Introduction: Knife Making
Disclaimers: Knife making is dangerous, I'm not responsible if you get hurt. Also, know your laws, and don't make anything illegal. I'm not responsible for anything that happens as a consequence of you reading this.
This is a personal project of mine, and when I finished, I thought, why not make an instructable out of this? So here's the result. This is my first knife in the pictures. This isn't an instructable to make the best knives while prancing about all your fancy machines, but rather an instructable that an ordinary person, with no prior experience and limited materials can do as well.
Overall, I spent around $5 on the knife itself, and the tools were $10, for the files and clamps. The rest I had. However, you can borrow tools from a friend as well.
You don't need too many tools, but the more you have, the easier it is. This is stock removal, meaning you start with a bar of metal, and remove whatever doesn't look like a knife. Full tang.
Tools:
-2 clamps
-1 Drill
-1/8" Drill Bit
-Hammer
-Saw, preferably a reciprocating saw, but hacksaw works too.
-Files. One flat, and one half round. Bastard files will do the job faster, although I use a single cut towards the end for smoother results.
-Sandpaper. As low as possible to as high as you want. I used 80-200, with 100 and 150 in between.
-Epoxy. I used JB weld. The longer it takes to set the better.
-Sharpie
-Tongs
Materials:
Sheffield's knife supply is a great place to buy. They may be a bit gruff, but they have great prices, and provide good and honest survice. USAKnifemaker's is also a good place.
-Steel. I used 1080 steel, which is probably best for beginners. Don't use random steel, since heat treat will be difficult. All temperatures and heat treating methods are for 1080 and 1084 steel.
-Handles. I used micarta handles, although any will work. If you're using wood, or something delicate, you need to be careful during the peening process.
-Pins. 1/8" Brass pins. If you want bigger pins, than you'll need a bigger drill bit.
-Canola Oil
I'm pretty sure I forgot something, please comment if you notice some materials are missing.
Step 1: Designing
I use inkscape for this part, but you can use whatever you feel comfortable with. Basically, draw out the knife, plan out the handles, and know where everything goes. The knife will probably change a bit from your design, but a good solid idea is essential.
Mine looks different from the design, but the main idea is still there. Also, I decided to go two pins instead of 3, since more isn't necessary for me. It's all your choice though.
I'm using 1/8 thick 1080 steel, and around 9 inches long.
Step 2: Annealing
If your steel isn't annealed, or soft, you need to anneal it. Unless you want to spend years on filing, drilling, sawing, and all that good stuff. So, it's quite easy to anneal. Heat the steel up to around 1500 F, and then bury it in sand or some other insulating material to let it cool. Vermiculite is one of the most ideal materials, just plunge it into the substance, but I didn't have any, and just dug a hole, lit the fire, and then buried everything under the sand. It worked well enough. To tell when you're at 1500, I use salt. Salt melts at 1478 degrees F, give it around another minute in the fire, and you'll be around there. And the steel is hot. Don't touch it. Common sense.
For the fire, I suggest starting it, and then waiting until you have a nice bed of coals. Add more wood around the coals, place the bar of metal in, and fan like a madman. Method doesn't matter. Just get the whole piece up to 1500F. The steel will probably come out black from the fire. Don't worry about it, you can clean it, but it'll just get dirty again.
Then, trace your design onto the steel. I used a sharpie.
Step 3: Cut It Out
Somehow, just cut it out. You can drill a bunch of holes around it, and connect the dots with a saw, or just saw the whole thing. You can use a hacksaw, with a metal cutting blade, and as many teeth per inch as possible, or you can use a reciprocating saw like I did. It's faster with power tools, but with patience, you can probably cut it out with a butter knife. Don't cut yourself.
I drilled the holes, and then used the saw. Here it is halfway through cutting. And I left it outside by accident and it rusted. But I cut out the rusted parts anyways, so all's good.
After that, use files or sandpaper or something, and polish the outline.
Step 4: File the Bevel
In this step, we're filing out the bevel, to form the cutting edge. Take a file, and file. I started out by filing perpendicular to the work, but ended up draw filing for flatness. To draw file, hold the file perpendicular to the blade, and starting at the tip, push to the base. Or push from the base. Either way, push. The file won't cut if you pull. I clamped a piece of wood at the base of the blade to make sure I didn't overfile.
Also, you can see some blue sharpie in the first picture. I draw a grid of sharpie so I can see where I need to keep filing, and once all of those sharpie marks file away at a the same time, I know it's flat.
Once you're done, clean up the blade with sandpaper. Make sure it's decently smooth, since we'll be hardening next, and sanding out scratches will be a pain after that.
DON'T FORGET TO DRILL YOUR HOLES BEFORE HEAT TREAT! IT'LL BE REALLY DIFFICULT AFTERWARDS.
Also, you want to leave around 1/16-1/32 material at the edge, don't have a sharp edge, otherwise it'll warp really easily in the heat treating process. I left mine at 1/16 just in case, it just means more work making your edge, but there's less chance of it bending.
Step 5: Normalizing
The thing is, your grain isn't perfect right now. You want the grain to be as small as possible, to reduce the chance of cracking, and for better cutting performance. To normalize, bring it up to 1500 degrees again, and leave it, edge up, to cool in the air. Remember, salt melts at 1479. Then, take it up to around 1414 and let it cool. You'll know you're there because a magnet will no longer stick to the blade. Put something in between the magnet and blade. If you don't, the magnet will crack due to the intense heat. Let it cool. Finally, take it up to a bare red glow, a less intense glow than at nonmagnetic. It should be a dull red, not bright. Let it cool down again. You might want to keep the fire going, since in the next step, you'll be heat treating.
Step 6: Heat Treating
Harden the blade! I quenched in canola oil. There are commercially available oils specially designed for the knives, but it is pretty expensive, and a lot harder to get than canola oil.
Also, heating the blade, and cooling it down 1000 degrees in a matter of seconds is stressful. You need to make sure your normalization is done right, and some nice luck. Otherwise your blade might crack, and you'd be at step 2.
The oil needs to be in some kind of container that will fit your knife, and heated to around 100 degrees F. This makes the oil thinner, and thus it'll move heat away from the blade faster. Heat the blade up to 1500 degrees for the final time. Once it's there, plunge the blade into the oil. Make it so it's like you're stabbing the oil. Now, don't wave the blade sideways, because then it'll warp and bend. Instead, you have to move the blade up and down in a slicing motion to cool it down fast. If you don't, it won't be fully hard. You just need to cool the blade down, hardness doesn't matter for handles. Thus, only the blade needs to be submerged.
Sorry, no pictures for this part, was too busy with the knife. But just remember to keep slicing with the blade. There'll be lots of smoke. Let it stop smoking, and leave it in for awhile. Watch out! The blade is brittle right now! Once you're done with this, you need to move right on to tempering.
Step 7: Tempering
The easiest step I believe. Put the blade into your oven, and bake it for 415F for 2 hours. Once it's done, take it out, let it cool, and back in at 415 for 2 hours. This relieves the stress in the blade, allowing it not to shatter when sneezed on. Shouldn't be any problems here.
However, don't delay at all. I had mine in the oven before it was cold. Don't put it in steaming hot, just at a nice warm touchable temperature. The more you delay, the more likely you'll bump it and have it shatter. It's like having an open wound, there's no reason to leave it exposed to bacteria and all that stuff.
Step 8: Handles
Well, first clean and polish it. Just a lot of work. Listen to a nice and motivational song while you're doing it. I usually go with Eminem, but whatever floats your boat. Handles are pretty simple. Trace the handle of your blade onto the handle material, and cut it out using a saw or whatever you have. Then, file and sand it down to the right size. I filed in finger grooves on the side for my index and middle as well. Especially important is to round your corners! This makes the knife feel a lot better. Don't be afraid to take off material, just sand down your corners.
Also, wear a p100 respirator when you're working on micarta, G10, or carbon fiber. All other materials, you should be wearing a mask anyways. Dust isn't good for your lungs, especially G10 and carbon fiber. Imagine inhaling little blades down your lungs. That's what the glass in those materials will do to you. You can buy a respirator for $20, but you certainly can't buy lungs.
I had drilled holes for the handles before, and use pins to keep the handle aligned with the metal. That way I can sand and file it down to the correct size without having to measure every three strokes.
Step 9: Attachments
Now you have the option of peening, or no peening. Peening is basically expanding your brass pin over the handle, so that it holds the handle together. If you don't want to peen, just epoxy the handles onto the metal, and slide the pins through. Once the epoxy dries, file the pins flat. Modern day epoxies are strong enough to hold the handles on for normal applications, but since you can add an extra attachment, I prefer to peen anyways. Probably superfluous, but just in case.
If you would like to put in the energy and time for an even stronger bond, than peening would be a good idea. What you do is you need to flare out the ends of the holes you drilled. I used a 3/16" drill bit and drilled around 1/16" down. Then, cut the pin down until 1/16" sticks out on both sides, and round the ends using a file. Epoxy the knife together, and stick the pin through. Then, using a hammer, preferably ball peen, gently tap to deform the brass. After a few taps, move on to the other pins on that side. Then, flip it over and tap all those pins. You want to go gently and slowly. Keep flipping and tapping, and eventually, the pins will be deformed, and crushed into the extra space. This allows the crushed pins to hold the knife together. If there's excess, just leave it sticking out, you can file it off later.
Either way clamp it down just in case, and epoxy as well. You want the epoxy to be a long cure one, certainly at least an hour, otherwise you won't have time to get everything together. I used JB weld, and it is doing great so far. The longer the cure, supposedly the stronger the bond.
Step 10: Polishing
Just use some sandpaper, and polish everything up. Clean it up, sand away the extra epoxy, file down your pins flush, and sharpen your knife!
Step 11: Extras
Etching: It's nice to have a little makers mark, or write something down into your blade. Another instructables member has a nice instructable on engraving, but I'll quickly cover it here too. You want to use nail polish, coat the blade with it, and use something to scrape the nail polish off. Write what you want with that tool. Then, you let the nail polish fully dry, and attach the positive end of a 9v battery to the metal, and the negative end to a q tip. Dip the q tip, with the negative wire, into salt water, and rest the q tip on the etching area. You should see bubbles, it's etching. Let it eat for awhile, switch new q tips, and redip in salt water. Stop when you think it's deep enough. The longer it stays, the more likely it will be less clear. Use nail polish remover to clean up.
For my mark, I used duct tape. I cut out the image in duct tape, and duct taped the blade. The metal you expose is the metal that will be etched. Then, same as above, positive end to metal, negative to q tip, and etched the design in.
Filework: You can use small files to create an intricate design into the back of your knife. I attempted a vine pattern on the back of mine. I used a round file and triangular, and filed in the vine. Then, I smoothed out the corners, to make the vine more curvy. A quick search on the internet for knife file work tutorials will yield a lot more patterns.
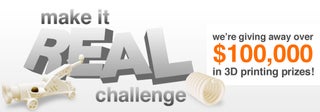
Participated in the
Make It Real Challenge