Introduction: Laser Cut Enclosure With Living Hinge Lid
I did all my laser cutting at TechShop San Francisco. It was my first attempt and 2 of the 3 boxes that I made worked out but one broke when I tried to bend the lid into place. I tried 3mm MDF, aromatic cedar "laser wood" from www.laserbits.com and birch "laser wood" from the same. The MDF cut and bent perfectly; the cedar burned quite a lot in the cutting (more on that later); the birch cut well but it was too thick to bend.
[Update] I've now improved the design (pictured) and it works perfectly with birch as well as the other woods. See the final step for the updated design files.
Materials:
- ~3mm laser ply or MDF.
- 6 x 10mm M2 screws and nuts.
- 1 x wireless sensor node (mine is my own design but a friend of mine has written up a very similar one, from which mine is derived)
- 1 x laser cutter, I used a 60W Epilog Helix.
Step 1: Designing the Box
Here's how I built up the design (sorry for the lack of screenshots of the working):
- Set the file to be 24inches x 18inches, which is the bed size of the laser cutter I was working with.
- In File > properties add a 1mm grid. (I prefer to work in metric
- Draw a 6 cm square for the base. I didn't worry about details like the screw slots at this stage.
- Draw half-circle for one side and extend down from the ends 1cm to give a flat portion; close the base.
- Calculate the required length for the top = PI * 3 + 2 cm = 11.5cm
- Create a rectangle of that length and 6cm tall.
- Using the grid snap, draw one copy of the living hinge pattern.
- Clone the pattern along the length of the lid.
- Using the path editing tool, refine the shapes, drawing in the pegs and T-slots for the screws. I used a 1mm grid for 90% of the work. For precise pieces like the T-slots, I selected nodes that needed to be "off grid" and manually entered the coordinates.
- Using the grid, draw in 2mm circles for the screw holes. For the antenna hole, I used the snap toolbar to turn on snap to cusp and snap to centre and then let the centre of the circle snap tot he end of the line. Then I used the path tool to edit the line to remove overlap.
- Finally, I added some rounder rectangles to the end piece for air holes and cloned the end piece.
- I was planning to cut different types of wood that have slightly different thicknesses and I didn't want to have to alter the design for each type so I made the pegs stick out past the end of the slots and curved the ends. On a thinner material, they stick out a bit further but no matter.
- I made made the pegs slightly wider than the holes (by 0.2mm) in the design to account for the kerf of the laser beam.
Step 2: The Fun Part: Using the Laser Cutter
I used Inkscape to draw the design but TechShop uses CorelDraw to operate the laser cutter. I found the only way I could get CorelDraw to read an Inkscape file was to export as DXF. I exported as DXF using 1mm units and imported 1:1 using 1mm units in CorelDraw. The design was automatically centred in the Corel document so I moved it to the top-left corner, which is the origin of the laser cutter.
I selected the whole design and confirmed the pen width was hairline, as required, then hit print.
Cutting MDF worked very well with close to the recommended starting settings. However, I found that cutting the cedar ply was problematic. The same settings that cut the MDF only went about 25% through the cedar. Juggling settings, I ended up cutting the cedar 3-4 times before the cut went through. This lead to a fuzzy cut with a lot of soot. However, the widening of the cut made bending the piece a lot easier later on so if I go back with corrected settings I'll have to alter the design to widen the bending slots!
I cut the birch in one pass using the settings I'd worked out on the cedar but that made a very precise cut and the birch snapped when I tried to make the bend. (See the update in step 7 for my improved design that works well with birch.)
Step 3: Assembling the Box Sides
Follow the instructions in the images to assemble the sides of the box.
Step 4: Install the Lid
- Feed the antenna through the hole in the lid.
- Carefully bend the lid down symmetrically to avoid snapping the small pegs on the sides.
- Hold the lid tightly in place while you install the remaining nuts and screws.
Step 5: Finished
Here's the completed article.
Step 6: What Might Go Wrong
Here's what happened to the birch ply lid with my original design when I tried to make the bend. back to the drawing board! (See step 7 for my improved design.)
Step 7: [Update] Improved Design
Since only 2 of 3 of my first batch of boxes survived the bending process, I made a few different modifications to the design and cut them over the weekend. One of the alternate designs worked much better. The lid was very flexible, and I could even bend it round in a circle!
The main change that I made was to reduce the width of the zig-zags in the living hinge. Before it was around 3.5mm, which was the width of the boards. My new design uses 2mm for the width and reduces the number of central supports to 1 in order to give maximum bend.
I've attached my final Inkscape SVG file to this step.
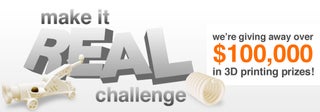
Participated in the
Make It Real Challenge
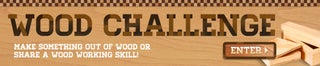
Participated in the
Woodworking Challenge