Introduction: Make a Stamp From Metal Type (Sort)
I made this stamp of our first initials with an ampersand for my wife for Valentine's Day. Since she likes sending handwritten letters, I thought this would be great for stamping on an envelope or as a signature. This was a fun, quick build (~4-5 hours) and made a meaningful gift at the end. It cost about $16 in materials, plus I bought a few tools I didn't have.
Metal type (or sort) can be found through a variety of ways. I managed to get these from a flea market in Washington, D.C. for $10, but you can also go to ebay or auctions.
Step 1: Step 1: Gather Your Materials
Here's your needed materials:
- The type you plan to use (I suggest all the same font/size)
- 1 block of wood (I used walnut) that is about double/triple the size of the type. My set of type was about 2"x1 1/2"x3/4" so my block of wood was about 4"x4 1/2"x1 1/2"
- 2 O-Rings that are able to fit around all your type
- 2 part epoxy
- Danish oil (you can use stain instead, if you prefer)
And the needed equipment:
- A rotary tool with cone and barrel cutting bits, along with a drill and sanding drum bits
- 220 grit sandpaper
- A pocket knife or chisel
- A small foam brush or a bunch of paper towels
- Pencil & paper
- Ruler
- Saw (if your block of wood needs to be cut down)
- I would suggest a small vice to assist you
Step 2: Step 2: Layout How It Will Look
Measure out how big your type is and see how you will line it up against the block. I made it twice as tall as the type, in order to have room to cut a groove for the handle. Draw your outline onto all sides of the block.
Take the pieces of type, outline them on a piece of paper as a guide for drawing the space on your block. Measure the guide, then measure the block to align it to the center of the the base. After that, trace the guide and make sure it's clear where you will be cutting by filling it in.
It is key to remember that you are not setting the entire piece of type in the block, but are going to leave some sticking out where the letters are. Take this into account when measuring and cutting.
Step 3: Step 3: Cut the Block to Size
I would suggest securing your block in a vice. This one was $20 and attached to my porch.
Hold the wood in the vice by the side you will not use for initial cuts. If you are holding it on the part you will use, wrap the block in cardboard to avoid the vice pressing into the wood. softwoods like pine or maple will have marks if you press them in the vice.
Using a hacksaw or reciprocating saw, cut the block near your lines. The cuts should be near the lines, but don't have to be perfect (as you can see on mine), as you will be doing a decent amount of sanding to this before we're done.
Step 4: Step 4: Drill Initial Holes
To make things go faster, secure your block in the vice using cardboard and drill in holes the same depth as the amount of type you are going to set into it. Remember, you are planning to leave some sticking out!
Step 5: Step 5: Cut Out the Inset
Using a rotary tool with cutting bit attachments, cut out the holes you've put into the block until you have cleared the space for the type. If using a softwood, go slow, as the bit can easier take out large pieces of wood. Use the type to determine it will fit inside and be approximately level. You can clean this out with a pocket knife of small chisel.
Note: Mine ended up being slightly off-center. I blame the cold February winds making me shiver.
Step 6: Step 6: Put in the Handle Groove
Measure a distance below the top of the block where you would like to have a handle groove and draw a line around the block.
Using a sanding drum bit on your rotary tool, center the drum on the line and draw it toward you slowly. This will allow you to see the line and have more control. Start with a shallow groove and apply more pressure with each pass. I continued until the drum was approximately 1/3 of the way into the wood.
Step 7: Step 7: Finish Major Sanding on the Block
Sand down the corners and rough faces of the block, going along the grain of the wood. You should be using the rotary tool for the more dramatic shaping, but not finishing. Try to make sure your lines are level and the faces don't have any peaks or valleys.
Step 8: Step 8: Do the Finishing Sanding
Using a 220 grit sandpaper or finer, rub down the entire block. Make certain to get all surfaces except the interior of the hole on the bottom. This is the time when you can decide how sharp or soft you would like your corners and edges to be. I would suggest making them softer and more flowing.
Step 9: Step 9: Prepare the Type
Take the type and 2 O-rings (found in the plumbing section of a hardware store). Wrap the O-rings around the very top of the type and make certain they are together and level. If you have type of different sizes or fonts, this step may be more difficult. The important thing is that the faces of the type are all level and will press on the paper at the same time when stamped. The O-rings will also seal around the wood and cover up any mistakes you made when cutting.
Step 10: Step 10: Epoxy the Type Into Place
Make certain the hole is clear of all dust, chips, etc. Make certain you have a clear, flat space to do this step and that there is some ventilation, as epoxy can be harmful/smelly. Ensure one last time that the type is level before you start.
Mix approximately half the tube of epoxy per the instructions (more if the area is larger than the type shown). I love Gorilla Glue products, especially since the plastic is a mixing tray and it comes with a mixing stick.
Use the mixing stick to spread the epoxy on the sides and bottom of the hole. You want to have the bottom have a thick layer of epoxy that the type can essentially float in slightly.
Slowly lower the type into the epoxy while making sure you do not move it in the O-rings. If your O-rings are secure, this should be easy.
If you see any large gaps or need more epoxy, you have a small window of time to pull the type out and add more.
Make certain the face of the type is approximately level with the surface of the block. Do not clamp it, as that will move the type.
Step 11: Step 11: Treat the Stamp With Oil (or Stain)
Here's where personal preference comes in. I like using oil (specifically Danish oil) on wood, as it brings out natural colors, but you may want to stain the stamp. Here's the steps for oiling it.
Make sure you have a clear space and have laid out some plastic, as this gets a bit messy.
Once the epoxy has set, use a cloth or paper towel to lightly apply oil to the entire block. You will see the wood get darker, as it would be if wet.
After a few minutes of letting this set, use a foam brush, cloth, or stack of paper towels to generously apply oil to all surfaces of the block. you should see a layer of oil on the block.
Leave this to set for a few hours and reapply.
After another few hours, wipe off the remaining oil and clean the metal type with a paper towel that has been dipped in soap and water.
Step 12: Step 12: Test Out the Stamp
You should now have a nicely stained stamp that has cool, custom letters. Double check for any touch ups with oil and make sure the metal is clean.
You can then get some stamp pads (I got all of these for under $10 on Amazon) and test out the stamp.
The important thing to remember is that the metal will not hold ink like rubber stamps you are used to. These were originally meant to have a heavy layer of ink on them and paper pressed against it. Therefore, make sure you dab the stamp against the pad a few times and get a coat of ink. I would suggest holding the paper and pressing it hard onto the stamp or making sure you hold the stamp and rock it slightly to get all the ink into the paper.
Now stamp everything!
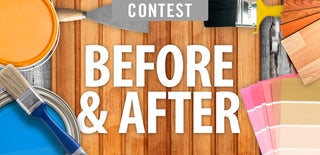
Participated in the
Before and After Contest 2016