Introduction: Motorising Any Model
There are a lot of plastic kits you can buy but they are static when done. It does not have to be this way any more. Modern technology allows you to modify your toys in interesting ways. This is one example of how 3d printing and electronics can transform a humble plastic model into a seething monster.
Motorising a Model and adding 3d printed tracks
For our Model we selected a “Landraider” Tank made by “Gamesworkshop” for their “Warhammer 40k” range. This model is approximately 1/35 scale its length is 17cm, Width 10cm and Height 7cm but you can choose any model you want.
First of all inspect your chosen model for size, and see if it has any design features which are going to help or hinder you in the conversion process. After inspecting the model we decided to fit working tracks into this model and to control them remotely.
Motors
Motors will need to run by battery so 3 volts or 5 volts is a good choice.
The speed of rotation of the driving wheels needs to be calculated and matched to the output shaft of the motor.
The tolerances of 3d Printing
What you can and cant do with SLS 3d Printing and how to make a 3d print will be explained in the next part.
Step 1: Construction of Custom Tank Tracks Creation in 3d for 3d Printing
Track system
It is recommended that you 3d model your dimensions so that you have an accurate layout and make sure that pieces will fit where you expect them to. At the same time you are also making models that can be 3d printed which is an added bonus. Using this software we designed our driving sprockets and tank tracks also the bogey wheels and determined where the shafts would go.
Here is your check list for the Track system: -
Check to see if motors will fit and line up with axle of the driving wheels.
Check how the track is assembled and if you can use the same path ( Some Kits will come with good rubber tracks that can be used with the motor).
If the tracks don't fit in with your conversion program be prepared to create your own tracks or source some from other models.
Are the provided drive wheels able to be converted for use? Are the road wheels able to be converted for use? How are your axle's going to work; are you going to drill the centre of the provided wheels for axle use?
The Tolerances and price of SLS 3d Printing
Here are some pictures so you can gauge the scale and precision you can print with using an SLS printer ( Not that we have One!) we used a company in England called 3d Print UK and they came in at a reasonable cost of £78. Now compare that to 3rd party retailers and its not a bad cost on each piece, and seeing that you can print 500 track segments on this print ( thats enough for 10 tanks) . So £7.80 for a set of tracks is very good.
The Tolerances of 3d printing are in the region of +/- 0.1 of a mm.
Construction of Custom Tank Tracks
We decided that the best way to make realistic custom tracks would be to 3d print each individual tank tracks, as there was no way that we could convert the original tracks into usable pieces.
To model my tank tracks I used a program called “3d Studio Max” its a free piece of CAD software that allows for powerful 3d Design and Animation and can also produce .STL (which is the files format you need to send to the 3d printer) Files which is what we want for 3d printing.
AutoDesk 3d Studio Max :
http://www.autodesk.com/education/free-software
You can also use Sketchup:
http://www.sketchup.com
and install the STL Plugin for Sketchup : http://extensions.sketchup.com/en/content/sketchu...
This is a great little tool for checking your .STL file
http://www.netfabb.com/basic.php
Check here for more info on free to use CAD software:
http://www.3dprint-uk.co.uk/free-cad-programs/
Here are some videos I have created to show you how to make your own tracks
Creating Tracks (created by me)
Designing with Accuracy / Building things to size (created by me)
The photos above show how the pieces came together and the sprew that we made in 3d Studio max and received from the printer with all our pieces on it.
To connect our tracks together we used house hold pins which we cut to length. And 2mm steel shaft for the bogey wheels to rotate on.
Step 2: Custom Drive Wheels, Road Wheels and Axles
Axles
For axles we used 2mm diameter shafts, which can be savaged from video players, old printers and tape players to name but a few. Different diameter shafts are available online, but why pay when you can salvage. Use a drill to make 2mm sized holes for the shafts.
Please refer to “How to Install the Road Wheels and Tracks” / “Drilling your Holes” for drilling procedure.
Custom Drive Wheels and Road Wheels
The difference between the two.
1. Drive wheels are toothed cogs that mesh with the track, as the cog rotates the track caught in the cog moves. They are in direct contact with the motor.
2. Road wheels are toothless wheels that the track rests upon. They are to be placed along the circumference of the track to allow it to revolve.
Now its time to make our custom Drive wheels and Road wheels.
How to Install the Road Wheels and Tracks
It is vital to get good track tension and at the same time to insure the tracks have enough flexibility to rotate. If the tracks are to tight the motor will not turn them as the friction is to high between the wheels and the track. To get this right I used the existing path of the track and placed the track belt along it. I then marked where the wheels would go so that the wheels top edge would fractionally take the underside of the tracks. When it came to fitting the last road wheel, I treated it like a tensioner and moved it into place so the track was tight but not to tight. You can always remove or add in a track segment; if you feel like the track it to tight and is producing to much friction with the wheels then add a segment in or if it is to loose and the driving cog is not able to rotate the track then add a segment in to increase the tension across the track.
Step 3: Drilling Holes for Axle
Drilling your Holes
When you are happy with the position of a Road wheel, get a pen and mark a spot in the centre of the wheel and drill though. Now to get the corresponding hole on the other side of the tank side. To do this place a piece of foam board onto the side without the hole. This will be for marking the position of the hole to be drilled. Now line up the two sides; The one with the hole drilled on top of the side without the drilled hole. To get the the two holes to be square place a wheel on top of the outside hole. The edges of the internal hole of the Drive wheel will insure that the hole on the opposite side is parallel to the hole already drilled.
Do this same procedure for all the Drive wheels and Cog wheels you are going to install.
This worked pretty well for prototype one,but for the next version we aim to have 3d printed inserts, to eliminate drilling the body of the tank at all and so positioning it very easy.
The Original Kit & Changes made to Original Kit (LandRaider Specific)
We decided upon several changes to the original Kit. First we cut away many of the protruding struts that connected the two sides together, as they would clash with the road wheels. Then we cut and smoothed the track path, so the tracks would rotate smoothly. Here are the areas we decided to remove.
So don't be scared to get in there with the craft knife and make you mark.
Step 4: Installing the Motors
The motors that we chose were Tamiya item 70189 because the 3D model showed they would fit, they run on 3 volts and they come as a kit so you can choose a variety of different gear ratios and hence different speeds. All this information is detailed quite nicely on the box and in the instructions that come with it. Also, the output shaft is a hex shape so with a hex shaped hole designed into our driving cog there would be no chance of the gear wheel slipping on the shaft.
The motors were attached to to model simply by glueing the gearbox to the inner wall of the model using a decent strong glue. We used gorilla glue but make sure the motor is well clamped because this glue will expand as is dries and push the gearbox away. Also do be patient and let it dry thoroughly before moving on. With the motors attached to the model the driving cogs can be slipped on to the shafts. Because of the hex shape of the shaft and the hex shaped hole in the driving cogs (from the 3D print) we did not need to glue these on at all but if you have round shafts then some glue here as well would be a good idea to stop any slippage.
The model is now ready to be assembled and powered up but first a little aside
Why have a motor+gearbox.
Q: Why not just use a motor by itself?
A: Because small d.c. motors spin too fast to be directly connected to the back wheels of a model. You might think – great! It will go really really fast but the likelyhood is that it wont be able to get going at all. (not enough starting torque as they say).
By driving through a gearbox you drop the speed that the driving wheels turn at but what you gain is torque (turning force). That is why cars have gearboxes. So you can select a low gear to pull away from a standing start or drive up a hill. Cant really do without them.
There are lots of model motor/gearbox combos that you can choose from. Things to consider
1. How physically big is the motor/gearbox. It needs to fit. Get the dimensions of the one you are thinking of and model it in 3D together with your actual vehicle. Saves a lot of guesswork and its fun.
2. What is the diameter (or shape) of its output shaft. These vary so don’t assume that it will likely be 2mm or anything else. You need to know this so you can design your drive wheel to match
3. What is the r.p.m at the output. A faster rpm means a faster vehicle (but with less torque remember). You can calculate quite easily what your speed is going to be if you know this.
e.g.
lets say the output rpm is 90 rpm (revolutions per minute).
And lets say your driving wheel is 20mm diameter.
So, being 20mm diameter the wheel will have a circumference of pi * 20 which works out to be 62.8 mm.
So, the track or ground will be moving 62.8 mm per minute.
There are 60 minutes in an hour so it will move at 60 * 62.8 mm per hour
Which works out to be 3768 mm per hour.
There are 1000 mm in a meter so this means the speed will be 3.8 metres per hour.
What if I want a scale speed?
Ok,
Lets say the real vehicle can travel at 20Km per hour.
So 1/35 scale speed will be 20,000/35 which is 571.4 metres per hour
Which is 571.4 / 60 metres per minute. i.e. 9.52 metres per minute
Which is 9520 millimeters per minute.
A 1/35 scale tank has a driving wheel roughly 20mm diameter which as we calculated above is a circumference of 62.8 mm.
So, 9520/62.8 gives us 1999 revolutions per minute of the back wheel. So you would want a gearbox with an output of 2000 rpm to give a roughly scale speed.
4. What voltage is the motor
5. On larger ones the amount of current drawn by the motor might become an issue too but we are talking small so will not worry too much about that.
Step 5: Wiring and Testing the Motors
The simplest test of the motors and tracks once assembled is simply attach the two motor wires directly to a battery. Note that the battery voltage needs to match the motor voltage. If the battery is 9 Volts and the motor is only designed to run at 3 Volts then the motor will run very fast for a short period of time and then it will burn out. If the battery voltage is too low then the motor will run very slow or not at all. But there is a reasonable amount of tolerance in most motors. You will see in the video below that we used a 4.5V battery box to test this motor which officially should run at 3V.
By swapping the two wires from the motor over at the battery you can test the motor in reverse. The motor doesn't actually care which way it is turning.
If the motor hums but doesn't turn then check for the track sticking somewhere.
then you assemble the side
then check it runs without sticking.
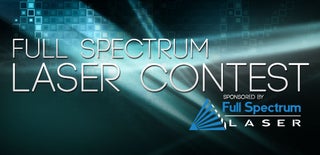
Participated in the
Full Spectrum Laser Contest