Introduction: Long Bed Printed 3d Printer
The Long Bed 3d Printer "aka Big Red" was created to see how much of a 3d printer could be printed. That lead me to design a frame that could be printed on a heated bed, soon discovered I needed a larger build surface. After making a way to accurately control a larger bed, I had the maximum size that the frame pieces could be. By combining different parts I was able to get the main frame down to 9 pieces.
This Printer Can Reproduce Most of the Parts to make itself
UPDATE: 10-6-2019
This Printer is STILL performing beyond expectations, I did have a printed "Z" coupler fail about a week ago, used a backup and printing again. 3D printed frame design is not deforming maintaining squareness of printer.
The RepRap Project was invented by Adrian Bowyer in 2004. More information can be found in these Links:
http://www.reprap.org/wiki/About and http://www.reprap.org/wiki/About
Many amazing printers have been designed over the years: Darwin, Mendels, Deltas, Simpsons, CoreXY, ......
Thanks for Checking This Out
Print area is: 200mm x 425mm x 140mm, (x,y,z).
Printed Frame Pieces:
- Lower Center Frame
- Lower Left Side
- Lower Right Side
- Lower End Plate with motor mount
- Lower End Plate with idler
- Upper Motor Mount
- Upper Left Side
- Upper Right Side
- Upper End Plate
_____________
Double sliding Tables:
The upper table moves faster than the lower table, this keeps support and proper alignment under the print head. Recommend using auto level (auto compensation) with this design.
_____________
X Carriage is designed to pass by the vertical part of main frame, giving more x travel.
_____________
Extruder (modified wades style) is rotated 90 degrees also increasing X travel.
This version is using 3.0mm filament. (have not tried 1.75).
__________________________________________
I Want to give a Thank You to the Gang in " Google Hangouts "
for their Support and Input during the development of this Design!
______________________________
The STL files are FREE to download. (Step 9)
_______
Here is a Video of the 2nd. calibration Print.
Attachments
Step 1: History
This Long Bed design is installed on an i2 that has 750+ hours of print time,
it has a print area of 200mm x 425mm x 100mm (x,y,z).
The i2 Long Bed can be seen running in Reprap Google Hangouts
some nights and weekends.
__________________
The Prototype of this 3d Printed Frame Design has a 200mm. x 200mm.
heated bed, with 100+ hrs. of print time.
I also experimented with a printed Rack and Pinion drive for Y Axis.
There is no signs of stress or fatigue to the printed parts.
__________________
One goal was to make a larger print area with out making the frame bigger.
And do this with common parts already being used in most Repraps.
Keep the cost down was also very important.
Is this the best design? no.
There are more expensive ways to do this:
This proves the theory of operation and can be developed further.
I am planning to test and monitor current design and see what
areas have weaknesses and failures, and improve them.
One upgrade could be: 10mm smooth rods or a printed ......
Post any Questions you have and I will try to answer them.
Step 2: Bill of Materials
Bill of Materials:
The first 4 Rods listed here are also listed in the Long Bed Conversion Instructable.
You do not need double these, listed here to make the printer BOM complete.
2 - 460mm x 8mm Smooth Rod (Y Axis upper table)
2 - 240mm x 8mm Threaded Rod (Y Axis belt tensioner mount)
1 - 470mm x 8mm Threaded Rod (Y Axis belt tensioner)
1 - 420mm x 8mm Threaded Rod (Y Axis Brace next to large printed pulley)
______________
2 - 340mm x 8mm Threaded Rod (Lower Frame Y Axis mount)
2 - 380mm x 8mm Smooth Rod (Y Axis lower table)
2 - 420mm x 8mm Smooth Rod (X Axis)
2 - 390mm x 8mm Smooth Rod (Z Axis)
2 - 340mm x 8mm Threaded Rod (Z Axis)
14 - 8mm Linear Bearings (4 used in Lower Table)
9 - 608 Skate Bearings (4 used in Lower Table)
_____________
1 - Control Board (Printrboard, Smoothie, Ramps, etc.)
1 - 12vdc Power Supply (an ATX computer power supply works well)
2 - 12vdc 200mm x 200mm Heated Beds (if 24vdc is used use correct Relays)
2 - 12vdc Relays (Provides power to heated beds)
5 - Micro Switches
1 - J-head Hot End (This design is using a .4mm nozzle)
5 - Nema 17 Motors (use Good Quality Motors)
2 - Gt2 20 Tooth with 5mm bore
3.5m - Gt2 Belt 6mm wide (Good Quality - a cheap belt WILL cause problems)
2 - Compression Springs (Z elevators)
2 - 8mm Collars (X Axis smooth rod)
Extra wire
____________
100 - M3 x 0.50 Nuts
20 - M3 x 0.50mm x 16mm Screws (motors)
40 - M3 x 0.50mm x 20mm Screws
8 - M3 x 0.50mm x 25mm Screws (lower table bearings)
17 - M3 x 0.50mm x 35mm Screws (printed lower table, extruder & Z elevator)
____________
20 - M4 x 0.70 Nuts
18 - M4 x 0.70mm x 30mm Screws
2 - M4 x 0.70mm x 50mm Screws
2 - M4 x 0.70 x 70mm Screws
____________
50 - M8 x 0.70 Nuts
60 - M8 Flat Washers
4 - M8 x 1.25mm x 50mm Hex Cap Screws (Lower Table)
1 - M8 x 1.25mm x 60mm Hex Cap Screw (idler bolt or use threaded Rod)
___________
Printed Parts
It takes about 2 - 2.5 rolls of 3mm. filament to print the frame.
Qty. to Print - File Name
- 1 - Lower Center Frame
1 - Lower Left Side
1 - Lower Right Side
1 - Lower End Plate with motor mount
1 - Lower End Plate with idler
1 - Upper Motor Mount
1 - Upper Left Side
1 - Upper Right Side
1 - Upper End Plate
_______________
The following will use about 1 - 1.5 roll(s) of 3mm. filament.
- 3 - Smooth Rod Clamp
1 - Smooth Rod Clamp with Micro Switch Mount
2 - End Stops
1 - 3072 Printed Pulley (for Gt2 belt)
1 - Lower Table
2 - Lower Table Bearing Holder
2 - Lower Table Bearing Holder (mirror)
4 - Tall Smooth Rod Clamp
2 - Wide Smooth Rod Clamps
4 - Z Axis Rod Clamp (Z Axis)
2 - Elevator
2 - Motor / Idler Mount
2 - Couplers (2 pcs per Coupler, front/back)
_______________
- 1 - X Carriage with dual 40mm fan mounts
1 - Extruder Body
1 - Idler Block
1 - Small Gear (9 tooth)
1 - Large Gear (47 tooth)
1 - Belt Tensioner Main Base
1 - Belt Tensioner Main Base Clamp
1 - Belt Tensioner Adjustable Base
1 - Belt Tensioner Adjustable Clamp
Step 3: Printing the Main Frame
If you do not have a printer large enough to print this, I have
included a link to another instructable for the large bed modification
for i2's that can be modified to fit other printers.
Link to: Long Bed Conversion for i2 3d Printer instructable.
Start by printing one of each of the following:
Prints vary from 3 to 10 hours, depending on the part, infill and print speed. No additional support was used for these parts. Some parts have support built in to the STL file, This support will need to be removed from the printed parts. All parts were printed with a wide Brim.
I have experimented with different infill amounts. Listed are the infill % that I have experimented with. Recommend printing the parts with motor mounts at a higher percentage. Experiment and see what works best with your printer, The higher the infill the more filament you will use and increased print time.
This project was printed in PLA, other material would work too.
- Lower Center Frame - - - - - - 20% to 25%
- Lower Side Frame - - - - - - - - 20% to 25%
- Lower Side Frame (Mirror) - - 20% to 25%
- Lower End Plate with motor mount - - 20% to 30%
- Lower End Plate with Idler - - - - - - - - 20% - 25%
- Upper Motor Mount- - - - - - - - 20% to 30%
- Upper Side Frame - - - - - - - - 20% to 25% (has support to remove)
- Upper Side Frame (Mirror) - - 20% to 25% (has support to remove)
- Upper End Plate - - - - - - - - - 15% to 20%
I use a 5mm brim to help keep large parts in place during printing.
Recommend thick bottom layer, walls and top layer. 1mm+
Some parts are hollow and get strength from the walls.
This printer preforms best when operating on a flat, solid surface.
_____________________
Latest percentages tried with new printer:
1. Lower Center Frame - - - - - - - - - - - - 15%
2. Lower Side Frame - - - - - - - - - - - - - -15%
3. Lower Side Frame (Mirror) - - - - - - - -15%
4. Lower End Plate with motor mount - - 20%
5. Lower End Plate with Idler - - - - - - - - 15%
6. Upper Motor Mount - - - - - - - - - - - - - 20%
7. Upper Side Frame - - - - - - - - - - - - - 15% (has support to remove)
8. Upper Side Frame (Mirror) - - - - - - - 15% (has support to remove)
9. Upper End Plate - - - - - - - - - - - - - - 15%
.25mm layer height
60ms Speed
Estimated Time: 60 hours to print
1.5 Rolls of filament
@ $40.00 per roll the Main Frame would cost $60.00 (material only)
@ $30.00 per roll the Main Frame would cost $45.00 (material only)
Step 4: Assemble the Main Frame
Clean all the parts.
Remove Brim, Support material and clear the holes for bolts.
Test fit all parts before bolting together.
There are recesses and notches where the parts fit together, these may need filing for a proper fit.
These should be a snug fit, adding sturdiness to the frame.
____________
Install bolts and nuts as you assemble, leave loose until all frame parts assembled.
Start with the (1) Lower Center Frame, attach (2) Lower Side Frame and (3) Lower Side Frame (Mirror).
Lower Center Frame is a mirror image either way is correct.
____________
Add the (4) Lower End Plate with Motor Mount to the short side of the (2)&(3) Side Plates
Add the (5) Lower End Plate with Idler to the tall side of (2)&(3) Side Plates.
___________
If you plan to zip tie or keep the wiring on the outside of frame skip routing wires through frame.
_________
Route your motor wires through the frame:
Remove the plugs from the nema 17 motors and route wires though the hole on top of (6) Upper Motor Mount.and use the wire path to go across to the side of (6) Upper Motor Mount your control board will be located.
Secure motors with 1 bolt, rubber band, tape etc. Motor will need to be movable, to install a bolt later.
_________
Route some scrap wires through (8)&(9) Upper Sides, These will be used to fish (pull) end stop, auto level, and
motor wires through the frame leave 200mm extra wire at each end. (I put extra wires in in case of a failure.)
___________
Install (8)&(9) Upper Sides to the (2)&(3) Lower Sides. Guide the scrap wires into the hole in the Lower Sides,
This is a tight fit and the wiring hole may need enlarging. You will need to gently force the mounting tabs of (8)&(9) past (2)&(3) To get the parts assembled.
___________
Add the (9) Upper End Plate to the frame assembly. (This also has a wire path if you want to use it).
___________
Add the (6) Upper Motor Mount to the frame assembly.
Move the motor to install the bolt behind the motor.
Add a 4mm x 70mm bolt to join the (6) Upper Motor Mount to the (7&8) Upper Sides.
(or use a piece of threaded rod).
___________
Finish routing all the wires through the frame. (remove any extra scrap wire(s) you may have added)
___________
Check for square as you tighten all the bolts in the frame.
Step 5: X & Z Axis Assembly
Print and Clean all of the X & Z Axis Related Parts
________________
LUBE ALL LINEAR BEARINGS BEFORE STARTING ASSEMBLING
________________
X Axis:
Assemble the Extruder
Install Linear Bearings for X Axis Carriage
Add 40mm Fan(s) to Carriage (if wanted)
Add the Belt Tensioner Base (install a nuts in the nut traps)
Attach Extruder and Hot End to Carriage (Motor is Aligned with Widest Part of X Carriage
______________
Z Axis:
- Loosely Assemble the Motor Coupler.
Install Linear Bearings to the Elevator and Motor/Idler Mounts.
Wire and install the Micro Switch in the Z Elevator.
Assemble the Z Elevator, Nut, and Spring on the Threaded Rod.
Put 2 - 8mm Nuts below the Z Elevator appx. 40mm from end of Threaded Rod,
Slide a Skate Bearing on the Threaded Rod.
Repeat for the Other Side.
_____
Take one of the Z Axis Assembles :
Add the X Carriage Motor/Idler Mount above the Z Elevator.
Lower the Z Assembly in the Bearing Holder in the Lower Center Frame.
Do you have tubing on your motor? (if not add a short piece of tubing to motor shaft)
Note: (motor is 5mm the threaded rod is 8mm)
Add the Motor Coupler to the top of the Threaded Rod and Slide Coupler on to Motor.
Install Screws for Motor (leave loose for now)
Seat Skate Bearing into Bearing Holder
Screw the Double nuts Closer to Bottom to Support the Threaded Rod.
Attach the Smooth Rod to the Frame with Z Axis Rod Clamps
All of Z Axis Assemble Should have all the Nuts and Bolts installed But loose.
Repeat for other Side
_____________
With both Sides Assembled:
Assemble The X Axis:
Partially Slide the Smooth Rod Trough the X Carriage Motor/Idler Mounts.
The smooth rod hole in the Idler Side of the Motor/Idler Mount is larger than,
the smooth rod hole Motor Mount side.
This is to stop the Smooth Rod from passing through.
Put 8mm collars on the Smooth Rod used on the GT2 belt side of the Motor/Idler Mount.
Slide the Smooth Rod through the Motor / Idler Mount, (idler side),
add one of the 8mm collars,
then put the Extruder/Carriage Assembly on Smooth Rod, (check for correct alignment)
(The motor, belt tensioner of the Carriage Assy. and Belt Idler all on same side)
add the other 8mm collar,
and Continue Pushing the Smooth Rod Until it hits the Stop in the Printed Motor/ Idler Mount.
Slide the other Smooth Rod Through the Motor/Idler Mount,
then though the X Carriage,
and Through the Other Motor/ Idler Mount.
Move the X Axis Assemble up and down a few times to align the bearings in the Linear Bearings.
It should move freely, (if not moving freely check to see if Linear Bearing Clamp
is to Tight).
Position the Collars Next to the Motor/Idler Mounts, and Tighten set screw.
Tighten the Screws in the Motor/ Idler Mount.
Move the X Carriage Left and Right a few times to align the Linear Bearings
Install X axis Motor with Pulley set screw loose and Tighten the screws for Motor.
Install The Idler Bearing Assembly and Tighten.
Route the GT2 Belt Around the Motor Pulley and Idler Bearing,
Fasten the one end of the Belt to the Belt Tensioner Base (nuts should already be in the nut trap)
Fasten the Belt to the Belt Tensioner Adjuster.
Attach the Belt Tensioner Adjuster to the Belt Tensioner Base,
and Tighten Screw to Tension the Belt.
Route the X Carriage Related Wiring to Control Board.
_____________
There is a non working motor added to the Idler side of the X Axis (Motor/Idler).
This helps balance the weight of X Axis making the Autolevel measurements accurate.
Any weight equal to the X Axis working motor would work.
Step 6: Y Axis Assembly (upper and Lower Tables)
Start with the End Plate with Motor Mount.
Put:
- Nuts
Washers - Bearings
- Smooth Rod Clamp
- Smooth Rod Clamp with Micro Switch Mount
on Threaded Rod as shows in picture.
___________
End Plate with Idler Mount.
Put:
- Nuts
- Washers
- Bearings
- 3072 Printed Dual GT2 Pulley
- Smooth Rod Clamps
on Threaded Rod as shows in picture.
_____________
Install: Linear Bearings in the Lower Table Bearing Holders. (leave screw loose for now)
Attach: Lower Table Bearing Holders to the Printed Lower Table (or your own table design)
Add the Skate Bearings with a washer on each side of bearing.
Slide the 380mm Smooth Rods Through the Linear Bearings (closest to the printed table).
___________
Slide the 460mm Smooth Rod Through the Upper Bearings (Next to the Skate Bearing)
Put a Tall Smooth Rod Clamp on the end of each 460mm Smooth Rod.
Add a Smooth Rod Clamp with nuts and washer to each of the 240mm Threaded Rods.
Slide a 240mm Threaded Rod Assembly through the Tall Smooth Rod Clamps on each end.
Add the belt tensioners, nuts, & washer to the 470mm Threaded Rod.
Put the Tensioner assembly through the Smooth Rod Clamps on the upper bed.
Position the Tensioner Assembly near the center, (leave nuts loose for now).
_____________
The Long Bed travel assembly should be complete. (But the bolts are loose)
Put the Long Bed Travel Assembly in to the Main Frame End Plate's Smooth Rod Clamps one at a time.
Do One end and repeat for the other end.
Measure and adjust as necessary to get the Long Bed Assembly Centered in the Main Frame.
Tighten the nuts on the Main Frame End Plate's Threaded Rods evenly.
Slide the Table Assembly back and forth as you tighten the nuts.
________________
With the Lower Smooth Rods Tight and Table Assembly Centered.
Tighten the Lower Linear Bearings Clamp (check free movement of Table Assembly.
Tighten the Upper Liner Bearing Clamps (checking for free movement of the Entire Table Assembly.
Slide the Table Assembly Back and Forth to align the linear bearings.
You should have Full movement of the Long Bed at this time.
________________
Install a belt for the Lower Table.
- Going around the 3072 printed pulley (small side) around the Skate Bearing.
Make a loop in the end of belt and zip tie the loops.
Bring both belt ends to the slot in the printed table.
Fasten to a long Bolt in the slot of the lower table. (zip tie work well here too)
________________
Install a belt for the Upper Table
Step a:
Start at the Nema 17 Motor (motor screws should be tighten and motor pulley Loose).
Go from the Upper side motor pulley to the far end of the Upper Table Assembly Belt Tensioner above the
3072 Printed Bearing.
Go through the hole in the Belt Tensioner for the belt and zip tie the loose end of belt back to the main part of belt.
_________________
Step b:
Take the other end of belt at the Nema 17 Motor
Start at the Nema 17 Motor pulley, Bottom side
Go under the Lower Center Frame to the 3072 Printed pulley (large side).
From the pulley (top side) back to the Upper Table Assembly Belt Tensioner above the motor.
Go through the hole for in the Belt Tensioner for the belt and zip tie the loose end of belt back to the main part of belt.
________________
Move the skate bearings and 3072 Printed Pulley in to operating position.
Align the Motor Pulley for proper alignment and tighten set screw.
Tighten all bolts evenly on the Long Bed Assembly.
Use the Belt Tensioners to adjust the Upper Table belt.
See Picture for Belt path Detail.
DO NOT OVER TIGHTEN THIS BELT !
With the M8 threaded rod and nuts, you can easily damage the Printer.
________________
Install a print surface of your choose to the Tall Smooth Rod Clamps.
It may be necessary to shim or file the Tall Smooth Rod Clamps attached to:
(Printing Plate) or (heated bed Mounting Plate) which ever you use.
The Skate bearings need to be in contact with your plate.
This maintains the proper distance between Hot End and Printing Surface.
________________
Review all connections and tighten as necessary.
Heated Bed Information will be posted after parts arrive and assembled.
The Printer should be ready to continue wiring, testing, and Printing : )
Step 7: Heated Bed Information
The Printer should have all the bolts tight and the bed moving freely.
No build plate installed yet.
Use the pictures above as reference to the following instructions.
____________________
To make the Heated Bed Wire Cable you will need:
10 wires (I started with each at 200 Centimeters long)
4 Wires 16 Gauge (power to Heated Bed)
6 Wires 22 Gauge (Sensors)
125 Centimeters of wire sheathing
Put about 60 centimeters of the completed Wire Cable outside the frame and Zip Tie the Wire Cable to the Lower Center Frame (refer to picture).
Make a loop with the Wire Cable going though the area between the bearing holders. Above the Lower Smooth Rods and under the Upper Smooth Rods.
Loosely Zip Tie the Wire cable to the Idler End of the Upper Table Frame.
Move the Upper Table Frame from one end to the other end. (home 0mm to Max 425mm) adjust the size and position of the loop for smooth operation of the table. Tighten and trim all Zip Ties after smooth operation is accomplished.
Run 2 Wires 16 Gauge and 2Wires 22 Gauge to the Motor End of the Upper Table Frame.
Zip Tie these wires to the Threaded Rod of the Upper Table Frame.
Install your build surface to the Tall Smooth Rod Clamps.
Check for proper spacing between build surface and skate bearings.
Shim or sand the Tall Smooth Rod Clamps so the skate bearings are in contact with the build surface.
Position your heated beds checking for best alignment with the Hot End for Maximum X Axis travel. Mark the locations to drill mounting holes for the Heated Beds.
After holes are drilled reinstall the build surface trim the extra wire and solder the Heated Bed power wires. Assemble the sensors to the 22 Gauge wires. Secure the sensors and wires to Heated Beds with Kapton tape.
I used Relays with adjustable temperature settings, the sensors allow for a max temperature to be set.
The 1 Sensor near the center of the print area is connected to the Control Board.
Fasten the Heated Beds to the build surface, Insulate the soldering pads if using Heat Spreader Plate.
And secure glass for printing area to the upper table.
Zip Tie all loose wires and Trim the sheathing as needed.
Wire one side of the Heated Bed Power wires to the Normal Open side of the contacts and the other to Common for VDC Heated Beds.
Use the Heated Bed Circuit on the control board to active the coils of the Relays.
Inspect / Review ALL Electrical connections be turning the power on.
When connected to Host program turn on the Heated Beds and set the pots on the relays for maxim temperature
Step 8: Optional Builds
If you do not want or need a Long Bed:
A print bed heated or non heated bed could be used.
Use the Smooth Rod Clamp to hold the Y Axis Rods.
And attach a Bearing Holder to the Table.
Slide Table Assembly on to the Smooth Rods and attach the GT2 Belt.
________________
Do Not want to use Auto Level:
Use the spring method to level the bed.
And the Back up Z end stop for homing the Z Axis.
Step 9: Download Files
ALL Files Have Been Uploaded
Any problems with files let me know.
If you have nonmanifold issues run through netfab etc.
The upper side frames give that error but have not found the hole yet
All files Print for me without any problems.
Thanks for all the comments!
- Download
- Clean
- Assemble
- Enjoy :)
Look forward to seeing some success builds of this project.
Step 10: Printer Information, Design Udates, Pictures and Videos
Printer Information:
This printer was commissioned on - April 11 2015 @ 8:pm
Calibrated to .5mm. - April 14 2015
Design Updates:
Add another Threaded Rod to the lower assembly next to large pulley.
Speeds up to 50mms Y axis preformed very well.
Speeds above 60mms and the belt on the motor pulley jumped once.
New good quality belt, but an older pulley. Pulley could be the issue,
new pulley has been ordered. Adding extra rod until pulley arrives.
Print new part: 2 pcs. Wide Smooth Rod Clamp, install with threaded
rod, nuts, and washers next to large printed pulley.
With extra support in this area, will be able to tighten belt more and try speed test again.
Videos:
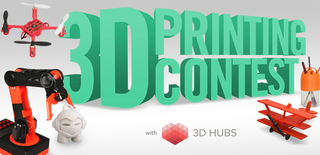
Runner Up in the
3D Printing Contest