Introduction: Make Your Own Shoes at Home!
This is an instructable for making your own pair of shoes with materials you can buy in an art store or a fabric store. I base my technique off of traditional shoe making methods, but you won't need expensive materials, a nice set up, or complex tools.
This method will also create perfectly fitting shoes as the pattern will be drawn from your own feet!
The total cost of this project is less than $50 and, will take under 20 hours.
*Note: if you choose not to use leather, you shoes will probably be best as indoor-only shoes*
Materials:
The Shoe
2 sqft 1/4" thick cork (OR shoe leather, which can be bought at a shoe repair store)
1 yard of each fabric/leather used on the outside of the shoe
1 yard of the fabric used on the inside of the shoe
Thread (thicker is best)
8+ Eyelets
Shoe laces
Masking tape
Superglue (or Shoe Goo)
Paper
The Last (cast of your foot)
13+oz. of alginate
64+oz. of Permastone (or another casting material like rubber)
Cardboard box
Tape
Tools:
Scissors
Retractable utility knife
Eyelet puncher (usually comes with eyelets)
Marker
Pliers
Needles
Awl
Cutting mat
Step 1: Generate a Concept
The most important step in any project is the design phase. Think about the type of shoe you want to make and do some sketches.
For my shoe, I ended up wanting to do a fancier-looking dancing shoe with a wider end that wouldn't constrict my toes.
Step 2: Making a Last
We need to make a last before we do anything.
A "last" is a hard, usually wooden, object that shoemakers build their shoes around. Lasts look like feet, with extra space in front of the toes to accommodate the sleek pointed style common in shoes.
Lasts are important because they allow you to accurately draw your patterns, give you a harder surface to work with, and they also provide a quick context when you are unsure.
Here you have two options:
1) Buy a last: ask a shoemaker or do an Internet search (these are not expensive)
2) Make a cast of your foot and augment that.
I'll teach you how to make your own lasts, but if you choose to buy some, they aren't very expensive.
Step 3: Casting Your Foot: Preparation
Making lasts is a great way of ensuring a perfect fit for your feet. For this process, you will need alginate to make a mold of your foot, a casting material, and a box to hold your mold in.
To make your mold, you first need a makeshift box for your foot.
Leave plenty of room around your foot (note: the more space you leave the more alginate you'll need to use).
Step 4: Casting Your Foot: the Mold
Time to make your mold, which is a negative of your foot. Alginate can be found at most craft stores. It's non-toxic and good for single-use molds. I'm using a 13 oz bag, which costs around $8. You may want to use a bag and a half, but we can make do with a single bag. This material will not damage your tools.
First, mix the alginate and water in a large mixing bowl. You can use a spatula, but your hands are the best mixers. You will use around 6 cups of *COLD* water for an entire bag, but I highly recommend you add water gradually to your mixture isn't too liquidy.
The alginate is ready to pour when it is gloopy.
Working quickly, pour the mixed alginate into the box you've made.
Put your foot in the box. Depending on whether you want your shoe to conform to your foot flat on the ground or not, you may want to suspend your foot in the alginate without letting it touch the ground.
Your foot should be covered to slightly above the ankles in alginate. If you don't have enough alginate add some napkins to the empty space in the mold to fill it out.
Wait for about 20 minutes until the alginate solidifies into sturdy jelly.
Step 5: Casting Your Foot: Removing Your Foot
Remove your foot from the alginate mold. Be careful as you do this; the alginate will hold well, but you don't want to rip chunks off.
If you are worried, you can use a utility knife to *carefully* cut along the top of your foot to pull your foot out.
Step 6: Casting Your Foot: Casting
You will need about 5 cups of your casting material for an average male shoe size (estimate). I am going to use Permastone, which is inexpensive and more durable than plaster. If you find yourself short of material, you can add filler in the form of napkins (as with the alginate mold) or powders like sawdust.
Mix your material according to its instructions and pour it into your alginate mold. Put your bowl and mixer in the sink under running water while you work to minimize the risk of damage to your tools.
Tips:
1) Tilt your box back and forth to make sure you get it into the toes and crevices.
2) Tap the sides of the box hard, shake it against the ground, and continue tilting it until to force air bubbles to the surface. This is satisfying.
Remember though, we're doing this cheap and easy, so your mold probably won't be perfect and that's OK.
Let your cast sit until you're sure it's dry.
Note: I am using PermaStone, which is pretty cheap ($6 a box), but you can substitute another material such as rubber if you have the means. I do not recommend plaster, as it takes forever to dry and it is fragile.
Step 7: Casting Your Foot: the Pull
When your material is dry, take apart your box so you have a big cube of alginate.
Don't be shy: tear your alginate apart to reveal your mold. Don't worry about the alginate, it's meant for a single use.
If you are planning on wearing your shoes, you'll want to make the other foot as well :)
Step 8: Making Your Foot Cast Into a Last
Following your shoe design, crumple up tape and add it to the front on your cast to round off the end as you desire.
It is important that you are satisfied with the shape of your last, because the shape of the last determines the shape of your shoe.
Step 9: Cover Your Last in Masking Tape and Draw Your Pattern
Wrap your entire last in two or three layers of masking tape (You need to cover the bottom of the last too!).
Then, carefully draw the patterns for your shoe design on the tape.
Finally, Cut your masking tape pattern along the lines you drew with your utility knife.
*Importantly,* continue your cuts down onto the bottom of your last at least 1". You will need this extra fabric to properly sew your shoe together in later steps.
Your pattern should consist of at least four parts (see the diagram).
1) Vamp: This part covers your laces and moves down to the bottom of the shoe
2) Counter: This is the back of the shoe. It is usually stiffer to give the shoe shape (but not necessarily)
3) Toe: The front of the shoe
4) The... other part: This part is in between the front of the shoe and the vamp.
* Note: This process could also be used to copy the pattern of a shoe you really like *
Step 10: Flatten Your Patterns
Remove your patterns (careful not to tear them) and flatten your 3-D patterns into 2-D patterns.
If you need to, cut darts (triangles) into the extra few inches of pattern from the bottom of the last to help the patterns flatten.
Step 11: Trace & Cut Your Patterns
Trace your patterns on paper.
Add a 1/4" seam allowance on all your patterns.
If you are a new sewer, you may want to add even more allowance so that you can "fudge" your shoe construction.
* Note: remember to draw a pattern for a shoe tongue as well (a rectangle whose shape is determined by your design). *
Step 12: Making Your Patterns More Useful
In the last step you drew your patterns on paper, and then drew an extra seam allowance.
If we left things here we'd have a problem: when stitching the fabric pieces together again it would be difficult to allow for the seam allowance purely by eye.
So in this step we cut out small pockets along the original pattern tracing so that we can mark our materials in the next step.
Step 13: Cut Your Fabric
Arrange your patterns on your fabric. Using either tape or pins, stick the patterns onto the fabric.
Using a pencil or marker, lightly outline the patterns on the fabric and remember to mark the seam allowance in the holes we cut in the last step.
Cut your pieces out.
* Note: remember that you are cutting your patterns twice: once for the outer material and once for the inner material. *
* Note: consider which side of your fabric you want showing. *
* Remember: Keep your paper patterns; for the opposite shoe you will flip your patterns over and repeat. *
Step 14: Sewing Pattern Pieces Together
You now need to sew all of your patterns together. If you aren't familiar with sewing, check out these next few steps for help.
There are two ways you can stitch your pieces together. Consult the photos.
The First Way:
Line your patterns up and pin them together so that the seam allowance guides you marked follow each other. This may be a little difficult.
Sew within your seam allowance. It is important to sew in a straight, smooth fashion or your seam will look messy when you invert the fabric.
The Second Way:
Depending on your style, you may want to cut the seam allowance off *one* of the two patterns, simply overlapping it with the adjacent pattern so that its edge lines up with the seam allowance markings you drew earlier.
Once lined up you can stitch your pattern without needing to invert the fabric later. I did this on the outside of my shoe, using the white string in my stitching to accent my black leather pieces (see photos).
*Note: user Lukieh suggests that machine-sewing or saddle stitching would improve the durability of the shoe, wherever sewing is required. I wholeheartedly agree. The stitching in this instructable is done in haste primarily, so, without a sewing machine, I didn't bother to saddle stitch.*
Step 15: Sewing Tip: Darts
Sew your patterns back together can be straightforward if you know how to sew. If you don't here are some tips.
*Before you begin, know which side will be showing and which side will be hidden (by the other fabric layer.) and work on the hidden side.*
Sewing your darts back together will give your patterns shape.
To sew these back together fold your fabric such that the corners of your two edges line up.
Grip the point where the actual lines on the pattern (excluding the seam allowance) meet with one hand and sew towards it with your needle/sewing machine.
Once you get to the point you're gripping, turn your sewing around and stitch back to the edge to ensure a strong stitch.
Refer to the photos.
Step 16: Sewing Tip: Tying Off Your String
Once you've finished a stitch tie it off.
The way I do this is by beginning a simple knot and then using my needle to guide the knot down close to the fabric.
Step 17: Sewing Tip: Use Your Last As a Reference
Messing up sucks, but you can easily avoid problems if you constantly refer to your design and use your last as reference.
Step 18: Sewing Tip: Working With Leather
Leather is pretty tough to stitch through, so if you're using leather and you don't have a capable sewing machine, I recommend banging your holes into the leather before you begin stitching.
You don't HAVE to do this, but it will save you some frustration.
Using a $4 awl and a hammer (and a cutting mat/book I didn't want), I banged each hole into my leather.
Step 19: Attaching the Outer Fabric to the Inner Fabric
Sew your pieces together until you have the two separate layers: the outside pattern and the inside pattern.
Now, you'll need to sew the inside pattern to the outside pattern.
To do this line your seam allowances up (*with the wrong sides of the patterns facing outward*) and stitch along the 1/4" seam allowance you cut out earlier.
Step 20: Flip Your Patterns Back Over
Make sure your sewing is neat and tight and when you have finished going completely around the ankle and the sides of your vamp (where your shoe laces will be) flip your pattern over.
Step 21: Shoe Tongue
Don't forget about the shoe tongue!
To make this you'll want to take your two shoe tongue pieces, the outer and inner, and line them up, their wrong sides facing outward.
Sew along the 1/4" seam allowance on both of the sides and the top of the tongue. *Do not sew the bottom of the tongue shut.*
Next, forcibly invert the tongue through its bottom (see photo).
If your corners aren't fully inverted you can push them out with a closed pare of scissors.
At this step you'll want to tack on your shoe tongue with a few stitches in discreet places.
*Tip: sew some extra stitches around the bottom of your tongue sides to add some reinforcement.*
Step 22: Adding Eyelets
Before we move on to the sole of the shoe we need to add eyelets and laces to the "upper."
Eyelets are the holes where your laces will be threaded.
Depending on what your design, you can either make holes in the fabric itself, or you can add metal eyelets. It's up to you.
A fancy eyelet tool will cost you $20, but you can packs of eyelets often come with simpler tools that do the same thing.
To add eyelets, mark the places on your fabric where you want to add shoe lace holes and, according to the instructions included on whatever tool you're using, punch holes or cut holes, place your eyelet pieces in, and punch them together. It's pretty simple!
Step 23: Add Shoe Laces
Put your last inside your upper to fill its shape in.
Pick a pair of laces you're happy with and tie your shoe for the very first time. Don't tie it so tight that your pattern distorts.
At this point you are essentially done with your upper and we will be moving on to your soles.
Make sure you have:
1) sewn your patterns together.
2) sewn your outer fabric to your inner fabric layer
3) punched eyelet holes
4) sewn your tongue on
5) added laces
Step 24: Soles
We are going to move on to the shoe sole. There are three parts of shoe soles.
1) The insole: this is the part of the shoe that your foot comes in contact with. This must be slightly soft.
2) The midsole: this is a part of the shoe we won't need to be making. Typically the midsole is curved to provide arch support.
3) The outsole: This is the bottom of the shoe that makes contact with the ground. Usually made of sturdy leather or rubber.
I will demonstrate everything using 1/4" and 1/8" cork, which is easy to find at any place with architectural supplies.
Begin by tracing your last on a piece of 1/4" cork. Make sure you add around 1/2" extra so that you avoid cutting something too small.
Cut out your sole with a utility blade.
**These steps also work with shoe leather, which you can buy from a shoe repair store for around $30 a sole**
Step 25: Shaping Your Insole
Soak your cork/leather sole in water for 24 hours.
Tie your sole to your last tightly so that it conforms to the shape of your foot. Set it in the sun and let it dry.
The sole will keep the shape of your arch when you untie it.
Step 26: Pare Down Your Insole
Hold (or secure) your insole to the bottom of your last.
Since you left some extra material around your foot tracing, you should have some paring to do.
Using your utility knife, carefully shape the insole to fit your last.
I urge you to be careful. If you are using a harder material like sole leather cutting can be difficult. My best advice is to take your time and be happy cutting only a little away with each cut.
You'll be paring down the rest of your sole pieces in the exact same way as you do here.
Step 27: Preparing to Sew Your Upper to Your Sole
Cut out another sole.
Then, cut a ring out of the sole about 1/2" from where your sole begins (see the photos).
Affix this ring onto the bottom of your insole with superglue or another strong glue.
Shoemakers use something called "Shoe Goo," which is best for this project but harder to find. It also takes hours to dry and stinks, so super glue is fine!
Do not throw away the other pieces of the sole from this step.
Step 28: Sew Your Upper to Your Sole
Put your insole and last into your upper (with its laces tied). Because your patterns continued onto the bottom of your last, you should have extra fabric that hangs down past the sole.
Hold the fabric tightly against the ring of sole you glued on in the previous step.
Now, using as thick a string as you can find, stitch through the fabric, through the ring of sole, and back, continuing around the entire shoe, pulling fabric tight as you go along.
This can be time consuming and irritating, but one thing you can do to ensure this process goes forward is keep your needle level as you pierce the ring of sole.
Expect to have a lot of excess fabric on the other side of your stitching.
*Note: One tricky area is the heel of the shoe, which can be difficult to maneuver in. You can always pierce the sole diagonally if you have trouble at this point.*
*Note: If you have trouble pushing your needle through consider using pliers to pull it through.*
Consult the photos if you aren't sure what to do!
Step 29: Cut Off Excess Fabric
Once you've completely sewn around the shoe sole you should have some excess fabric. Use your utility knife to shave this fabric off.
Your shoe is coming together!
Step 30: Glue in the Extra Material for Your Sole
Remember those sole pieces I told you to keep a few steps ago?
Glue them into your sole now! You may have some problems putting the outer ring on, so you can trim some material off of the inside to make room for the fabric you sewed on.
As with the insole, use your utility knife to trim off excess sole.
Step 31: Add a Heel And/Or Treads
If you want a heel or some treads just add another layer of cork or leather!!
Step 32: Finish the Sole
Add a final, thinner layer of cork or leather (the normal width is fine for that) to cover all the work you did affixing the sole to the upper.
I used 1/8" cork.
As always, trim off extra cork that you have.
*Note: If you plan on using your shoes outdoor and you didn't use leather you can shellack your shoe to add some integrity to the material.*
Step 33: Appreciate Your Shoe and Make the Other One
Woo! Your shoe is officially done!
Put it on and see how it fits. The shoe I made with cork was extra light and flexible, but still pretty classy looking.
Now you have to make the other shoe :)
You should definitely make a cast of your other foot, but you won't need to draw your patterns again.
Take the paper patterns you drew and turn them over. If you made your right shoe first the flipped over patterns will fit a left shoe perfectly and vice versa.
Good luck and I hope you enjoyed this homemade shoe Instructable!
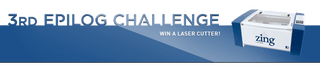
Participated in the
3rd Epilog Challenge