Introduction: Making a Plywood Kayak
The Jupiter Point series of kayak designs are intended as easy-to-build, fun-to-paddle, versatile collection of kayaks. With a simple 3-panel hull and unique 3-panel deck, the boats are quick to assemble, have a lot of character and perform very well. Plans are currently available for Ganymede a 13' recreational kayak that uses 3 sheets of plywood. You can download free plans from my website: http://bit.ly/xde8Bz. I've also drawn it up as a 7' childs boat I call "Io" that can be made out of a single sheet of plywood. The free plans for this are also available. Chesapeake Light Craft makes high quality boat kits they offer a complete kit for Ganymede if you don't want to scrounge materials on your own. I have blog post on Makezine.com that discusses the Io design specifically.
The construction is done with a technique called “stitch-and-glue” and is built from thin plywood. The stitch-and-glue (S&G) method use plywood panels cut to shape that are temporarily wired together with copper wire. This wire is the “stitches”. With the panels held in their intended shape with the wire the plywood is permanently glued together. The wires are removed and the whole thing is covered in a layer of fiberglass cloth and the cloth is saturated with epoxy resin to make it strong and waterproof.
The preferred material for this construction is 4 mm thick okoume marine plywood, covered with a 6-ounce per square yard fiberglass cloth coated with an epoxy resin. This will provide the strongest, longest lasting construction, but if you are strapped for cash, you can substitute lauan “door-skin” for the okoume and polyester resin for the epoxy. Lauan is apt to have gaps in the interior veneers that make the plywood. These gaps can weaken the material and may accumulate condensation leading to rot, but with a little care in building and storage when you are done lauan can make a nice boat. The description of techniques in these instructions assume epoxy resin, you may need to adjust your technique if you opt to use polyester.
Step 1: Prepare the Plywood Sheets
Plywood usually comes in 8 foot long sheets. Most of the Jupiter Point designs use panels that are longer than 8 feet. As a result, you will often need to make longer pieces of plywood. The standard way of doing this is by creating a “scarf” joint. All this means is the ends of two pieces of wood are shaped to a sharp knife-like angle, and two matching angles are over lapped and glued together. The glue used is the same epoxy you use to coat the fiberglass cloth with a little bit of powder used to thicken it up. Colloidal silica or cellulose are typical powders used, but bread flour works also.
First you need to form the scarf shape. Your plans will provide guidance on how to cut the plywood, you can just go ahead and scarf 2 full sheets, but these can be hard to handle. You may want to cut the plywood down into smaller sizes so it is easier to move around.
Stack the plywood with the edges you want to scarf aligned on one side. Plywood often has one “better” side. Flip over one of the pieces so on one the better side is up and on the other the better side is down. This way you can the better side up on both pieces when you glue up the scarf. It will help get the scarfs even if you have a piece of scrap plywood the same thickness on top and bottom. Stagger the edges back 1 inch each to make a shallow stair case. Clamp this down the edge of your workbench so the bottom layer hangs of the edge by a small amount.
One of the best tools for cutting the scarf is a sharp block plane, but you could do this with about as easily with a belt sander. If your plane has not been sharpened in the past 24 hours is probably needs to be touched up. If you have never sharpened it, you definitely need to give it a through sharpening.
Use the slope of the stair steps as a guide as you plane down the stairs. Cut into each step evenly, trying to keep the amount of material you have sliced off each layer even and consistent. The goal is to make a smooth, flat, wedge all the way from the top to the bottom. If you that the planed area on on one layer is getting wider than the other layers, adjust your planing to make them even again. As you plane deeper into the plywood you will start to see dark stripes and then the wood may change color a bit. The dark lines are the layers of glue between the plies of the plywood. Use these glue lines as guides to help assure a straight flat surface. Work to keep the glue lines straight and parallel. If you see part of the line curving up higher than on either side, plane down the sides to bring the rest of the line up even and straight.
You are done cutting the scarf when the side of the plywood has sharp edge and there is no step down from one layer of plywood to the next. Give the surface a quick sanding with 80 grit sandpaper to promote a good glue bond. Take one sheet of the plywood and flip around to the sharp edge is facing the other way and the bevel is facing down. Put a strip of wax paper under the joint. Mix up some epoxy and then add your powder to make a mayonnaise consistency glue. Spread this on the planed surface. Line up the joint so the two wedges overlap 1” such that the thickness is consistent throughout. Place a layer of wax paper on top of the joint and pile some weights to clamp the scarf tightly.
When the epoxy has cured, peel off the wax paper and scrape and sand off any rough spots. Don’t sand into the wood around the joint.
Drawing the Panels
If you down load the free plans you will need to graph out the dimensions at full size. These dimensions are sometimes called "offsets" This will take a large sheet of paper such as Rosin Paper you can get at hardware store or home center. Mark out the dimensions for each panel on the paper with little "x"s. Push some "T"-pins into the x and bend a narrow, flexible wood strips or fairly stiff wire around the pins to create a long smooth curve. Mark along this spline to draw the edge shape. You can fold the paper in half to cut out the symmetrical parts.
Layout the Panels
Cut out your paper patterns from the plans. Lay the patterns on the plywood as suggested by the plans. If you find a more efficient layout of the patterns, feel free to use it, but on the long panels you want the grain of the plywood running down the length of the long axis as much as possible. With the parts that require you cut two, such as the hull sides and front deck, lightly mark out the location with a pencil of both sides before doing any cutting. You want to make sure you arranged the parts correctly to get both pieces. Plywood generally has one better side, flip the pattern over when you layout the other side so you will have the better plywood side showing on both sides of the boat.
Once you have determined exactly where each part will come from, tape down the patterns so they don’t move. Make sure the paper is smooth and flat, without wrinkles or bumps or lifted areas.
Use an awl or sharpened nail to punch holes through the paper along the edges of each part into the plywood. Make the marks deep enough so you will be able to see them later. Make the marks as close together as necessary to assure you will be able to reproduce the curve accurately. This may be every 3 or 4 inches in straight areas, or ever 1/2 to 1 inch in places with tight curves. The patterns have little “+” marks with circles that indicate wire stitch holes. Use a 1/16” drill to drill out all these holes right at the crossing point of the lines.
Use a pencil and flexible strip of wood to connect the awl marks. Make a dark line that will be easy to see when it comes time to do the actual cutting.
Before you do the final cutting loosely cut out the parts where you will be making to matching pieces. Use a power jig saw to do the cutting. Install a new, fine tooth, smooth cutting blade in the tool. Cut outside the line but pretty close. Be aware of where you will be cutting the other side so you don’t cut into the area you will need for that other side. If you roughly cut out the marked piece first you can use it as a pattern to trace for the other side. With the two pieces cut out lay the marked on on top with the marking showing. Drill through the stitch holes of the first side into the other side. Push a small finish nail or brad through the holes as you drill them to keep the panels from shifting. Now, use your jig saw to cut out the final shape. Cut just on the outside of the leaving half the line. If you are uncomfortable cutting that close, leave more of the line and then come back with a block plane or sanding block to even out the edge and remove half the line.
Cut all the pieces in a similar manner. Work slowly and carefully. While the Jupiter Point boats are more tolerant of a little inaccuracy than other S&G designs, good, accurate cuts will make assembly easier and assure the finished boat is the desired shape.
Drill Holes
Starting at the bow end of each edge, drill 1/16" diameter holes about 1/2" from the edge every 6 inches along the edge. You will need holes along each side of the bottom, the bottom edge of the sides, the center edge of the front deck panels. On the front and back edge of the side panels drill holes every 3 inches. Do the same on the front deck panels on the short sides near the cockpit. Drill matching holes on the two forward sides near the cockpit on the back deck. With the sides and front deck pieces you can stack the two pieces together while you drill to save time.
You don't need holes on the top edge of the sides, or the outer edges of the deck.
Step 2: Wire or "Stitch" Together the Plywood Panels
Wire the ends to the side panels together. Cut pieces of wire about 3” long. Insert them through the holes, all the way through both sides. Bend the wires over and hold the ends at right angles to each other and pull them tight before wrapping them around each other. Make a tight twist in the wires with your fingers.
Clamp the two hull forms to some saw horses. Look at your plans to determine which end of the bottom panel is the front and which form is the front. Adjust the distance between the sawhorse so that the bottom panel drops down loosely into the forms.
Lift the side panels that have been wired together at the ends on to the forms. Separate the middle so that the bottom fits inside the two sides.
With the bottom fitted inside the sides run wires out through the holes. If the holes don’t line up you may have the bottom in backwards - try turning it around.
Cut the copper wires into 3” lengths. Bend them into a loose “U” shape and push each leg out through the stitch holes.
On the outside of the boat, pull the wires so both exposed ends are about the same length. Hold the wires so the cross at about a 90° angle. Use a pair of pliers to pull the wires tight, then give the wires a twist to hold the panels tightly together.
Wire up the deck pieces. Start by taking the two symmetrical bow panels and wire them together. Start by stacking the two panels on top of each other with the better faces on the outside. Push wires through the stitch holes along the shorter of the two long sides. Twist the wires securely together leaving a small gap between the twist and the plywood.
When the all the stitch holes along the edge have been wired up, open the panels like a book.
Locate the double stitch holes along the longer long edge. This is where the deck form will go. Wire one side of the deck into one side of the form. Open the deck up so it fits into the deck form. The wire stitch will make the “book” quite stiff to open, but just force it open slowly and evenly. Wire the other side into the form and twist the wires so the deck fits the form tightly. Again you want the wires going from the inside out.
Next stitch in the back part of the deck to fit between the open “V” of the two front deck pieces.
When the wires are stitched up tight, glue up the seams with CA glue. Before gluing, check the alignment of the center seam of the fore-deck to be sure the seam is even. Use your hand to reach under the deck to feel what will become the top of the seam. The joint should feel smooth and even. If one side feels higher than the other push on the seam with your fingers to get it into alignment.
Step 3: Gluing Together the Plywood
The hull is tack-welded together with CA glue. Check the alignment of the bottom, it should be even with the bottom of the sides. Make adjustments accordingly. If the bottom does not stay in place, tighten up the wires a bit.
Run a short (1/4”) bead of CA glue into the chine ever 3” along the seam. Don’t over due this, just a little bit of glue every few inches.
After applying glue to about a foot or so of seam, mist the glue with accelerator. Move down both side until the whole chine is tacked together.
Put a few drops going up the stems at both ends of the boat. Spray to set the glue.
When both seams are glued and set and the stems are secured together, remove all the wires.
Clip the wire on the inside with a pair of diagonal wire cutters. Pull the wires out from the outside. Leave the wires at the top of the sides which hold the sides to the forms. These will get glassed over and removed later. Make sure they are tight to the inside of the hull.
Step 4: Fillet the Plywood
The deck and hull are now ready for a fillet of thickened epoxy. Check the hull for twist by laying a couple straight sticks across the gunwales. Place one stick near the front form and the other near the back. Get your eye near the bow and look at the two sticks. If they look parallel, every thing should be fine. If one end of one stick looks higher than the other end, adjust the saw horses to make the sticks parallel.
The “fillet” is made with epoxy thickened with wood flour. Actually bread flour would work fine if that is what you have. Mix up about 1 cup of epoxy and then add small amounts of the flour until it reaches the thickness of peanut butter when it is mixed up. This “dookie schmutz” is the filleting material.
If the dookie schmutz is too thin it will not stay in the seam, if it is too thick it will be hard to apply.
Put the schmutz in a zip-lock freezer bag. Cut one bottom corner off the bag to make a 1/4” in hole. This makes a simple cake decorator.
Squeeze a line of schmutz into the chine seam. You want an even 1/4” to 5/8” diameter worm of gunk dispensed directly into the corner between the deck and hull.
Because the big bag of schmutz being held in your hand can warm up and start to cure, it is a good idea to get the whole bag of filleting material at once, then go on to the smoothing step.
With a good bead of schmutz dispensed along the seam, it is now time to smooth it out. I use a plastic picnic spoon as a high-tech smoothing tool. Press the spoon firmly into the schmutz and pull it along the seam. Place one finger into the bowl of the spoon to apply pressure and control. Use a smooth, even pull to get a smooth even fillet. Avoid poking at the schmutz with the spoon in an effort clean things up, instead use long smooth strokes instead.
If you need to add more schmutz into the seam, mix up more and place it in the bag and dispense it where it is needed. Use a new bag if needed.
If you apply enough schmutz into the seam you should get extra squeezed out to the side. You will need to clean this up. Use a plastic squeegee to scrape up the excess. Hold the squeegee at a low angle and pull it parallel to the seam so you don’t wreck the actual fillet in the seam.
If you used enough pressure on the spoon there should be a nice clean line between the fillet and the squeeze-out. Use this clear space as a guide as you scrape up the squeeze-out.
Collect the excess schmutz in your epoxy mixing cup. It can be re-used. If you need to mix up more epoxy and dookie schmutz you can mix this excess in with the new batch.
I know you will want to grab a hold of a blob of schmutz with your fingers and push it into a spot where you need a little extra. Avoid this urge. You will only make a mess. Stick to the program of dispensing with the bag, smoothing with the spoon and removing the excess with the squeegee. Your results will be neater. You will have a chance to use your fingers soon enough.
When you have done the long seams of the hull and deck, you can now make a mess of your gloves by making the fillet in the stems of the hull. You want a lot of material in the bow and stern of the boat because this is where you will hit stuff.
Apply the fillets to both sides then work on the stems at each end. The stems can take some abuse if you should run into anything and a good fillet will reinforce them. You should make a fillet that appears to be about 1/2” to 3/4” wide.
Start by squeezing a large, thick, heavy worm of dookie schmutz into the joint area. You probably will not be able to get your hands and the zip-lock bag right in where you want the schmutz so use gravity to drop the material into the stem area.
Use your gloved finger to press the material firmly into the joint, forcing it in to fill up the corner area. Start at the bottom and pull your finger, evenly and smoothly up the stem. Wrinkles in your glove will tend to cause groves and roughness in the fillet so it helps to pull the glove tight up around your finger. Like the other fillets, don’t poke and prod at the material as it will only make more of a mess.
Use your squeegee to scrape out any excess.
Repeat the filleting process on the deck. Because of the shallow angle of the seam you can clean up the excess by pressing the middle of your squeegee down into the seam so edges on each side scrape up the squeeze out. The fillet will be quite small, but it does not need a huge amount of material in the seam to be strong.
Step 5: Fiberglassing the Inside
Don’t wait for the fillet to dry before moving on to the fiberglassing. It is easier to lay the glass in while the dookie schmutz is still soft. If you don’t you may need to come back and sand the fillet smooth.
Lay the fabric down into the hull, smoothing it out across the bottom and up the sides. Do not press the cloth into the fillet as it will only make it stick and be harder to move around.
Trim the excess cloth about 2 inches above the side of the hull. Don’t worry about getting the cloth perfectly into the stem area, just leave yourself enough excess cloth to cover everything later.
Mix up approximately 1 cup of resin and pour it directly into the bottom of the boat.
Note about epoxy safety: Epoxy is a concoction of petrochemicals. While it does not smell much, it does produce some vapors. These vapors are generally considered safe, but epoxy can produce an allergic reaction in some people. If it were my lungs, I would be careful with the stuff. Personally, I wear a good quality respirator with filters suitable for organic compounds.
You also don’t want to get the resin on your skin. Wear gloves whenever working with epoxy. Long sleeve shirts and long pants will also protect you from splashes.
If you should get epoxy on your skin, wipe it off with a dry towel and then wash using soap and water. DO NOT use solvents such as acetone, lacquer thinner or white vinegar to clean your skin. These only make it easier for the compounds to enter your blood stream.
Use a plastic squeegee to spread the epoxy around. Move the epoxy from clear/shiny spots to white/dry spots. Pull epoxy up the side, but don’t press the squeegee into the soft fillet.
You want to keep the epoxy contiguous. Don’t put a puddle here and another there, instead try to advance in a solid front from the middle of the boat towards the ends. Don’t worry if there are gray/partially wet areas, but do not trap large areas of loose white cloth between areas of saturated clear cloth.
As you get to the point where squeegeeing no longer moves any resin, it is time to mix up more. Again pour a puddle in the bottom starting within an already wet-out area and spreading into the dry area. Continue pulling resin up both sides as you go. Switch sides frequently so you can see what needs to be done.
Once the epoxy is spread out a little you will have plenty of time to work on it, but if you leave a lot in your mixing pot or a big puddle it will start to stiffen up and make it harder to work with. It is better to move rapidly but deliberately than to get every spot perfect before moving on to the next. Instead get the cloth initially wet and smooth at this point, you can come back later to touch up dryish spots.
If you need more epoxy on the sides and do not have enough in the bottom, use a chip brush to dab a brush full of epoxy in the area, then use your squeegee to spread it out.
As you pull epoxy of the side you will see the fabric lift out of the chine area a bit. This is to be expected. Resist the urge to take your squeegee and ram the edge down into the cloth and the fillet. This will mess up the fillet and won’t eliminate the bridged cloth. We will come back later and fix it. Time wasted now worrying about it will only make it harder later.
Step 6: Fiberglassing Details
Get the epoxy distributed just about to the end. Then smooth out one side of the glass all the way to the stem, allowing a large wrinkle or fold to accumulate on the other side.
Use scissors to cut down along the stem fillet, snipping all the way to the bottom.
Pull back the loose side of the cloth and tuck the smooth side back into the fillet, removing any wrinkles that may have appeared from your cutting. Then tuck the loose side in to over lap the existing glass. If the overlap extends more than about 2 inches you can trim off the excess.
Spread epoxy onto the cloth using your brush as needed to apply epoxy into the over lapping cloth.
If you end up with a gap in the cloth for some reason, just cut a patch from any scraps you cut off earlier.
Now for those bridges of cloth at the chine. These appeared as you squeegeed epoxy up the sides. As you did this you pulled a little fabric up with the resin. As a result there is not enough fabric in the boat to fill into the fillet.
The solution to this is introduce a small amount of cloth back down into the seam by sliding it down from the top.
With a somewhat dry brush place just above the fillet and pointed down, lightly press the fabric down towards the fillet. It should slide fairly easily, but sometimes it gets caught up on the rough top edge of the plywood. You may need to lift the cloth at the top away from the edge a bit so it doesn’t snag.
Work gently from one end of the bridged fabric to the other, sliding the fiberglass down into the bubbled area. You may not need to add any more resin, but as you do this look for areas that are slightly gray or look starved for resin. If there is a shiny spot near by, use your squeegee to spread the excess resin in the shiny spot to the dull grey spot. If there is not source of resin already in the area, blot a brush full of resin on the spot then squeegee it around.
Inspect the hull for bridges and dry spots before going on to the deck. You have now competed the hardest fiberglassing work of the whole project. Everything else will be easier.
Step 7: Fiberglassing the Deck
Lay glass on the deck and trim it a few inches over size. Smooth out the cloth to eliminate any wrinkles.
Mix up epoxy and pour a small puddle onto the back deck. In case you need to be told, don’t pour it where the cockpit hole is, it will run through.
Spread the epoxy around with your squeegee. Again, don’t trap large islands of dry cloth in oceans of wetted out cloth, move in an even tsunami from here to the other end of the boat, working up both sides of the cockpit at the once.
Double check your work, looking for grey or poorly saturated glass. Dab on a little resin where needed and squeegee around.
When you are done doing the wet-out coats of the fiberglass you should end up with a matte finish with the texture of the fabric readily evident. There should not be shiny spots. If you need to remove any excess use your squeegee to scrape off the excess.
Use a grunge cup to remove excess resin from your squeegee after scraping the glass. Do not use too much pressure while scraping excess. If you are uncertain, just leave it be.
If you can get to it the same day, wait a couple hours after applying the resin. At this point the epoxy should be partially cured, but still soft. Now is the best time to give the cloth an extra coat of resin to seal any pin holes. Use a foam roller to apply a thin coat of mixed epoxy over the whole interior surface of the both the deck and the hull.
If you can’t do this coat right away, let the resin set up hard, then scuff of the surface with a green Scotch-Brite kitchen scrubber to help the epoxy adhere better. Then apply the thin coat.
After the second coat has cure, clip the copper wires holding the forms. If you leave the wires a little long you may be able to use pliers to pull the wires out. Don’t try too hard, if they don’t come easily, just leave clip them close and we’ll deal with them shortly.
Trim off the excess fiberglass with a utility knife. Hold the edge of the blade tight against the wood and hold the fiberglass. Slice the glass off in smooth even strokes. You should not need to saw at the glass, just hold the knife tight against the wood and slide it down the length of the boat.
You should be ready to flip the hull over on to the saw horses. Put the deck to one side for now.
Step 8: Preparing the Outside of the Hull
Fiberglass doesn’t like sharp corners and sharp corners are delicate and easily damaged. The best tool for rounding over the chines is a block plane, but you can do this with a sanding block. If you don’t think a plane is better than sanding, it is probably because your plane is dull. If you just bought it or have not sharpened it within the past week it is dull. Sharpen it and give it a try.
Set the blade so it just barely sticks out. If you have a plane with an adjustable throat, open it up all the way. If the plane is adjusted well and sharp, your first stroke along the chine should remove a tiny little shaving. It shouldn’t look like much but if you get a big shaving it means you have the plane set to deep. If you get little chips scraped off the edge, the plane is dull, sharpen and try again.
Start by planing a chamfer at a 45° angle, in other words the angle between the plane and the hull bottom is the same as the angle between the plane and the side.
Maintain this same angle until the top edge of the chamfer is cut all the way back to the edge of the hull bottom panel. Don’t cut into the bottom panel. Next angle the plane to knock the corners off each side of the chamfer. This will mean a couple swipes of the plane on the top edge of the chamfer, cutting into the bottom panel a bit, and then a couple swipes along the bottom edge.
If the plane continues to allude you, you can use coarse sandpaper to do the same thing. A good sharp plane is faster and easier, but sandpaper works also.
After making the 3-sided chamfer, use the plane to knock off the remaining corners. Use your hand to feel for sharp edges. Your fingers are very sensitive to and irregularities. Put your hand on the edge and pay attention to what you feel.
Round over the stems in a similar manner as the chines. Start by making the front edge flat and straight across about 1/2” to 5/8” wide. Then knock the corners off with a chamfer on either side. Then proceed to complete rounding over the stem.
Step 9: Fiberglassing the Outside of the Hull
Roll cloth over the hull and trim off the excess about 4” to 6” below the edge of the side. This excess will absorb some epoxy drips so they don’t make a mess of your floor.
Smooth out the glass on the bottom and let it hang down the sides. Apply resin in the same manner as you did the inside. Pour a puddle on the bottom and then spread it out with a squeegee. Again, work in a unified front down the length of the boat. Pull small amounts of resin over the side at a time. As you pull the squeegee over the chine, roll your hand over to maintain the same angle between the squeegee and the surface. If you need extra resin on the side, use a chip brush to apply dabs of epoxy where you need it and then squeegee it around. Don’t try to pour resin on to the side, it will just end up on the floor.
When you get to the end, wet out both sides all the way to the stem so you have a neat fold of cloth protruding from the end.
Notice the “starved” areas in the photo where the glass is not completely saturated near the chine and along the bottom edge. I want to get the stems taken care of while the resin is still liquid and easy to deal with. I’m moving quickly knowing I will be able to touch up these spots shortly.
Cut off the excess glass about 1 inch from the stem.
Snip off the corner starting at the “bottom” of the stem so the glass can be folded over either side without bunching up.
Peel back the cloth from one side then fold the opposite side over. Wet this out completely.
Lay the loose side down on top of the newly wetted glass.
Then fold the second side over and wet it out. There will probably be some loose fabric sticking up at the corner at the “bottom” of the stem. Wet it out as best you can but don’t obsess about it.
Go back and take care of any spots you missed on the rest of the hull and scrape off any excess into your grunge cup.
Step 10: Installing the Deck
Let the epoxy set up and then flip the hull and trim off the glass. The glass is easiest to trim while the epoxy is still a little green, but you don’t want it so soft that you will damage the glass with your saw horses.
Again, place the edge of the blade tight against the plywood and trim the glass off in a smooth fluid cut.
Use 80 grit sandpaper to clean up the sharp edges of glass. Sand the glass flush with the plywood. You do not want to change the shape of the wood, you just want to remove any messy drips and leave a clean, smooth edge. Clean up the edges of the deck while you are at it.
While your at it sand the inside 2 inches down from the edge on the side and the same on the deck. This is to rough up the surface so the interior tape will adhere better.
The deck fits on top of the hull sides. Start by aligning each end and loosely taping them down with fiber-reinforced packing tape. Then, starting near the cockpit, tape the deck tight down against the top edge of the hull sides.
Pull the tape tight as you stick it down. This will hold it in place better than loose. If you need to align the deck with the hull sides you can stick a putty knife in the gap and wiggle it around, then tape it snuggly down.
When the seem is held securely in place, go back with CA glue and spot weld every 3 to 4 inches. Check your alignment as you go, you can push the deck down tighter if you see any gaps. Spritz on accelerator to set the glue. You can then strip the tape off.
Run a strip of masking tape over the outside of the sheer seam. This will keep the epoxy from running out when we do the inside. To make any drip-through as smooth as possible you need the tape to be smooth without wrinkles. The best way to do this is to stick down the tape on just one side of the seam as you dispense it out, then come back and fold it over the seam later.
Step 11: Taping the Inside Seam
Brush on a stick! We will be running a strip of fiberglass tape down the inside seam. We need a tool to reach all the way to the end. Find a stick that will reach from the cockpit to both ends. Cut one end at a 45° angle, screw a chip brush to the end and cut the handle off the brush.
On the other end of the stick, taper the end down a bit then pound a small finish nail through it. Bend the nail over so it point back down the length of the stick. Then rotate the nail to point out to one side.
Tip the boat up on edge on your saw horses with the sheer line angled down. A stick clamped to the saw horses will keep boat securely in place. A little tape can hold the boat to the stick.
Measure out a length of pre-woven fiberglass tape from the knuckle in the sheer line next to the cockpit down to the bow of the boat. Lay a length of waxed paper on the floor or your workbench. Wet out the length of tape with epoxy. While you have the brush in your hand, pre-wet the lower seam inside the on-its-side boat. You can use your brush-on-a-stick to get epoxy on the seam all the way into the end.
Make sure the tape is well saturated and even a little sloppy wet. Roll it up loosely so you can carry it over to the boat.
Place the tape down on the inside of the lower seam; starting 6” behind the knuckle and roll the cloth out towards the bow. Center the tape on the seam with half on the hull; half on the deck. When you roll it down the seam as far as you can get; pull it back a bit so you can unroll it into a neat Z-Fold on top of seam.
Use the nail on the stick to pick up the loose end of the tape. Point the nail down, poke it through the tape, then rotate the nail so it point upward.
Push the stick down into the end of the boat, pulling the tape along with it. With one hand hold down the end of the tape as you pull the tape tight. Hold the tape above the seam and then slowly release the tension on the tape so the cockpit end starts to lay down into the seam. Move the stick to keep the tape centered on the seam as it goes down.
When the tape is all the way down, rotate the stick so the nail points down. If the tape does not just fall off, give the stick a quick, sharp push to release the tape.
Switch ends of the stick and use brush to nestle the tape down into the seam. Brush on a couple layers of epoxy. You want a good heavy coat of epoxy to help create a fillet.
If this technique does not end up with the tape covering the seam the first time, don’t spend a lot of effort using the stick to try to straighten out the tape, just pull the tape back and give it another try. Because we measured the tape from the knuckle to the stem and we started the tape 6 inches behind the knuckle, the tape will not reach all the way to the end. This is intentional. If the tape is too long you will not be able to get it off the stick. Fix this by pulling the tape farther back. We will deal with the last few inches later.
The tape should be approximately centered on the seam. At the very least you want it to have a little bit on both sides of the seam. When you have the bow done; do the exact same thing for the stern.; Let these set up solid so you won’t end up with the tape on your head when you flip the boat over and do the same thing to the other side.
Step 12: Fiberglassing the Top
When the interior tape is cured, peel the masking tape off the outside. Then round over the outside sheer line in the same manner you had rounded the chines.
Start with a chamfer, knock the corners off the chamfer then smooth out the round-over. Sand the edge to smooth it out and give the whole deck a light sanding with 120 grit. Sand the upper edge of the hull with 80 grit to help the epoxy adhere.
Run a strip of masking tape about 1 inch below the sheer line. Fold up the bottom edge slightly so any drips of epoxy won’t run down the side of the boat.
Roll out layer of fiberglass on the deck and trim it even with the bottom of the tape.
Start wetting out the deck around the cockpit as this is where it will be trickiest to get it to lie flat.
Brush a little epoxy on then spread it with a squeegee. Bring the epoxy down over the side and wet out on to the masking tape.
After doing the area around the cockpit continue wetting out the rest of the deck in the same manner you did the hull. Make sure the glass is wet out on to the masking tape. Brush some extra resin on to the center line of the front deck to help fill up the gap between the panels.
Step 13: Trim the Glass
Let the epoxy set up so it is starting to get rubbery. Put a brand new blade in your utility knife.
Lightly score the surface of the new glass just above the tape. Don’t press to hard or you will cut into the older glass. It does not take much force to clip the fibers in the still-soft resin. If you wait to long the epoxy will be harder and you will need to press a little harder, but again you don’t want to press too hard or you will get a permanent mark.
Lift the end of the tape and pull it off the boat, the new cloth below the score line will come up with the tape. Work all the way down the boat on both sides.
You can do the deck without this masking tape but you will end up with a lot of loose fiberglass threads that get all over the place and generally make a mess.
You now have something that looks a bit like a kayak. You can cut the excess glass out of the cockpit hole.
Step 14: Installing the Cockpit
Glue down the cockpit risers pieces. Mix up epoxy and mix in colloidal silica, cellulose powder or wood flour to make a loose paste-like glue. Brush this the riser piece and around the perimeter of the cockpit. Lay the riser in place. When you have all the pieces in place for one layer adjust the position so it is centered around the cockpit hole.
Apply glue on top of the first layer and on the bottom of the next layer and build up another lamination.
Two layers of riser laminations is the minimum. Three layers will make getting a spray-skirt on-and-off a little easier.
Coat the whole bottom of the coaming lip with a thick layer of thickened epoxy to seal it completely against water. Apply epoxy to the top lamination of the riser and then lay the lip on top.
Check the alignment of all the lamination. Make sure they are all centered around the hole. Check to see the butt-joints between the pieces in each layer are tight.
Add as many clamps around the coaming as you have access to. Keep checking that you don’t knock any of the laminations out of place. Align the tips of the clamps along the inner perimeter, over the riser laminations If you place the clamps too far out from the inner edge you will bend down the coaming lip.
Now, do your best to clean up any squeeze out. Run your gloved finger all the way around the outer edge of the riser laminations, under the lip. Use an acid brush to wipe off any excess glue onto the inside.
Step 15: Cleanup and Glass the Coaming
The more glue you wipe off when it is still wet, the less work you need to do after it has dried. Use a very coarse rasp or file to clean off the glue. The Shinto wood rasp shown does a good job.
When the glue has been cleaned off it is time to round over the edge. Again, start by making a chamfer about 3/8” wide. A half-round rasp works well here. After the chamfer, knock off the corners then round it over. Do the same to the top and bottom interior edge of the coaming. If you have a round-over bit and a router you can use it on the top edge, but you will still need to do the bottom edge by hand.
Clean up your work with 80 grit sandpaper then smooth it out with 100 and 120 grit.
A good radius top and bottom will make the next glassing step much easier. Sand the deck underneath the coaming to rough it up for glassing.
Cut out strips of fiberglass about 4 to 5” wide. Cut these on a diagonal at 45° to the weave, i.e. on the “bias”. This bias-cut cloth distorts very easily. This is why we use it, but it means you need to be careful handling it. Do not pull on it as if you start out with a 4” wide piece, a little tug can make it 1” wide and it won’t be wide enough to cover the whole coaming.
Start by painting some epoxy on to the coaming, then carefully lay the bias-cut cloth on to vertical edge of the coaming by just pressing it into the wet epoxy.
Next use your chip brush to dab down the cloth. Don’t stroke the cloth yet as it will distort. Just press the cloth down with the tip of the brush. Add epoxy as needed to saturate the cloth. Make sure to saturate the cloth under the deck as well. Let the top edge of the cloth over hang the edge of the coaming lip. Do not try to wrap it back under the lip.
If your strip of cloth does not reach all the way around cut another piece and over lap the first by about 1 inch.
After applying one layer of cloth all the way around the coaming, lay down another layer so you have two complete layers of cloth completely around the cockpit.
Step 16: Finish Work
While you have a wet brush, apply a fill coat over the whole deck. Apply masking tape on the side of the hull about 1 - 1/2” down from the sheer (1/2” below the trimmed edge of the deck glass. Then brush on an even coat of epoxy over the whole deck. If you are more comfortable making an even coat with a foam roller, feel free to do so. The goal is to build up enough resin to fill in the weave texture of the fiberglass fabric. Apply the resin over the side on to the masking tape.
Let the fill coat cure for about 1 hour before removing the masking tape.
After the deck has cured, trim off the excess cloth around the coaming and sand it smooth. Apply a fill coat to coaming then flip the boat over so you can work on the bottom. We want to do a fill coat on the bottom as well.
If you have some gaps in the glass near the stem, now is your chance to patch them and even if you don’t it is a good idea to add some extra glass in this area.
Sand away any roughness at the “bottom” of the stem.
Run a strip of masking tape about 1/2” above the sheer line.
Paint on a good fill coat over the whole hull. Then cut a two 3” x 12” strips of bias-cut fiberglass. Lay these over the stem onto the bottom of the boat to protect this high-wear area. Do the same to both ends.
After the resin has cured for an hour, peel off the tape.
When the epoxy has had a couple days to set up hard it is time to start sanding. We over lapped the fill coats along the sheer where the edge of the deck glass made a little bump. This extra resin will make it easier to mask this edge.
Use 60 grit to sand the whole boat. The goal is to make the surface of the boat smooth and level.
Sand all surfaces, but do not sand the angles at the chine and sheer yet. It is very easy to sand through these areas and we don’t want to mess up our fiberglass work.
Strive to obtain an even, matte finish over the whole boat. If you start sanding into the fiberglass, stop sanding. You will see when you get into the glass because little whitish spots in the pattern of the weave will start to appear. If you start seeing the glass and you still have shiny spots in the area, you can apply another fill coat to the whole boat so you have more material to level out the surface.
Once you get an even surface you can come back and carefully hand sand the sheer and chines.
When everything is sanded evenly with the 60 grit sandpaper, go over everything again with 80 then 100 grit. You are now ready to varnish or paint.
You want at least three coats of varnish or enough coats of paint that the paint is opaque. Use a marine-style varnish with UV protection or a exterior enamel paint. Marine boat paint is good, but a good deck enamel will work also.
Step 17: Outfitting
A seat is glued to the bottom of the boat with contact cement. The kit seat is first assembled by first gluing together the two pieces of 1” minicell. You can make your own seat by carving 3” minicell. The backrest is screwed into the coaming riser from underneath. Drill a small pilot hole up into the riser lamination about 1/4” back from the interior edge of the cockpit. Screw the webbing in on either side at approximately the widest part of the coaming. The backrest is held up with the shock cord at the back of the coaming. Use the plastic loop to hold the shockcord. Tie the shock cord to make a loop going through the nylon loops on the back of the backrest.
Go Paddling!
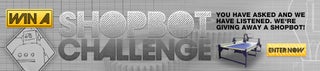
Runner Up in the
ShopBot Challenge