Introduction: Make an Electric Motor
Introduction
This electric motor is made in reference and inspired by Roobert33's "How to make an electric motor homemade" YouTube video.
This was made for a physics coursework. Although the video has already briefly explained how it works and made, here's my take. Or rather an improved version.
Suggestions
Revising on how a DC motor works and Flemming's left hand rule for motors may help.
If the embed video of this motor doesn't work, click here
Happy Building- CCX
Step 1: Materials
Materials used:
● MDF
● Board pins
● 30SWG enameled wire
● Wooden dowel
● 2 ball bearing
● Some plywood
● 2 Banana socket (black and red)
● 1 speaker magnet
● Screws
● 2 L bracket
Step 2: The Rotor's Frame
This is the main section of the motor.
Cut out two circles of MDF with a diameter of 100mm x 3mm. with a central hole of 10mm.
The MDF can be substituted by some other material like acrylic
Attach 8 board pins evenly around the circle for the coiling after on, make two of these totaling of 16 board pins.
Combine two of the circles with a wooden dowel of 200mm x 10mm with a maximum distance between both of 120mm
Painting it or not is just for aesthetic purposes.
Step 3: Coiling
Probably the best part of the entire project, coiling.
The coils are shaped rectangular, lapped on the board pins.
It consist of 4 coils of 30SWG enamelled wire coiled with 160 laps on 4 board pins.
I suggest on either taping it or zip tying it so that the fragile wires will not tangle or come loose and also hot glueing the coils to the board pins and circle.
Step 4: Making the Commutator
The commutator is the segment where the electrical current contacts and flow through.
The commutator is made out of 8 plates of copper 15-20mm x 0.4 mm. bent in a curve with a quarter circumference of the wooden dowel. The plates of copper are to be glued over the wooden dowel with the hot glue.
Make sure that the copper plates DO NOT TOUCH EACH OTHER.
The ends of the wires from the coils are soldered on the sides of the plates of copper as seen on the picture attached, adding flux would make the soldering easier.
I just realised I did not take pictures of this segment, sorry for the lack of images. Here's a drawing on how it's wired to supplement that.
Step 5: Completing the Rotor
Add ball bearings of 26 x 8 x 10 mm on both ends of the dowel.
As seen on the second picture, the ball bearing has some EVA foam sticked around the ball bearing to reduce vibrations and noise.
Once your rotor is done time to make the motor frame.
Step 6: The Motor Frame
A plywood base with two stands on both end supported with screws and an L bracket.
A speaker magnet is then glued on the centre of the base.
To give it a much nicer look and allow it to stay on surfaces, I attached an EVA foam cut out sticked on the base with some double sided tape
Step 7: The Holder of the Rotor
Two plywood of a "V" shape is cutted out to support the rotors ball bearing.
A spring is added on both side to stabilise the rotor from leaning to one side and shaking violently.
A small dowel is also added on the top on both side using screws to secure the rotor in place as seen in the fourth picture.
Step 8: Commutator Contact Points
A custom made metal plate touches the copper plates (commutator) on both ends with a Pencil lead as a contact point, as it is much smoother for the coil to rotate or rather conduct. Less noise too! The metal plates on both sides are different varying from the way you wired it.
Two banana sockets are attached to the motor frame and contacts the metal plate via the screw.
Step 9: Put Everything Together
Put the rotor in ensuring the contact points touches the commutator and secure it with the dowels mentioned in step 7
Step 10: Complete!
Here's a video of it in action!
If the video doesn't work, click here
Credits to HHM, HZQ, TWZ and Dylan for working on this mid-term coursework.
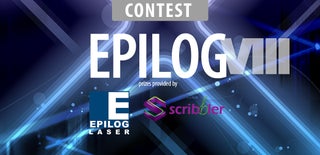
Participated in the
Epilog Contest 8