Introduction: Make a Graphene Supercapacitor
This Instructable (loosely) follows the method of graphene production described by C&EN, who cite a paper published by Parvez, Wu, et. al. In the paper (Exfoliation of Graphite into Graphene in Aqueous Solutions of Inorganic Salts), it is explained that putting a graphite electrode and a platinum electrode into a solution of inorganic salts (ammonium sulfate works best, they say) with a 10V supply (graphite = anode, platinum = cathode) causes the graphite to be torn apart by electrochemical activity to become graphene! Graphene has attracted much hype and study recently. One of its near-term applications may be in high density supercapacitors.
Attachments
Step 1: Making the Graphene
To make the experiment conditions described in the paper, pure platinum was required for electrode material. Unfortunately, all I had on hand was 90%/10% Pt/Ir wire, a deplorable situation no doubt shared by many in the audience. (Those who do not have either on hand may try gold, or carbon, but I have not tested these.) Also, instead of graphite sheet of some sort that was used by the referenced experimenters, we used a piece of graphite mold blank. This choice is probably why our experiment time was around 19 hours but the published one was 3-5 minutes. Surface area to volume ratios...
To make graphene, you need:
10-15V supply, a car battery would work
0.1 molarity solution (NH3)S04, in water, and awareness of how to calculate molarity (ammonium sulfate weighs 132.14 g/mol)
graphite, we used a piece of a mold blank (it may be possible to use carbon fiber but I haven't tried)
Pt electrode or platinized electrode or possibly many of the noble metals (we used 90%/10% Pt/Ir wire)
See attached lab notes for a detailed description of the exfoliation procedure as completed by me.
Step 2: Making a Capacitor
To make a capacitor for testing, I used two carbon rods extracted from "heavy-duty" (leclanche, carbon-zinc) cells as electrodes, and poured settled graphene mixed with paper pulp around each. Paper separators were glued in with hot-melt adhesive to enable compartmentalization of the graphene (it can't touch). Then, imprecisely mixed sodium chloride contaminated with iodine was poured into each compartment (and stirred with the graphene). This structure can be tested for capacitor action.
Step 3: Test the Capacitor
I found mine wouldn't light an LED. However, when tested with a millivoltmeter after being charged to 2.2V, it did have a capacitor-ey type of curve, though it doesn't seem to be good for storing more than 0.7V without really high self-discharge. A table of values for the capacitor's voltage vs. time with just a 10MOhm meter in parallel with it is included in the lab note transcript.
-V
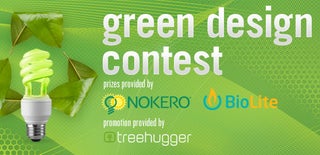
Participated in the
Green Design Contest
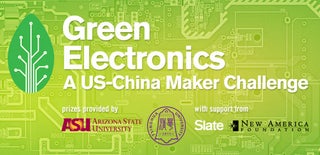
Participated in the
Green Electronics Challenge

Participated in the
Gadget Hacking and Accessories Contest