Introduction: My 123D Jansen Strandbeest Mechanism
So this is a Strandbeest mechanism, a mechanism invented by Theo Jansen, a Dutch artist. This kinetic sculpture moves when on a slope, or as in Theo Jansen's creations, harnessing the wind's energy. I designed this kinetic sculpture using the complex but very accurate ratios of the original design. I used Autodesk 123D, and later on tested and tweaked my creation in Autodesk Inventor's dynamic simulation program, but i created it using 123D. This contraption doesn't need any screw, bolt or anything, just to be printed out. I purposely did not include dimensions in my Intsructable, as not to constrain people's imaginations and ideas. As long as you follow the ratios and concepts from the following site, you should have a great, perfectly working, awesome Strandbeest.
Step 1: Leg
We'll start out with the leg. First like every part, we start with the sketch. The sketch is made to the original proportions of Jansen's original design, like all of the other parts. The image sketch is one of my first attempts, so it's slightly different from the final piece. Once you've finished with the sketch, you need to extrude the body, and give the two pivot points a little bit of height, above the main body, on both sides. After everything is to your liking, it would be better to fillet the edges on the main body parts, but not the pivot points.
Step 2: Structural Limbs
The mechanism has a couple of limbs, each one having a different length, but the procedure is very similar. First you want to make the two pivot points, from which limb will be attached to the rest of the mechanism. What you want to do is connect the two pivot points with an arc of whose radius is sufficient to hold the load and yet not disrupt the motion of the other parts. After making the sketch, as in the example below, you need to revolve the area between the arch and the line connecting the two pivot points (the axis line). After revolving the limb, you need to cut off, in both directions, the excess material that will impede with the two pivot points (as marked in drawing 3). After cutting, extrude the pivot points in both directions, again slightly higher than the main body. Once you've done that, you need to again cut a little depression in one of the sides of the pivot point, which later on will be used for the connectors. repeat the same procedure for each different limb.
Step 3: Upper Triangle
You can make the upper triangle the same way as the leg, except the time there are three pivot points. you also need to cut out a depression in the upper point.
Step 4: Disk
The disks are the ones who enable the motion of the legs, and each axis point as shown in the sketch), need to be to be at a 60 degree angle from each pair of disks. This is the reason the shaft connecting points are a six point 'star', with each groove at exactly 60 degrees from the next one.
As long as you follow the main concept while making your sketch, just extrude the part to a thick enough width to handle the load. On one side, make again the same depression for the connector, at the axis point.
Step 5: Shaft
The shaft is connected to each wheel through main body, to allow simultaneous motion, through the mechanism. While building the shaft, you need to make grooves on the top and bottom parts, as shown in the image, that will be mated with the disks at the connecting points, with the groove being the same width of the connectors, and the distance between them being the same as two disks plus the body between them.
Step 6:
The shaft closer is something that's supposed to close the edge of the disks. They basically just snap on. You need the inner radius of the closer to be only a slightly bit larger the shaft's outer radius, and the closer's outer radius to match the disk's.
Step 7: Connector
Like the limbs, each connector is is of a different size, depending on what pieces it connects. The connector is also made using the same revolving tactic as the limbs. Follow the images below, they are pretty much self explanatory.
Step 8: Base
The base is built in a way, which makes it one parts, that is repeated several times. With each side of the triangle, use the same procedure as the limb, revolving, cutting and extruding. On the bottom middle pivot point, is the main axis point, from which the shaft that connects the disks together goes through. Next, extrude all three points on the triangle, with the two bottom ones shorter than the top one (as shown in image). The two bottom protruding struts are where the upper triangles will be connected. When you finish, mirror the part with the mirror plane being the end of the tallest protrusion made earlier (top one). After you mirror the parts, you need to use the rectangular pattern tool, to repeat the part you just made as many times as the amount of legs you want.
Step 9: BOM
Bill of Materials, as JPEGS.
Step 10: Video
Step 11: NXT!
My next goal is to build an NXT powered Strandbeest, but since exam week is starting, I won't have the time to finish it currently. this is as far as I got.
http://www.thingiverse.com/thing:166585
Attachments
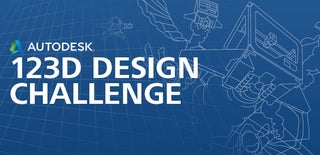
Runner Up in the
Autodesk 123D Design Challenge