Introduction: Large Vacuum Former
We had a requirement for a big vacuum former, as many of our members were interested in costume making and cosplay and needed to be able to make torso size "armour" etc. so we first took look to see what was available commercially and soon realized anything we could afford even second hand would be way too small for our needs. Having decided that our only option was to build our own we scavenged the internet for ideas and came up with a basic design that evolved into the machine we have made.
Step 1: Building the Vacuum Table
So first the simple bit, all the vacuum table really is is a hollow box with a way of drawing a vacuum and a grid of holes. We opted for constructing it out of MDF, but any strong sheet material would work. Your next problem is to decide how to drill the holes we opted to use a doweling jig but you could get them cnc routed.
For legs we used some steel ones from Ikea that we had in our donation room, but timber would be possible. This thing is heavy so rather that rely on screws to hold the legs on we bolted them on using Tnuts. You will also want to reinforce the box, the air pressure acting on the out side of this box will want to deflect the table and make it concave. However you choose to reinforce the table make sure your reinforcments do not restrict the air flow too much, we drilled 75mm holes in ours.
Step 2: The Heat Source
We had originally intended to use nichrome wire for the heating unit but found it a little difficult to get hold of at a reasonable price in small qty. After a bit of thought we decided to go with halogen GU10 lamps they are woefully inefficient when it comes to light which means they dump out a lot of heat.
We explored various mounting options but soon found the most cost effective was to purchase ceramic GU10 lamp holders (we made the mistake of ordering the exact qty we need, unfortunately one was smashed on delivery so its worth getting a couple extra just incase) and mount them to a sheet of steel with self tappers. The steel sheet came from the back of a shelving unit we had lying around although once again you could just purchase some from you local metal stockist.
We then faced the nightmare of 70 lamp holders, 2 wires from each that need to be wired together. everything from terminal blocks to soldering the wires to each other was considered but in the end we decided to make a basic PCB. Due to the size of the PCB we were unable to etch it in house and the usual companies proved too expensive. In the end we manually milled them.
Due to the width and thickness of the tracks you will require a very powerfull iron to solder the wires from the lamp holders in place. You will also need to mount the PCB's we opted for using simple mounting pillars.
This everything was then enclosed in an MDF box with a ledge to support the steel plate and a removable lid for servicing and repair. At the moment it seems to be remaining cool enough but if we find its getting hot we will add ventilation.
Step 3: The Controls
Whilst investigating the options for the heat source, we talked about the possibility of being able to heat specific areas of the vacuum bed in order to reduce power consumption when accomodating different sized work pieces. As we had originally planned to use nicchrome wire, this ability would have been limited to being able to switch on perhaps two different lengths of nichrome to give half and full power in similar way to a cooking grill. With our choice of heat source being a large array of spot lights arranged in rows and colomns we have much greater flexibility in terms of controlling both which areas of the vacuum bed recieve heat and how much. However, this greater flexibility does make the control system more complex since it now requires relays to switch power to the rows and colomns and an AC phase control system to regulate how much mains power the whole array recieves.
The control system is composed of six major component parts: Front panel assembly, Microcontroller PCB, AC phase control PCB, Row Relay PCB, Colomn Relay PCB and Triac assembly for vacuum plus heat.
The front panel assembly is made up of an PCB mounted LED matrix corresponding to each heating element in the array, an alphanumeric LCD for system status, a key switch to enable the machine, an emergency stop button and switches to select the various heating patterns available.
The microcontroller PCB contains an Atmega644 device that runs custom firmware written in C for controlling the machine. This PCB has inputs from the front panel switches, temperature sensor within the heating array and pressure sensor within the vacuum bed. It outputs digital signals to switch the row, colomn and vacuum relays and a PWM output to control heating power. The status LCD is also driven from the microcontroller.
WARNING: The following components connect directly to 240V AC power.
The AC phase control PCB takes the PWM output from the microcontroller and provides triggering pulses synchronised to the AC line to a Triac switch, by controlling the point during the AC cycle when the Triac fires it is possible to regulate how much power is supplied to the load, in this case the heating array.
The colomn relay PCB consists of six electromechanical relays driven by the digital signals from the microcontroller, five switch power to the rows of the heating array and a sixth switches power to the cooling fans.
The row relay PCB has seven electromechanical relays driven from the microcontroller that switch the neutral to the rows of the heating array, it also contains a temperature sensor to monitor the temperature within the array.
The Triac assembly is made up of two opto-isolated triac solid state relays, these are rated at 20A, 240V AC and control the power to the vacuum fans and the heating array.
Step 4: The Clamping Frame
Right from the start we wanted to be able to use this vacuum former for big sheets (600mm x 900mm) of plastic but we were aware that most of what we would do would be much smaller so we want the clamping frame to be able to work for all sizes from A4 up. For the larger sheets we have opted for a large frame made of two sheets of mdf with a 600 x 900 hole with the holding force coming from wingnuts and tee bolts. If you wish to form a smaller sheet you can replace the bottom sheet with one mounting either a toggle clamp frame for the common sizes or additional wing nut frames. To aid sealing of the frame to the table and the sheets to the frame we have used foam tape.
Step 5: The Vacuum Source
Finally we needed to find a source of a decent vacuum. A search around in our donation room found a couple of vacuum motors which we believe had came from a garage forecourt vacuum cleaner. As we had these we decided to go with them but if you cant get any a powerful domestic vacuum or shop vac would be a good substitute. Using these did however pose a problem as there was no easy way of mounting them. In the end we drilled a hole in the bottom of the vacuum table, and with a neoprene gasket in between clamped them in place with a MDF clamp plate and all thread. For now these have been left exposed but will need to be enclosed with some form of vent to allow the air to flow out.
Step 6: Final Assembly
You should now have all the key parts of your vacuum former, all that remains is too bolt everything together. We decided to use Unistrut to link the vacuum table to the lamp box and to act as the guide rail for the clamping frame, as we already had some left over from the previous project. The clamping frame runs on Unistrut bearings which were salvaged from a sliding barn style door.
For now we are relying inserting pins through the Unistrut to hold the frame in position below the lamps but in the future we may add a counter balance system to aid sole operation.
Step 7: Testing
So the moment of truth. As we did not have a mould to hand we laid some tools out on the bed to spell out fizzPOP. We clamped a sheet of Hips in the frame and raised it up next to the heat source, we soon noticed that we were getting a warm spot below each lamp (our first attempt ended up with thin spots). Lowering the material further away from the heat source by a few inches resulted in a much more even heat. We allowed the material to come to temperature turned on the vacuum motors and quickly lowered the frame over our "mould".
Other than around the edges were the frame had both shadowed the material slightly and also conducted the heat away we go a very crisp and detailed form with very little distortion. If the future we may look at adding reflective tape around the edge of the frame to try and reduce the shadowing effect.
Step 8: How to Operate
To help clarify a couple of point and answer some of the questions in the comments, below are instructions on how to operate the vacuum former.
- Clamp your plastic sheet in the frame.
- Raise the frame to the appropriate height below the lamps and support by inserting the pins through the slots in the Unistrut.
- Turn on the lamps and allow the plastic to soften (this will take between 30sec and 5min depending on the material). Do not walk away when the heating lamps are on!
- Position your mould on the vacuum table.
- Once the plastic is heated sufficiently (HIPS will tend to warp to start with, then go taut then sag slightly) turn on the vacuum system
- Pull the pins and by hand push the frame with the now softened sheet down over your mould until the frame makes contact with the vacuum box.
- The sheet should rapidly be drawn down around your mould.
- Turn off the lamps and vacuum system and wait for your moulding to cool before removing.
Hopefully that should make things a bit clearer.
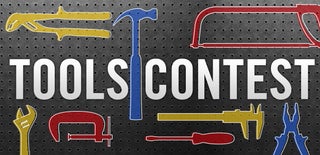
Third Prize in the
Tools Contest