Francis Cycles. It is the ultimate for every day errands, grocery store trips, and hauling children around. It fits in the bike lane, it is nimble and quick, and is a pleasure to pedal. I am loving it and seriously think a car free society will rely on these puppies in addition to normal bicycles.
After trying a trailer, backpack, and rear seat, I think the bakfiets is the best way to transport children. Although there are some concerns...(see step 6 for some ideas on the safer ways of placing children in the box).
This instructable is all about how to design and build a bakfiets style cargo bike. The design tips apply to any bakfiets style cargo bike and there is no need to build it out of bamboo. I like the ride quality and uniqueness of bamboo. However, if I do it all over again I might use steel... Building a bakfiets is like building three normal bikes. The amount of epoxy and sanding seemed to add up. I think my next bike may be fillet brazed steel.
Here is the breakdown:
Cost: $600 (including components - mostly used)
Time Frame: 4 months
Useful links:
Larry vs. Harry Bullit
the dimensions of the bullit
Francis Cycles
Tom's Cargo Bikes
My Instructable
Bamboo Bike Blog
https://www.instructables.com/id/Long-John-Cargo-Bike/
https://www.instructables.com/id/build-a-2-wheel-cargo-bike/
Sources for materials:
Epoxy: West Marine (I used West Systems but I think I should have tried this: http://www.entropyresins.com/products/super-sap-clr - half the price of West System 105)
Hemp:http://www.hemptraders.com/
Bamboo: local bamboo nursery
Drop Outs and Tube: Nova Cycle Supply : http://www.cycle-frames.com/bicycle-frame-tubing/home.php
The art of building bamboo bikes has really come a long way. I have realized that my technique from 2008 is probably not worth emulating. I strongly recommend that you look at the Bamboo Bike Blog and other instructables for the next level of building with bamboo. I particularly like this instructable by kentdvm:
https://www.instructables.com/id/Building-a-Recumbent-Bamboo-Trike-Frame/step20/Finishing-the-Bamboo/
So let's get started!
Step 1: Design Geometry
In designing a bakfiets there are few constraints when it comes to size and shape. There are however some real constraints - you don't want the pedals to hit the road when you go over a small bump or turn the corner. You also don't want the basket to hit the road when you turn the corner. Width is another issue. I went with much the same width and geometry as the bullit. Steering is another big design consideration/constraint.
The design concept of the bakfiets is that you have two wheels (which makes the bike nimble and easy to steer and ride) and a low center of gravity which makes it very stable.
Wheel size - smaller theoretically means more stability. I went with a 20" wheel in the front and a 26" wheel in the back. I have heard of some people using a 20" rear wheel, although I have never seen this. There are a few different sizes that are all called 20". The front wheel I used is a 406 mm rim diameter. This seems to be the most common 20" size and there are a lot of bmx tires and recumbent tires readily available.
Bottom Bracket Height - 265 mm - this should probably be 30 to 50 mm higher. When I drew the bike out I had this as 290 mm but somehow in building the bottom bracket came down. This may have something to do with skinny tires I ended up using. I do get pedal strike when turning corners sharply or pedaling over speed bumps.
The basket is pretty low (150 mm). The lowest point however is the bottom of the steering tube (120 mm) I am pretty sure this has never struck a bump in the road.
The bike is 580 mm wide. This is no wider than many mountain bike handle bars (600-700mm).
Below is the geometry of my bike as it is built. So far the only issue with the geometry is the bottom bracket height - this really not too big a deal and I subconsciously keep my pedals up when going over speed bumps. The bike may be unnecessarily long. There seems to be a bit of spare room between my knees and the basket.
Another thing I did was slope the seat tube back to allow me to keep my butt on the seat and still have my feet reach the road. This makes stopping and starting much more comfortable.
I have long chain stays which are not really necessary. This was a half baked idea to get more tire clearance by moving the wheel back. (I ended up messing up a bit and don't have the tire clearance I would like.
I would design the bike to accept big tires even if you end up riding skinny tires.
The bike is surprisingly upright in the turns and unlike a normal bike the bakfiets is steered with the front wheel and not by leaning over. Because of this you almost always have to have at least one hand on the bars at all time and really need to to have your butt on the seat for stability.
It is slower but I am enjoying learning to take my time on the rides. One big advantage has been the added effort required to get around. My daily commute on my road bike is not much of a work out anymore. Now on the bakfiets I am getting a workout again. My 5 mile trip to work takes me just under half an hour on the road bike and just under 40 minutes on the bakfiets.
The attached pictures show the geometry of the bike and some ideas on design changes you can make if you go with cable steering instead of rod steering. I chose rod steering and a very rectilinear design - this works particularly well with bamboo. If I used steel I would definetly added some curves because curves are pretty. Josh Muir's bikes are works of art.
Steering is discussed in more detail in step 3.
Step 2: Design Details
I used a bottom bracket cut out of an old steel bike.
All of the bearing surface need to be metal - the two headsets and seat post. The forward headtube is all metal. The headtube that supports the handlebars is bamboo with metal tubes epoxied in top and bottom. To get the metal tubes epoxied in place I wrapped masking tape around the steerer to keep it centered when tacking the tubes in place.
Brakes: with all the extra weight I strongly recommend disc brakes. With the long distance between the brake lever and the brake itself the cable seems to stretch quickly. It may be a good idea to go with hydraulic disc brakes. Personally I like the simplicity of cables and feel like it is not a huge expense to replace cables every six months.
The earlier you figure out which front derailleur you are going to be using the better. I did mine as an afterthought and I only have access to two of the three rings and ended up making a special top pull road bike mount derailleur out of two different derailleurs. This is something I will eventually have to fix.
I also had this idea to add little stays between the chain stays and the seat stays for added strength. Oops, the chain moves quite a bit when you change gears. The drive side stay has a huge cutout in it to accommodate the chain. Life goes on.
Step 3: Design - Steering - Time to Braze
The steering is probably the only thing that makes a bakfiets complicated. There are two methods of steering - rigid rods or cable steering.
Cable steering relies on quadrants attached to the handlebars and the fork connected by some burly cable and housing. Apart from having to custom make the quadrants (or maybe order them from Josh Muir?) the cable also stretches over time. Cable steering is very elegant but decided to go with rigid rod steering.
Rigid rod steering relies on a super long steerer tube connected to the handlebars with a tab on it. The tab is connected to another tab on the fork with a rigid rod. Each end of the rod has a joint that allows movement. I messed up by using two universal joints on the rod. This resulted in the rod flopping from side to side rather than pushing or pulling the fork. Make sure you have one end of the rod constrained so that it can only rotate in one plane.
I drew a picture of what I think is a better shape for the rigid rod (I believe the bullit uses a rod like that). I have also seen pictures of a bakfiets made by Rick Hunter with a steering rod on each side of the fork.
I used a 1/2" diameter by 0.065" thick carbon steel seamless tubing from McMaster Carr for the steering tube. This is a little bit too flexible. I think something stiffer would be better )i.e 5/16" diameter tube.
I am a big believer in good headsets for a quality, smooth ride feel. I used a 1" diameter steerer and a 1" thread-less headset. The fork has a 1-1/8" thread-less headset.
The fork is a modified bmx fork. Order a fork with the disc brake mounts already on it. I ended up adding the brake mounts and extending the steerer. It would have been much simpler if I didn't have to deal with the disc brake alignment and placement.
I added some extra holes in the tab on the steerer. The center hole provides 1 to 1 ratio steering (distance from center of bike to bolt hole is the same at the steerer and the fork). The outer one seems to be slightly better but it is really hard to say.
All of the steering needs to be welded up or brazed. Brazing is fantastic. Lower heat, slower, more controlled and very strong. I recommend finding somebody who is good at it and working with them to get the steering worked out. Mad props to Darren and Quentin who helped out with this step.
One last thing about steering - if you plan on carting around kids then the bars have to be pretty high so that the brake levers don't scrape the tops of you passenger's heads. It may make sense to rearrange the seating to solve this problem.
UPDATE (September 2013)
I made a new steerer out of 3/4" chromoly steel tubing (0.035" wall thickness). It is much better! See the pictures below.
Step 4: Start Building - Cut Your Bamboo and Jig It!
My Jig consisted of a sheet of oriented strand board. I tacked it together piece by piece and relied on measuring with string, calipers and a plumb bob. Nothing beats throwing the fork and wheels onto the tacked up frame to check for true before epoxying it all together. Tires on the rim are a good idea (what? it looked like I had plenty of clearance?)
I tacked everything with a thickened mixture of epoxy. (West Systems 404 high density filler)
I have attached a picture showing how thick and burly the pieces of bamboo are that I used. Unfortunately I did not measure the thickness before gluing it all together. I also don't know which species of bamboo I used.
Don't forget to rough up the metal pieces so that the epoxy has something to grip to. I am also a believer in roughing up the bamboo to get a good joint.
I think the pictures speak for themselves.
Step 5: Epoxy and Hemp That Frame
Again, I think you would be better off following some other methods for doing the actual epoxy work. I did not compress my joints enough. There is a lot of talk about electrical tape, etc for really getting compact joints.
I do think it is good to keep it all clean when working with epoxy - I used acetone to remove the grime and grease before taking and again before wrapping. Also wear gloves and a respirator.
I filled in some big voids with thickened epoxy.
Sorry I don't have more instruction on this step. I have attached some pictures of a Calfee bamboo bike. I have never seen better.
Step 6: Finish It Up Build a Box
I was really worried that the geometry was somehow not right so I put the wheels on as soon as I could. You can still see the plastic wrap on the bamboo to keep it clean in the picture.
Sand sand sand. Be really careful not to scratch the bamboo - the scratches really jump out (visually, that is).
I also coated the whole frame with thinned epoxy (kind of like a varnish). Thin the epoxy with ethanol alcohol.
The box is just 1/4" plywood. Nothing fancy. I would maybe like it to have more impact resistance. A lot of stuff on the bike is zip tied in place (cables, the box to the frame, etc.). My long term goals are to slowly change this...
A stronger box might also be good for safety. Ideally the whole bike would get shoved in an accident instead of the box just breaking. Not sure how this would all work. Maybe a detachable box that flies out of harms way. Hmmm.
There is really no limit to how you do the box. Tom's Cargo Bike webpage has a lot of great ideas. I thought about doing the box like a stitch and glue boat but I ran out of steam.
Step 7: Future Thoughts
I hope this instrucatble inspires you to build your own cargo bike and provides you with enough information so that you feel comfortable taking on the challenge.
I have some future plans for my bike.
I would like to add a surfboard rack.
I would like to re-arrange the seating arangement so that the kid's heads are not under the brake levers and that they are out of the way of cars as we ride along.
The last idea I have is electric assist for the cargo bike. All that extra weight adds up and it is more work to haul around. I think electric assist would be nice to bring the speed up to that of a normal bike (although I still pass some people on their normal bikes - ha ha!). My vision for the electric assist is something that automatically adds power based on how hard I am mashing on the pedals - some kind of strain gauge in the cranks,,, that is another project for another time.
I will leave you with some inspiring words:
I rode past a gang of hipsters and I heard one of them say - "Hey look, that guy has a Jamaican bobsled".
If you liked this instructable please vote for it in the "Wheels Challenge" and the "Bicycle Contest"
Please note that I am a bit slow/erratic with responding to comments and messages. I will try to answer questions.
Thank you.
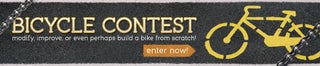
Grand Prize in the
Bicycle Contest
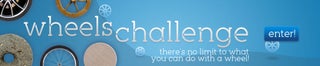
Finalist in the
Wheels Challenge