Introduction: Making Dimensional Recycled HDPE Stock for Projects Part 2
This will be a continuation of my instructable Making Dimensional Recycled HDPE Stock for Projects.
https://www.instructables.com/id/Making-Dimensional...
The photos are of a Christmas present I made this year. It is made of walnut and maple (no HDPE) After making the material for the cider press restoration (tray, buckets, and press plates) I only worked with what I call flowing HDPE. I have collected a supply of non-flowing HDPE and needed to find a method of utilizing the collected material.
I had a basketball hoop base made of HDPE (non-flowing), material was approximately 1/8" thick. I wanted to make 1/2" material, so I cut four pieces to fit inside the 9x13 pan leaving room for the 1/2" aluminum spacers. The material was heated for 90 minutes at 375 degrees. Then it was pressed between two boards until cool.
Cutting the finished piece several inclusions were found (air pockets). The piece was cut into strips looking for the voids. There were some areas where the material did not adhere, this was either dirt or lack of heat. On inspection I feel the problem was lack of heat. The HDPE is a good insulator and with small air pockets between layers of the material it just did not get to the melting temperature in 90 minutes.
The strips were placed back in the pan, reheated, and press as before, the results were disappointing. The strips did not adhere to each other. The pressing pressure did not transfer laterally (sideways) so the pieces did not weld together. The encouraging result was the consistency of the thickness, it ran 0.480"
Step 1: Next Process to Make HDPE Flat Stock
In step one several sheets of HDPE were melted at once, with the result of several air pockets and lack of adhesion. To keep material from having air pockets it was decided to melt each sheet individually and press flat. Then the flat sheets would be melted together to give a thicker piece of flat stock.
The individual pieces were heated at 375 degrees for 30 minutes, then pressed as before till cool.
Six flattened pieces were stacked on a jelly roll pan (12x17x1), 3/4" spacers were placed around the perimeter of the pan. The material was heated at 375 degrees for 3 hours. The part was then pressed until cool. The results gave a very consistent part. The measurement was 0.670" (will try 1" spacer next time) There were minimum inclusions and no visible areas of poor adhesion.
Step 2: Return to the Milk Jug HDPE
Two milk jugs were cut into quarters and the handle was cut apart. These pieces were melted and pressed as above, 375 degrees for 30 minutes, pressed and cooled.
These single sheets were layered with the milk jug material from first instructable, the part one pieces had been cut into strips for inspection. When layered there were some voids. To fill the voids two sheets of flowing HDPE were add to the stack. One on the bottom and one on the top.
The stack was heated to 375 degrees for 3 hours. milk jug HDPE is unique in that it turns clear when melted. (this will be used to gauge melt times and temperatures in the future)
The sheet was then pressed and allowed to cool. The part was consistent and no major defects.
Step 3: First Item Made From the Non-Flowing HDPE
A friend has a cistern that collects water from his roof gutters. A sand filter keeps the bulk of the dirt and debris out of the cistern. This is an older system and the piping is clay tiles. A clay grate keeps the sand in the filter, all the grates were broken and had missing pieces. Three new grates were made from the HDPE using woodworking tools. (bandsaw and drill press, forstner bit) These parts should last longer than the original clay grates.
Step 4: Making a Cylinder of HDPE
The pieces from the above step were cut in strips again and this time the goal was to make a cylinder of HDPE to be made into wheels and knobs.
It was thought that the pressing and solid sides of the form would give a consistent cylinder. It did not.
The material was heated at 375 degrees for 3 hours. It was then pressed until material was leaking past the wood pusher. The material flowed about 1 1/2" on the end but the rest of the material did not move.
Back to the drawing board.
Step 5: Second Attempt to Make a Cylinder From Non-flowing HDPE
Since the first attempt to make a cylinder of HDPE did not produce a satisfactory part another attempt was made. The first part did not fill out the form, so this time flat disks were cut from two different source, the basketball goal and a drum that had contained vegetable oil. A hole saw cut the disks and they were alternated in the form so it would be easier to judge if there was good adhesion. The disks were heated for 2 hours at 375 degrees, the disks were compressed (tamped with the homemade tool, plug of wood on a threaded rod) The was done at 45 minute intervals.
The blue material (drum) had a very different behavior from the black (basketball goal) the blue would expand when compressed and then at the next compression it had contracted into an oval shape small than the original disk. The black material would expand when compressed and would stay that way.
The first part was cut in half and it showed the black had encapsulated the blue, adhesion was questionable.
A second test of just blue disks was conducted and the disks did not adhere to each other and they did not fill out the form (a "tin" can).
Step 6: Side Note: Test of Blue Drum Material
Since the blue drum material did not adhere and shrunk at a different rate then the other material a test was conducted on the blue material alone.
A piece was heated at 375 degrees for 30 minutes. It shrunk the piece that is wider was cutoff the piece in the pan since it was too long to fit in the pan. The shrinkage is on the order of 40%. The material also got thicker almost double original thickness.
The part was then folded in two and clamped in a vise till cool. The part was then cut and two and it was noted that there no adhesion between the two side.
Currently this material will be only used in a single layer and all material will be shrunk before cutting to stabilize the material.
Additional test:
The material was sanded to see if it was clean. A film of a clear material was found. This film was scraped off using a card scraper. Note in the photo the rib is lighter colored and has a matt finish. When scraping it was observed that the film formed white chip and when it was removed the chips were blue. Both sides of the piece were scraped to blue chips. The piece was cut in two along the ribbed area. Then the pieces were place on top of each other and heated at 350 degrees for 30 minutes and then press between 2 boards with a c-clamp and allowed to cool. The finished part was squared up and the cuts revealed good adhesion and the part had a consistent thickness. Note the light colored places on the surface, this is some of the film that did not get scraped off.
A test was conducted using the blue and black HDPE. The pieces were heated at 375 degrees for 60 minutes and then pressed between 2 boards using 5 clamps. The results were a piece with good adhesion and very consistent size.
Conclusion:
Back to basics, make sure the material is clean, you may have to use physical means (sanding, scraping, planing, wire brush) and rewash in soap and water to assure cleanliness. Use enough heat to get the faces to welding temperature. This is currently trial and error when the material looks shiny wet and sagging it is probably hot enough.
Step 7: Making a 3 Inch Diameter Cylinder 2 Inches Long
19 disks were cut with a hole saw, 6 were placed in a "tin" can and heated for an hour at 375 degrees. The melted disked were pressed (tamped) until no movement was felt. 6 more disks were added and heated for another hour at 375 degrees. Then pressed and the last 7 disks were added and heated for another hour at 375 degrees. The HDPE was again pressed and left to cool in the oven, the oven was turned off. When cool the can had to be peeled from the compressed HDPE.
The part was turned on the lathe to get a concentric part and a center hole was drilled for clearance and bearing holes were drilled. There were inclusion (voids) in the outside 3/16" of the circumference and the ribs in the "tin" can mold added to the irregularities. No inclusions were found while drilling. The wheel was turned to a 2" diameter and the bearings were pressed into the wheel.
This process produce a very nice wheel for the 2x72 belt grinder project. Additional wheels will be made another 2", and 2- 5" diameter. One of the 5" wheels will not have a bearing, it will mount to the drive pulley on a keyed shaft.
Step 8: Final Thoughts
The photos are of the various items I have made from the recycled HDPE. I have several other items that I plan to make. Currently have 5 out of 8 pieces produce to make a beehive brood box. Need to make the additional wheels for the 2x72 belt grinder. Plan got keep stock around for making fixtures and knobs for the fixtures. Want to make some bird housed and feeders that will not rot in 2 or 3 years.
The major key to success is cleanliness and enough heat. When a new source of material is found, test some pieces to see if it behaves as other material or have you discovered a different type of material and have to find new perimeters for processing.
Also plan to see how #5 polypropylene works, have a pile of pails and lids. Have made one 9x13x1/2 piece, it looks like the HDPE but when sawing and drilling it seems more brittle causing some chip out. Other than that it works very much like the HDPE.
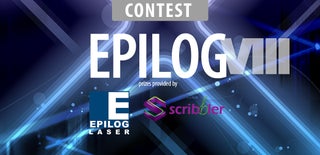
Participated in the
Epilog Contest 8