Introduction: Low Cost Plastic Blasting Cabinet
My wife lives to craft. If there's a craft that's been mentioned in a blog somewhere, she wants to give it a go. Her latest pursuit is glass etching with abrasives. I've never been a fan of her using chemical etching products because of the significant health risks (read an MSDS on hydrofluoric acid!!!). So naturally I wanted to help her move in a safer direction. She found a low cost "Air Eraser" from Harbor Freight. When I mentioned a blasting cabinet, she also tracked one down at harbor freight. The low cost HF unit costs about ~$160, is pretty bulky, and is really overkill for how she wants to use it. After a brief google search, I found plenty of DIY units made from a wide variety of materials (yes, I know there are a couple similar instructables --thanks "kington99"(https://www.instructables.com/id/Homemade-ShotGrit-Blasting-Cabinet/) and "DIY Hacks and How Tos"(https://www.instructables.com/id/DIY-Glove-Box/) for ideas). So when my wife asked, "well, can you make one of those?", I said, "No problem".
My goals for this project were to keep it cheap, keep it contained (no leaks), and keep it small and light enough to store on a garage shelf. My cost for the plastic blasting cabinet was around $50. I went to a fair amount of effort to ensure that all openings were reasonably sealed while creating a filtered vent to relieve pressure. Finally, the "cabinet" shares the dimensions of a normal bin that I already have on my garage shelves so storage won't be a problem. I think I'm on track to meeting my goals.
Step 1: Inventory
Materials
1x-Transparent 66quart plastic storage bin with latching lid
2x-3"x4" ABS Toilet flange
16x-#10-32x0.75" Bolts
16x-#10-31 Nylon locking bolts
16x-#10 Washers
1x-Rubber, long cuffed chem gloves
1x-1.5" Rubber flange with 0.375" center
1x- 0.375" Weather stripping
1x-Silicone
1x-.75" Plastic tube
1x-Sponge (from aquarium sponge filter)
1x-0.25" Ball Valve
1x-0.25" Air regulator with pressure gauge
1x-0.25" to male FPT air plug
1x-Ptoilumbers tape
Tools
Tape measure
Jigsaw
Drill
Wrenches
Scissors
Screwdriver
Step 2: Measure and Cut Holes for Flanges
Try to place your flanges for comfort and to ensure that there is sufficient space to see into the plastic bin between them. I placed them near the sides/bottom but not so close that the round edges of the bin would create a problem with mounting the flanges. After marking the holes with a Sharpie, I drilled a starter hole and then used the jigsaw to cut out the porthole.
Step 3: Mount the Gloves
The toilet flanges I used had 8 holes, each, for hardware. I first drilled holes for the bolts through the sides of the bin using the flange as a guide. I then placed a glove over the male end of the flange and inserted it into the bin's porthole (from outside-in). The chem gloves I bought happened to have a cuff on the edge of the gauntlet that worked like magic to retain the glove between the flange and the bin (on the outside of the bin). If the gloves you purchase don't have such a nice cuff, you can use 4" screw clamps to secure them to the flange. I had screw clamps in my original design but didn't need them. I also laid down a heavy bead of silicone around the porthole and each bolt hole to ensure that the openings had a really good seal. I don't want any abrasives blowing out towards the user. Finally, I secured the flanges to the bin using the bolts with a washer and locknut on the inside of the bin.
Note on the toilet flanges: Many similar plastic bin blasting cabinet designs I've seen use a PVC coupling or just an open hole. The toilet flanges I bought were actually cheaper than a 4" PVC coupling plus have the added benefit of allowing me to better seal the hand openings.
Step 4: Airline for the Tool
I don't know where I read it, but someone recommended an inline ball valve and regulator be placed close to the tool for fine-tuning of air-flow and to allow the pressure to be shut off temporarily. I want to make this as user-friendly as possible so I added the hardware. The air eraser tool comes with a 0.25" threaded female fitting so it will connect to the regulator perfectly. I first mated the regulator, ball valve, and male NPT fitting together using teflon plumber's tape to create a good seal. I just happened to have a 1.5" rubber grommet with a 0.375" opening that fit the air eraser's line well, so I used it to create the opening. I drilled the appropriate size opening in the bin with a hole saw. Then I placed the grommet in the hole, once again, using silicone to seal it.
Step 5: Add a Vent
You may have noticed that I sealed up all of the openings in this bin so far. Some of you might be thinking, "as soon as he starts blowing air into that thing it's gonna explode." While I don't think I did that great of a job sealing this thing, I chose to err on the side of caution. So I needed a pressure vent that will keep the abrasive media inside the cabinet. It was time for a trip to the "left-over junk bin" I keep in the garage. I found a 0.75" plastic spacer and a left-over (unused) sponge from an aquarium filter. The sponge should trap the abrasive media while allowing air pressure inside the bin to equalize with outside air. I cut a chunk of sponge to fit (slightly compacted) inside the spacer to create the vent. Then I cut another hole in the bin. Finally, I inserted the vent and sealed the edges.
Step 6: Seal the Lid
The final step was to seal the lid. The lid of the storage bin I chose has a latch on either side to help secure it to the bin. It should also help compact the weather stripping just enough to make a good seal. I placed a line of weather stripping all around the top edge of the bin and checked the fit.
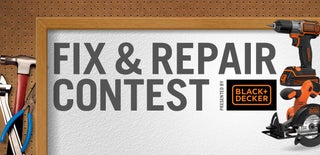
Participated in the
Fix & Repair Contest
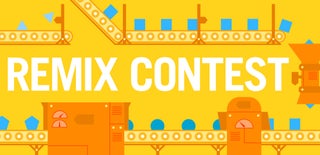
Participated in the
Remix Contest