Introduction: "Little Dipper" SLA/DLP 3D Printer for Under $500 (projector Included)
If you would like to keep up with our 3D printing projects, follow us here or visit:
https://www.facebook.com/protobuilds
Protobuilds.com
"Little Dipper" SLA/DLP 3D printer overview
This Instructable is about building a simple yet versatile resin (SLA) 3D printer that uses a cheap DLP projector to build the part from the "top down". This orientation of the light source is similar to other large scale industrial SLA machines. It has some advantages in simplicity, scalability and disadvantages in minimum feature size and print time.
This version build is budget conscious, has a low part count, can easily be upgraded and scaled in size. The entire 3D printer (projector and resin included) can be built for just about $500 or less which makes it one of the cheapest bang-for-your-buck 3D printers using SLA resin out there.
There are many good Instructables and resources that contain more exhausting detail about DLP resin 3D printers and background information. If you are interested in learning more about this http://www.buildyourownsla.com/forum/ will be one of your best community resources for knowledge relating to the topic.
Autodesk Spark recently released more information and support data for SLA 3D printers that use DLP chips. As their project develops, more DIY applications might emerge. http://spark.autodesk.com/
How it works
A DLP projector is used to cure UV setting resin one layer at a time while a moving axis drops incrementally into the vat of resin. A projected slice cures each layer and builds the part. This style of resin printer is different from a FormLabs 3D printer and some others in 2 ways.
1) It uses a DLP projector rather than a laser to cure each layer.
2) It shines the light source from the top rather than up from the bottom.
Advantages over laser based bottom up and DLP bottom up designs:
Simplicity
Lower start-up cost
Modifiable to bottom up
Fast build (~1 evening)
Major Components and Materials:
DLP projector
There are 2 known choices, although others may work.
1) Acer P1283 DLP Projector (eBay or other online)
2) Acer H6510BD DLP HD projector (eBay or other)
Linear Slide/Axis
Almost any linear axis that is belt driven or screw driven will work. I choose a minimal version of this:
http://www.openbuilds.com/builds/v-slot-lead-screw...
Below I will include a striped down parts list for the axis build. A more budget minded and adventurous person could even choose a drawer slide, but you may find that rigidity and smooth sliding in the z-axis will be a useful feature.
4x4 sheet of 1/2in MDF or equivalent material and hardware
The version shown here is as simple as it gets. 2 pices of MDF cut to provide a mount for the axis, projector and stable footing for the machine. Pretty much any kind of enclosure can be designed for this 3D printer. Your main objective is frame rigidity and ambient light blocking.
Ramps 1.4 or Arduino based electronics capable of running at least (1) nema 17 stepper motor
This build features a RAMPS 1.4 board, stepper drivers and an Arduino Mega 2650 with standard Sprinter firmware. There are some basic modifications needed depending on the hardware you choose. None of these modifications constitute needing to know anything in-depth about programming. The firmware I used is modified for 5/16 standard threaded rod and has end-stops disabled. You can modify this firmware using the Arduino environment to further suit your needs.
UV Resin
Makerjuice.com, Madesolid.com are the 2 most seemingly popular and affordable options for UV resin suitable for DIY resin printers such as the one featured in this build. This build has been tested with G+ from Makerjuice. Funtodoo, Form1+ and Spark/Ember resin formulations are likely suitable.
Build Platform and Plastic Tupperware vat
This build includes plans for a build platform that fits a specific set of Tupperware available at "wallyworld". The benefit to the type chosen in this build is that you get a variety of sizes that scale easily, so that extensive design modifications are not needed. You will also need additional containers for post-cure/clean up of your resin parts.
Control Software and Slicer
I used Creation workshop to control and slice 3D models. Download Creation Workshop here.
Step 1: Setup Electonics and Software
Overview:
I choose a RAMPS 1.4 for this build. That may seem a little overkill since an Audino UNO with a single stepper would work. A RAMPS is a cheap option for additional stepper drives that could be used for a wiper or tilt mechanism. You can also drive a 12v heater for the vat directly from the board and support temperature monitoring later on. Only one stepper and single axis is covered in this build.
Materials:
(1) RAMPS 1.4 with Audruino Mega 2560 and Stepper Drivers
Purchase example- ~$40
Nema 17 Stepper motor
Purchase example - ~$15
12v 30a Power Supply
Purchase Example - ~$30
Desktop PC with Auduino Environment and creation workshop installed.
1) Connect the Electronics
Connect your RAMPS to a 12v power supply and connect your stepper motor to one of the z-axis ports.
View this guide for wiring your RAMPS. *Be careful not to switch your power supply wires and always connect wires with your power supply unplugged.*
The only steps you need to follow in the above guide are connecting a power supply to the ramps and connecting (1) z-axis motor. No end stops are required and will be disabled in your firmware update.
2) Configure and upload Firmware
*Note PC reboots may be required between each milestone step*
The power supply does not need to be connected for this step. I recommend only connecting the USB to your RAMP/Arduino for updating firmware.
I included a link to the version of Sprinter firmware I used for my build here (folder must be named Sprintermod). You can use this for your printer, but beware. You may need to change the steps per mm line in the firmware to suit your z-axis. Here's a good calculator to use.
http://www.prusaprinters.org/calculator/
To change the Steps per mm open the Arduino IDE application, then file > open (sprintermod) folder from your desktop, then open the "Sprintermod" Arduino file icon. Several tabs should appear (if only one tab appears, you will need to make sure your folder is named correctly). Go to the 2nd tab "configuration.h" and scroll to "//// Calibration variables" to modify the z-steps. "2272.7272" would be your z-steps in this example if using 5/16 threaded rod. Change that value to match your linear axis.
// X, Y, Z, E steps per unit - Metric Prusa Mendel with Wade extruder:
#define _AXIS_STEP_PER_UNIT {80, 80, 2272.7272,700}
Once modified, click the upload icon in the Auduino IDE and if no errors are detected, you're probably ready to test your hardware.
3) Power up RAMPS connect USB and Connect with Creation Workshop
After your RAMPS is connected with USB, open Creation Workshop and click the CONFIGURE button/tab at the top. Under Machine Connection, click "configure" and select the port and baud rate (baud rate is defined in firmware) my default spritnermod setting was 115200. Click ok. Your port number may vary.
Click the connect icon (a pair of plugs up top).
Click the "control" button/tab up top.
Click the z 1 and z-1 buttons to see movement on your stepper.
Does it move? If so, hooray!
4) Projector Test (pre-modification)
Connect your projector to your PC and enable it as a secondary monitor. Open Creation Workshop and click on "control". You should be able to click "show calibration" and see a red grid. This will work regardless of having an Arduino connected. You will need to adjust your "build size" under "Configure" to suit your aspect ratio, vat size and projector distance.
Now it's time to build the linear axis, vat then modify and mount the projector. The next step is all about that.
Step 2: Build Linear Axis, Resin Vat, Platform, Then Modify and Mount a Projector
The Linear Axis
This printer works by incrementally lowering a z-axis into a vat of UV resin then projecting a new layer or "slice" of the model onto the top of the resin vat. By default Creation Workshop will move the platform down to submerge the part, raise the platform (slightly lower than before), then wait for the resin to settle and new slice to be projected.
I used a linear axis build that is based off an OpenBuilds design you can view here: There are a lot of creative ways you can make a linear axis. I won't focus heavily on that, instead here are some pictures of my linear axis and projector mount.
Possible improvements:
Shielding from sunlight and ambient UV
Smaller formfactor using 1st surface mirror
More rigid bracket design
Files used:
Anti backlash nut (scale as needed)
Arm bracket (re-design as needed)
Rod Coupler (parameterize as needed)
Modify the projector
You can actually skip this step entirely however, it is entirely reversible. If you're using an Acer P1283 like I did or the higher resolution Acer H6510BD, then it will be able to cure resin without modification, but with longer layer curing times.
*Note*
LED projectors will likely not work as they do not emit UV light.
Bulb projectors with xenon bulbs (most common) are a good out-of-the-box projector solution.
The projector modification is fairly simple. Unscrew your projector case using the same procedures as you would replacing the projector bulb. You will be needing to access the projector bulb housing just as you would if you were replacing it so documentation should exist for this step depending on your projector model.
The projector housing contains a bulb and on the outside of the housing, in front of the bulb, is a small square piece of glass. This glass blocks UV from the bulb. Remove the metal bracket that holds this piece of glass and the glass it'self. That's it! You projector will now emit less filtered beams of UV light. Your projector should still work as normal. *Disclaimer* modifying this area on some projectors may damage the projector over time or change the cooling air flow dynamic. Projector overheating would be a sign that the mod may not be compatible or need to be re-thought.
Determine your appropriate mounting distance by zoom/ focusing the projector on a wall and moving it closer until you can no longer focus a sharp image. Give your self a little bit of extra distance in both directions for fine adjustment later.
Printed parts, resin vat and Platform
The platform is the part that your print will be built on. This part will be lowered into the resin one layer at a time. I cut an aluminum shape that matched my resin vat which is simply a plastic food container. An aluminum bed is necessary because UV resin curing is exothermic and will cause plastic materials to melt while curing the first layer. Sanding the bed prior to printing will help with adhesion.
You can use almost any size vat that fits in your projected grid.
3D printed parts should not be printed in ABS. ABS will dissolve in the presence of resin. 3D printed parts should be made in PET, PLA or with a chemically resistant material.
Next, mount the axis, projector and line up your platform. As you can see, my design is nothing more than 2 pieces of MDF and some shelf brackets.
That's it, you're done! Well... almost.
I plan on covering more in-depth printing and calibration in another Instructable... eventually. Until then, check out other people's Instrutables on Creation Workshop and DLP 3D printers. A lot of great 3D printers have used this method and you may find a helpful support network out there in the community.
This type of 3D printer takes a few days to calibrate your ideal layer cure times and other quirks. Spend some time looking through the settings in Creation Workshop and check out the new ember/spark project by Autodesk for new alternatives and shared ideas relating to DLP/SLA 3D printing.
https://www.instructables.com/group/ember
Step 3: Prints Made With the "Little Dipper" and Some Quick Tips
The grey rook was an SLA resin print sample sent from Formlabs. The white print on the right was made using our homebrew DLP/SLA 3D printer.
If your prints come out wide and flat, it's likely that your x and y build size is off and needs to be adjusted. The red grid-lines in creation workshop should measure 1x1cm.
.2mm layer height works great for top down resin printing.
Depending on the color of resin, cure times may be between 8 and 12 seconds. First layer cure time may need to be up to 1-2 minutes for a solid adhesion to the bed. Your first layer should be very thin. See screenshot above for cure time examples.
Larger part geometries may require longer layer delay times (wait between layers) in the lift sequence. This can be modified in Creation Workshop under "configure slicing profile" > "gcode" tab by adding delay values in milliseconds at the top and bottom (see screenshot above).
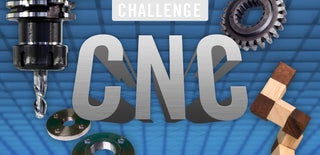
First Prize in the
CNC Challenge
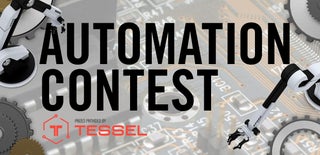
Second Prize in the
Automation Contest
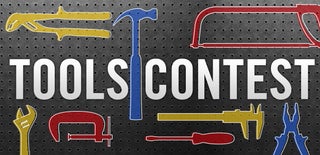
Participated in the
Tools Contest