Introduction: Keeping Grandpa's Saw Alive
I found this small hand saw in my grandpa's workshop and knew I had to save it and bring it back to life. It is the perfect size for my scale of work and would be the first panel saw in my collection. The fact that this is my grandpa's makes it all the more special to me.
Let's get started!!!!
Step 1: How Bad Is It?
Assess the extent of damage and come up with an idea of what you want to replace and/or restore.
This saw handle is chipped and cracked. It is usable as is but I want to make a new handle and give this saw some new life in my collection.
The saw plate has a patina from years of sitting around, as well as rust and the teeth are dull and not completely uniform. I want to clean the plate so I can find out what kind of saw this is and shape and sharpen the teeth.
Step 2: Select the Material
I had some nice rough sawn cherry the would be beautiful for a saw handle. I found a board that was thick enough and used my scrub plane to surface the material to see what it looked like below the dull grey outside layer.
It is like opening a present. The colors and grain came alive. This piece of cherry had a nice sapwood streak and interesting color. Some call sapwood a defect, I call it character!
Step 3: Layout the Handle
I used the old handle as a template and located where I wanted the handle to be on the board. It is important that the grain direction goes along the thinner parts of the handle so it isn't likely to break at those weak spots. I also kept part of the sapwood streak at the top.
I then used a compass and found the diameters that matched the profiles at certain parts of the handle. I drew them in and noted the the size too for reference on the next step.
Step 4: Start Drilling
I selected the right forstner bit for the right curve and drilled out the different parts of the handle. This is a great way to accurately cut out the curves of the handle that would be difficult to do with a jigsaw or drill press.
After the holes were drilled I used the holes in the saw plate as a template and traced their location on the outside face of the handle. Notice in the second picture that I practiced drilling the recess for the saw nuts before attempting to drill the holes that count on the final piece.
I marked the center of the holes with an awl to aide in drilling later.
Step 5: Cut the Saw Plate Groove
This step was always harder in my head then it actually was. I first used a marking gauge to mark the center of the board. The marking gauge leaves a crisp line that will help guide your saw cut. I used a saw with a similar kerf thickness and cut from both sides a little at a time constantly checking to see if I followed the marking gauge line. Eventually your saw cuts will meet in the middle and you finish the saw cut to the boundary lines you draw on the board before you start cutting.
I did not take a picture of this process but here is a picture of what the blade groove looks like and how straight the saw plate ended up using this method.
Step 6: Drill for the Saw Nuts
I drilled the top hole using the same series of steps drilling the practice holes and fit the first saw nut. After Fitting the top saw nut, I drilled the bottom hole so I could see if my alignment was good. As you can see by the first picture the hole lines up perfectly. Success!!
Next is the medallion. I drilled the relief holes and then pressed it into place using my vise so it would leave a mark around the outside diameter of the medallion. I could then use a carving gouge to cut along the indent before removing the waste. After the waste is removed with chisels, the medallion is installed and the alignment checked again. Bottom hole still lines up!
Step 7: Test the Handle
Now is the time to cut the saw handle using a bandsaw, coping saw, or jigsaw. I used a jigsaw because it was what I had on hand.
I cut slightly outside the lines so I could come back later with files and rasps to finesse the curves to the line.
After the handle is rough cut, insert the saw plate and install the saw nuts to get a first look at your new saw!
It is an ideal time to test fit the handle in your hand and make changes where needed. As you can see in the last picture, I decided the upper and lower horns were too tight so I marked where I wanted to flare them out to be more comfortable. Make the changes and test fit again until you are happy.
Step 8: Shape the Horns
Now it is time to shape the upper and lower horns.
To accomplish the look I wanted I marked the centerline and then marked a small offset on either side. I used a compass and estimated the radius that looked good to my eyes and then drew a perpendicular line to give myself crosshairs to place the point of my compass. Using this offset method gives you a more sweeping radius rather than a perfect semi circle. I think it fits the handle better.
Use files and rasps to fair the curve.
Step 9: Layout for the Handle Curves
I start by drawing pencil lines about the distance I wanted the curves to end. I wanted there to be a flat on the side of the handle after shaping so I left plenty of flat area not to be touched.
Notice that as the line approaches the horns, I made them sweep in to meet at the tip. This will give the handle a nice look once done.
I also drew layout lines on the back and inside flats. I just divided it into four sections. It will make sense why in the next few steps.
I have no excuse for the feet in the background :)
Step 10: Shaping the Back of the Handle Grip
This is a methodical approach to shaping the curve.
The first step is to file a flat that connects the line drawn on the face to the first line drawn on the back flat. (Picture 1)
The next step is to draw a new layout line that splits the new flat that was just filed in two. (Picture 2)
Then you want to file a flat that connects the line down the middle of the handle to the new layout line just drawn. (Picture 3). This eliminates the ridge created by the first flat and creates uniform facets across the back.
The rest of the shaping is time consuming but simple now that the basic shape is created. I used the thin cloth backed turners sandpaper and just round the back. To help me know when it was done, I scribbled pen lines on the back so I could see where the low spots were. (Picture 4)
Just keep sanding. I started out with 100 grit until the facets were rounded and the shaping was done. Almost there, just a little bit of pen still showing. (Picture 5)
Now that the shaping is all done and my fingers are raw from sanding, I moved to 150 grit, then 220, 320, and finally 400. I wanted it to be super smooth so I spent the time to go to a higher grit than necessary for most people. (Picture 6)
Step 11: Repeat on the Inside Curves
I started off with coarse rifler files on the inside curves. Use the same progression payed out in the step before. For me, this was the hardest part of the build. Sanding the inside corners will rub your finger tips raw but it is worth it in the end.
I used carving gouges and chisels to shape the sharp crease where the two curves meet.
Once finished it looks great and I am totally happy with the outcome.
Step 12: Shape the Chamfers
I added the chamfers to the front of the handle to get rid of the blocky look.
First I took a sharp chisel and scored the fibers all the way around to help prevent tearing out the grain. I then used a chisel to remove the waste. Work down to the line and make sure to use a sharp chisel and don't take too much at a time or you might break something. It would be a shame to mess up now.
Step 13: Smooth the Handle Shape
The final bit of shaping and smoothing is to the flats on the top and bottom. They are still raw from the jigsaw and need some work. This is where you want to use every tool in your arsenal to get the job done. I used a scraper, chisel, sandpaper, rasps and files on this step. A scraper is great because you don't have to worry about grain direction much. Stop and check yourself regularly to make sure you are square to the face.
At this point you might want to clean up the flat faces on the sides of the handle. I used a smoothing plane and also glued some sandpaper to a granite block to sand the sides smooth and flat.
Step 14: Admire Your Work
By now your fingers hurt and you are covered in sanding dust and curls from the scraper, But you are done shaping!!!!! The handle looks great and you should be proud. It is hard work but it is something you did with your own hands and should last another 100 years.
Step 15: Apply the Finish
Now for one of the best parts..... Applying a finish
I started off with a wash coat of shellac. This allowed me to see any places that needed more sanding and also brought out the richness of the cherry. After final sanding, I applied TruOil sanding lightly with 320 sandpaper between coats. TruOil is best applied in thin coats and dries hard. It is ideal for saw handles and looks great. All the sanding in prior steps really pays off here.
Step 16: Clean and Sharpen the Saw Plate.
I used fine sandpaper and steel wool to clean the saw plate. After cleaning, I found out that this saw was made for the Buddy L corporation which produced a line of tools designed for kids. There is nothing toy-like with this saw other than it being small. What a cool story and only adds to how neat this saw is to me.
I purchased all the necessary saw files and a saw set to re-set the teeth after sharpening. The order of operations is to joint the teeth, shape them, set them, and then sharpen them. I love the geometry of cross-cut saw teeth.
Step 17: Final Assembly
It is finished!!!!
Here is the before and after pictures. I love how it turned out and it will serve me we'll for many years to come.
I am extremely proud of it and I know Grandpa will love to see it too.
Thanks for looking. I hope this was informative and entertaining.
Cheers,
Cory
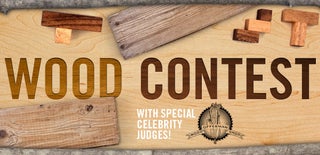
Runner Up in the
Wood Contest
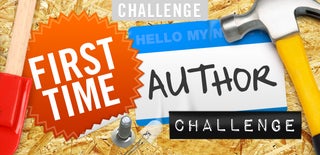
First Prize in the
First Time Author Challenge